Manuel Alejandro Solano
Quality Manager at Hisense Mexico- Claim this Profile
Click to upgrade to our gold package
for the full feature experience.
-
English -
Topline Score
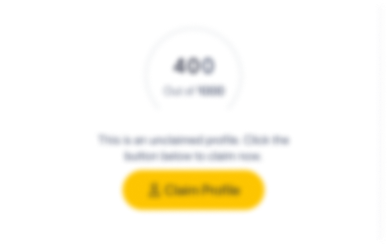
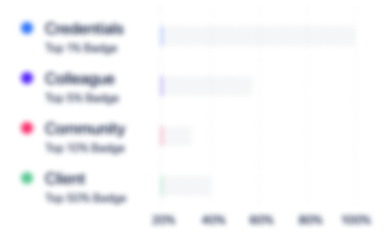
Bio


Credentials
-
Green Belt Six Sigma
DelphiDec, 2015- Nov, 2024
Experience
-
Hisense Mexico
-
Mexico
-
Computers and Electronics Manufacturing
-
100 - 200 Employee
-
Quality Manager
-
Jun 2021 - Present
-
-
-
Whirlpool Corporation
-
United States
-
Manufacturing
-
700 & Above Employee
-
Quality Manager - Incoming inspection, containment & Customer Assurance Lab.
-
Oct 2018 - Feb 2021
Quality Manager in charge of customer satisfaction, incoming inspection & Customer Assurance Lab. at Whirlpool refrigeration plant, projects leader working along with desing and manufacturing areas to improve product performance and internal and external KPI's for continuous improvenent.WCM Quality Control pillar specialist
-
-
Operational Quality Manager
-
May 2017 - Oct 2018
Operational Quality leader for refrigerators assembly lines.Responsible of maintain kpi's (FPY/FTQ, internal claims) of 4 assembly lines attending assembly, supplier and internal processes issues and develop of problem solving analysis for metrics improvements, layered procees audits.Costs reductions and continuous improvement projects.Administration and talent development of +120 operators and 8 engineers organization.
-
-
-
Bocar Group
-
Mexico
-
Motor Vehicle Manufacturing
-
700 & Above Employee
-
Product Quality Chief
-
Oct 2016 - May 2017
Responsible to maintain quality assurance metrics in a Motor Covers make plant (processes: Fusion, Casting, punching, machined and assembly). Follow up to PTR for changes, pilots for new products, develop/update control plans and define acceptance criteria, leader for QRQC analysis for customer complaints, product audits, process audits, kaizen journals for findings during audits leading. Customers: Ford, GM, Nissan, Chrysler, Sachs ZF, Mazda. Responsible to maintain quality assurance metrics in a Motor Covers make plant (processes: Fusion, Casting, punching, machined and assembly). Follow up to PTR for changes, pilots for new products, develop/update control plans and define acceptance criteria, leader for QRQC analysis for customer complaints, product audits, process audits, kaizen journals for findings during audits leading. Customers: Ford, GM, Nissan, Chrysler, Sachs ZF, Mazda.
-
-
-
Hyundai MOBIS
-
South Korea
-
Motor Vehicle Manufacturing
-
700 & Above Employee
-
Quality Assistant Manager
-
Jan 2016 - Sep 2016
Responsible of New car projects, customer feedback and warranty claims analysis in an automotive lamps production plant (Molding, paint and assembly). In charge of new projects development for ISIR submission, follow up and perform environmental and photometry tests, monitor customer systems for quality reports and follow up to cases reported on daily basis, direct contact with customer, responsible for track customer reports and daily findings in internal system, attend customer visits and audits.
-
-
-
Delphi
-
United Kingdom
-
Motor Vehicle Manufacturing
-
700 & Above Employee
-
Quality General supervisor
-
Feb 2015 - Jan 2016
Responsible of customer feedback in harnesses make plant working for Ford and GM, main customers contact, warranties and plant indicators for quality area.
-
-
Quality Engineer
-
Mar 2013 - Feb 2015
Responsible of customer feedback in connectors assembly area (plastics) and metal stamping area (terminals for harnesses). In charge of 8D elaboration, control plan & pfmea update, DPS, 5 why's.Respond and follow up to customer complaints.Coordinate and lead multifunctional team meetings to solve and respond failure modes reported by the customer and follow up to corrective actions completion and implementation. National and overseas customers.
-
-
Customer Support Engineer
-
Aug 2011 - Mar 2013
Component Customer Support Engineer. Responsible to establish communication with customers, customer visits and support to suppliers with customer concerns.
-
-
Supplier development technician
-
Mar 2010 - Sep 2011
Supplier development/supplier monitoring (harnesses make plant) - Administrate supplier development area; Elaborate internal and external supplier complaints of raw materials, containment and inspection of suspect raw materials, direct contact with national and international supplier quality contacts; Six Sigma projects, part specification drawings interpretation; Failure modes analysis and defects reproduction in manufacturing area.
-
-
Engineering/Kaizen Technician
-
Nov 2009 - Mar 2010
Assigned to "eyes for waste" project. Responsible of times and movements studies for improve/reduce headcount in manufacturing lines. Racks/shelves desing and improvement, lay out re-design.
-
-
Education
-
Instituto Tecnológico de Los Mochis
Ingeniería, Ingeniería industrial
Community
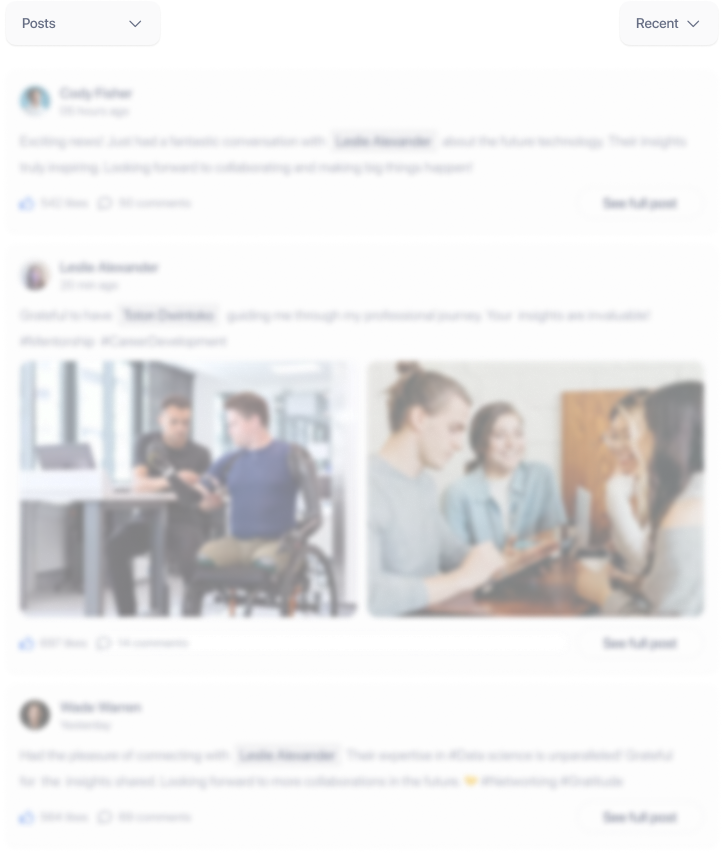