Manol Manolov
Sales Manager - MikroPul at Nederman MikroPul UK- Claim this Profile
Click to upgrade to our gold package
for the full feature experience.
-
Bulgarian Native or bilingual proficiency
-
English Full professional proficiency
Topline Score
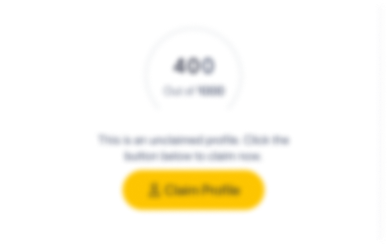
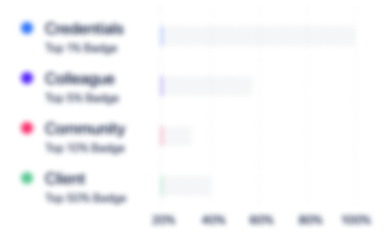
Bio


Experience
-
Nederman MikroPul UK
-
United Kingdom
-
Environmental Services
-
1 - 100 Employee
-
Sales Manager - MikroPul
-
Jan 2020 - Present
The Clean Air Company The Clean Air Company
-
-
-
Primetals Technologies
-
United Kingdom
-
Industrial Machinery Manufacturing
-
700 & Above Employee
-
Sales Manager
-
Jan 2013 - Dec 2019
My core responsibility was to lead complex B2B sales opportunities with a cross-functional team and prepare winning sales strategies. Essential part of my duties was to manage and build relationships with global key customer accounts, contract negotiations and present complex technical solutions. Other Key Responsibilities: * Develop and maintain strategic relationships with key accounts and understanding of their key needs and future investment plans. * Prepare and present sales strategies and business risk assessment for any new sales opportunity. * Conduct market research and product/solution development for key technologies and innovations. * Identify new business opportunities and strategic partnerships for specific projects. * Review of existing technical portfolio regarding specific markets and customers. * Support new production development with market intelligence and business case studies. Show less
-
-
-
Sahaviriya Steel Industries PCL
-
Thailand
-
Mining
-
100 - 200 Employee
-
Technical Development Specialist - Coke & Sinter
-
Dec 2011 - Dec 2012
My main responsibility was the development of Value-in-Use evaluations of new raw materials used in the coke and sinter making processes, and the blast furnace burden mix. I have achieved operation savings exceeding 10 (ten) million GBP and prevented production stoppages worth millions of pounds per day, by adjusting the raw materials strategy and operational planning. I also supported the research and development activities for new technology aimed to improve production and quality performance. Using my commercial skills I was able to advise and assist the procurement team at key stages of the raw materials sourcing process. Other main accountabilities included: This included the following accountabilities: * Providing technical expertise in assessing coking coals selection for the coke making process, sintering fines, iron ore lump, pellets, including analysing new suppliers. * Support of new development projects - technical, IT and production. * Analysis coal and coke quality, product and production monitoring. * Expertise in coal & sinter blending, burden composition and coal processing (coal crushing). * Coal and coke quality prediction modelling, based on mathematical models and coal properties(coal ash analysis, thermoplastic and coal composition). This includes cold and hot strength indexes - M40, M10, CSR, CRI, etc. * Evaluation of value in use (VIU) for new and existing raw materials (coal, sinter fines, lump ore, reverts, scraps,etc.) to determine the most cost effective burdening solution under given strict specifications. * Supporting Redcar Blast Furnace burdening requirements, with technical evaluation of lump ore, pellets and fluxes. * Aiming to develop further knowledge in PCI coals and operations. * Supporting the procurement team with suppliers analysis and raw material planning strategy. Show less
-
-
-
Tata Steel in Europe
-
United Kingdom
-
Mining
-
700 & Above Employee
-
Area Technical Manager
-
Apr 2011 - Dec 2011
Key Responsibilities:• Technical lead for the mill downstream operations managing all quality systems under ISO 9001• Project management of key improvement projects focused on implementing new technology, increasing production performance and product quality.• Co-ordination of all QA/QC enquires from the main on site customers.• Managing new product development, trials and testing.• Yield improvement team leader, resulting in increased yield performance of the mill.• Key account manager for the main on-site customers offering prompt and technical support for all products supplied by the mill.• Successfully completed the implementation of several new product development projects by planning and managing the product testing to successfully pass the customer specifications.• Achieved the prompt implementation of KPI for the operational team to improve the OEE (Overall Equipment Effectiveness) performance of the mill.• Continuous Improvement Champion with a key role in the culture change programme. Show less
-
-
Process Engineer
-
Jun 2010 - Apr 2011
Key Responsibilities:• Process lead responsible for the product delivery performance of the mill, and direct report to the business development group• Key role in the implementation of new business KPIs such as OEE (Overall Equipment Effectiveness) for the mill.• Continuous Improvement Champion leading several key project (5S, TPM and SMED) and culture change programme.• Implemented a new automated delay recording system to improve the visibility of time loss during production helping the engineering team to improve defect elimination, equipment maintenance and OEE performance of the mill.• Promoted to Area Technical Manager within 9 months from the start of my new role Show less
-
-
Manufacturing Graduate
-
Sep 2008 - Jun 2010
I worked across 3 main areas in Teesside Cast Products, as part of my graduate placements: Burden Preparation, Steelmaking (BOS Technical), Redcar Blast Furnace (Production). I was involved in many projects and day-to-day tasks both technical and manufacturing based. Some of the main once are:*Coal blending, including coal bed planning, coal and coke quality prediction modelling, monitoring production execution of bed build, quality analysis and research.*Sinter productivity - quality research on sintering raw materials.*BOS Technical Trial – Improving hot metal phosphorus removal using Clinker Cement, including trail planning and monitoring, data mining and analysis of the results.*BOS Technical Trial – Improving steel deoxidation and aluminium alloys savings, including data mining, cost analysis, technical review aluminium usage by steel grade.*Improving ladle argon bubbling performance - leading part of a continuous improvement group, process analysis and monitoring, research and benchmarking of new technology, review of PLC controls of the system.*Improving Health & Safety performance and standards - involved in number of H&S projects.*Improving taphole length and clay injection at Redcar Blast Furnace - review of taphole clay injection and evaluation of the process.*Developing new and improved SPC scheme for maintaining taphole length.*Technical assessment of the carbon blocks of Redcar Blast Furnace - monitoring and assessment of the furnace heart carbon refractories condition.*Part of the RBF “blowdown” team, following the mothballing of the plant - H&S control of the Salamander tap preparation. Assisting the engineering team with numerous task to safely mothball the plant.As part of the placements I was involved in many day-to-day tasks, shift work, continuous improvement projects and R&D. During these placements I gain a great technical and process knowledge about the iron and steel making process, covering the full product cycle. Show less
-
-
-
DARS Printing Shop
-
Burgas, Bulgaria
-
Purchasing & Supply
-
Oct 2006 - Aug 2007
I supervised and maintained an efficient and effective supply system. I was responsible for controling costs within assigned units and keeping with approved budgets. Big part of my job was compiling orders for supplies and equipment. * Purchase requisitions, contracts and payment terms negotiations. * Order compilations, including organising international logistics and control. * New technology installation, proving support to the manufacturing team. * MRP I - supported busy batch production process, with JIT deliveries, stock control and Kanban systems. * Technical evaluation of raw materials - adhesive and list paper, cartboard, inks, glue, cutting dies, etc. Show less
-
-
Education
-
The University of Salford
MSc, Manufacturing Systems and Management -
Technical University Varna
BSc (Hons) Industrial Management, Manufacturing Engineering -
PMG Acad.N Obreshkov
Community
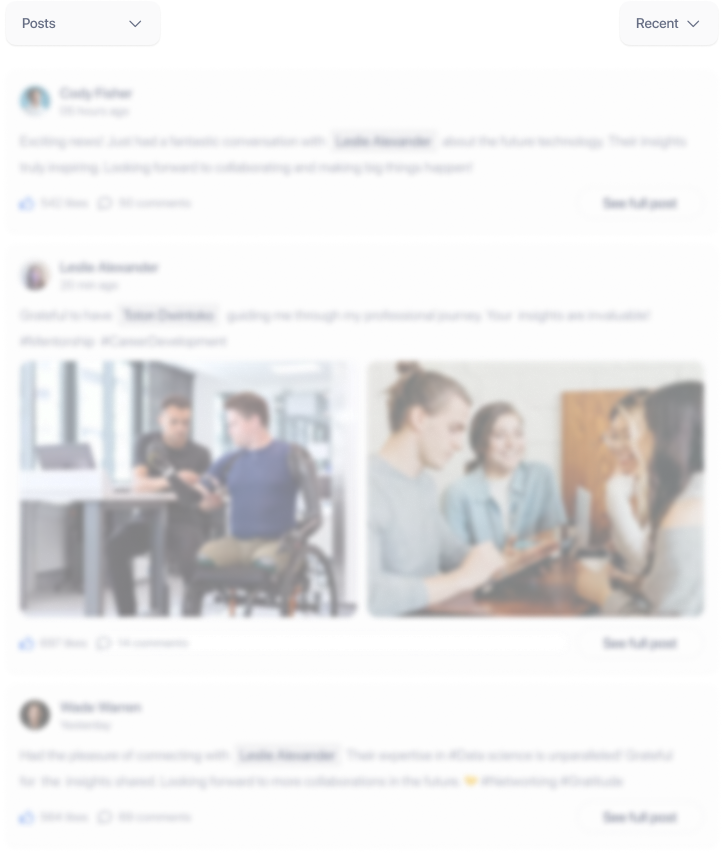