Mannar Mannan
Operations Manager at Mathi Engineering Enterprises (MEE)- Claim this Profile
Click to upgrade to our gold package
for the full feature experience.
-
English,Hindi,Tamil -
Topline Score
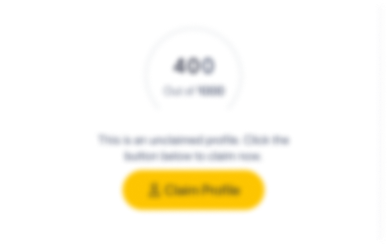
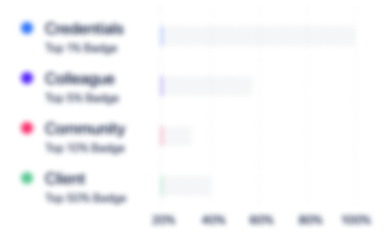
Bio


Experience
-
Mathi Engineering Enterprises (MEE)
-
India
-
Oil and Gas
-
1 - 100 Employee
-
Operations Manager
-
Feb 2019 - Present
-
-
-
Vi ENERG Resources Private Limited
-
India
-
Oil and Gas
-
1 - 100 Employee
-
Project Manager
-
Jul 2014 - Dec 2018
-
-
-
Samsung C&T Corporation
-
South Korea
-
Construction
-
700 & Above Employee
-
QC Inspector Piping Welding
-
Sep 2013 - Jan 2014
Execute the inspection as per client QA/QC documents such as ITP (Inspection Test Plan), QCP (Quality Control Procedure) and MS (Method Statement). Maintaining, Implementation and updating of ISO procedures and formats. Co-ordination with Client and Third party inspector as well / AI with respect to the fabricated items. Initiate NCR for all Materials that do not conform to project specification and codes. Monitoring the QA/QC documentation of the subcontractors and ensure that all activities are incorporated to their system on daily basis. Base material Inspection as per supplier / manufacture document/ mill certificate With respect to type, size, quantity identification and visual inspection. Handling different welding processes like SMAW, GTAW, GMAW, FCAW and SAW. Surveillance of welding activities like essential like current, voltage, heat input, welder techniques and other requirements according to WPS. Control and monitor the welding consumables, calibration of welding machine, portable oven, holding oven and baking oven on regular basis. Witness of visual inspection weld fit up, dimensional check and welding process (before, during and after). Review of fit up, welding, PMI and PWHT reports on daily basis. Welder’s performance (WQT) in production welding (WPS & PQR) Repair welding Procedure. Witnessing & reviewing of non destructive tests such as Radiographic interpretation (RI), Utrasonic test (UT), Penetrate test (PT) and Magnetic particle inspection (MPI). Checking the punch listing item as per P & ID and Isometric, such as pipe support, valves, guides, and NDT completion. Review Weld map, Welding summary records and final welding documentation before hydrotest. Witnessing of Final Piping Pressure test and Valve test(Hydro & Pneumatic). Final reinstatement and verification inspection, Pipeline and P&ID walkthrough, final mechanical completion and inspection. Show less
-
-
-
Consolidated Contractors Company
-
Greece
-
Construction
-
700 & Above Employee
-
QC Inspector Piping Welding
-
Oct 2012 - Apr 2013
Receiving inspection of pipes, fittings, valves and flanges as per purchase order and ensure mechanical, chemical properties as per code and specification requirement Controlling of welders certifications and issuing of their Job Clearance Card as per project requirement Monitoring welding consumable log sheet (for baking, holding and portable ovens) Ensure different welding process as per approved WPS Visual inspection of weld joints for different materials by different processes. Liaison between company and third party inspection. Review and Verification of Hydro Test Packages, line checking and Punch Listing. Monitor and close out of identified NCR. Reviewing and Approving the Welding Performance Qualification Report (WPQR) and Welding Procedure Specification (WPS). Organizing / Witnessing the Welder Training Program and Welder Qualification Test. Show less
-
-
-
Topaz Energy and Marine
-
United Arab Emirates
-
Oil and Gas
-
700 & Above Employee
-
QC Inspector Piping Welding
-
Feb 2012 - Aug 2012
Monitoring the QA/QC documentation of the subcontractors and ensure that all activities are incorporated to their system on daily basis and can be traced according to project requirement. Surveillance inspection of construction activities in accordance with approved ITP and project requirements, and report findings. Preparing and monitoring weld sequencing as per code to avoid distortion during production and supervising the systems for qualification of weld procedures and welders. Ensuring that all the welding related records such as weld maps, welding procedure, welder qualification documents and calibration records of welding related equipments etc. are maintained as per code requirements. Welder’s performance (WQT) in production welding (WPS & PQR) Repair welding Procedure. Witnessing & reviewing of non destructive tests such as Radiographic interpretation (RI), Ultrasonic test (UT), Penetrate test (PT) and Magnetic particle inspection (MPI). Material handled Super Duplex (UNS S32750), Copper Nickel (Cu-Ni), Nickel Alloy and Galvanized Steel. Radiographic film interpretation and evaluation in compliance with relevant codes. Show less
-
-
-
Consolidated Contractors Company
-
Greece
-
Construction
-
700 & Above Employee
-
QC Inspector
-
Feb 2007 - Feb 2011
Daily co-ordination with Construction and sub contractors to perform sequence based inspections Familiar with the construction Drawing, General Arrangement Drawing, Piping and Instrument Diagram and Isometric Drawing. Carryout material receiving inspection in accordance with the inspection planning. Inspect the activities of fabrication (fit-up & welding), installation of pipe spool in pipe rack, Pressure testing, valve testing, punch list, reinstatement and final mechanical completion. Review drawing and specification, making field modification report whatever changes or revision on the drawing. Carryout visual inspection of valve test, piping, welding, offering NDT and PWHT. Witnessing & reviewing of non destructive tests such as radiographic test (RT), ultrasonic test (UT), penetrate test (PT) and magnetic particle inspection (MPI). Witnessing Welder Qualification Test and conduct tool box meeting to improve welder’s technical skill. Material handled Carbon Steel, LTCS, SS (304L, 316L), Duplex (UNS S31803), Super Duplex (UNS S32750), Copper Nickel (Cu-Ni), Nickel Alloy and Galvanized Steel. Confirm repairs, re-testing and re-inspection in accordance with specifications. Reviewing the spool releasing check sheet and sending to the site after approval. Reviewing final package for hydro test approval and releasing for test. Verify installation of field piping and equipment pressure test punch list. Ensure correction or completion of punch list items. Verify preparation of piping test package including piping test record; Ensuring all fabrications are constructed in accordance with drawing assembly/fabrication details Final reinstatement and verification inspection, Pipeline and P&ID walkthrough, final mechanical completion and inspection. Closing the issue of DR (Discrepancy Report), NCR (Non Confirmation Report), Project Owner Log Book. Show less
-
-
Education
-
Annamalai University
Bachelor's degree, Mechanical Engineering -
Muthailpet Higher Secondary School.,Chennai
Community
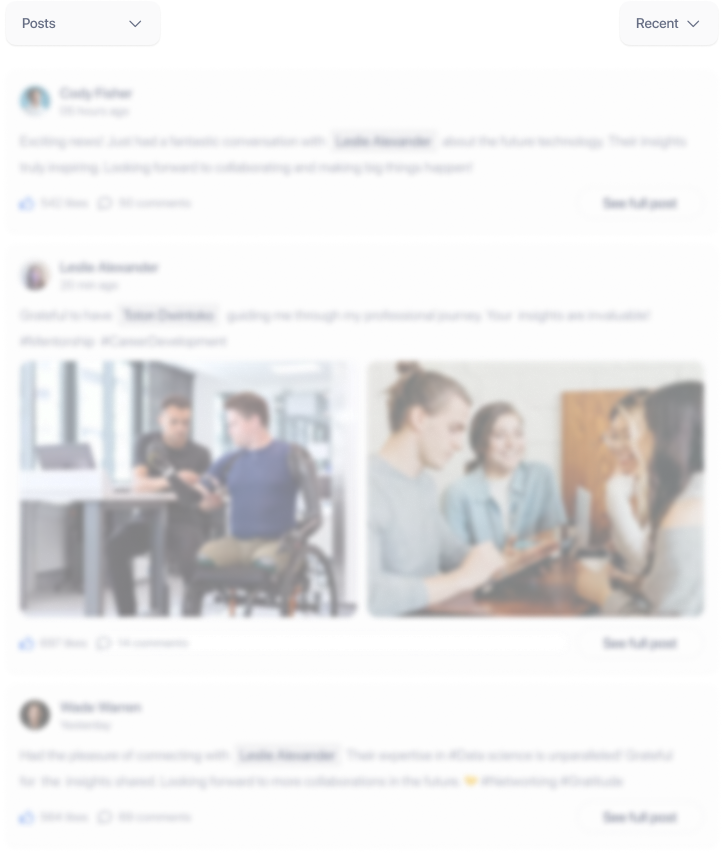