Malcolm J. McCullouch
Sr. Business Unit Analyst at CR Bard- Claim this Profile
Click to upgrade to our gold package
for the full feature experience.
Topline Score
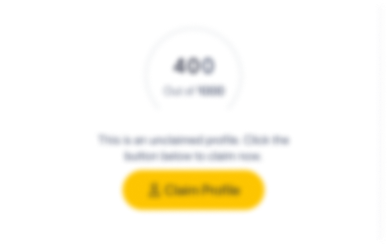
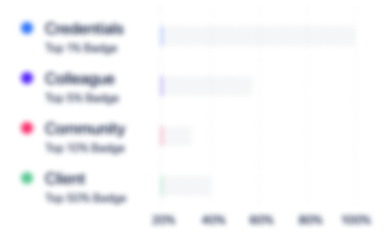
Bio

Jay Teagle
I had the pleasure of working with Malcolm for approximately eight years at Tyco Healthcare. Malcolm possesses an extremely strong work ethic and exhibits exemplary ethical standards. Malcolm's background of industrial engineering coupled with his acquired experience in finance allow him a unique perspective in business environments where he can quickly analyze a problem and recommend and implement solutions. Malcolm is a very quick learner and demonstrates outstanding leadership skills. He is adaptable to all types of organizations and interacts very well with salaried and hourly people alike. Malcolm would be an asset to any organization and I would welcome the opportunity to work with him again.

Jay Teagle
I had the pleasure of working with Malcolm for approximately eight years at Tyco Healthcare. Malcolm possesses an extremely strong work ethic and exhibits exemplary ethical standards. Malcolm's background of industrial engineering coupled with his acquired experience in finance allow him a unique perspective in business environments where he can quickly analyze a problem and recommend and implement solutions. Malcolm is a very quick learner and demonstrates outstanding leadership skills. He is adaptable to all types of organizations and interacts very well with salaried and hourly people alike. Malcolm would be an asset to any organization and I would welcome the opportunity to work with him again.

Jay Teagle
I had the pleasure of working with Malcolm for approximately eight years at Tyco Healthcare. Malcolm possesses an extremely strong work ethic and exhibits exemplary ethical standards. Malcolm's background of industrial engineering coupled with his acquired experience in finance allow him a unique perspective in business environments where he can quickly analyze a problem and recommend and implement solutions. Malcolm is a very quick learner and demonstrates outstanding leadership skills. He is adaptable to all types of organizations and interacts very well with salaried and hourly people alike. Malcolm would be an asset to any organization and I would welcome the opportunity to work with him again.

Jay Teagle
I had the pleasure of working with Malcolm for approximately eight years at Tyco Healthcare. Malcolm possesses an extremely strong work ethic and exhibits exemplary ethical standards. Malcolm's background of industrial engineering coupled with his acquired experience in finance allow him a unique perspective in business environments where he can quickly analyze a problem and recommend and implement solutions. Malcolm is a very quick learner and demonstrates outstanding leadership skills. He is adaptable to all types of organizations and interacts very well with salaried and hourly people alike. Malcolm would be an asset to any organization and I would welcome the opportunity to work with him again.

Experience
-
CR Bard
-
United States
-
Medical Equipment Manufacturing
-
700 & Above Employee
-
Sr. Business Unit Analyst
-
Nov 2014 - Present
-
-
-
Covidien (Medtronic Minimally Invasive Therapies Group)
-
United States
-
Medical Equipment Manufacturing
-
700 & Above Employee
-
Plant Controller
-
2006 - 2014
Directed all financial aspects for the local operations. Prepared monthly financial reports, annual operating budgets, and capital budgets. Analyzed product costing, managed inventory, handled financial audits, and administered financial controls.• Won FY2013 COVIDIEN Top Financial Performance Small/Medium Plant award through controlling spending and managing variances.• Developed a system for on-boarding new Plant Controllers by leading an international team.• Experienced in both on-boarding and off-loading manufacturing operations.• Supervised a 4 member Financial and IT team to continuously develop strategies to improve operations.• Directed processing of hourly payroll, accounts payable, fixed assets, and cost-accounting functions.• Administered plant’s Information Systems with experience in multiple system implementations.• Skilled in Fixed Asset physical inventories (organizing, conducting, and reconciling).• Experienced physical inventory manager (organizing, conducting, and reconciling).
-
-
Assistant Controller
-
2003 - 2006
• Collaborated with Plant Controller in managing all aspects of plant’s financial operations. • Oversaw Accounts Payable and Payroll, managed standard cost system, coordinated fixed asset records, and prepared month-end and year-end financial reports. • Contributed to annual capital and operating budgets. • Served on New Product Development team to provide financial guidance.• Conducted plant’s first-ever fixed asset physical inventory and reconciliation.
-
-
Senior Cost Accountant
-
2002 - 2003
• Backed-up to the Plant Controller as required.• Supervised Accounts Payable and Payroll activities.• Prepared material, labor, capital, and cost reductions portions of annual budget.• Administered all aspects of the standard cost system insuring accurate cost standards and inventory valuation.
-
-
Planning/Logistics/Cost Supervisor (Acting Materials Manager)
-
2000 - 2002
• Coordinated efficient production schedules to manufacturing through supervision of Production Planners. • Improved warehouse effectiveness through organization and personnel changes. • Maintained all cost accounting responsibilities.
-
-
Cost Accountant
-
1998 - 2000
• Insured accurate cost standards and inventory valuation for all aspects of the standard cost system.• Reviewed and evaluated potential standards changes based on previous performances.• Participated on new product development teams.• Coordinated cost improvement teams.• Assisted with various other financial reporting requirements.
-
-
Schedule Coordinator
-
1996 - 1998
Returned to former role as a result of business needs and successful completion of on-loading a new business acquisition.• Directed efficient and economical operations of the manufacturing floor.• Insured adherence and compliance to quality standards and GMP's.• Coordinated production schedules and set-ups.• Established production targets (Units/Hrs. goals).• Led Process Improvement Teams.• Provided leadership and direction to Production Supervisors by reviewing and auditing Daily Operating Schedules and schedule attainment status.• Conducted monthly manpower planning analysis and coordinated special projects.
-
-
Department Supervisor
-
1995 - 1996
• Supervised activities of up to 30 people while assuring quality and compliance to GMP's.• Maximized utilization of materials and equipment and achievement of production schedules.• On-loaded a new business acquisition including startup of equipment, training of associates, and relocation of inventory.• Identified, recommended, and implemented solutions to production and operating problems.• Maintained the communication network amongst the company and its employees.
-
-
Schedule Coordinator
-
1993 - 1995
• Directed efficient and economical operations of the manufacturing floor.• Insured adherence and compliance to quality standards and GMP's.• Coordinated production schedules and set-ups.• Established production targets (Units/Hrs. goals).• Led Process Improvement Teams.• Provided leadership and direction to Production Supervisors by reviewing and auditing Daily Operating Schedules and schedule attainment status.• Conducted monthly manpower planning analysis and coordinated special projects.
-
-
Technical Training Supervisor
-
1992 - 1993
• Wrote and implemented formal manufacturing procedures for compliance with GMP's.• Created, implemented, and conducted formal training programs for the entire manufacturing facility.• Participated with all new product development projects and their associated introductions into manufacturing from Research & Development.
-
-
Production Supervisor
-
1992 - 1992
• Supervised activities of up to 40 people while assuring quality and compliance to GMP's.• Maximized utilization of materials and equipment; achieved productions schedules.• Identified, recommended, and implemented solutions to production and operating problems.• Maintained the communication network amongst the company and its employees.
-
-
-
NAMIC, Electronics Systems Division
-
Glens Falls, New York
-
Industrial Engineer
-
1990 - 1992
• Insured efficient and economical electronic assembly operations using detailed methods analysis, time study, work sampling, pre-determined time systems, plant and process flow layouts, and ergonomics. • Identified and implemented creative solutions to production and operating problems through design, fabrication, and implementation of special tooling, fixtures, and processes. • Trained supervisors and employees in efficient methods for assembly. • Managed all phases of new prototype builds, troubleshooting specific assembly problems and issues. • Selected, justified, and implemented capital equipment projects. • Assisted with the development of individual job quotations, development of cost reduction measures, expediting production while assuring quality; and computer programming.
-
-
-
Carisbrook, Industries, Inc
-
Glens Falls, New York
-
Industrial Engineer
-
1983 - 1990
• Utilized classical Industrial Engineering techniques to conduct performance and productivity reviews, establish production goals, and recommend and implement savings and improvements in all manufacturing and administrative departments. • Analyzed, developed, implemented, and corrected new and existing wage incentive payroll programs. • Participated with selection, justification, and installation of capital equipment projects. • Assisted with development of capital and operating budgets and cost reduction programs. • Established unit cost standards. • Trained personnel to operate personal computers. • Special assignments included development of personal computer application programs for scheduling, materials requirements planning, manufacturing, administrative functions, and preparation of CAD drawings for plant and warehouse layouts.
-
-
Education
-
Clarkson College of Technology
Bachelor of Science (BS), Industrial Distribution -
Institute of Industrial Engineers
Certification, Time Study Procedures -
Adirondack Community College
Community
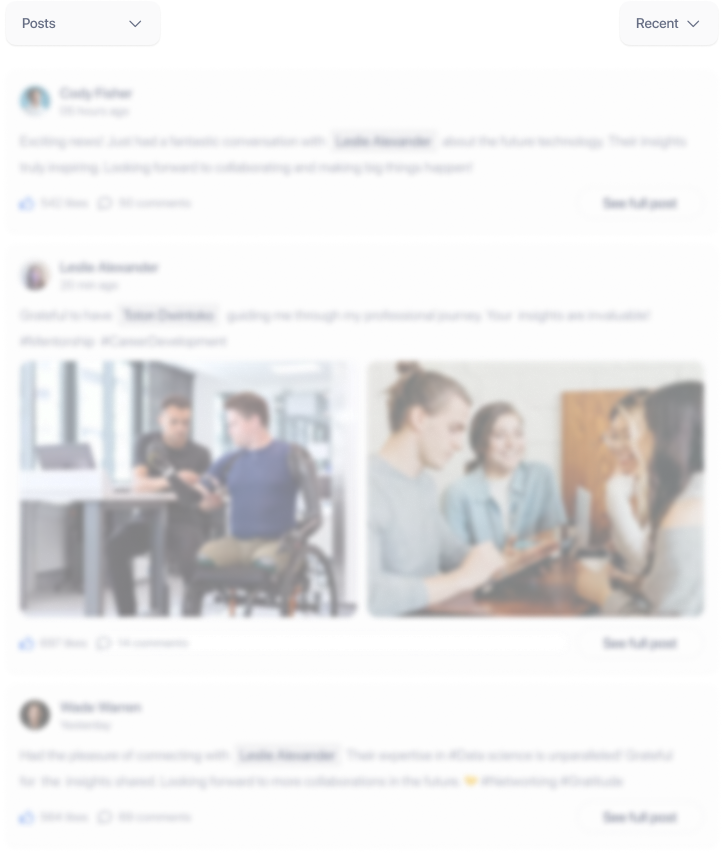