Mahesh Gawde
Head of Sales & Operations at Steriscience- Claim this Profile
Click to upgrade to our gold package
for the full feature experience.
Topline Score
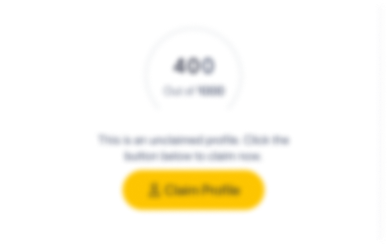
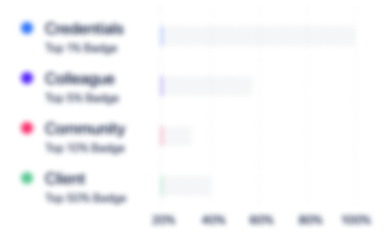
Bio


Experience
-
Steriscience
-
Pharmaceutical Manufacturing
-
100 - 200 Employee
-
Head of Sales & Operations
-
Nov 2022 - Present
Banglore
-
-
-
Dr. Reddy's Laboratories
-
India
-
Pharmaceutical Manufacturing
-
700 & Above Employee
-
Associate Director, Supply Chain Management and Head of Central Planning
-
Jan 2018 - Nov 2022
Hyderabad Area, India o Leading team of 5 people responsible for planning of finished goods supply for manufacturing to meet customer demand (orders and forecast). o Inventory management and control; monitor net inventory against the target and take corrective actions (long term & short term) to keep inventory within target. Continuous review of COPE (cost of poor execution) and action plans to achieve COPE targets. Monthly update of savings ( 80crs FY19 ) from COPE+FTS to GMO leadership o Core member of… Show more o Leading team of 5 people responsible for planning of finished goods supply for manufacturing to meet customer demand (orders and forecast). o Inventory management and control; monitor net inventory against the target and take corrective actions (long term & short term) to keep inventory within target. Continuous review of COPE (cost of poor execution) and action plans to achieve COPE targets. Monthly update of savings ( 80crs FY19 ) from COPE+FTS to GMO leadership o Core member of Fixing Foundation initiative aimed at improving S&OP process and strengthening SCM capabilities o Design and Develop automated dashboards to provide required analytics to GMO leadership and SCM users to measure performance of SCM-total 22 dashboards. e.g. Sales OTIF, R vs C vs A, Forecast Accuracy, Capacity utilization, Net Inventory, COPE, Sourcing OTIF, Sourcing DCO, etc o Monitor health of end to end planning processes, Master data and identify scope of improvements & automations.
-
-
Associate Director, Supply Chain Management, Central Planning
-
Jan 2017 - Dec 2017
Hyderabad Area, India o Leading team of 2 people responsible for planning of finished goods supply for manufacturing to meet customer demand (orders and forecast). o Own Demand and Supply Planning, Rough capacity Planning, Production Planning and detail scheduling and Procurement Planning to ensure that forecast can be fulfilled within time and ensuring health of related processes for Formulation & API business in India, US, UK and Mexico having turnover of $2.3 bn o Distribution Planning for India from 2… Show more o Leading team of 2 people responsible for planning of finished goods supply for manufacturing to meet customer demand (orders and forecast). o Own Demand and Supply Planning, Rough capacity Planning, Production Planning and detail scheduling and Procurement Planning to ensure that forecast can be fulfilled within time and ensuring health of related processes for Formulation & API business in India, US, UK and Mexico having turnover of $2.3 bn o Distribution Planning for India from 2 global distribution centers to 27 CFAs on daily frequency with full truck load criteria o Improved forecast accuracy from 65 to 78% by identifying SKUs with high error index and applying correct statistical models as well correcting sales history. o Reduced manual PRs from 25% to 13% by optimizing inventory policies, ensuring master data correctness and improved production plan o Ensuring adoption of KPIs-dashboard through gap identification and user acceptance through hand holding
-
-
Manager, Supply Chain Management, Central Planning
-
May 2014 - Dec 2016
Hyderabad, Andhra Pradesh, India o Continually identify opportunities for system and process improvement and utilize operational excellence and project management skills to implement change o Highlight specifics risks and opportunities within the supply chain which could impact the cost or service levels expected by the plan o Rough cut capacity/ Supply Planning & Production scheduling : identification of gaps, reduction in manual intervention below 10% and user trainings o Improved sourcing OTIF from 55 to 85% o… Show more o Continually identify opportunities for system and process improvement and utilize operational excellence and project management skills to implement change o Highlight specifics risks and opportunities within the supply chain which could impact the cost or service levels expected by the plan o Rough cut capacity/ Supply Planning & Production scheduling : identification of gaps, reduction in manual intervention below 10% and user trainings o Improved sourcing OTIF from 55 to 85% o Member of I^2- Intelligent Integration Project- implementation Core Team for consultation, diagnostic & design phase. o I^2: A Supply Chain Operations transformation initiative of business ‘upgrading to industry leadership standards’ ensuring a structured, end to end integration of Supply Chain and Operations Management. Worked closely with the Top Management and Deloitte as well as Bristlecone Consulting firms. o Track Lead for Procurement planning & Execution o Track Lead for Long Term Planning in APO implementation linking together Strategic Planning, Capacity Planning and Material Requirement Planning for 5 Years horizon. o KPI dashboard created by defining KPIs, aligning Stakeholders on expectations, thorough testing and user trainings o Smooth Change Management achieved resulting in to 100% adoption of new processes by end users. o Saved 9 man days per month through Mass Contract- Outline Agreement & Auto PO creation Process implementation. o Procurement linked with constrained production plan (RCCP) for better warehouse space management & inventory cost reduction. o Full kitting of production orders improved to 97%
-
-
Manager, Supply Chain Management, Strategic Sourcing & Purchase
-
Apr 2013 - Apr 2014
• Supplier Scorecard: o Supplier performance management solution to help in making strategic decisions w.r.t. supplier. Driven by Senior Management & Deloitte. o Automate supplier rating system & Generate scorecard to monitor, evaluate & communicate back supplier performance. o Said project received Global Excellence awards Viz. CPhI Pharma Operations Excellence Awards, 2014 • Project Managed ‘Business Continuity Planning & 80% of Business De-risking initiative’ with wide CFT… Show more • Supplier Scorecard: o Supplier performance management solution to help in making strategic decisions w.r.t. supplier. Driven by Senior Management & Deloitte. o Automate supplier rating system & Generate scorecard to monitor, evaluate & communicate back supplier performance. o Said project received Global Excellence awards Viz. CPhI Pharma Operations Excellence Awards, 2014 • Project Managed ‘Business Continuity Planning & 80% of Business De-risking initiative’ with wide CFT spans: o Analysis of Packaging material criticality w.r.t. top business Value at Risk. o Develop alternate vendor development plan for selected pipe line of packaging materials. o Close coordination with RA, QA & Pkg. Development for meeting the time lines of AVD projects. o Developing solutions proactively through brainstorming sessions. • Project Managed ‘Warehouse Space Optimization for Packaging Material’: o No of total pallets space occupancy reduction from 8300 to 3200 Nos. o Successfully drove the closing of outsourced warehouse operations with pallets space of 5100 Nos. focusing long term plan of 4200 Nos. of pallets space and JIT implementation, jointly analysed with Meibach consulting. o Facilitated creation of implementation plan through coordination with Planning, Warehouse. • Material Harmonisation/Standardization projects: To reduce procurement, warehousing and production complexities and increase logistics efficiency. o Foil Harmonisation: Reduced number of SKUs (Import material) from 80 to 11 nos. This reduced warehouse space requirement in totality. Further it enabled us to avail volume discounts. o Shipper Harmonisation: No of shipper SKUs reduced from 400 to 70. It enabled us to reach a volume for each SKU suitable for VMI arrangement.
-
-
Deputy Manager, Supply Chain Management, Strategic Sourcing and Plant Purchase
-
May 2011 - Apr 2013
1) Operational: o Procurement of 70 Crs: Import Spend 50 Crs- , Domestic Spend : 20 Crs o Daily review of materials in Symphony tool, identifying the gaps and expediting as required. o Continuous End to end follow-up (incl. vendor, transporter & other service providers). o Coordination with QC/QA/Planners/WH to ensure availability of materials in approved condition as per manufacturing plan. o Resolve vendor or service provider issues/grievances o Liaison with CHA for… Show more 1) Operational: o Procurement of 70 Crs: Import Spend 50 Crs- , Domestic Spend : 20 Crs o Daily review of materials in Symphony tool, identifying the gaps and expediting as required. o Continuous End to end follow-up (incl. vendor, transporter & other service providers). o Coordination with QC/QA/Planners/WH to ensure availability of materials in approved condition as per manufacturing plan. o Resolve vendor or service provider issues/grievances o Liaison with CHA for timely custom clearance of imported material without any demurrages. o Monitor and arrange for disposal/return of rejected materials and arranging replacement. 2) Strategic: o Developing quality & supply agreements with vendors o Developing Clean Sheet Costing, Price Indexing of materials and Reverse Auctioning aimed at reduction in Cost o Actively supported analysis and spend budgeting for the financial year (INR 190 Crs) o Facilitator for PACE (Performance Acceleration and Cost Efficiency Program) : An organization wide cost efficiency project with a target of $140MN over 3 years. Worked closely with Top Leadership and McKinsey Co. Spend Analysis of entire packaging spend base Application of Supply Levers like clean sheet costing, price arbitrage, LCC sourcing, AVD, LPP (Linear Performance Pricing) Conducting CFT meetings and Idea generation session for improvements in process. Developing solutions and debottlenecking of initiatives. Tracking of Idea implementation Drove ideations worth @ 24 Crs & Syndication of ideas worth @ 15 Crs.
-
-
-
Larsen & Toubro
-
India
-
Construction
-
700 & Above Employee
-
Senior Executive Engineer in ESP/EBG
-
Jul 2006 - May 2009
o Design of press tools, moulds & electrodes using modelling software “Pro-E” o Planning, Control & Outsourcing of tools o Tool Budget of worth 30 Crs o Prepared study material on Thermoplastic Moulding & Thermoset Moulding for internal consumption o Implemented a New Development Project ‘Omega’ to increase current carrying capacity with less copper in a record time of 4 months. o Successfully managed the project of scanning of 20000 drawing tracings & creating database to reduce… Show more o Design of press tools, moulds & electrodes using modelling software “Pro-E” o Planning, Control & Outsourcing of tools o Tool Budget of worth 30 Crs o Prepared study material on Thermoplastic Moulding & Thermoset Moulding for internal consumption o Implemented a New Development Project ‘Omega’ to increase current carrying capacity with less copper in a record time of 4 months. o Successfully managed the project of scanning of 20000 drawing tracings & creating database to reduce average retrieval time from 2 days to 1 min. Show less
-
-
Education
-
Symbiosis Centre For Management and Human Resource Development
Master of Business Administration (MBA), Operations Management -
College of Engineering Pune
Bachelor of Engineering (B.E.), Production Engineering -
VJTI
Licentiate in Mechanical Engineering ( Diploma ), Mechanical Engineering
Community
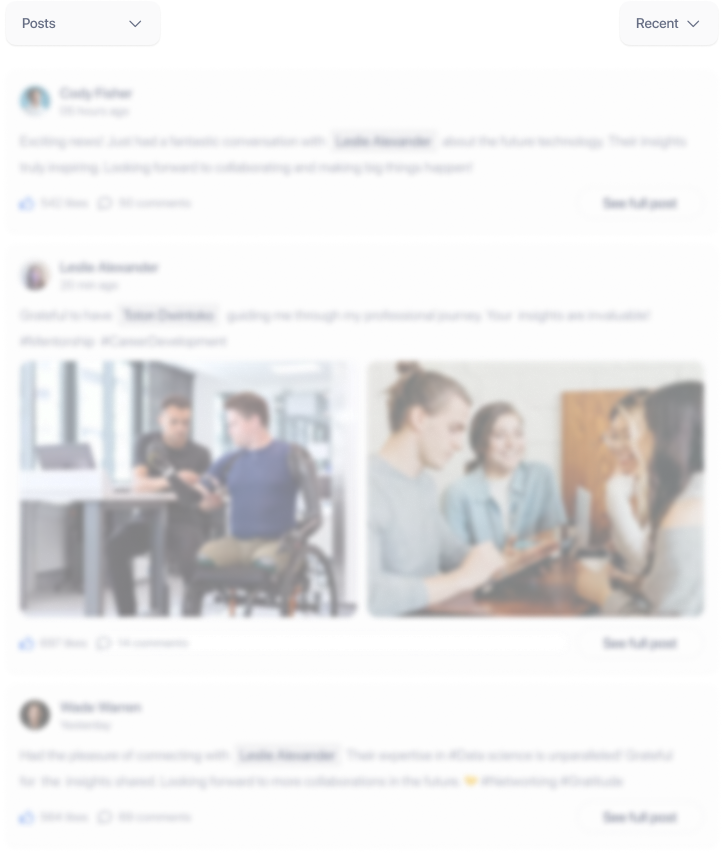