Magdalena Ewa Godziszko
Company Owner at Good Wood Poland- Claim this Profile
Click to upgrade to our gold package
for the full feature experience.
-
English Professional working proficiency
-
German Limited working proficiency
-
Polish Native or bilingual proficiency
Topline Score
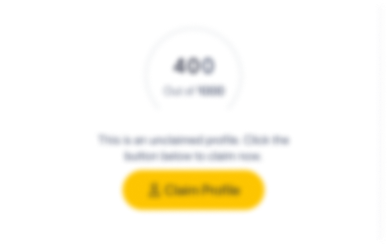
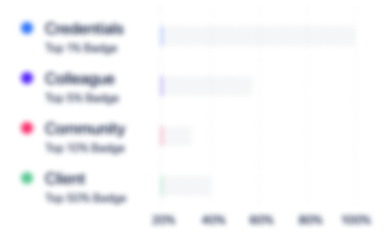
Bio

Cyril Aratoon
I would like to personally recommend Magdalena, Until just recently, I have had the pleasure to work alongside Magdalena as part of a business wide continuous improvement team, I have always found her to be consistently reliable, intelligent, taking on all assignments with dedication and a smile. Besides being great to work with, Magdalena is a take-charge person who is able to generate good ideas, communicate the benefits and then see it through to a successful result, She successfully owned several savings projects that helped the company save over £500,000 in a 12 month period. Magdalena was also instrumental in improving communication across the business and is a capable and effective trainer. I highly recommend Magdalena for employment, she would make a great addition to any management team or organization.

Cyril Aratoon
I would like to personally recommend Magdalena, Until just recently, I have had the pleasure to work alongside Magdalena as part of a business wide continuous improvement team, I have always found her to be consistently reliable, intelligent, taking on all assignments with dedication and a smile. Besides being great to work with, Magdalena is a take-charge person who is able to generate good ideas, communicate the benefits and then see it through to a successful result, She successfully owned several savings projects that helped the company save over £500,000 in a 12 month period. Magdalena was also instrumental in improving communication across the business and is a capable and effective trainer. I highly recommend Magdalena for employment, she would make a great addition to any management team or organization.

Cyril Aratoon
I would like to personally recommend Magdalena, Until just recently, I have had the pleasure to work alongside Magdalena as part of a business wide continuous improvement team, I have always found her to be consistently reliable, intelligent, taking on all assignments with dedication and a smile. Besides being great to work with, Magdalena is a take-charge person who is able to generate good ideas, communicate the benefits and then see it through to a successful result, She successfully owned several savings projects that helped the company save over £500,000 in a 12 month period. Magdalena was also instrumental in improving communication across the business and is a capable and effective trainer. I highly recommend Magdalena for employment, she would make a great addition to any management team or organization.

Cyril Aratoon
I would like to personally recommend Magdalena, Until just recently, I have had the pleasure to work alongside Magdalena as part of a business wide continuous improvement team, I have always found her to be consistently reliable, intelligent, taking on all assignments with dedication and a smile. Besides being great to work with, Magdalena is a take-charge person who is able to generate good ideas, communicate the benefits and then see it through to a successful result, She successfully owned several savings projects that helped the company save over £500,000 in a 12 month period. Magdalena was also instrumental in improving communication across the business and is a capable and effective trainer. I highly recommend Magdalena for employment, she would make a great addition to any management team or organization.

Credentials
-
IPMA Level D
International Project Management AssociationSep, 2010- Oct, 2024
Experience
-
Good Wood Poland
-
Poland
-
Design Services
-
1 - 100 Employee
-
Company Owner
-
2017 - Present
Good Wood to rodzinna, autorska marka. Tworzymy place zabaw dla dzieci – wielofunkcyjne, w naturalny sposób wspierające ich motorykę, integrację sensoryczną i kreatywność. Nasze hasło to RADOŚĆ w RUCH! Good Wood to rodzinna, autorska marka. Tworzymy place zabaw dla dzieci – wielofunkcyjne, w naturalny sposób wspierające ich motorykę, integrację sensoryczną i kreatywność. Nasze hasło to RADOŚĆ w RUCH!
-
-
-
-
Process Engineer
-
Feb 2014 - Present
As a P&G Process Engineer I am responsible for optimizing, evaluating, developing, reapplying and delivering breakthrough processes that provide winning products for consumers around the world. Dealing with a multitude of current and future products I have the technical curiosity and knowledge to develop new approaches to big problems. My work requires creativity, innovation, teamwork and leadership. I employ cutting edge technologies with multi disciplinary and highly professional teams across the P&G. My role provides me opportunities to lead projects where technical as well as leadership skills are essential and I can utilize them with a high level of autonomy. All my work leads to reduce cost, improve sustainability and develop best practices within the production process.
-
-
-
-
Plants Performance Improvement Task Force
-
Aug 2013 - Dec 2013
• Leading SMED project. Mixer change over time reduction by 74%.• Facilitation of yield improvement project across site. Annualized saving of £ 64k delivered through strong execution of lean methodology.• Roll-out of Continuous Improvement system across site.OEE monitor system leader. • Support 6 sites in daily use and provide information on wider use of OEE Toolkit • Manage data updates & system upgrades• Liaison between system supplier and CSM
-
-
Plants Performance Improvement Task Force
-
Sep 2012 - Jul 2013
Training and change management• Preparing and leading workshops, provide trainings and coaching in defect root methodology, Continues Improvement systems, lean tools.Daily control• Give away and physical waste - implementation of waste monitoring system by line across the site• Morning meetings - designing and preparing boards, meeting agenda, roll out, information, data collection, introduction of topics at the meeting: waste, speed loss, unspecified loss. Results• Yield improvement – Tunnel Oven line – Detailed data analysis (waste and yield per SKU), focus on waste reduction, revision of system (BOMs and photo standards) to clean up all differences, monitor and analysis of any abnormalities. Yield loss reduction: 10%.• Process capabilities studies for give away on Wirecut line – Several studies on weight distribution and process capabilities, calculation of give away and loss from checkweigher data. Give away reduction via a combination of employee engagement and focus through daily control.
-
-
Plants Performance Improvement Task Force
-
Jan 2012 - Aug 2012
Training and change management• Supported the PPI implementation at Delmenhorst, liaison between consultants and CSM.• Give away reduction – team preparation - data collection, trainingDaily control• Give away reporting – set up system and provide good clarity on the next steps• Speed losses reduction – set up daily control, data analysis• Reduction of unspecified loss – unspecified loss reduction via a combination of employee engagement and focus. Data collection and analysis to give team sufficient knowledge to start project.Results• Weekend cleaning time reduction – process review, data collection, standardization, process improvements. Cleaning time reduction by 20%.• Review of single doughnut packing process capability - my analysis has led to development of capital expenditure which could save >200k€ per year in savings
-
-
Plants Performance Improvement Task Force
-
Nov 2011 - Dec 2011
It was a unique experience to learn different points of views about CSM, its strategy and policy. I did this through very interesting and inspiring meetings and discussions with senior managers and other people who work hard to make our company a leading player in its sectors worldwide.
-
-
-
Philips Lighting
-
Appliances, Electrical, and Electronics Manufacturing
-
LEAN Engineer
-
Oct 2010 - Oct 2011
Since October 2010 I have worked as an LEAN Engineer in Philips Lighting Poland S.A. where automotive lamps were manufactured. I was responsible for introducing LEAN Philosophy in the company. I have learned and experienced sides of cultural change and change management. I was also responsible for workers’ trainings in the field of LEAN management. I had opportunity to coordinate and participate in several LEAN projects. I was using LEAN tools such as: waste management, visualization management, SMED, VSM, 5S, Kanban, FIFO, TPM etc. One of my projects -related to waste elimination, won internal competitions (BIC - Business Improvement Competition). That gave me a great chance to represent Philips Pabianice at European finals of Philips Business Improvement Competition in April 2011 on Rhodes. My main roles and responsibilities: • Workers training in LEAN: 7 wastes, 5S, Standard work, problem solving with 5 why analysis, VSM, Flow management, Training within industry, etc. • Implementation of LEAN Philosophy - change management • Tight cooperation with managers of mechanical, assembly, warehouse, maintenance departments in the field of coordination of implementation of LEAN Philosophy • Standardization - implementing standards at different work levels (setter, team leader, group leader, area manager) • Processes' audits - VSM (Value Stream Mapping),SOP (Standard Operating Procedures), internal audits Trainings: • Simplicity in Leadership. Two weeks´ training to become change agent of the LEAN Philosophy and facilitator in terms of a number of activities, designed around training and coaching the next level leaders in the organization. • Train the Trainers. Two days´ training on preparation and training other workers.
-
-
-
GE
-
Brazil
-
Engineering Services
-
1 - 100 Employee
-
Lead Time Reduction Team Member
-
Oct 2009 - May 2010
I was a member of the WIP (work in progress) reduction team – one of the key projects leaded at the company, aiming reduction of Work in Progress. I became acquainted with the process of production planning in the factory and its influence on the size of stocks, management of material flow in the system MRP SAP R/3, stock management, and Lean Philosophy connected with the optimization of flow and stocks in the General Electric Enterprise. My main tasks: • Preparation and analysis of daily, reports on stocks for the WIP Team, Planning Department, Production Department and Purchasing Department on the base of the SAP R/3 system, • Analysis and optimization of the materials flow, • Analysis of balances of production orders, • Daily monitoring of Work in Progress in the factory, • Tight cooperation with managers of mechanical department, assembly department, plastic department in the field of coordination of reduction of stock, identification and optimization of bottle-necks, • Standardization of supermarkets systems, • Design, creation and implementation of the “pull system” on the ground of supermarkets' systems, • Implementation of the Kanban pull system, • Audit of supermarkets, • Participation in the SMED –changeover time optimization project on the area of manual presses
-
-
-
-
Project Manager Assistant
-
Mar 2009 - Apr 2009
-Coordination of currently curried projects -Coordination of currently curried projects
-
-
Education
-
Technical University of Lodz
Master of Science, International Faculty of Engineering. Specialisation: Business and Technology -
Technical University of Vienna
Master of Science, Faculty for Mechanical Engineering and Business Science
Community
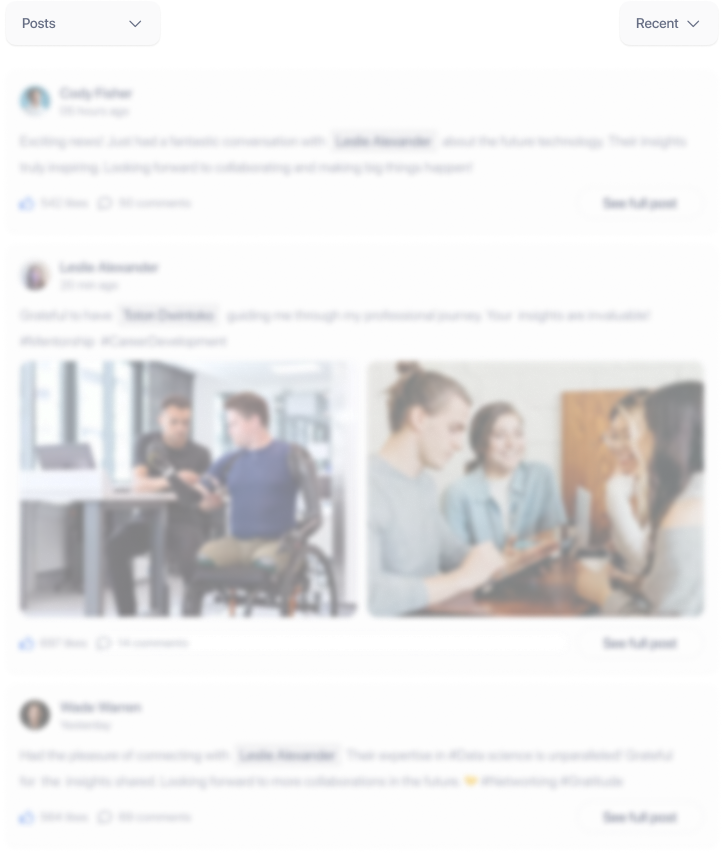