Mackenzie Poirier
Sales Engineer at HTS Engineering - Heat Transfer Solutions- Claim this Profile
Click to upgrade to our gold package
for the full feature experience.
-
English -
Topline Score
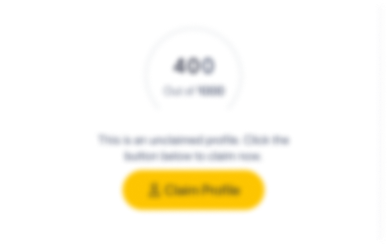
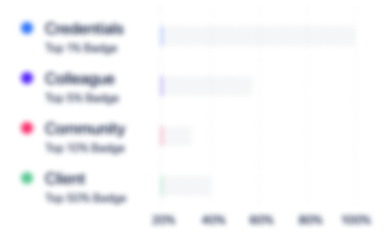
Bio


Experience
-
HTS Engineering - Heat Transfer Solutions
-
Canada
-
Construction
-
500 - 600 Employee
-
Sales Engineer
-
Jul 2017 - Present
Attended Daikin Applied Graduate Engineer Training Program 7/10/17 - 10/20/17 - Received technical product training on Daikin Applied products - Gained insight in the HVAC industry through leading professionals - Hands on experience working with operational equipment Providing technical support to clients and other sales engineers within the office 10/21/2017 - Present Attended Daikin Applied Graduate Engineer Training Program 7/10/17 - 10/20/17 - Received technical product training on Daikin Applied products - Gained insight in the HVAC industry through leading professionals - Hands on experience working with operational equipment Providing technical support to clients and other sales engineers within the office 10/21/2017 - Present
-
-
-
Flexaseal Engineered Seals and Systems, LLC
-
United States
-
Industrial Machinery Manufacturing
-
1 - 100 Employee
-
Univeristy of Vermont Senior Design Project
-
Sep 2016 - May 2017
A Senior Design Team from The University of Vermont was assigned a project working with Flex-A-Seal, a company located in Essex Vermont that specializes in design and manufacturing of mechanical cartridge seals. The senior design team consisted of myself and two other mechanical engineering students. The team was tasked with designing and building an API 682 compliant static testing device for a variety of single mechanical cartridge seals. Flex-A-Seal will be implementing this device on their shop floor to quality control check the assembly of their seals. I was tasked with designing and building the base of the device, pneumatic, and electrical systems. These tasks not only helped my proficiency in Solid works but also provided a bridge between modeling and constructing one would not achieve in the classroom. The electrical system consists of: An Arduino microcontroller, Led, switch, lcd screen, and pressure transducer. The system was first designed using wiring diagrams and data sheets before being built and tested in breadboard form. A perma-proto board was designed and custom made for the final product. The pneumatic system was designed around high safety factors and safety devices such as air mufflers and relief valves. The pneumatic system was designed to fit into the base by use of custom fitted copper pipes and panel mounted valves. Aside from my involvement in the design of the device, I also budgeted the elected sum of money and constructed a bill of materials for every sub assembly. Show less
-
-
-
Nolato GW, Inc.
-
United States
-
Plastics Manufacturing
-
200 - 300 Employee
-
Quality Engineering Intern
-
May 2015 - Aug 2016
Over the past two summers I developed my skills (both analytical and interpersonal) as a quality intern working in the medical device sector at GW Plastics in Bethel Vermont. My first summer at GW Plastics I worked under a Quality Engineer performing: Gage R and R, First Article Inspections, Cross Qualifications, and Steel Validations. These tasks allowed me to familiarize myself with the following measurement devices: micrometers, radius gages, drop indicators, height gages, a comparator, vision systems, CMM programs, and multiple other devices. Minitab software was used to perform the required capability and equivalency tests. Performing these studies also allowed me to familiarize myself with the potential problems and root causes associated with the injection molding process. Daily machine inspections also provided experience with the electronic interface of Engel and Van Dorn molding machines. I was allowed to attend early stage design reviews where fixturing and measuring device selection were developed. As a result, I was responsible for designing a test fixture in CAD. Over winter break of 2015 I started a project that entailed processing client’s data from GW’s data base, and performing capability analyses in order to validate the manufacturing process over the entire history of a particular part. I also worked on this project during the spring semester and 2016 summer break due to the vast number of reports that needed processing. Show less
-
-
Education
-
University of Vermont
Bachelor's degree, Mechanical Engineering -
Randolph Union High School
Community
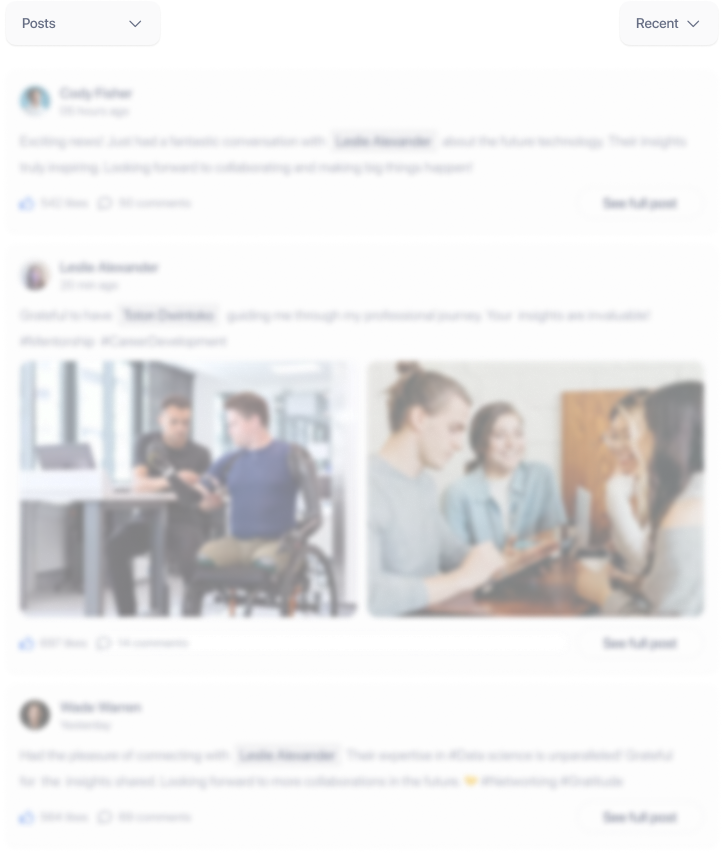