Lynne Smith
Engineering Analyst at BOOZ ALLEN HAMILTON ENGINEERING SERVICES, LLC- Claim this Profile
Click to upgrade to our gold package
for the full feature experience.
Topline Score
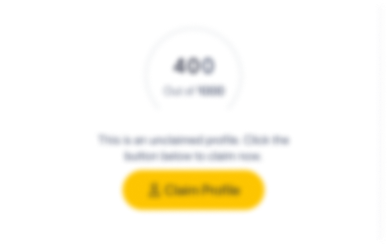
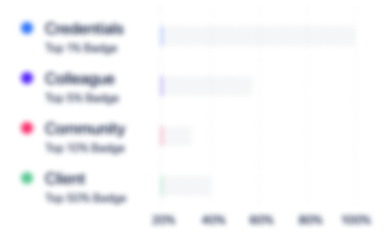
Bio


Experience
-
BOOZ ALLEN HAMILTON ENGINEERING SERVICES, LLC
-
United States
-
1 - 100 Employee
-
Engineering Analyst
-
Nov 2012 - Present
Provide organizational, technical, and administrative support to Director of Engineering, Program Managers, Quality Management, and Lead Engineers. Act as main point of contact and liaison with government Program Offices, Aircraft Integration and Materiel Personnel, and Configuration Management ensuring timely delivery of a quality product. Serve as Configuration Management Administrator, responsible for drawing and document deliveries in support of total delivery package. Maintain Configuration Management Database, track drawing and document deliveries, and initiate and implement Engineering Change Requests (ECRs). Prepare CDRL documentation package, strictly adhering to contract requirements and deadlines, with a strong emphasis on quality control. Prepare PDR/CDR presentation for delivery to government customer. Ensure all actions assigned during PDR are complete and updated information is provided for the final Critical Design Review. Prepare and maintain ERR (Engineering Release Record) and Engineer Change Proposal (ECP) for Federated Advance Navigation System (FANS) and UH-60N Conversion Program. Serve as AWBS (Automated Weight and Balance System) Operator. Prepare Weight and Balance Analyses and Reports. Research and verify part availability for MDW (Military District of Washington) sustainment program. Prepare Navy Technical Directive to serve as a Record of Purpose of Airframe Changes for delivery to government customer. Prepare and maintain Navy Technical Manuals as part of deliverable Logistics Package Supervise and document complete wire removal of MH-60S Navy Blackhawk for use in development of electrical installation drawing. Create Weight and Balance part lists and tables, using Sikorsky drawings, Navy Technical manuals, FedLog and IHS. Current position requires strict attention to detail and meticulous record keeping, following company AS9100 Quality Management System Guidelines.
-
-
-
Yulista Management Services
-
Business Consulting and Services
-
100 - 200 Employee
-
Project Coordinator
-
Jun 2008 - Nov 2012
Developed Rough Order of Magnitude (ROM) estimates for submission to Government Customer. Prepared and maintained program budgets and schedules. Responsible for documenting and tracking the delivery and receipt of official government document correspondence for Program Manager and Project Leads as part of an 8 person team. Scheduled and coordinated Program Management meetings, prepared bi-weekly IPT agendas and meeting minutes for submission to the government, and maintained Action Item Database. Established, updated, and maintained project schedule using Microsoft Project. Prepared and tracked Contract Data Requirements List (CDRLs) in compliance with current program Statement of Work (SOW). Worked with subcontractors to ensure Statement of Work (SOW) compliance. Updated Monthly Program Analysis (MPA) and Quarterly Internal Program Management Review (IPMR) for submission to Program Director. Performed research to develop spare and long lead item part lists for customer. Created Build of Material from engineering drawings. Interfaced with vendors and tracked delivery schedules. Generated quote requests and purchase requisitions. Resourceful and energetic in prioritizing work flow and assignments.
-
-
-
DS2
-
United States
-
Advertising Services
-
1 - 100 Employee
-
Production Control/Logistics Analyst
-
Mar 2006 - Aug 2007
Planned, prepared, issued, and controlled production schedules and material requirements for the Army’s Reset Program under the direction of AMCOM. Advised management of the status of work in progress, material availability, and potential production problems to ensure that personnel, equipment, materials, and services were provided as needed. Assisted Modification Work Order teams in the field to ensure modification kits were requisitioned and received, technical bulletins were provided, and accounted for all man-hours. Trained and experienced in all aspects of U.S. military aviation operational procedures, regulations, and documentation. Knowledgeable in the reset, phase and repair of the UH-60A/L Blackhawk, AH-64 Apache, OH-58D Kiowa and CH-47 Chinook helicopters. Maintained accurate man-hour records used to prepare Certificate of Service (COS)/DELTEK and DD 225 for billing purposes. Prepared status reports used by AMCOM to verify equipment, materiel and aircraft readiness. Coordinated 1st Article fit items; provided completion reports to QAR and DLA. Proficient with SAMS, FEDLOG, and ULLS-A(E).
-
-
-
L3 Vertex Communications
-
United States
-
Government Administration
-
1 - 100 Employee
-
Production Control/Logistics Analyst
-
Nov 2003 - Dec 2004
Worked as a Supply and Production Control Technician in support of the National Maintenance Program (NMP) Repair and Return Program (R&R) for Task Force AVCRAD. Advised management and customers on status of work in progress, material availability, and potential production problems. Trained and experienced in all aspects of U.S. military aviation operational procedures, regulations, and documentation. Knowledgeable in the reset, phase and repair of the UH-60A/L Blackhawk, AH-64 Apache, OH-58D Kiowa and CH-47 Chinook helicopters. Worked with the Supply Support Activity to ensure that repair parts were requisitioned and received to maintain aircraft fleet. Acted as liaison for contractor and military to resolve logistic problems and develop real time solutions to meet mission requirements. Performed as a technician within the Supply Support Activity using the Standard Army Retail Supply System (SARSS) to provide customer service for military aviation units transitioning to and from Iraq. Conducted reconciliations with Supply Support Activity to ensure 100% accuracy of all open and closed requisitions for repair parts.
-
-
-
-
Production Control/Supply
-
Jul 1999 - Jul 2002
Planned, prepared, issued, and controlled production schedules and material requirements for an intermediate level military aviation unit. Knowledgeable in the reset, phase and repair of the UH-60A/L Blackhawk, AH-64 Apache, OH-58D Kiowa and CH-47 Chinook helicopters. Interfaced with higher sources of supply to ensure critical parts were received in a timely fashion. Managed the work order evacuation process to higher echelons of maintenance with 100% accuracy. Ensured accurate accounting of all high dollar Depot Level Repair & Aviation Intensively Managed Items. Compiled daily, weekly, and monthly status reports to analyze maintenance and supply trends. Conducted reconciliation of all open and closed repair parts work orders with the Supply Support Activity through SARSS and SAMS generated reports. Processed requisitions and turn-ins for repair parts using manual and automated form DA 2765-1 with the Supply Support Activity. Received updates on status of repair parts from Supply Support Activity to maintain accuracy in SAMS database.
-
-
Education
-
Fayetteville State University
Bachelor of Science - BS, Psychology
Community
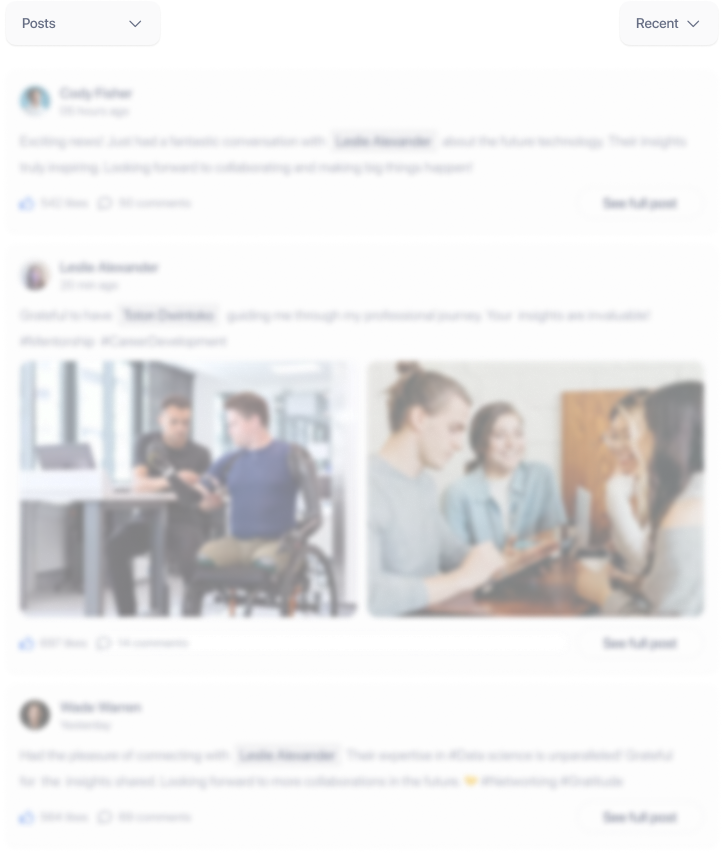