Luthfy Clarke
Quality Engineer at Libra Industries- Claim this Profile
Click to upgrade to our gold package
for the full feature experience.
Topline Score
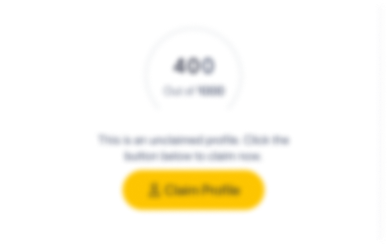
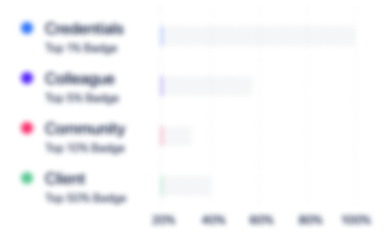
Bio


Experience
-
Libra Industries
-
United States
-
Appliances, Electrical, and Electronics Manufacturing
-
100 - 200 Employee
-
Quality Engineer
-
Nov 2021 - Present
• Performs root cause analysis, corrective and preventative action planning, execution, and verification • Supports Supplier Quality Engineer in supplier qualification and auditing. • Develops quality plans as required by customer and company requirements. • Develops and performs product inspection and testing. • Oversees complaint management, complaint trending, and analysis. • Performs process validation planning and execution, revalidation assessments in accordance with company, regulatory and customer requirements. • Coordinates equipment and facilities calibration and preventive maintenance. • Implements and trends manufacturing and quality system indicators (e.g., SPC, scrap trending, etc.) • Performs internal audits, as needed. • Identifies and coordinates with the Quality manager for Quality System Improvements. • Resolves Exception issues identified by production and inspection by verifying customer requirements and other needed documentation. Exception outcomes will be documented per company policy. This includes participation in the Material Review Board (MRB) in accordance with non-conforming product policy. • Maintains records in accordance with company policy, customer requirements and regulatory requirements. • Working with a major Semiconductor customer machine manufacturer, along with new product introduction. • Customer portal monitoring, review MN’s and report back to customer on findings. • Putting part TCD together for each Shipment, MRB reporting and disposal. Show less
-
-
-
Bullen Ultrasonics
-
United States
-
Aviation and Aerospace Component Manufacturing
-
1 - 100 Employee
-
Quality Engineer
-
Mar 2018 - Nov 2021
• Worked with silicone material product for Silfex, Lam Research, Admap and Tokai. • Interacted with external customer, resolved problems and non-conforming material disposition. • Determined material conformity going into production with the use of customer IP’s and drawings. • Prepared DECAR, scrap reporting, and operator training. • Pinned material analysis from external lab. • Worked with silicone material product for Silfex, Lam Research, Admap and Tokai. • Interacted with external customer, resolved problems and non-conforming material disposition. • Determined material conformity going into production with the use of customer IP’s and drawings. • Prepared DECAR, scrap reporting, and operator training. • Pinned material analysis from external lab.
-
-
-
Usui International Corporation
-
United States
-
Motor Vehicle Manufacturing
-
100 - 200 Employee
-
Quality Engineer
-
Oct 2011 - Mar 2018
• Developed and maintained all IATF 16949:2016 ISO 9001:2015 requirements. • Coordinated, maintained, and updated the quality system documents/records with other department managers in preparation for the audits and or other certifications. • Audited internal schedules as part of our Quality system requirements.• Promoted standardization and improvement of quality system by using control plans and specific customer requirements that will include establishing and revision of procedures, work instructions, checklists, training program, etc. • Provided training, guidance and professional support to new production operators and office staff of our Quality system (IATF 16949:2016 ISO 9001:2015 processes, company’s objectives and goals, 4S practice and methodology, etc.) to support product and process quality, productivity and continuous improvement. • Proactively assisted production and engineering team to resolve product or process issues using problem solving tools such as 8D, 5Why, seven steps, Fishbone diagram, etc. • Recommended, supported and implemented continuous improvement activities such as scrap reduction, process flow improvement, increase productivity, etc. This requires a good knowledge of lean manufacturing principles, value stream mapping, SPC, and six sigma methodologies. • Conducted internal and customer delegated source inspection activities to ensure compliance of quality requirements relating to customer and UIC specifications. • Assisted Quality Manager in improving product and processes to enhance or exceed internal and external customer expectations using continuous improvement tools and initiatives. This includes monitoring product quality by conducting capability process (PPM, CPK, etc.) and proper gauge assessment before production use. • Assisted and or lead cross functional team in developing and maintaining a defect prevention system through the use of PFMEA and other quality tools such as SPC, histogram, pareto chart, etc. Show less
-
-
-
F & P America Manufacturing Inc.
-
Troy, Ohio, United States
-
Quality Engineer
-
Nov 2009 - Sep 2010
• Confirmed parts layouts, read and interpreted blue prints, parts fixturing in the Stamping and Hydro-forming department. • Set up training and monitoring of internal and external sorts. • Led and presented 5P Corrective Action. • Performed root cause analysis of each defect internal or external. • Confirmed parts layouts, read and interpreted blue prints, parts fixturing in the Stamping and Hydro-forming department. • Set up training and monitoring of internal and external sorts. • Led and presented 5P Corrective Action. • Performed root cause analysis of each defect internal or external.
-
-
-
Neaton Auto Products, Mfg, Inc.
-
Motor Vehicle Manufacturing
-
200 - 300 Employee
-
Quality/Process/Warranty Engineer
-
May 2006 - Mar 2009
• Worked with Honda, Toyota and Nissan supply team for warranty root-cause analysis. • Counter measured implementation, to increase customer satisfaction and reduce warranty cost. • Used Honda/Toyota Portal in responding to customer concerns and countermeasure implementations. • Collaborated with customers - HCM, HMA, MAP, ELP, TS-Tech, American Honda, Nissan Tennessee, Nissan Mississippi, Nissan Technical center; Nissan quality lab and Toyota KY technical center. • Partnered with Neaton engineering, design dept., production, sale, procurement, M.I.S, technical lab, CMM, Rome GA, Mexico, Niplast Japan facilities and suppliers in various part of the world in resolving warranty issues. • Analyzed customer approval/agreement including: duplication of defects because of partial return components, print change, redesigning or getting the problem resolved and shipping new product to customer. • Warranty reduction/elimination project for steering wheel, airbags and several other components. Processed accounts receivables of money returned from the customer back to the company. • Involved in the product from design to launch, PCN, destruct testing, welds analysis, shainin technique, lab testing of return product, outsourcing testing. • Languages/translations and interfacing with other countries on video conferencing and telephones/emails.• Coordinated timely information from oversees’ suppliers and design changes initiates from Neaton for suppliers in other countries. • Advised accounting of what warranty claims to pay and not to pay. Negotiate with customers on warranty claim percentages base on data and findings. • Achieved warranty cost reduction by 23% • Improved overall customer satisfaction with less part change, less defective product pass on to customer. • Determined engineering change base on warranty analysis. Show less
-
-
Education
-
Madonna University
Masters Business Administration, Quality and Operations Management -
Texas A&M University
Bachelor of Science - BS, Economics
Community
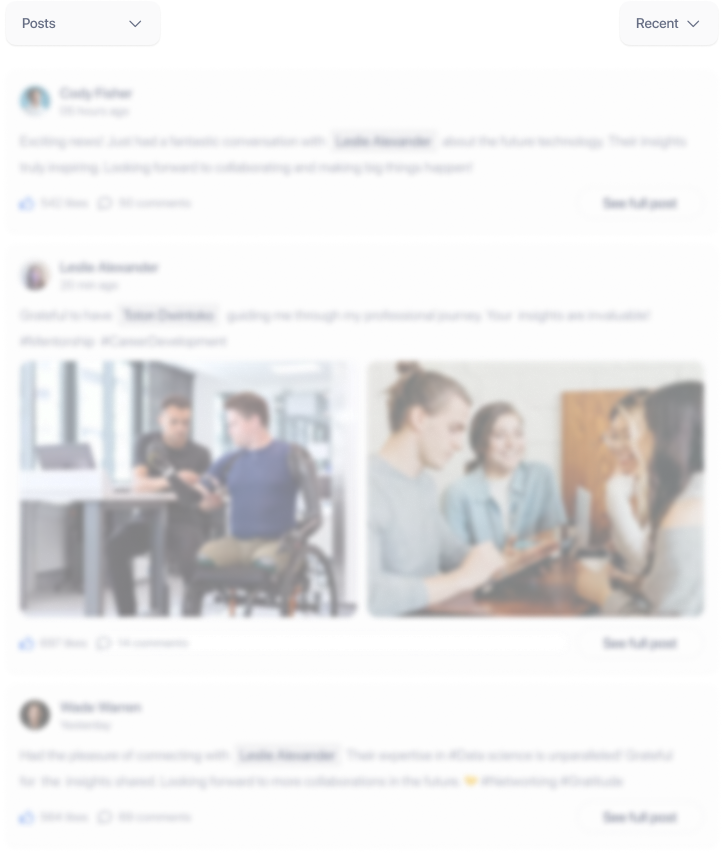