
Luciano Russo
Global Procurement and Planning at SM Jaleel & Company Ltd- Claim this Profile
Click to upgrade to our gold package
for the full feature experience.
-
Spanish Native or bilingual proficiency
-
English Native or bilingual proficiency
-
Portuguese Native or bilingual proficiency
Topline Score
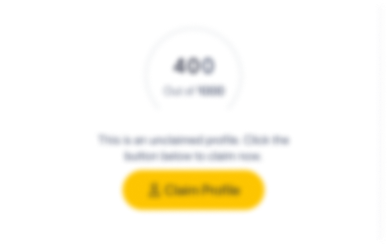
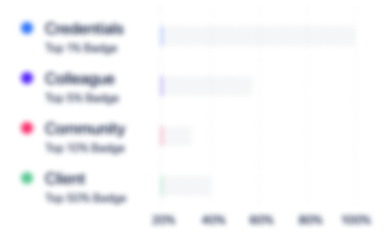
Bio

Kleber Nascimento Santos
Grande profissional!

Jose Martin del Campo
Luciano is a very well rounded Procurement professional, with high drive to transform Sourcing strategies into sound savings.

Kleber Nascimento Santos
Grande profissional!

Jose Martin del Campo
Luciano is a very well rounded Procurement professional, with high drive to transform Sourcing strategies into sound savings.

Kleber Nascimento Santos
Grande profissional!

Jose Martin del Campo
Luciano is a very well rounded Procurement professional, with high drive to transform Sourcing strategies into sound savings.

Kleber Nascimento Santos
Grande profissional!

Jose Martin del Campo
Luciano is a very well rounded Procurement professional, with high drive to transform Sourcing strategies into sound savings.

Experience
-
SM Jaleel & Company Ltd
-
Manufacturing
-
1 - 100 Employee
-
Global Procurement and Planning
-
Mar 2022 - Present
Leading the S&OP processResponsible for all the categories in Procurement (Directs and Indirect) and USD 650MM in spend.Accountable for MRP, MPS, Demand Planning and DistributionRestructuring the entire Procurement department implementing the category management, strategic sourcing methodologies and focused on indirect categories as well.Inventory reduction and optimizationActing strongly in change the way of working brings financial results for the local operations. Leading the S&OP processResponsible for all the categories in Procurement (Directs and Indirect) and USD 650MM in spend.Accountable for MRP, MPS, Demand Planning and DistributionRestructuring the entire Procurement department implementing the category management, strategic sourcing methodologies and focused on indirect categories as well.Inventory reduction and optimizationActing strongly in change the way of working brings financial results for the local operations.
-
-
-
DöhlerGroup
-
Germany
-
Food and Beverage Manufacturing
-
700 & Above Employee
-
Supply Chain and Procurement Head - America Latina
-
Dec 2018 - Mar 2022
227/5000Reporting to CEO and managing a team of 56 employees.Responsible for all the categories in Procurement (Directs and Indirect) and USD 500MM in spend.Leading the S&OP processAccountable for Demand Planning, MRP, MPS and Production Schedule for Brazilian’s plant (4 sites).Leading Logistics Department (intralogistics, DRP and warehousing)End to end distribution process managementIn charge of Raw material portfolio and data management team.Restructuring all the Procurement department, creating the indirect area and implementing the category management as well. Acting strongly in change the way of working bring financial results for the local operations.Part of government affairs committee - ABIA
-
-
-
Kerry
-
Ireland
-
Food and Beverage Services
-
700 & Above Employee
-
Procurement Director Latam
-
Nov 2017 - Aug 2018
Responsible for all the categories in Procurement (Directs and Indirect) and USD 500MM in spend.Restructuring all the Procurement department, creating the indirect area and implementing the category manages as well. Acting strongly in change the way of working bring financial results for the local operations. Responsible for all the categories in Procurement (Directs and Indirect) and USD 500MM in spend.Restructuring all the Procurement department, creating the indirect area and implementing the category manages as well. Acting strongly in change the way of working bring financial results for the local operations.
-
-
-
PepsiCo
-
United States
-
Food and Beverage Services
-
700 & Above Employee
-
Global Procurement Director - MSO
-
Oct 2015 - Jun 2017
Responsible for all categories of procurement with a Spend of R$ 2.2B.Leading a team of 45 people divided into direct and indirect materials, identifying opportunities that impact the company's NOPBT, increasing shareholder value while maintaining or improving the quality of products and services purchased.Acting as general manager's business partner in reducing fixed costs, lowering the break-even point, helping to improve profitability at the time of volume reduction. Responsible for all categories of procurement with a Spend of R$ 2.2B.Leading a team of 45 people divided into direct and indirect materials, identifying opportunities that impact the company's NOPBT, increasing shareholder value while maintaining or improving the quality of products and services purchased.Acting as general manager's business partner in reducing fixed costs, lowering the break-even point, helping to improve profitability at the time of volume reduction.
-
-
-
Coca-Cola FEMSA
-
Mexico
-
Food and Beverage Services
-
700 & Above Employee
-
Sourcing Head Sudamérica
-
Feb 2010 - Oct 2015
At Coca Cola Femsa I created the sourcing structure Sudamérica with Spend $ 5,000 MM and together with this team through strategic negotiations got 7% in Savings contributing significantly to improve EBITDA of the Division and transforming sourcing in a Business Partner of the operations. This process took place in three phases:Brazil centralization: Centralization of purchasing structure in an administrative office located in SP. In this process, we achieve an optimization of purchasing processes benefiting internal customers. In addition, we achieve TCO savings of $ 4MM.Mercosur Centralization: Design of a Mercosur procurement team covering operations in Brazil and Argentina, strategically negotiating the major categories of the business. Participating in the Business Plan meetings of these countries and influencing strategic decisions of investment and acquisitions. At this stage we segregate the roles of buyers, creating the roles of traders and buyers, the latter being responsible for the operational activities and the first by tactics ones. With this, and the negotiations of division strategic purchasing team, we reached USD 2.5 MM in additional savings.South America Centralization: Incorporation of Colombia and Venezuela in the Division purchasing team, contributing to better financial and operational results for the organization. Even in Coca Cola Femsa, I was responsible for develop and implement of a Business Intelligence department within the sourcing area which implemented a supplier development process in order to promote a rapprochement between suppliers, buyers and internal customers, recognize the best suppliers and through action plans and semiannual reviews, develop suppliers with growth potential partnerships. This team implemented a new system of Contract Management - South America optimizing the electronic approval and contract management earning 30% on time and 100% approval in advance before negotiations and due dates.
-
-
-
Avon
-
United Kingdom
-
Personal Care Product Manufacturing
-
700 & Above Employee
-
Sr. Regional Sourcing Manager
-
Sep 2004 - Feb 2010
• Participated actively in the implementation of the structure LATAM in Avon, as well as the redesign of the NPI purchasing structure Avon Mexico focusing on productivity gains, reduced costs and times to respond to internal clients (Based on Mexico City). • As Regional Manager of Raw Materials, I was the leader of a team that conducted strategic sourcing processes in various categories such as surfactants, esters and general chemicals bringing savings of more than USD 7 million.• Also participated as theme leader for LATAM, project Global Strategic Sourcing at Avon to reduce costs for the following areas: Telecom, Paper, International Logistics, IT with 10 MM USD savings.• As Senior Manager Regional Purchase of finished goods managed a team that implemented best business practices as well as the whole methodology of strategic sourcing with earnings of over $ 2MM. In addition, I developed the whole redesign the structure of regional purchases for non-cosmetics business
-
-
Senior Supply Chain Consultant
-
Sep 1997 - Sep 2004
• Responsible for production scheduling and master planning (MPS), material requirement plan (MRP), demand planning and distribution requirement plan (DRP).• Reduced inventory levels of finished products and raw materials due to optimization of the planning processes - Raw materials (MRP) and finish Good (MPS).• Processes improvement in DRP and demand planning.• Development and implementation of management reports to aid in decision-making and prioritization of products as well as reducing the cycle time of reprogramming.• Responsible for establishing metrics for the balance between the demands for sales of finished products, production thereof, and availability of inputs - S&OP implementation
-
-
-
-
Professor
-
Jan 1995 - Dec 1996
Classes in physics, chemistry, mathematics and science Classes in physics, chemistry, mathematics and science
-
-
Education
-
Fundação Getulio Vargas
MBA Financas, MBA -
Universidade de São Paulo
Master's degree, Business Administration and Management, General -
Universidade Paulista
Engenharia de Producao, University -
Colégio Bandeirantes
Colegial, High school
Community
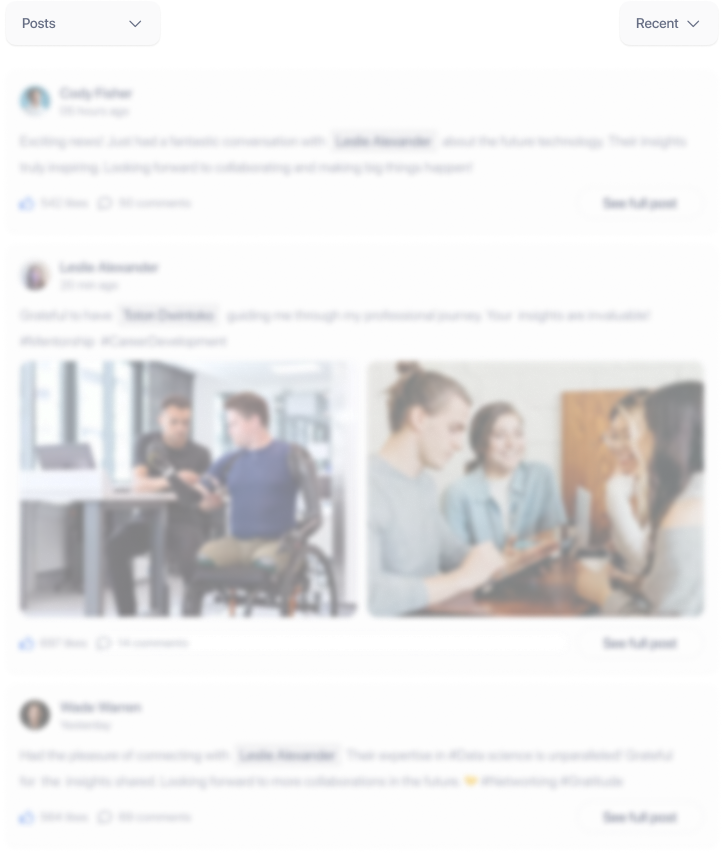