Lucas Machado de Oliveira
Operational Excellence Manager at Faculdade Unimed- Claim this Profile
Click to upgrade to our gold package
for the full feature experience.
-
Inglês Native or bilingual proficiency
-
Espanhol Professional working proficiency
Topline Score
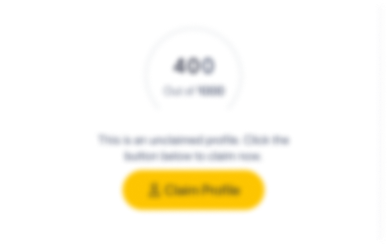
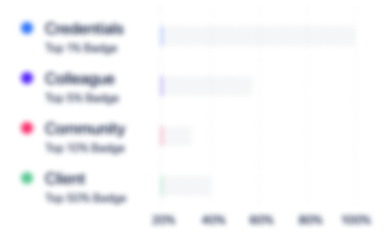
Bio

Barbara Santana
Lucas é um profissional muito competente, com muito conhecimento em Lean Manufacturing e gestão de equipe. Conta com alta produtividade no seu dia-a-dia além de ser bastante criativo e aberto a ouvir as ideias de outras pessoas. Meu período de trabalho com o Lucas foi de grande aprendizado, ele como gestor foi peça chave para minha formação, o considero como um mentor que me direcionou para as minhas tomadas de decisão e para solucionar dúvidas de trabalho.

Barbara Santana
Lucas é um profissional muito competente, com muito conhecimento em Lean Manufacturing e gestão de equipe. Conta com alta produtividade no seu dia-a-dia além de ser bastante criativo e aberto a ouvir as ideias de outras pessoas. Meu período de trabalho com o Lucas foi de grande aprendizado, ele como gestor foi peça chave para minha formação, o considero como um mentor que me direcionou para as minhas tomadas de decisão e para solucionar dúvidas de trabalho.

Barbara Santana
Lucas é um profissional muito competente, com muito conhecimento em Lean Manufacturing e gestão de equipe. Conta com alta produtividade no seu dia-a-dia além de ser bastante criativo e aberto a ouvir as ideias de outras pessoas. Meu período de trabalho com o Lucas foi de grande aprendizado, ele como gestor foi peça chave para minha formação, o considero como um mentor que me direcionou para as minhas tomadas de decisão e para solucionar dúvidas de trabalho.

Barbara Santana
Lucas é um profissional muito competente, com muito conhecimento em Lean Manufacturing e gestão de equipe. Conta com alta produtividade no seu dia-a-dia além de ser bastante criativo e aberto a ouvir as ideias de outras pessoas. Meu período de trabalho com o Lucas foi de grande aprendizado, ele como gestor foi peça chave para minha formação, o considero como um mentor que me direcionou para as minhas tomadas de decisão e para solucionar dúvidas de trabalho.

Credentials
-
Agile Discovery & Design
DesignThinkers AcademyJun, 2023- Oct, 2024 -
Management 3.0 Foundation Workshop Online
Management 3.0Mar, 2023- Oct, 2024
Experience
-
Faculdade Unimed
-
Brazil
-
Higher Education
-
100 - 200 Employee
-
Operational Excellence Manager
-
Jan 2023 - Present
Gerente de Excelência Operacional da Faculdade Unimed Gerente de Excelência Operacional da Faculdade Unimed
-
-
-
AngloGold Ashanti Brasil
-
Brazil
-
Mining
-
700 & Above Employee
-
Operations Management Manager
-
Apr 2022 - Jan 2023
Responsible for supporting operational units in Minas Gerais: - Definition and standardization of management routines - Support in the development of process improvements - Support in the scenarios of strategic decisions - Support in the consolidation of the strategic and budget planning process - Strategy execution follow up
-
-
Continuous Improvement Manager
-
Feb 2021 - Apr 2022
Responsible to start the implementation of continuous improvement at the site through training, kaizen projects, daily routines and improvement ideas; Also responsible for the data to build and consolidate the main KPI's and also the routines performance reports;- Responsible for the weekly and monthly Operational Performance Reports;- Site macro agenda and operational routines definition and organization;- Also, part of the Brazil team responsible to develop the Continuous Improvement part of the management system.- Active participation in the Strategic Options and Budget process Show less
-
-
-
Vallourec South America
-
Brazil
-
Oil and Gas
-
700 & Above Employee
-
Performance Team Leader
-
Jul 2020 - Feb 2021
- Responsible to manage and define the guidances in 6 Sigma, Kaizen and Improvement Ideas for South America- Responsible to organize the Continuous Improvement celebration ceremony - Responsible to manage and define the guidances and routines for the Cultural Transformation team (Workstream Leaders and areas)- Leader in the strategic development and deployment for Vallourec South America applying the Hoshin Kanri methodology
-
-
Senior Performance Engineer
-
Jan 2018 - Jun 2020
- Responsible to develop and consolidate the main department operational standards such as SMED (Single Minute Exchange of Die), Intensive Kaizen, FTE Analysis, Wrench Time;- Leader of the Office Lean pilot in the Account and Tax department- Responsible for the restructuring the “old” Suggestion Plan to a new on called Improvement Ideas- Part of the team which started the cultural transformation project first wave with Mckinsey team- Responsible to organize the Continuous Improvement celebration ceremony- Leader of a team of 3 performance engineers responsible to implement the operational daily routine part of the Management System around the units in South America in 4 months.- Responsible to manage and define the guidance’s in 6 Sigma, Kaizen and Improvement Ideas for South America.- Corporate Performance focal point in order to discuss and define the Group guidelines- One of the focal points during the Covid-19 Crisis Committee (Jan 20 to Jun 20)- Leader in the strategic board deployment for Vallourec applying the Hoshin Kanri methodology Show less
-
-
Lean Manufacturing Coordinator
-
Nov 2015 - Jan 2018
- Deploy and train managers, engineers, supervisors and operators in the Vallourec Management System - Support to implement the Group Lean Departments Guidelines and the Vallourec Management System deployment at the siderurgic area.- Train and develop one Jr. engineer to understand and to implement Vallourec Management System and it's tools.
-
-
Lean Manufacturing Coordinator
-
Apr 2015 - Nov 2015
- Help the creation and consolidation of the Lean Department at VSB.- Work with Mckinsey team in the transforrmation project that was launched for the entire Vallourec Group. - Participate and conduct several workshops to generate ideas to improve the plant performance and achieve the group objectives.
-
-
Lean Manufacturing Engineer
-
Oct 2011 - Apr 2015
-VMS ( Vallourec Management System), developed by Vallourec as a new management culture based on Lean Production principles. Acting as an internal consultant the VPA (VMS Performance Analyst) is responsible for deploying Lean Management techniques in the different areas of the company, while developing key personnel in the areas to maintain the new culture.This support is given in the form of:- 5 day training on lean principles for managers, engineers and supervisors.- Methodology consultancy, guaranteeing that DMAICs is always respected, and that all new process designs follow Lean principles.- Conduction of Kaizen weeks (blitz), where a problem is intensively analyzed by a multi-functional team and solutions proposed are implemented to obtain a rapid and relevant change on the root causes of the problem defined.- Support development and advancement of lean implementation.During my development as a VPA, I took part in different Kaisen blitz, first as a participant and later as the leader. The subjects varied between 5S, process standardization, SMED, flow implementation, process design, autonomous maintenance, between others.-Since I have been working at this position for almost 4 years, I've participated in various strategic projects such as the two successful projects at the Threading Lines and at the Rolling Mill. Show less
-
-
Quality Control Intern
-
Jan 2011 - Oct 2011
- Follow up the quality KPI that belongs to the Plug Mill.- Follow up the Continuous Improvement Team's working in the Plug Mill quality area .- Development of a benchmarking study to analyze and understood the requirements and indicators needed to guarantee the quality at the Plug Mill area.
-
-
Education
-
PUC Minas
MBA em Gestão de Projetos Ágeis, Business Administration and Management, General -
PUCRS - Pontifícia Universidade Católica do Rio Grande do Sul
Master of Business Administration - MBA, Management, Entrepreneurship and Marketing -
Pontifícia Universidade Católica do Rio Grande do Sul
Competências Profissionais, Emocionais e Tecnológicas para Tempos de Mudança, Produtividade -
Universidade Federal de Ouro Preto
Industrial Engineer, Engenharia de Produção -
Colégio Magnum Agostiniano - Buritis
-
Liceu Santa Maria Imaculada
Community
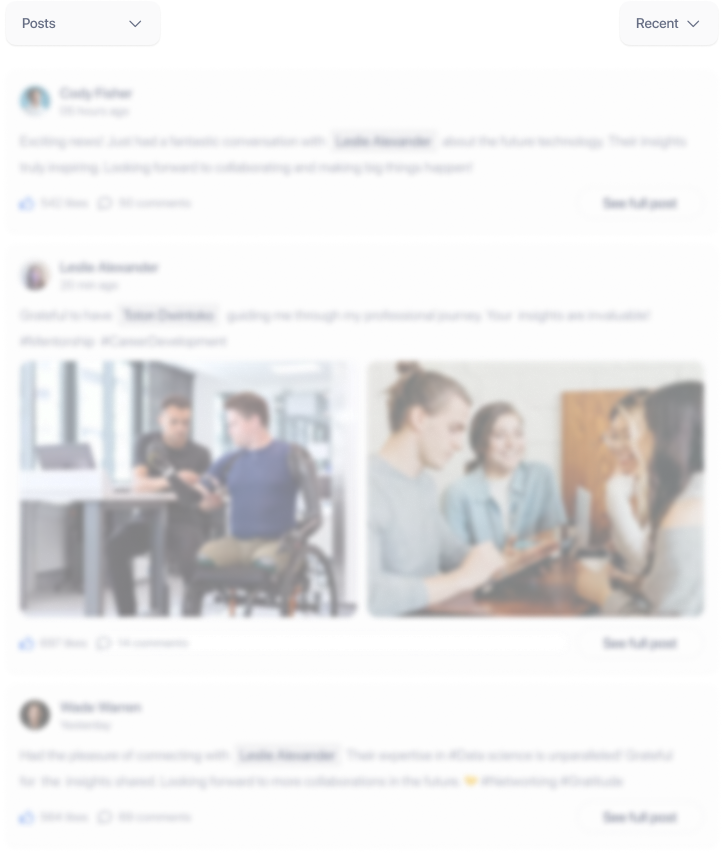