Lucas Layher
Distribution Center Manager at Bell’s Brewery- Claim this Profile
Click to upgrade to our gold package
for the full feature experience.
-
English -
Topline Score
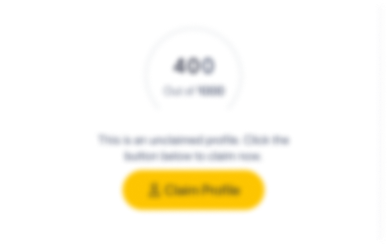
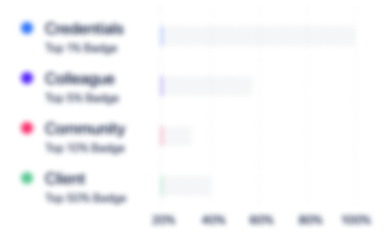
Bio


Experience
-
Bell’s Brewery
-
United States
-
Food and Beverage Services
-
100 - 200 Employee
-
Distribution Center Manager
-
May 2023 - Present
-
-
-
Anheuser-Busch
-
United States
-
Food and Beverage Services
-
700 & Above Employee
-
Business Process Manager I, Warehouse
-
Jun 2021 - Feb 2022
• Managing a team comprised of 3 salaried warehouse group managers, three contractor services, and 60+ hourly team members in a high-performing 24/7 manufacturing environment responsible for shipping out roughly 9,000,000 barrels of beer a year.• Responsible for monitoring and process improvement of area KPIs around loading cycle time, optimization of shipment weights, and labor management on a variable flex labor budget. Implemented change that reduced live load on-premise time by ~14%• Organized monthly full packaged goods counting. Held responsibility for the reconciliation of these counts, comparing our Warehouse Management System, SAP, and brewery production database (IMS) to investigate and rectify discrepancies.• Brewery subject-matter expert for our proprietary Warehouse Management System (WMS). Show less
-
-
Business Process Manager I, Capabilities
-
Apr 2021 - Jun 2021
• Responsible for the overall training and development for all team members within the brewery.• Conducted structured interviews for the newly created hourly Training Coordinator position, and was charged with defining and training the roles and responsibilities of the position. After successfulimplementation of this role, a second Training Coordinator was hired to further improve routines.• Brewery SPOC for the management portion of Voyager-Plant-Optimization (VPO), the sustainability and improvement model used by all Anheuser-Busch InBev facilities. Show less
-
-
Business Process Manager II, Warehouse
-
Feb 2021 - Apr 2021
• Trained team members in 5-Why problem solving methodology, and lead small group problem solving sessions on each shift within the warehouse. The goal of these groups was to upskill team members and focus on implementation of process improvements from the analysis done in these meetings.• Managed weekly manpower allocation for all logistics personal.
-
-
Logistics Planning Group Manager
-
Jun 2020 - Feb 2021
• Managed brewery short-term production schedule for 4 can lines, 3 bottle lines, and a draft line, requiring use of INFOR ERP software. • Responsible to align the often-conflicting needs of the brewing, packaging, warehousing, 3rd party material vendors, and Zone logistics teams into one efficient schedule to meet customer demand.• Created and maintained brewery primary material delivery schedule in SAP. Also used SAP to manage the physical inventory for these assets through monthly cycle counts and responsible for month-end reconciliation meeting Sarbanes-Oxley (SOX) requirements. Show less
-
-
Warehouse Group Manager
-
May 2019 - Jun 2020
• Worked autonomously through off-shift and weekend coverage where I was the sole on-site logistics contact for the brewery, multiple contractor groups, as well as the hourly warehouse team members.• Lead the rollout of the Operator Work Station in the Warehouse. This included structuring the tool for Fort Collins specific needs using team member guidance and training team members in small groups following the train, coach, execute, audit format.
-
-
Utilities Group Manager
-
Aug 2018 - May 2019
-
-
Brewery Trainee
-
Jun 2018 - Aug 2018
-
-
-
Nestlé
-
Switzerland
-
Food and Beverage Services
-
700 & Above Employee
-
Operational Managment Trainee Intern - Industrial Performance
-
May 2017 - Aug 2017
• Led a cross functional team to reduce stoppages and build operator autonomy on a top loss piece of equipment. A 12.4% reduction in time loss resulted, which yields $66,656 in average annual savings. • Used operator experience, data analysis and collections tools, and cumulative product projections to build justification for a $50,000 capital improvement to the line. • Reviewed equipment standards and worked with subject matter experts to compile a best-practices reference to eliminate variation between operator performances. Show less
-
-
-
Pfizer
-
Kalamazoo, Michigan
-
Drug Products Intern
-
May 2016 - Aug 2016
• Developed an inventory list and parts retirement program for the 4000+ parts that circulate through the sterile filling line to increase efficiency and reduce downtime caused by out of specification equipment. • Created an electronic database for the tracking of equipment, in compliance with sterile environment standards, as part of a 4-member team. • Received Six Sigma Method 1 Training to enhance my leadership and problem solving skills. Using these tools, I co-lead two Method 1 investigations. • Received training in sterile environment gowning, operations, and protocol. Show less
-
-
-
Molecular and Organic Excitonics Laboratory
-
East Lansing, Michigan
-
Undergraduate Research Assistant
-
Sep 2014 - May 2016
• Performing research into Organic Light Emitting Diodes (OLEDs) under the direction of Dr. Richard Lunt and a collaboration of graduate and undergraduate students. • Designing and testing new procedures for utilizing materials of interest in devices. • Refining my ability to read, comprehend, and discuss scientific articles and research. • Performing research into Organic Light Emitting Diodes (OLEDs) under the direction of Dr. Richard Lunt and a collaboration of graduate and undergraduate students. • Designing and testing new procedures for utilizing materials of interest in devices. • Refining my ability to read, comprehend, and discuss scientific articles and research.
-
-
-
Consumers Energy
-
United States
-
Utilities
-
700 & Above Employee
-
Cooperative Student
-
Jun 2012 - Aug 2014
• Experience in calibrations of various electrical measuring devices, as well as a multitude of metallurgical evaluation and testing methods. • Enhanced abilities in how to network and communicate in a professional setting, whether in person or over electronic communications. • Experience in calibrations of various electrical measuring devices, as well as a multitude of metallurgical evaluation and testing methods. • Enhanced abilities in how to network and communicate in a professional setting, whether in person or over electronic communications.
-
-
Education
-
MIT Professional Education
Certificate, Applied Data Science -
Michigan State University
Bachelor of Science - BS, Chemical Engineering -
Northwest High School
General Eduation, 4.0
Community
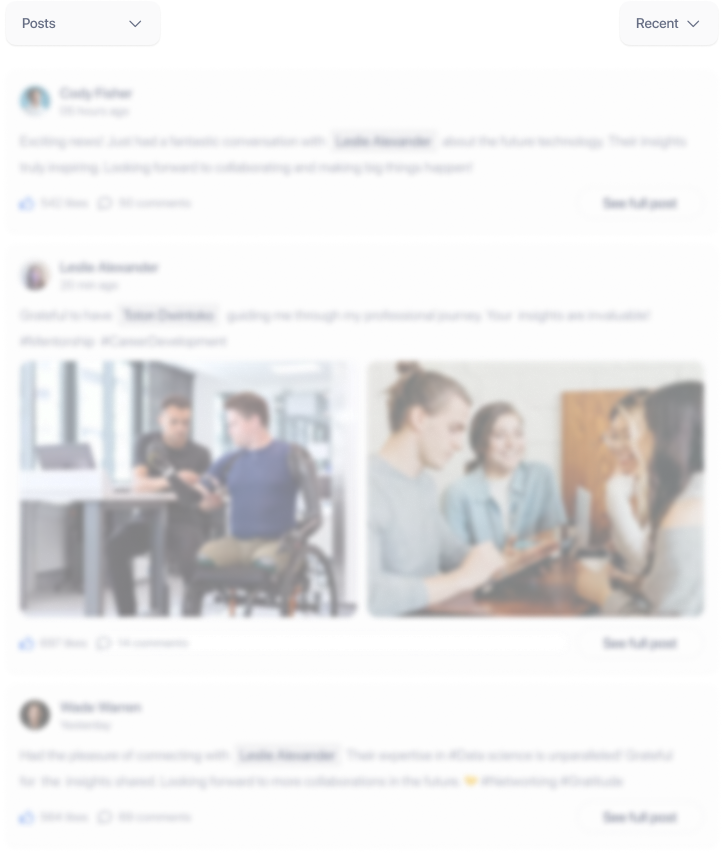