Louis Leon III
Director Of Manufacturing at FONA International- Claim this Profile
Click to upgrade to our gold package
for the full feature experience.
-
Spanish -
Topline Score
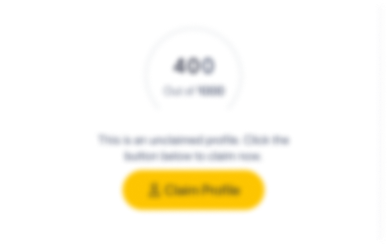
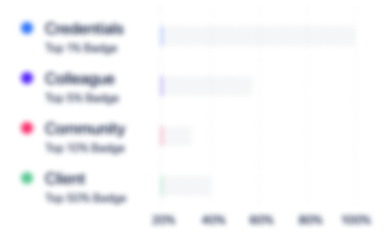
Bio


Credentials
-
HACCP
International Alliance - HACCPAug, 2014- Nov, 2024
Experience
-
McCormick FONA
-
United States
-
Food and Beverage Services
-
100 - 200 Employee
-
Director Of Manufacturing
-
Jun 2018 - Present
-
-
-
Terri Lynn Fundraising
-
United States
-
Fundraising
-
1 - 100 Employee
-
Plant Manager
-
Oct 2017 - May 2018
A disciplined Plant Manager that assesses process capability, improving process control and instill a culture of accountability. Engendered and Cultivated a work force that put the safety and welfare of all employees ahead of all other goals. Monitored Leading and lagging indicators needed to manage and link actions that reduced risk in the workplace. Developed manufacturing operating plans in accordance with company policies, goals, and objectives. Accountable for leading Manufacturing, environment, health and safety, quality, sanitation, and maintenance to achieve business objectives including meeting customer requirements and achieving financial objectives. Champions a clear channel of communication and coordination between functional counterparts in business units. Show less
-
-
-
Cheese Merchants of America
-
Bartlett
-
Plant Manager
-
Sep 2013 - Oct 2017
Oversee rapid expanding processing plant implementing strategy, lean process techniques while driving Continuous Improvement in a constant evolving environment. Trained and mentored growing plant from 40 to 220 full time employees within18 month time frame. Direct all facets of operations from Production, Shipping/Receiving, Human Resources, Maintenance, Quality, and Quality Control. Directly responsible for costs associated to operating payroll and capitol expense projects. Reduced payroll operating costs by 25% through developing job descriptions and designating "most qualified" employee for position. Developed Safety LOTO programs, Disciplinary procedures, Quality Control Process, and Streamlined Production Processes utilizing Process mapping. Established several recycle programs at Cheese Merchants that categorized plant as a Zero Waste Facility. Developed Forecast Demand module that enabled us to forecast customer demands resulting in scheduling to minimize waste in changeovers/product poilage. Show less
-
-
-
Ampac Packaging
-
United States
-
Packaging & Containers
-
1 - 100 Employee
-
Department Manager
-
Oct 2012 - Sep 2013
Manage daily operations in Press, Laminating, and Slitting departments, Develope and Benchmark SOP's and training procedures for processes, Coordinate production shift start-ups, shutdowns, and changeovers, Schedule and conduct shift meetings, Participate in the recruiting/hiring process, Work directly with technical and quality assurance to develope root cause analysis and corrective action measures for product rejects. Manage daily operations in Press, Laminating, and Slitting departments, Develope and Benchmark SOP's and training procedures for processes, Coordinate production shift start-ups, shutdowns, and changeovers, Schedule and conduct shift meetings, Participate in the recruiting/hiring process, Work directly with technical and quality assurance to develope root cause analysis and corrective action measures for product rejects.
-
-
-
JMFG - Smithfield Foods
-
Food and Beverage Manufacturing
-
700 & Above Employee
-
Production Supervisor
-
Aug 2011 - Jan 2013
Cross-trained in all departments to effectively develope action plans for issues relating to staffing, product out of spec, process improvement, and line efficiencies, assured compliance with safey and health regulations and good housekeeping practices within assigned areas by conducting monthly audits, supervisor 30+ union employees while setting production goals daily. Cross-trained in all departments to effectively develope action plans for issues relating to staffing, product out of spec, process improvement, and line efficiencies, assured compliance with safey and health regulations and good housekeeping practices within assigned areas by conducting monthly audits, supervisor 30+ union employees while setting production goals daily.
-
-
-
U.S. Masonry, Inc.
-
Greater Chicago Area
-
Field Superintendent
-
Sep 2002 - Jul 2011
Ran field operations and manufacturing plants. Oversee about 80 employees in a union setting. Ran field operations based on prints and architectural designs. Ran field operations and manufacturing plants. Oversee about 80 employees in a union setting. Ran field operations based on prints and architectural designs.
-
-
Education
-
Keller Graduate School of Management
Master of Business Administration (M.B.A.), Business Operations Management -
Nova Southeastern University
Master of Business Administration (M.B.A.), Operations -
Jacksonville University
Bachelor's degree, Business, Management, Marketing, and Related Support Services
Community
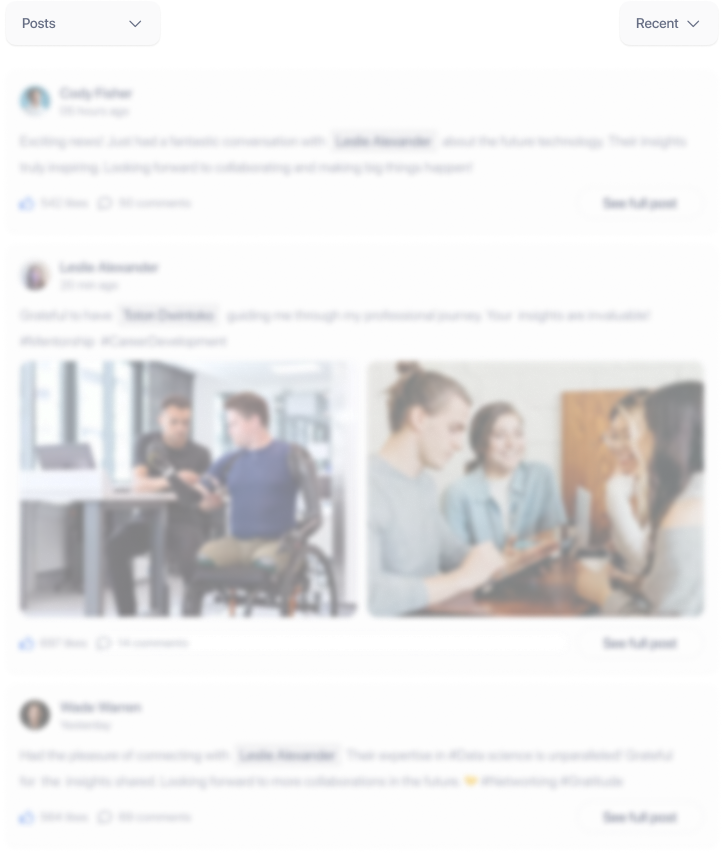