Loryn Magdaleno-Schroeder
Quality Assurance Technician Lead at Romac Industries, Inc.- Claim this Profile
Click to upgrade to our gold package
for the full feature experience.
Topline Score
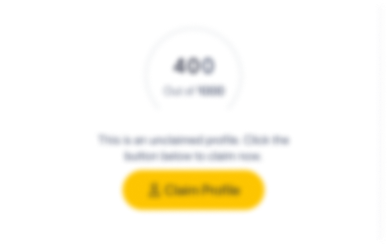
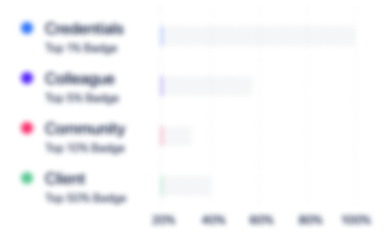
Bio


Experience
-
Romac Industries, Inc.
-
United States
-
Wholesale Building Materials
-
100 - 200 Employee
-
Quality Assurance Technician Lead
-
Jan 2023 - Present
-Manages the day to day delegation for the inspection team-Responsible for the training and development of new and current inspectors-Creates and monitors logs for better documentation of daily inspections-Purchases supplies for the inspection team-Assists SQE with monitoring, logging and inspection of incoming supplier product. -Responsible of overseeing the inspection of returned customer overstock products. -Trained in basic calibration and logging of gauges used in the warehouse. -Responsible for writing and documentation of current and newer inspection procedures. -Reports any non conforming parts to engineering and helps assist in root cause analysis. -Backup assistance for the QA supervisor when needed. Show less
-
-
Quality Assurance Technician II
-
May 2021 - Apr 2023
-Performs repetitive inspections following standardized methods and procedures-Inspects or checks parts using a variety of precision measuring instruments or against fixed samples-Check dimensions and finishes against blueprint or work order specifications-Specialized in receiving inspection processes-Leveraged standardized Quality Assurance methods and established best practices to perform repetitive inspections and assessments-Reviews material test reports (MTRs) supplied with raw material or components and confirm they match applicable standards and/or requirements-Performs basic root cause analysis on assigned materials and work with Engineering and Purchasing to confirm materials are usable-Leverages a working understanding of Oracle materials management software to electronically record receipt of materials into system-Logs materials from outside processing back into DBR scheduling system-Delivers materials to predetermined locations throughout the plant, typically using a reach truck, forklift, and/or electric pallet jack-Enters material variance data to the Material Conformance Report (MCR) system-Performs outgoing inspection of finished goods, including dimensional, welds, finish, markings, and component configurations, typically using visual inspection methods and simple tools-Performs weekly process audits in various production departments-Drafts and distribute audit reports to share quality status-Entered data into established databases and run standard reports-Works with more senior level technicians and engineers on in-process product inspections and vendor qualifications/first article inspections-Completed Hazardous Waste Materials training and adhere to guidelines Show less
-
-
-
ENOVIX Corporation
-
United States
-
Appliances, Electrical, and Electronics Manufacturing
-
100 - 200 Employee
-
Test Engineering Technician
-
Mar 2019 - Mar 2021
-Responsible for running batteries through various tests using Kinte, Maccor, and Arbin testing software. -Trained in basic battery function and safety. -Navigates daily correspondence between departments/engineers/ops regarding the daily Test duties. -Collects and interprets data for projects, dispositions cells, and proceeds with experiments accordingly. -Works with engineers to develop safer and more ergonomic tools for operators. -Helps formulate & implement better lab organization systems (ex. filing, labeling, archiving, etc.). -Trained in X-Ray safety and operation. -Trained new hires in Test procedures and safety. -Able to run Test Lab alone or with a team depending on staffing and workload. -Keeps track of alerts on Slack to better keep track of cell issues. -Performed some basic battery assembly tasks as needed. -Uses calipers, micrometers, and company made tools to measure products to ensure quality and specifications. -Entered data on spreadsheets and company made web uploaders. -Trained new hires in the Test department -Monitored batteries throughout the testing process and dispositioned accordingly based on data. -Facilitated a Kaizen 5S organization event in the Test Lab -Wrote and updated work instructions -Prepared batteries for customer shipment and performed final quality control checks. -Helped create an updated filing system for testing paperwork -Trained in and helped organize a safe waste disposal system for scrapped parts Show less
-
-
-
Adient
-
United States
-
Motor Vehicle Manufacturing
-
700 & Above Employee
-
Quality Control Inspector
-
May 2018 - Nov 2018
-Responsible for quality inspection of pre production parts for defects -Trained in inspecting multiple different lines of production. -Trained in proper warehouse safety procedures. -Collected and submitted data regarding inspections to upper management following each shift -Maintained communication between engineers and product leads regarding defects -Comfortable using various equipment and gauges for inspection purposes. -Followed quarantine procedure for inventory when defects were present. -Certified to train new hires. -Monitored in-house part inventory for accurate counts. -Loaded passing parts into containers for pick-up and shipping. Show less
-
-
-
Amazon
-
United States
-
Software Development
-
700 & Above Employee
-
Fulfillment Associate
-
Apr 2018 - May 2018
-Responsible for sorting packages to ensure they are placed on the correct delivery pallet -Trained in proper warehouse safety -Inspected outgoing packages for damage or defects and sorted them accordingly. -Used RF scanner to track packages and pallets -Trained in Amazon RF scanner interface -Wrapped up pallets for delivery -Assisted in re-packaging damaged packages -Moved pallets via pallet jack to the proper loading dock -Assisted in clean up and prep for the next shift Show less
-
-
-
Starbucks
-
United States
-
Retail
-
700 & Above Employee
-
Shift Supervisor
-
May 2014 - Oct 2017
-Learned all current and prior menu items, as well as associated brands. -Promoted to shift supervisor after one year of employment. -Gained knowledge of newer forms of taking inventory. -Preformed cycle counts as well as daily, monthly and yearly physical counts -Learned how to read an follow a plan-a-gram (product display outline) -Was responsible for setting up seasonal & promotional plan-a-grams unassisted. -Trained in managerial cash handling and safe procedures. -Certified to train new hires. -Trained for and successfully tested into the Coffee Master program. -Helped plan a better store organization system. -Responsible for organizing daily shipments and ensuring quality of delivered items. Show less
-
-
-
Jamba
-
United States
-
Food and Beverage Services
-
700 & Above Employee
-
Shift Lead
-
Mar 2013 - Mar 2014
-Quickly learned all current and prior menu items. -Promoted to shift lead after six months of employment -Trained in store opening and closing procedures. -Gained knowledge of eRes inventory system, as accurate data entry. -Trained in Kronos to help monitor labor hours. -Took daily physical inventory and trained to perform cycle counts. -Certified to train new hires. -Quickly learned all current and prior menu items. -Promoted to shift lead after six months of employment -Trained in store opening and closing procedures. -Gained knowledge of eRes inventory system, as accurate data entry. -Trained in Kronos to help monitor labor hours. -Took daily physical inventory and trained to perform cycle counts. -Certified to train new hires.
-
-
-
McDonald's
-
United States
-
Restaurants
-
700 & Above Employee
-
Crew Member
-
Jul 2012 - Mar 2013
-Trained on McDonald’s custom POS system. -Able to retain recipe knowledge of products offered at location. -Trained in and preformed morning inventory counts. -Learned to work quickly and efficiently in an extremely fast paced environment. -Trained on McDonald’s custom POS system. -Able to retain recipe knowledge of products offered at location. -Trained in and preformed morning inventory counts. -Learned to work quickly and efficiently in an extremely fast paced environment.
-
-
-
Dickey's Barbecue Restaurants, Inc.
-
United States
-
Restaurants
-
500 - 600 Employee
-
Cashier
-
Mar 2009 - Dec 2010
-Learned proper cash handling procedures. -Trained on Aloha POS register systems and customer service etiquette. -Gained knowledge of basic food preparation and order preparation. -Assisted with preparation for large catering orders. -Learned proper cash handling procedures. -Trained on Aloha POS register systems and customer service etiquette. -Gained knowledge of basic food preparation and order preparation. -Assisted with preparation for large catering orders.
-
-
Education
-
Academy of Art University
Motion Pictures and Television -
Ohlone College
General Education
Community
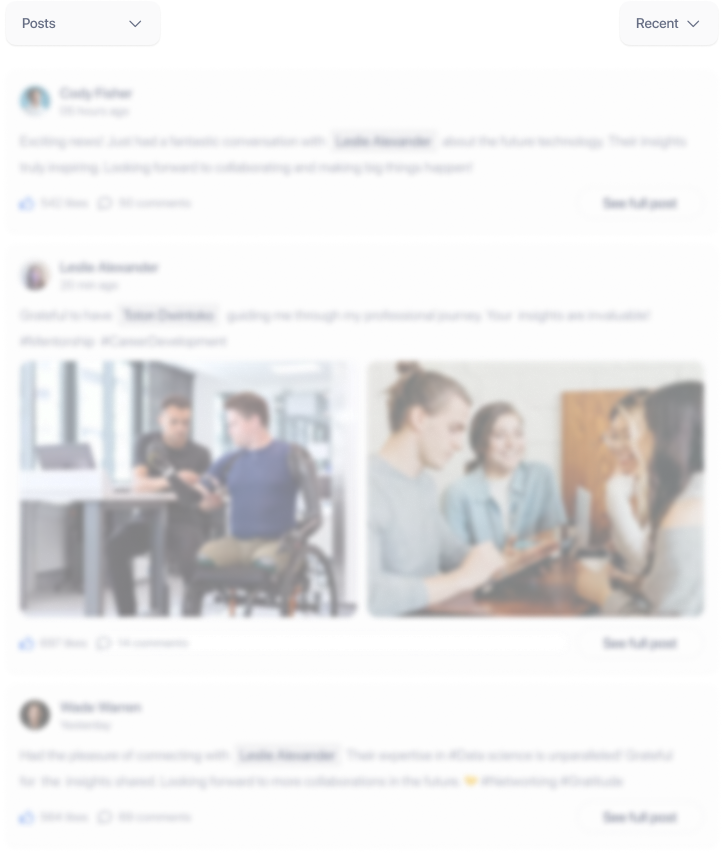