Lori Nichols
Assistant Chief at Va Montana Healthcare Systems- Claim this Profile
Click to upgrade to our gold package
for the full feature experience.
Topline Score
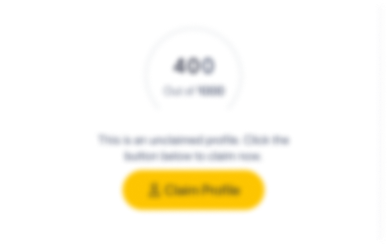
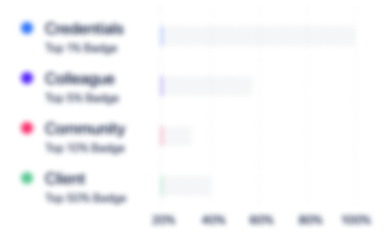
Bio


Experience
-
Va Montana Healthcare Systems
-
United States
-
Wellness and Fitness Services
-
1 - 100 Employee
-
Assistant Chief
-
Mar 2018 - Present
• Managing of all SPS processes completed in the decontamination, instrument preparation and sterilization, and endoscopic equipment reprocessing units associated with SPS. • Designated as the statewide Reusable Medical Equipment (RME) coordinator. • Responsible for the organization and management of the SPS Section, exercising supervisory authority over Medical Supply Technicians (MST) and a Supervisory Medical Supply Technician. • Serves as a technical and program advisor and consultant to management including RME oversight, the reprocessing of surgical instrumentation, patient care equipment, and other related equipment and throughout he Medical Center. • May fill the role of Acting Chief SPS in the absence of the SPS Chief making decisions that are in the best interest of the SPS organization and medical center. • Supervises technicians and directs the activities of non-supervisory employees whose duties are to procure, receive, decontaminate, sterilize and prepare for distribution, of all instrumentation and patient care equipment, • Ensuring the availability of a large number of medical and surgical equipment processed and distributed throughout the medical center. • Determining priorities, establishing appropriate levels, determining reorder frequencies, reprocessing schedules and managing procurement activity. • Maintaining an in-depth knowledge of overall SPS total support programs to maintain the availability of care to the veteran patients. • Designated as the Censitrac super user for the SPS department. • Responsible for the Censitrac marking of all new instruments received in the facility. • Marinating the database for the Censitrac program. • Responsible for maintaining and procuring items listed on Special Purpose Funding listing as funds become available. • Responsible for the ordering of supplies needed in the SPS department for daily operations. Show less
-
-
-
Salem VA Medical Center
-
Salem Virginia
-
Supervisor SPS
-
Mar 2015 - Mar 2018
• Function as supervisor for Sterile Processing Service (SPS), furnishing the medical center with reusable medical equipment, surgical instruments and other related materials for use by clinical staff in fulfilling patient care responsibilities. • Train all staff within SPS on receiving, decontaminating, cleaning, disinfecting, and sterilizing of reusable medical equipment. • Assume accountability for instrumentation utilized by clinicians, ensuring appropriate function and operation of equipment utilized in the cleaning and sterilization process such as ultrasonic cleaner, washer disinfector, automatic endoscope reprocessors, Sterrad Plasma, and steam sterilizers. • Track, trend and manage costs regarding reusable medical equipment. • Assign work to be accomplished by medical supply technicians. • Monitor working conditions such as seating, ventilation, lighting, safety, etc. • Provide advice, counsel, or instruction to employees on both work and administrative matters. • Issue minor disciplinary measures, such as warnings and admonishments for employees directly under my supervision and recommends more serious cases to higher authority. • Initiate projects to develop better processes and create better efficiencies. • Implement infection control policies and procedures for the sterile processing service section and ensure that written procedures are being followed. • Function as the Automated Data Processing Application Coordinator (ADPAC) for SPS. • Co-Chairman of the EEO Committee. • Function as Time Certification Official for SPS. • Oversee instrument tray audit program. • Oversee Instrument Repair program for SPS. • Function as Chief SPS in his absence. • Designated departmental “Super User” for Censitrac system Show less
-
-
-
Willis Knighton Medical Center North
-
Shreveport Louisiana
-
Sterile Processing Technician
-
Feb 2013 - Mar 2015
• Ability to rotate assignments among the various areas: sterilization, processing, decontamination, surgical tray assembly, reusable inventory, medical equipment processing and quality assurance functions. • Collection, receipt, inspection and decontamination processing of soiled supplies, instruments, equipment, and apparatus including complex diagnostic equipment and medical apparatus. • Completely and thoroughly dissembling all parts of technical reusable medical equipment (RME) to ensure the removal of bio-burdens prior to sterilization. • Operating decontamination equipment such as washer decontaminators, sonic washers and laparoscopic insulation tester. • Validating all cleaning of instrumentation and RME using department Standard Operating Procedures and manufacture guidelines. • Performing inspection, assembly, packaging, and terminal sterilization of all trays, sets, and packs for use throughout the medical center. • Determining the criticality category of RME using the Spaulding Classification System and interpretation of sterilization parameters provided by manufacturer guidelines to determine the proper method of sterilization. • Operating sterilization equipment such as Steam Sterilizers, Sterrad, Sterrad NX, VPRO Maxx sterilizers, ETO sterilizers, heat sealers, tube dryers, and biological incubators. • Troubleshooting complex sterilizers used in the medical center to ensure optimal operation. • Assembling minor and complex tray sets and instrumentation packs used for a variety of general and specialized medical and surgical procedures and surgical case carts. • Experienced in the cleaning, packaging and sterilization of DaVinci Robotic surgical instruments. Show less
-
-
-
Overton Brooks VA Medical Center
-
Shreveport Lousiana
-
QA Specialist Sterile Processing
-
Nov 2012 - Mar 2015
• Monitoring specialist for all Quality Assurance (QA) activities of the Sterile Processing Services (SPS) Section and all other areas in the facility where reprocessing of reusable medical equipment (RME) takes place. • Monitoring work performed in Decontamination, Processing, Instrument Preparation, Operating Room Core Area, Distribution, and case cart operations, as they relate to support of the OR and all other areas in the facility where reprocessing of RME takes place. • Responsible for monitoring of documentation as it relates to the functions of SPS, training of competencies and Standard Operating Procedures (SOP’s), and reports presented at monthly at RME Committee meetings. • Serve as direct liaison with Surgical Service and all other areas in the facility where reprocessing of RME takes place. • Provide Quality Assurance monitoring for the cleaning/decontamination, sterilization, reprocessing, and distribution of surgical instruments and technical medical equipment processed in SPS and throughout the facility. • Reviewing completed work to ensure that supervisor's instructions on work sequence, procedures, methods and deadlines have been met as deemed appropriate to assess the quality and quantity of work produced by each employee. • Monitoring customer satisfaction with services provided by SPS utilizing Voice of the Customer Survey. • Taking appropriate action if Non-Compliant Products are found via recall or issues with equipment or supplies. • When necessary, and in coordination with the Chief, SPS, revise work schedules to meet anticipated changes in the workload based on the surgical schedule, staff vacations or sick calls. • Research and write new SOP’s and Competencies. Review and update current SOP’s and Competencies. • Participating in the RME committee and the Clinical Product Review Committee. • Serve as Acting Assistant Chief SPS in the absence of both Assistant Chiefs. Show less
-
-
-
Alexian Brothers Healthcare
-
Elk Grove Village Illinois
-
Senior Sterile Processing Technician
-
Sep 2011 - Nov 2012
• Ability to rotate assignments among the various areas: sterilization, processing, decontamination, surgical tray assembly, reusable inventory and medical equipment processing. • Collection, receipt, inspection and decontamination processing of soiled supplies, instruments, equipment, and apparatus including complex diagnostic equipment and medical apparatus. • Completely and thoroughly dissembling all parts of technical reusable medical equipment (RME) to ensure the removal of bio-burdens prior to sterilization. • Operating decontamination equipment such as washer decontaminators, sonic washers and laparoscopic insulation tester. • Validating all cleaning of instrumentation and RME using department Standard Operating Procedures and manufacture guidelines. • Performing inspection, assembly, packaging, and terminal sterilization of all trays, sets, and packs for use throughout the medical center. • Determining the criticality category of RME using the Spaulding Classification System and interpretation of sterilization parameters provided by manufacturer guidelines to determine the proper method of sterilization. • Operating sterilization equipment such as Steam Sterilizers, Sterrad, Sterrad NX, ETO sterilizers, heat sealers, tube dryers, and biological incubators. • Troubleshooting complex sterilizers used in the medical center to ensure optimal operation. • Assembling minor and complex tray sets and instrumentation packs used for a variety of general and specialized medical and surgical procedures and surgical case carts. • Experienced in the cleaning, packaging and sterilization of DaVinci Robotic surgical instruments. Show less
-
-
-
Edward Hines VA Medical Ceter
-
Hines Illinois
-
Medical Supply Technician Sterile Processing
-
Nov 2010 - Nov 2012
• Ability to rotate assignments among the various areas: sterilization, processing, decontamination, surgical tray assembly, reusable inventory, medical equipment processing and quality assurance functions. • Collection, receipt, inspection and decontamination processing of soiled supplies, instruments, equipment, and apparatus including complex diagnostic equipment and medical apparatus. • Completely and thoroughly dissembling all parts of technical reusable medical equipment (RME) to ensure the removal of bio-burdens prior to sterilization. • For endoscopes, performing leak testing to determine the water tight integrity of the scope is intact before initiating the cleaning and high level disinfection process. • Operating decontamination equipment such as washer decontaminators, sonic washers, irrigators, laparoscopic insulation tester, automatic cart wash and tube dryers. • Validating all cleaning of instrumentation and RME using department Standard Operating Procedures and manufacture guidelines. • Performing inspection, assembly, packaging, and terminal sterilization of all trays, sets, and packs for use throughout the medical center. • Determining the criticality category of RME using the Spaulding Classification System and interpretation of sterilization parameters provided by manufacturer guidelines to determine the proper method of sterilization. • Operating sterilization equipment such as Steam Sterilizers, Sterrad, Sterrad NX, VPRO Maxx sterilizers, ETO sterilizers, heat sealers, tube dryers, and biological incubators. • Troubleshooting complex sterilizers used in the medical center to ensure optimal operation. • Assembling minor and complex tray sets and instrumentation packs used for a variety of general and specialized medical and surgical procedures and surgical case carts. • Experienced in the cleaning, packaging and sterilization of DaVinci Robotic surgical instruments. Show less
-
-
-
Covenant Healthcare
-
Saginaw Michigan
-
Sterile Processing Technician
-
Aug 2004 - Nov 2010
• Ability to rotate assignments among the various sterilization, processing, decontamination, surgical tray assembly, reusable inventory, medical equipment processing and quality assurance functions. • Collection, receipt, inspection and decontamination processing of soiled supplies, instruments, equipment, and apparatus including complex diagnostic equipment and medical apparatus. • Completely and thoroughly dissembling all parts of technical reusable medical equipment (RME) to ensure the removal of bio-burdens prior to sterilization. • Operating decontamination equipment such as washer decontaminators, sonic washers and irrigators. • Validating all cleaning of instrumentation and RME using department Standard Operating Procedures and manufacture guidelines. • Performing inspection, assembly, packaging, and terminal sterilization of all trays, sets, and packs for use throughout the medical center. • Determining the criticality category of RME using the Spaulding Classification System and interpretation of sterilization parameters provided by manufacturer guidelines to determine the proper method of sterilization. • Operating sterilization equipment such as Steam Sterilizers, Sterrad, heat sealers and biological incubators. • Troubleshooting complex sterilizers used in the medical center to ensure optimal operation. • Assembling minor and complex tray sets and instrumentation packs used for a variety of general and specialized medical and surgical procedures and surgical case carts. • Inventorying cardiac arrest carts, urology carts, chest tube carts and line carts and replacing used items. Show less
-
-
-
Algonquin/Lake in the Hills Fire Department
-
Algonquin Illinois
-
Firefighter/Paramedic-EMS Lieutenant
-
Jan 1996 - Aug 2004
• Perform firefighting activities including driving fire apparatus, operating pumps and related equipment, laying hose, and performing fire combat, containment and extinguishment tasks. • Participate in fire drills, attend classes in firefighting, emergency medical, hazardous materials, and related subjects. • Receive and relay fire calls and alarms. • Operate radio and other communication equipment. Participate in the inspection of buildings, hydrants, and other structures in fire prevention programs. • Maintain fire equipment, apparatus and facilities. Perform minor repairs to departmental equipment. • Perform general maintenance work in the upkeep of fire facilities and equipment; clean and wash walls and floors; care for grounds around station; make minor repairs; wash, hang and dry hose; wash, clean, polish, maintain and test apparatus and equipment. • Assist in developing plans for special assignments such as emergency preparedness, hazardous communications, training programs, firefighting, hazardous materials, and emergency aid activities. • Present programs to the community on safety, medical, and fire prevention topics. Perform salvage operations such as throwing salvage covers, sweeping water, and removing debris. • Performs duties as a certified EMT-P, according to criteria and standards set forth by the department. • Responsible for the proper administration of patient care on dispatched emergency medical calls. • Completed Hazardous Materials Operations Certification training. Obtained certification at completion of class following certification testing. Show less
-
-
-
-
Avaiation Electricians Mate
-
Mar 1981 - Mar 1988
• Maintain a wide range of electrical and navigational equipment in Navy aircraft. • Trained on all the computer systems that support this state-of-the-art equipment. • Testing, installing and maintaining a wide range of aircraft instruments and electrical equipment like generators, motors and lighting systems. • Reading electrical system diagrams. • Maintaining aircraft compass systems. • Performing electrical troubleshooting operations. • Using a variety of electrical measuring equipment. • Maintaining automatic flight control systems. • Maintaining inertial navigation systems. • Standing watches as assigned. Show less
-
-
Community
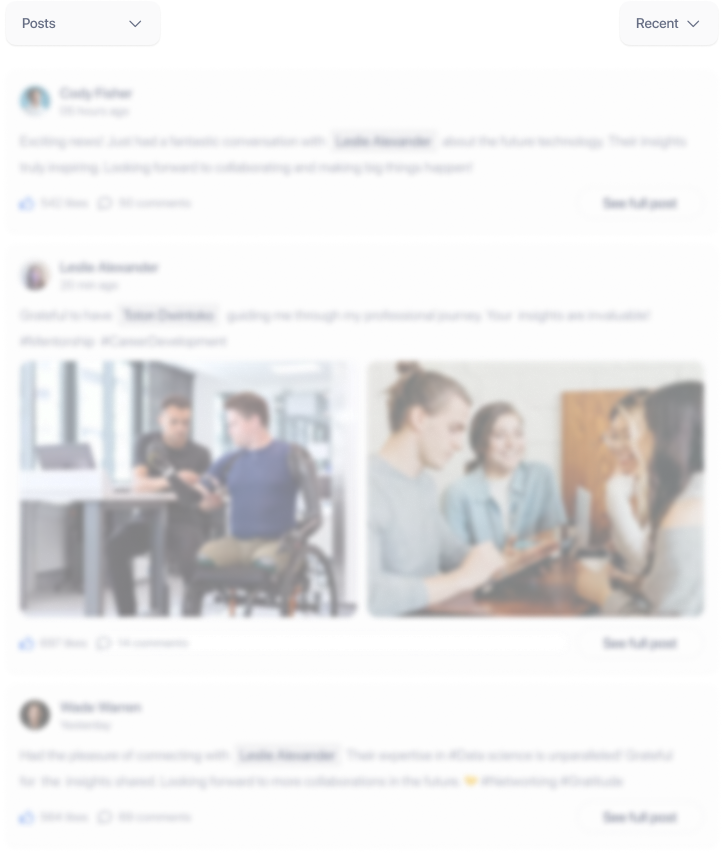