Lorette Van Der Walt
Business Analyst at OPSI Systems- Claim this Profile
Click to upgrade to our gold package
for the full feature experience.
-
English Full professional proficiency
-
Afrikaans Native or bilingual proficiency
Topline Score
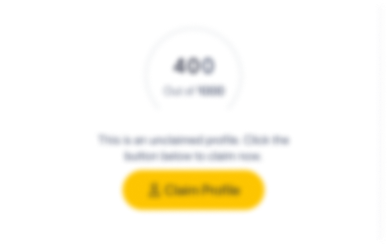
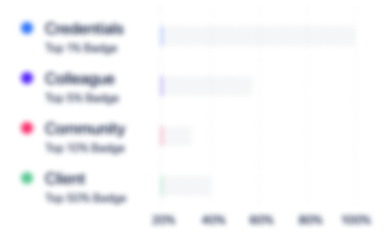
Bio
0
/5.0 / Based on 0 ratingsFilter reviews by:
Experience
-
OPSI Systems
-
South Africa
-
Transportation, Logistics, Supply Chain and Storage
-
1 - 100 Employee
-
Business Analyst
-
Oct 2019 - Present
-
-
-
ASSA ABLOY Group
-
Sweden
-
Building Materials
-
700 & Above Employee
-
Senior Industrial Engineer
-
Apr 2017 - Nov 2018
Managed the industrial engineering division at ASSA ABLOY Roodepoort consisting of junior Industrial Engineers and engineering students. ASSA ABLOY is the global leader of door opening solutions of which Roodepoort specialises in the production of cylinders, padlocks, mortice locks, etc. The department is responsible for supporting production in terms of processes, efficiency, maintenance, quality, etc. Responsibilities included the following: - Manage engineering team, and their performance - Adhoc problem solving - Develop and implement quality control and -assurance tools/processes - Develop and implement production planning and -scheduling tools - Improved scheduling of tool services and machine maintenance, improved machine utilisation, reduced unplanned tool services and breakdowns, improved efficiency. - New product introduction w.r.t. costing, functionality and design, samples, production processes and requirements, standard operating procedures, etc. - Managed the development of standard operating procedures (SOPs) - Set-up and change-over time reduction projects (SMED) - Implemented Kanban inventory control systems - Eliminate waste, minimize non-value adding activities and continuously improve processes - Line balancing of production - Implement visual management systems - Implement production KPI's such as overall equipment effectiveness (OEE), rework and scrap - Develop and implement new and improved factory layout and flow - Apply Theory of Constraints (TOC) - Implement and train employees on Kata boards - Manage all products' bill of materials (BoMs). - Improve stock accuracy and product costing. - Process mapping - Manage execution of time studies for costing, line balancing and setting of production targets - Value Analysis Value Engineering (VAVE) product workshops. Reduced cost and improved functionality - Assist with automation projects w.r.t. concept development, design, implementation and optimization Show less
-
-
-
Transnet Freight Rail
-
South Africa
-
Truck Transportation
-
700 & Above Employee
-
Industrial Engineer
-
Apr 2015 - Apr 2017
Employed in the Organisational Development and Performance Department. Responsibilities included the following:- Development of simulation models using Tecnomatix Plant Simulation Software with the purpose of verifying the feasibility,capability and efficiency of future train yards to deliver the desired amount of tonnages. - Document future yard operation processes. - Verify practicality and effectiveness of future yards’ layout and design.- Develop a network capacity model indicating the performance of various sections on the railway network in terms of tonnages and revenue and thus highlighting constraints.- Develop and automate real-time reports with a view of staged trainloads within specific corridors. - Calculation of financial benefit of proposed projects e.g. Financial impact of changing wagon placement quantity and time at customer sidings- Lean Six Sigma Green Belt project team member. The project focussed on reducing import wagon dwell times in a specific yard- Implement/roll-out of prototype tools and reports developed. Managing and tracking development of reports into the official Transnet Freight Rail Portal. Show less
-
-
Engineer In Training
-
Apr 2013 - Mar 2015
Completed a two year development programme for Industrial Engineering graduates within the Performance Enabling and Reporting Department.Responsibilities included the following:- Develop and program decision support tools to assist with optimization of empty wagon distribution- Develop and program reports to improve visibility of wagon/train positions and to monitor key performance indicators- Automation of real time reports - Process mapping of management and execution processes- Application of project management tools for planning and tracking the execution of projects- Assisted with the Transnet Freight Rail organisational restructuring project Show less
-
-
-
-
Student Vacation Work
-
Jan 2012 - Feb 2012
Development and programming of basic wagon distribution logic/principles in an Octave model for a fictitious rail network. Development and programming of basic wagon distribution logic/principles in an Octave model for a fictitious rail network.
-
-
-
-
Student Vacation Work
-
Jun 2010 - Jul 2010
Develop a yard count down board which will improve the visibility of train and wagon movements in the yards. Develop a yard count down board which will improve the visibility of train and wagon movements in the yards.
-
-
Education
-
University of Pretoria/Universiteit van Pretoria
B.Eng. Honours Cum Laude, Technology Management -
University of Pretoria/Universiteit van Pretoria
Bachelor of Engineering (B.Eng.) Cum Laude, Industrial Engineering -
Hoërskool Oosterlig
High School, Senior Certificate
Community
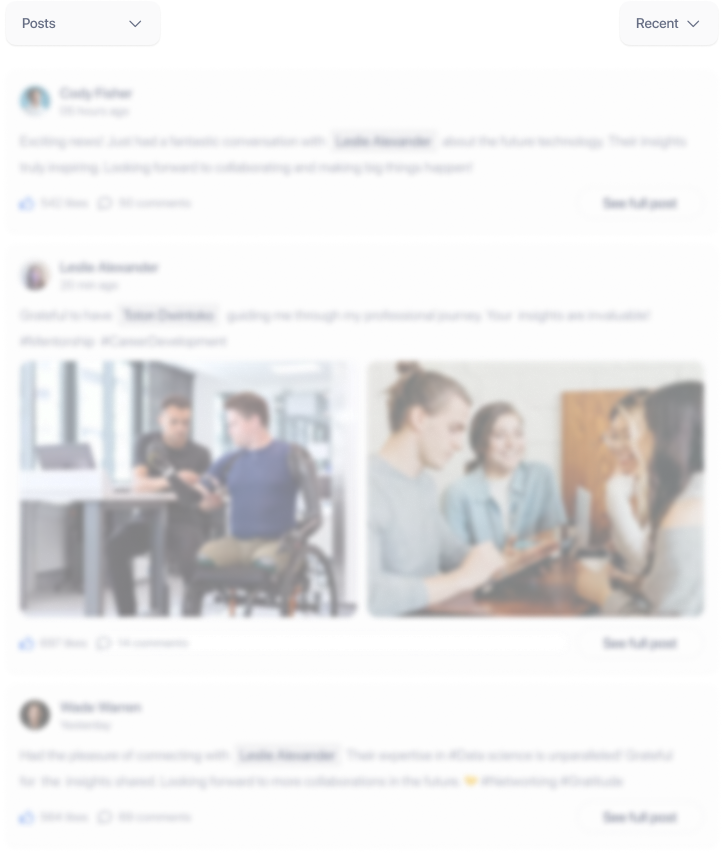