Loredana Andreea Cotovanu
Global Corporate Customer Quality Manager at Wittur Group- Claim this Profile
Click to upgrade to our gold package
for the full feature experience.
Topline Score
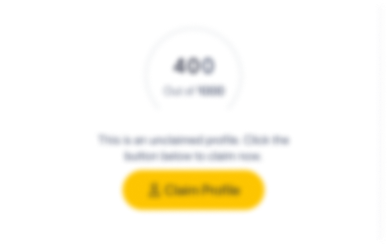
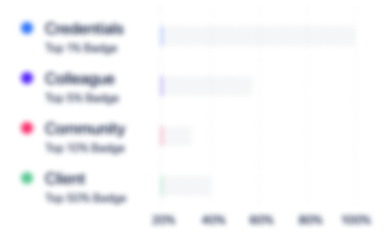
Bio


Credentials
-
Field Failure Analysis
-Jan, 2018- Nov, 2024 -
VDA6.3
QMCJun, 2016- Nov, 2024
Experience
-
Wittur Group
-
Germany
-
Industrial Machinery Manufacturing
-
700 & Above Employee
-
Global Corporate Customer Quality Manager
-
Feb 2020 - Present
Main activities and responsabilities: • Act as interface between Customer and Wittur Group for all quality related topics. • Transfer customer requirements and needs to the Wittur facilities. Be a link between customer and plant. • Harmonize the knowledge and share lessons learned between plants. • Develops customer communication and becoming the Wittur interface to establish and maintain effective trusting business relationships at all levels. • Reference point for the customer in case of escalation for major customer issues. • Take the lead for problem solving activities in case of critical customer quality issues by working closely with experts in order to ensure that the root cause is found, and robust corrective actions are implemented. • Initiate and drive supplier development projects on customer satisfaction. • Monitors performances against targets and ensures the goals are met and report risk situation inside the organization. • Share QP results with the plants and support the local team in the management of the action plan if needed. Share the successes and recognition. Be pro-active • Coordination of the visit and support audit of the Customer • Support on customer product approval (PPAP) • Weekly and monthly reporting customer KPI´s and escalated customer topics Show less
-
-
-
Autoliv
-
Sweden
-
Motor Vehicle Parts Manufacturing
-
700 & Above Employee
-
Customer Quality Engineer
-
May 2014 - Feb 2020
Main activities and responsibilities: Follow Quality Philosophy from supplier to end user Customer Interface Facilitate 8D Meetings and non-conformant report writing (Corrective Action Reports) Set up containments and quality alerts to protect the customer Be aware of Quality KPIs and the steps required to achieve and maintain KPI standards Provide written reports to customers and company management teams detailing performance measures, issues and improvement action plans as required Lead problem solving activities using company and customer methodologies to ensure verifiable and effective actions to contain defects, establish root causes, implement corrective actions and prevent further occurrence Participate in all customer-related liaison, Quality activities and new product introductions utilizing appropriate APQP techniques Contribute to the overall operational effectiveness of the plant by recommending sound proposals to support the business objectives Elaborate the Acceptance Criteria’s Catalogues Prepare PPAP file documentation and submit to the customer portal Monthly reporting to quality manager of quality indicators Act as mentor for the integration period of new colleagues: support the definition of Training Integration Plan Show less
-
-
-
Quin GmbH
-
Germany
-
Motor Vehicle Manufacturing
-
1 - 100 Employee
-
Customer Quality Engineer
-
Jul 2011 - May 2014
Main activities and responsabilities: Ensure the interface between the plant Division and the customers Manage the assigned customers overall perception of the organization Coordinate and moderate the problem solving teams and ensure action plan completion Manage activities related to quality performance, initiatives and requirements at the customer Follow-up of the actions Submit 8D Report to the customer Portal Make sure the customer requirements are in place after the actions implementation Organize, if the case, sorting activity internal or at customer side Make sure that the delivery during containment actions implementation are marked if customer requires Assure support in case of nonconformity found on the production line Assure support for process quality and supplier quality department teams Assure interface for the customer, for serial life topics and during launch phase Participate to FMEA meetings Show less
-
-
-
DRÄXLMAIER Group
-
Germany
-
Motor Vehicle Manufacturing
-
700 & Above Employee
-
PROCESS ENGINEER
-
Jun 2007 - Jul 2011
Main activities and responsibilities: Suggest, define and implement new processes and process improvements Assumptioning own responsability for process developement before the series production starts, Producing measurement parts, sample parts and prototypes, Improve the production process by closely monitoring and analyzing production process, participate to the process and quality audits Assumptioning own responsability and colaborating for defining the best technology, process, machines, tools and prototypes, Cooperation and coordination for developing technologies, Accomplish and supervising the process optimisation within processes, of new products and series products, Coordination and tehnical training for series production, Accomplish the capability documents, Elaborating work instructions, Making testreports and exchanging experience with Process Development Department from Germany Show less
-
-
Education
-
Universitatea Transilvania din Brașov
Bachelor of Engineering (BE), Engineering Economics and Business Management in product developement
Community
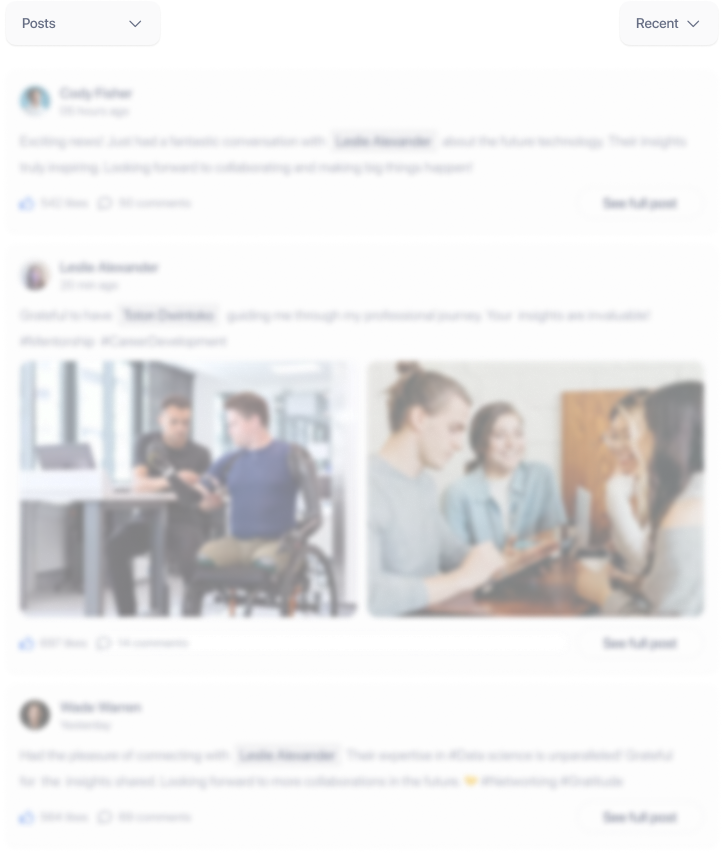