Lisa McHutchison
PDC Distribution Planning & Improvement Co-ordinator at Incitec Pivot Fertilisers- Claim this Profile
Click to upgrade to our gold package
for the full feature experience.
-
German -
Topline Score
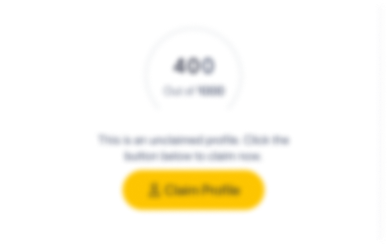
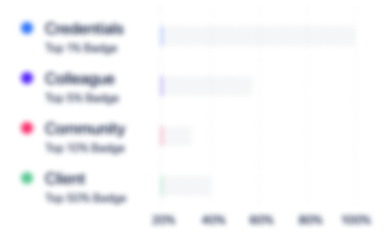
Bio

Rif Altay
Lisa is an extremely intelligent, capable and efficient person to work with. No task is too great or outside of her capability. Great person to work with! No hesitation in recommending her.

Wayne Snelson
Lisa is a highly competent performer who can be trusted by others.

Rif Altay
Lisa is an extremely intelligent, capable and efficient person to work with. No task is too great or outside of her capability. Great person to work with! No hesitation in recommending her.

Wayne Snelson
Lisa is a highly competent performer who can be trusted by others.

Rif Altay
Lisa is an extremely intelligent, capable and efficient person to work with. No task is too great or outside of her capability. Great person to work with! No hesitation in recommending her.

Wayne Snelson
Lisa is a highly competent performer who can be trusted by others.

Rif Altay
Lisa is an extremely intelligent, capable and efficient person to work with. No task is too great or outside of her capability. Great person to work with! No hesitation in recommending her.

Wayne Snelson
Lisa is a highly competent performer who can be trusted by others.
0
/5.0 / Based on 0 ratingsFilter reviews by:
Experience
-
Incitec Pivot Fertilisers
-
Australia
-
Farming
-
100 - 200 Employee
-
PDC Distribution Planning & Improvement Co-ordinator
-
Jun 2018 - Present
-
-
-
Fonterra
-
New Zealand
-
Food and Beverage Manufacturing
-
700 & Above Employee
-
Site Scheduler
-
Jan 2014 - May 2018
-
-
-
Air Radiators
-
Australia
-
Industrial Machinery Manufacturing
-
1 - 100 Employee
-
Production Planner
-
Jun 2008 - Aug 2013
Position: Production Planner Employer: Air Radiators – specialising in the design and manufacture of air movement and heat transfer solution for industrial, vehicle and mining applications Role / Achievements: Co-ordinating Sales and Operations to ensure 100% in full on time delivery. Ensuring adequate capacity, resources and materials to meet product delivery. 2012 - Air Radiators Ideas Scheme Award Implementation of an IT solution to automatically adjust department schedules to allow for Quality Inspection time to be added when required by customer 2011 - OH&S Representative Certificate From Gordon Tafe. 5 day course. On the OH&S Committee for Air Radiators 2011-2013 • Created an end to end scheduling tool – Heading up the Pronto One Page Plan team to ascertain business needs and develop a framework for a software based department scheduling program that provides end to end seamless scheduling to ensure customer requirements are met. • Cross Functional communication – key role as a communications hub between sales and operations. Primarily to streamline communication, reduce confusion and convey information in a succinct and timely manner to ensure smooth operations, remove road blocks and meet project goals. • Capacity Planning – combining historical sales data with budget projections to produce medium to long term capacity plans with break downs by area / product line. • Lean Manufacturing – implementation of 5S, 6 Sigma and Lean Manufacturing principles in both factory and office environments. Results of these projects include less downtime from searching for tools and information, less product contamination due to more regular housekeeping and documented minimum standards as well as cost reduction due to wastage, lost time and lost tools. Show less
-
-
-
-
Logistics Analyst
-
May 2006 - Dec 2006
Position: Logistics Co-ordinator, Material Planning and Logistics Employer: Sumitomo Wiring Systems Australia - A provider of electrical distribution systems (wiring) and instrument consoles to the automotive industry. Role / Achievements: Working with internal departments, customers and suppliers to ensure customer requirements are met on time with zero defects and shipped at a competitive cost. Cost savings of $1.5million in my role as cost savings champion for the Material Planning and Logistics Department. 2007 - TS 16949 Internal Auditor Certification Auditing certification for manufacturing quality systems. 2007 - 5S Champion for Material Planning & Logistics Training, implementation, auditing and continuous improvement of the 5S standard for the Material Planning and Logistics department (11 people + Production in warehouse). 2007 - Cost reduction Champion for Material Planning & Logistics Initiate, plan and track cost savings, avoidance and recovery efforts of the department. Report out to head office as part of monthly KPI reporting. • People Management – directing and coaching Logistics Clerk position, creating department and training budgets. Delegating, prioritising and allocating tasks to manage work load in the Material Planning & Logistics team. • Logistics– shipping, freight forwarding and transportation experience. Carrier and freight forwarder selection and management, import / export costing and documentation, department budgets and cut off calculations for product lines and break points. • Material Planning and Inventory Management – using historical data and customer forecasts to produce MRP usage data to determine order quantities and timelines for run out of old stock • Cost analysis and savings – recovery of freight costs, order quantity management to reduce obsolescence costs and also ensure design change costs are passed on to customers where applicable. Show less
-
-
-
-
Indirect Purchasing
-
Feb 2004 - Jul 2005
Position: Buyer – Indirect Purchasing Employer: Holden Ltd Role / Achievements: Processing electronic orders on SAP as well as paper orders. Sourcing of suppliers, negotiation of contracts, and SRM (supplier relationship management). • Introduction of SAP – awarded administration security rights for our departments SAP functions due to knowledge of software. Created SAP department manual and delivered training to the Indirect Purchasing department. Position: Buyer – Indirect Purchasing Employer: Holden Ltd Role / Achievements: Processing electronic orders on SAP as well as paper orders. Sourcing of suppliers, negotiation of contracts, and SRM (supplier relationship management). • Introduction of SAP – awarded administration security rights for our departments SAP functions due to knowledge of software. Created SAP department manual and delivered training to the Indirect Purchasing department.
-
-
-
-
Purchasing Analyst
-
Jan 2003 - Feb 2004
Creating a supplier delivery evaluation system. Processing purchase orders. Leveraging volume to achieve cost downs. Creating training manuals and teaching. Process improvement. Monitoring KPI's. Negotiating vehicle accessories for Ford Falcon and Territory. Creating a supplier delivery evaluation system. Processing purchase orders. Leveraging volume to achieve cost downs. Creating training manuals and teaching. Process improvement. Monitoring KPI's. Negotiating vehicle accessories for Ford Falcon and Territory.
-
-
Education
-
RMIT University
Masters - Logistics Management, Logistics Management -
Victoria University
BBus, International Trade
Community
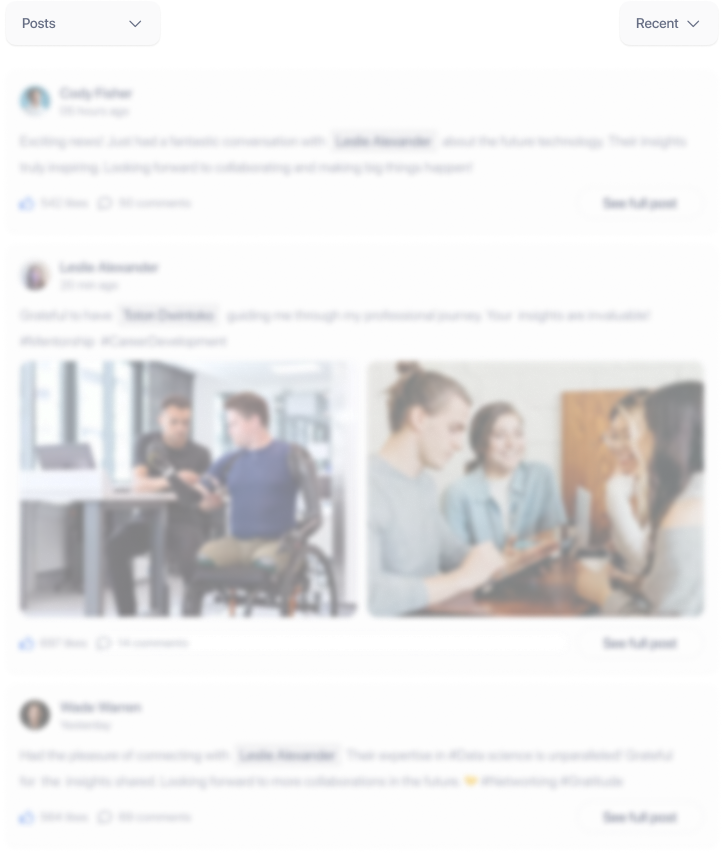