Lisa Alvin
Process Engineer at Rust-Oleum Corporation- Claim this Profile
Click to upgrade to our gold package
for the full feature experience.
Topline Score
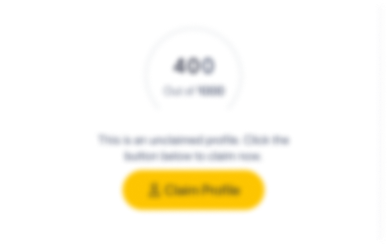
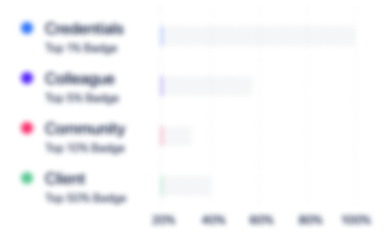
Bio
0
/5.0 / Based on 0 ratingsFilter reviews by:
Experience
-
Rust-Oleum Corporation
-
United States
-
Manufacturing
-
700 & Above Employee
-
Process Engineer
-
Oct 2021 - Present
-
-
Supplier Quality Manager
-
May 2020 - Oct 2021
• Validated new products and new sites for outsourcing; completed stability review requirements, assessed R&D risk review and need for FMEA, and safely conducted 7 site visits/audits during quarantine lockdown• Provided Supplier Quality Requirement (SQR) documents for new products at contract manufacturers, managing ~1000 existing SQR documents with ~100 updated or newly created each quarter; each document consisted of information from up to 6 different departments such as R&D, Purchasing, and Regulatory• Successfully lead a cross-functional project team to simplify and automate SQR completion, with heavy resistance to change• Managed customer complaints, production issues, or other quality concerns for over 700 companies that supplied all raw materials, components, and finished goods for Rust-Oleum; created and used a CAPA form with 5-why analysis, and lead many cross-functional investigation meetings with suppliers Show less
-
-
-
Vantage Specialty Chemicals
-
United States
-
Manufacturing
-
400 - 500 Employee
-
Production Engineer
-
Jul 2018 - May 2020
•Implemented new OEE metrics for the site, trained operations and site management on key parameters; Quality remained above 96% yearly goal, Availability and Rate increased ~5 - 10% through the year from CI and PSM projects suggested by operators •Took ownership of bi-monthly shutdown planning for maintenance, capital project work, and PM’s, outages ranged 4 to 48 hours with contractors, union maintenance workers, operations, safety, and project engineering involvement; 2020 was turned back over to maintenance management with SOP and Gantt Chart templates •Created a new Washout Matrix to include 6 reaction vessels and 10 finishing vessels for >150 unique products •Volunteered as temporary Engineering Manager for >1 month, attending site incident meetings, directing month-end and year-end reports from fellow engineers to multiple departments, and familiarizing myself with the Continuous Emissions Monitoring System being commissioned •Reduced the turnover time from 6 days to 1 day to clean and convert a large prep vessel between process lines; frequency of this practice recently increased to be done several times a month •Sought out a Foxboro DCS training course to learn about IACC sequence blocks and ladder logic, and trained the engineering team on these learnings; also shadowed the electrical/instrumentation maintenance specialist to train myself on PLC logic and provide support in his absence Show less
-
-
-
Huntsman Corporation
-
United States
-
Chemical Manufacturing
-
700 & Above Employee
-
Production Engineer
-
Mar 2016 - Jul 2018
•Supported several batch and semi-batch processes, producing ~3 kT of product per year •Assisted in the design, quoting, installation, and debugging of a $600,000 capital project; capacity with the new equipment increased 60%, totaling a potential $5.8 million additional yearly revenue •Innovated a new way to increase throughput by changing batch sizes, conducted trials on several key products including internal and external quality testing; capacity of the process increased 12%, with $1.7 million additional yearly revenue •Qualified new source of a key raw material, designed and conducted trials and worked with purchasing to continue high priority after qualification, saved ~$3 million in raw material costs per year •Renovated several EHS excellence initiatives, and introduced fresh new programs to improve employee involvement and communication Show less
-
-
-
Dow Corning
-
Italy
-
Chemical Manufacturing
-
Manufacturing Engineer
-
Sep 2014 - Dec 2015
•Oversaw 4 large processes worth several billion in leveraged sales, each with at least one planned shutdown per year, and oversaw all safety, environmental, and quality aspects of each; unit operations included reactors, distillation, phase separation, and heat exchangers, some of which were enclosed in bomb stalls•Interfaced with R&D, global sharing committee, operators, and supply chain consultants to work through plant troubleshooting and several capital improvement projects•Utilized statistical software and PLC/automation programming to improve rates and lower manufacturing costs•Took over relevant responsibilities from the supply chain logistics coordinator to handle product scheduling and corresponding with both customers and suppliers when issues arose Show less
-
-
Process Engineer
-
Jul 2011 - Aug 2014
•Optimized distillation column operation to better purify byproduct, thereby reducing the need to convert our main product; 5 sigma shift in product quality, $400,000 annual savings•Traveled to the Dow Corning plant in China for 2 weeks to optimize the internal and operational parameters of their Fluid Bed Reactor; inexpensive, promising solution proposed to and implemented by global sharing committee•Created benchmarking spreadsheet for the physical and operational parameters of each Fluid Bed Reactor at our 3 global manufacturing sites and coordinated the international sharing and analysis of this data by all involved engineers•Managed a summer intern and successfully guided him through an 11-week assignment around cyclone efficiency Show less
-
-
-
-
Process Engineering Intern
-
May 2010 - Jul 2010
• Utilized Design Of Experiment software and reasoning to design and carry out a series of experiments to optimize a sugar siloxane reaction and understand the impact of certain variables • Conducted 13 lab runs, 7 to 12 hours each, and determined amine content, viscosity, percent non-volatile content, and rheology for analysis of samples • Utilized Design Of Experiment software and reasoning to design and carry out a series of experiments to optimize a sugar siloxane reaction and understand the impact of certain variables • Conducted 13 lab runs, 7 to 12 hours each, and determined amine content, viscosity, percent non-volatile content, and rheology for analysis of samples
-
-
-
Gas Technology Institute
-
United States
-
Research Services
-
1 - 100 Employee
-
Gasification Intern
-
May 2009 - Aug 2009
• Created multiple interactive spreadsheets for the calculation of complex processes relating to Cooling Towers, Prime Movers, and Sulfur Recovery with up to 75 inputs each • Troubleshot with team members the Kerosene Absorption, Ethylene Glycol Dehydration, H2S/SO2 Contact Combined Process Unit when it was first being tested; employed Design for Manufacturing (DFM) concepts • Individually collected data to calculate mass and heat transfer and developed test methods to fix various vessels • Created multiple interactive spreadsheets for the calculation of complex processes relating to Cooling Towers, Prime Movers, and Sulfur Recovery with up to 75 inputs each • Troubleshot with team members the Kerosene Absorption, Ethylene Glycol Dehydration, H2S/SO2 Contact Combined Process Unit when it was first being tested; employed Design for Manufacturing (DFM) concepts • Individually collected data to calculate mass and heat transfer and developed test methods to fix various vessels
-
-
-
Abbott Laboratories
-
Colombia
-
Personal Care Product Manufacturing
-
200 - 300 Employee
-
Global Project Management Intern
-
May 2008 - Aug 2008
• Assisted in gathering project details for laboratory renovations and relocations for seven scientific groups averaging 75 people • Proposed new locations within existing vacant lab buildings for these groups to accommodate their size and equipment requirements, presented through power point • Recommended new options to reduce energy consumption of 68 new fume hoods, saving up to $328,178 • Assisted in gathering project details for laboratory renovations and relocations for seven scientific groups averaging 75 people • Proposed new locations within existing vacant lab buildings for these groups to accommodate their size and equipment requirements, presented through power point • Recommended new options to reduce energy consumption of 68 new fume hoods, saving up to $328,178
-
-
Education
-
University of Illinois Urbana-Champaign
B.S., Chemical Engineering
Community
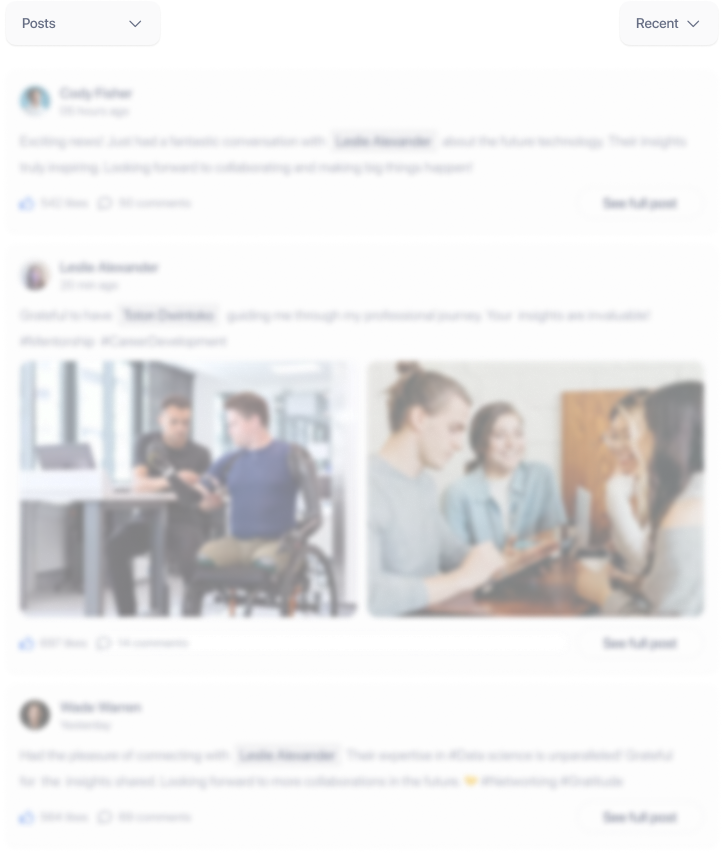