Linda Rorye
Sr. Engineering Manager at SANTIER- Claim this Profile
Click to upgrade to our gold package
for the full feature experience.
Topline Score
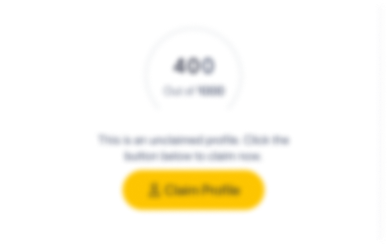
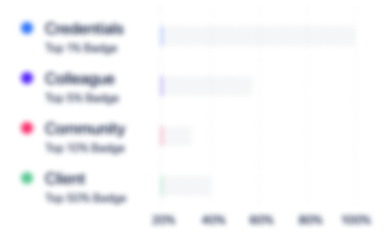
Bio

Steven Tower
Linda is a highly motivated and detail-oriented Manufacturing Leader that I had the privilege to work alongside at AMETEK Programmable Power. She always had her finger on the pulse of operations and was driven to solve any issues that threatened her build schedules. She was organized, data-driven, and always able to communicate her needs. On a personal level, I am happy that I had the chance to meet Linda. And I miss our lunches down on Convoy Street!

Steven Tower
Linda is a highly motivated and detail-oriented Manufacturing Leader that I had the privilege to work alongside at AMETEK Programmable Power. She always had her finger on the pulse of operations and was driven to solve any issues that threatened her build schedules. She was organized, data-driven, and always able to communicate her needs. On a personal level, I am happy that I had the chance to meet Linda. And I miss our lunches down on Convoy Street!

Steven Tower
Linda is a highly motivated and detail-oriented Manufacturing Leader that I had the privilege to work alongside at AMETEK Programmable Power. She always had her finger on the pulse of operations and was driven to solve any issues that threatened her build schedules. She was organized, data-driven, and always able to communicate her needs. On a personal level, I am happy that I had the chance to meet Linda. And I miss our lunches down on Convoy Street!

Steven Tower
Linda is a highly motivated and detail-oriented Manufacturing Leader that I had the privilege to work alongside at AMETEK Programmable Power. She always had her finger on the pulse of operations and was driven to solve any issues that threatened her build schedules. She was organized, data-driven, and always able to communicate her needs. On a personal level, I am happy that I had the chance to meet Linda. And I miss our lunches down on Convoy Street!

Credentials
-
Implementing Continuous Improvement: A Case Study
LinkedInJul, 2020- Nov, 2024 -
Working with Difficult People
LinkedInJul, 2020- Nov, 2024 -
Performance-Based Hiring
LinkedInOct, 2017- Nov, 2024 -
Engineering In Training (E.I.T.)
NCEES -
PMP
Project Management Institute
Experience
-
SANTIER
-
United States
-
Appliances, Electrical, and Electronics Manufacturing
-
1 - 100 Employee
-
Sr. Engineering Manager
-
Mar 2022 - Present
Promoted to direct overall company’s engineering effort in process planning, product costing, process improvement and sustaining activities to deliver quality thermal management products. Managed 7 direct reports from Engineering to Documentation Control.Operations | Engineering Management• Process planning and configuration. Aligned process planning priorities with production build schedule. Led 7-member cross-departmental team through contract and drawing reviews. Created collaborative team environment with focus on capturing flow-down requirements and material selection for deliverables. Eliminated the chances of manufacturing non-compliant products. • Continuous Process Improvements. Introduced streamlined and poka-yoke processes that enhanced reliability and contributed to efficiency increase by 10%, reduced error rate by 75% and accelerated customer satisfaction.• New Products. Introduced and transitioned new products to production after proven feasibility. Established new product manufacturing schedule with production team and tracked progress. Provided and guided manufacturing team with work instructions and testing procedures. Addressed all non-conformance with corrective and preventive actions and verified the effectiveness through the subsequent lots.• Cost Reductions. Introduced alternative suppliers as second sources for material and processes that dropped the average COGS by 5% while improving internal first pass yield.• Coaching and mentorship. Provided professional development and empowered associates to try and learn that contributed to a high-performance team. Show less
-
-
Quality & Application Engineering Manager
-
Oct 2020 - Jun 2022
Responsible for overall company’s QMS and processes. Managed 6 direct reports from QA/QC to Document Control. Liaison with Sr. Management to foster a continuous improvement environment and nurture quality excellence.Operations | Quality Management• Schedule Workflow. Prioritized day-to-day Incoming Quality, In-process Quality, and Final Quality centers to meet production build and ship schedule including certification testing and First Article Reporting. Relieved inspection bottleneck through streamlined inspection plan and upskilling associates.• CAPA. Led investigation and initiated actions to correct non-conformities. Guided cross functional team to develop and implement preventive measures. Verified effectiveness of implemented actions which resulted in 99% closure with satisfactory from initiators.• Audit and Source Inspection. Led and conducted internal audits. Provided internal audit training. Facilitated external audits from Customers’ or Agency Auditors and successfully passed and awarded with AS9100 re-certification. Coordinated for source inspections. Show less
-
-
-
AMETEK Programmable Power
-
United States
-
Appliances, Electrical, and Electronics Manufacturing
-
1 - 100 Employee
-
Manufacturing Process Manager
-
Apr 2018 - May 2020
Responsible for engineering custom design new product production line encompassing production planning, scheduling, assembly, and testing of electromechanical devices that supported a full range of legacy and newly introduced engineered power subsystem (ie. Avionics ATE, eCASS) to fully integrated programmable power system such as Solar Array Simulator, Battery Simulation System for spacecraft testing. Managed 22 direct reports (planner, material coordinator, test technician, master assemblers). • Production Planning, Material Scheduling. Defined monthly production build plan and aligned with business unit. Created a quick material shortage report for BOM with over 2000 SKU through utilizing excel in place of the DOS base ERP system, which contributed to past due reduction by 80% and provided early identification of EOL or obsolescent materials. • Lean Manufacturing. Created flow from assembly through test by implementing one-piece flow which resulted in shortening the cycle time of 2 days. Re-laid out manufacturing assembly and test work centers resulting in transportation reduction of 250% and efficiency improvement by 200% which was recognized as 1st place 6S winner among 8 functional groups. • Quality Improvement. Provided feedback of manufacturing challenges of using deviated material to contract manufacturers and suppliers resulting in improved materials quality at incoming. Introduced standardized assembly process and empowered manufacturing associates with SOP resulting in yield improvement of 30% and productivity improvement by 15%. • Regulation Compliance. Spearheaded the transformation to full ITAR compliance without compromising the quality nor the delivery of the products. Show less
-
-
-
Kyocera International, Inc. (North America)
-
United States
-
Appliances, Electrical, and Electronics Manufacturing
-
200 - 300 Employee
-
Production Manager
-
Apr 2005 - Dec 2016
Entrusted with P&L accountabilities for production lines (High Temp Cofire, Post-fire Ceramic assembly, and Flip Chip PWB assembly) encompassing planning, scheduling, budget forecast, inventory control, product quality, processes, safety, regulation compliance, and delivery for both commercial and ITAR products. Managed 22 direct reports and 70 indirect reports.• Expansion. Captured 300% revenue growth through utilizing Sales and Marketing forecast to align internal and external suppliers’ capacity including setting up a brand-new manufacturing line, purchasing capital equipment to support this demand.• Inventory Control. Spearheaded the consolidation of component design across product mix, ordered only what was needed through MRP, and exercised JIT resulting in raw material inventory level reduction from 12 months to 3 months.• Cost Reductions. Implemented poka-yoke manufacturing processes and optimized material design resulting in yield improvement by 30%.• Leadership. Led cross-training programs. Created flow through line-balancing that met tight delivery schedule. Produced growth and profitability despite competitive marketplace and surpassed master plan. Show less
-
-
Development Engineer
-
Apr 2003 - Mar 2005
Developed new processes, created SOP, and implemented low-cost material set for existing products to stay competitive in the marketplace.• Designed and implemented selective plating process resulting in sustaining market share with one of the major customers and increased market share from the others.• Co-developed and patented low-cost organic material set for drop-in replacement of existing product footprints.• Characterized high thermal conductivity material set, selected the matching material, and implemented for manufacturing resulting in increased revenue of $126M year over year. Show less
-
-
Production Engineer
-
Jan 2001 - Mar 2003
In charge of first pass yield improvement, process capability, reviewed and updated specification• Troubleshoot and optimized processes through initiatives including utilizing FMEA to identify potential failure and prioritize efforts in eliminating and minimizing failures resulting with 98% yield • Set up internal processing as well as IQC spec to align with Customers’ requirements.• Designed tooling and fixtures to support production new demands.
-
-
Education
-
California State Polytechnic University-Pomona
Bachelor of Science (BS), Chemical Engineering
Community
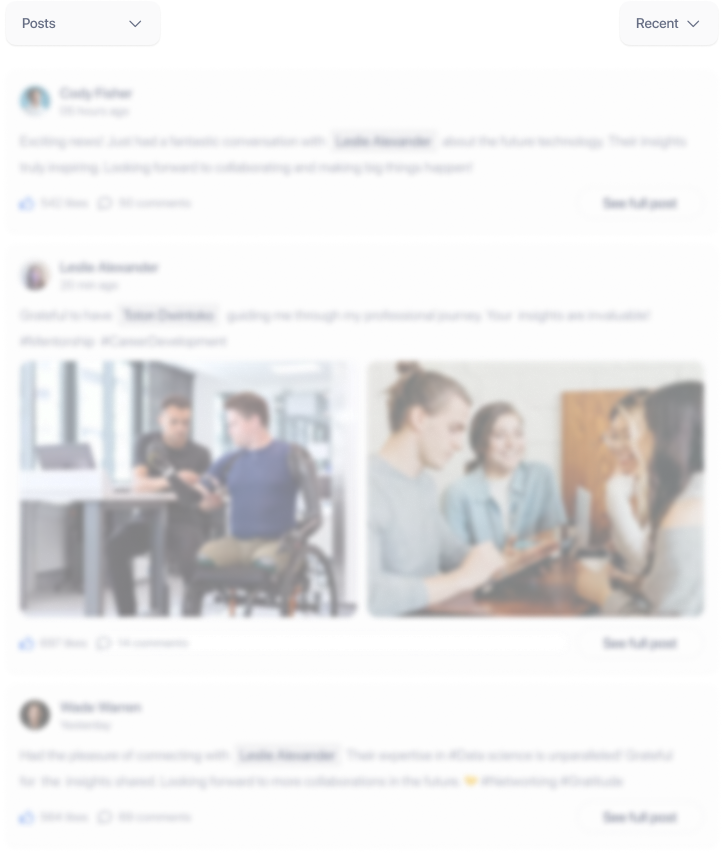