Liam Collington
Solutions Architect at Waterlogic UK & IE (Formerly Angel Springs)- Claim this Profile
Click to upgrade to our gold package
for the full feature experience.
Topline Score
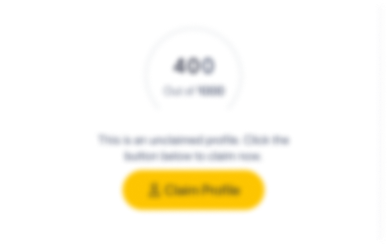
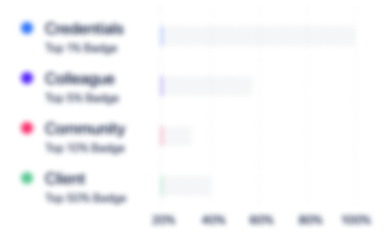
Bio

Karen Carter
Liam is very professional and thorough in his work, whilst also being empathetic to the needs of the business. He will go the extra mile to understand the business requirements in order to implement a robust, fit for purpose system. In addition to this he will put himself out to assist should a problem arise and will work with his clients to ensure a successful outcome

Steve Shephard
I worked alongside Liam during the implementation of IFS at JLA. Liam not only has a huge amount of functional IFS knowledge but also has a very strong understanding of the technical requirements of the application. His clear understanding of IFS enables him to clearly spec out projects to ensure the end client receives the best solution for their requirements. He has a real passion for his role and was able to keep the team fully motivated during the project. I thoroughly enjoyed working with him and would highly recommend him for either a functional or project management role in the future.

Karen Carter
Liam is very professional and thorough in his work, whilst also being empathetic to the needs of the business. He will go the extra mile to understand the business requirements in order to implement a robust, fit for purpose system. In addition to this he will put himself out to assist should a problem arise and will work with his clients to ensure a successful outcome

Steve Shephard
I worked alongside Liam during the implementation of IFS at JLA. Liam not only has a huge amount of functional IFS knowledge but also has a very strong understanding of the technical requirements of the application. His clear understanding of IFS enables him to clearly spec out projects to ensure the end client receives the best solution for their requirements. He has a real passion for his role and was able to keep the team fully motivated during the project. I thoroughly enjoyed working with him and would highly recommend him for either a functional or project management role in the future.

Karen Carter
Liam is very professional and thorough in his work, whilst also being empathetic to the needs of the business. He will go the extra mile to understand the business requirements in order to implement a robust, fit for purpose system. In addition to this he will put himself out to assist should a problem arise and will work with his clients to ensure a successful outcome

Steve Shephard
I worked alongside Liam during the implementation of IFS at JLA. Liam not only has a huge amount of functional IFS knowledge but also has a very strong understanding of the technical requirements of the application. His clear understanding of IFS enables him to clearly spec out projects to ensure the end client receives the best solution for their requirements. He has a real passion for his role and was able to keep the team fully motivated during the project. I thoroughly enjoyed working with him and would highly recommend him for either a functional or project management role in the future.

Karen Carter
Liam is very professional and thorough in his work, whilst also being empathetic to the needs of the business. He will go the extra mile to understand the business requirements in order to implement a robust, fit for purpose system. In addition to this he will put himself out to assist should a problem arise and will work with his clients to ensure a successful outcome

Steve Shephard
I worked alongside Liam during the implementation of IFS at JLA. Liam not only has a huge amount of functional IFS knowledge but also has a very strong understanding of the technical requirements of the application. His clear understanding of IFS enables him to clearly spec out projects to ensure the end client receives the best solution for their requirements. He has a real passion for his role and was able to keep the team fully motivated during the project. I thoroughly enjoyed working with him and would highly recommend him for either a functional or project management role in the future.

Experience
-
Waterlogic UK & IE
-
United Kingdom
-
Food and Beverage Services
-
100 - 200 Employee
-
Solutions Architect
-
Apr 2019 - Present
-
-
-
LNC Consultancy Limited
-
Oxford, United Kingdom
-
Managing Director
-
Jul 2011 - Present
LNC Consultancy Limited provides IFS ERP business solutions across a large sector of businesses. LNC Consultancy Limited provides IFS ERP business solutions across a large sector of businesses.
-
-
-
JLA Group
-
United Kingdom
-
Facilities Services
-
500 - 600 Employee
-
Project Manager
-
Apr 2017 - May 2019
-
-
-
TBS Engineering Limited
-
United Kingdom
-
Automation Machinery Manufacturing
-
1 - 100 Employee
-
Project Manager
-
May 2018 - Sep 2018
-
-
-
LGC
-
United Kingdom
-
Biotechnology Research
-
700 & Above Employee
-
IFS Supply Chain/ Data Migration Support consultant
-
Mar 2017 - Jun 2017
-
-
-
IWS Water Hygiene
-
United Kingdom
-
Environmental Services
-
1 - 100 Employee
-
IFS WO Moblie Implementation Project Manager
-
Jan 2017 - Apr 2017
-
-
-
South Staffs Water
-
United Kingdom
-
Utilities
-
100 - 200 Employee
-
Project Manager
-
Nov 2016 - Apr 2017
-
-
-
IWS Water Hygiene
-
United Kingdom
-
Environmental Services
-
1 - 100 Employee
-
IFS Implementation Project Manager
-
Aug 2014 - Nov 2015
-
-
-
Clancy
-
United Kingdom
-
Construction
-
700 & Above Employee
-
Functional consultant
-
Jan 2014 - Aug 2014
Upgrade from IFS 7.5 sp3 to IFS 8 sp1 Upgrade from IFS 7.5 sp3 to IFS 8 sp1
-
-
-
Clancy
-
United Kingdom
-
Construction
-
700 & Above Employee
-
IFS Rental Implementation Project Manager
-
Jul 2011 - Apr 2013
My responsibility was to understand/explore the new IFS functionality and produce a gap analysis for further development and/or discussion with IFS. Once a business decision had been made to develop additional functionality in-house, my role was to guide the technical team to achieve business requirements whilst managing the expectation of all stakeholders. Implementation was phased based on the advice I provided and implemented to the timescales required. Significant financial changes were applied across all five companies, these changes were planned, documented, presented, authorized and applied using best practice approach within the programme cutover plan. The delivery of the project required me to implement many processes across the application starting from the point of fixed asset creation and purchase, to the sale/scrap of these items. With the following headline areas in-between these two points, creation of serial objects, maintenance of hire items using service management, hire out of hire assets, sales invoicing/credits for hire out, hire in of external items, supplier invoice entry for external items, reconciliation of all costs in the ledgers. • Analysis of the business processes to identify the solution outline and subsequent definition for Hire in, Hire Out, Procurement of Fixed Assets, changes to existing service management processes, finance processes and configuration. • Interfaces to TFL and fuel providers to ensure these costs where automatically applied to the general ledger of the correct company using the required financial code string and intercompany postings if required. • Full financial configuration set-up/amendment in all companies to include posting controls, code parts, ledger accounts, voucher types, voucher series, user groups, Pseudo codes, authority classes etc. • Implementation of the solutions into all UK (65 Sites, 5 companies) offices. • Full data extraction from legacy system and Data Migration into IFS. Show less
-
-
-
LGC
-
United Kingdom
-
Biotechnology Research
-
700 & Above Employee
-
Functional Analysis
-
Jan 2011 - Jul 2011
-
-
ERP Implementation Supply Chain Lead
-
Sep 2008 - Dec 2010
Primary role to Improve business processes and efficiency by developing an ERP system, requiring engineering, re-engineering, and implementing within a global organisation.• A critical team member on all LGC implementations across multiple sites, companies and countries (France, Sweden, Spain, Poland, Germany, UK and Italy)• Establish global supply chain ERP architecture by integrating ERP solution across functional lines; determining functional layers, establishing partner collaborations, translating ERP needs into IT solutions, recommending best-fit and best-breed architectures.• Validation of ERP system, defining metrics to measure business and operations systems success, developing and conducting tests of system integration, functional layers and entire system.• Communicating essential information, coordinating actions, obtaining expert input, reviewing open issues and action items. Contributing information to team meetings and reports.• Functional lead for purchasing and Inventory, maintaining work stream accomplishments by establishing and monitoring milestones.• Working closely with IT project staff and related third party partners to provide guidance and architecture leadership, ensuring all proposed ERP solutions are aligned with LGC’s overall IT architecture.• Combining an excellent knowledge of the business with extensive and detailed IFS expertise. • Proficient in the design of, effective and innovative solutions • Combining analytical and methodical thinking with good communication skills. • Good team player and leader. • Provide technical support including custom events, data migration and application administration.• Production and delivery of core team and end user training.• 3rd line help desk support and management of IFS related calls to closure.• Proven track record in "Getting things done", "Making it happen" and "Adding value for customers". Show less
-
-
Procurement & Equipment Maintenance Manager
-
Aug 2005 - Aug 2008
Day to day management of the external supplier network ensuring that it fully meets quality requirements whilst minimising expenditure. Working closely with Head of Group Purchasing including contract tender processes and renegotiation of existing contracts to leverage best value from suppliers.• Project management of consolidation of suppliers to include tender process, review, selection/recommendation, approval and introduction.• Introducing supplier appraisals and benchmarking to monitor performance and identify areas for improvement, encouraging a 2-way communication process.• Implementing departmental procedures to meet and exceed ISO900I requirements.• Liaising & negotiating with suppliers ensuring contractual matters are addressed efficiently and promptly. • Implementation of various consignment inventories and vendor managed stock.• Identify suppliers/categories, review & implement revised service level agreements.• Produce bespoke contractual supply agreements.• Implementation of central procurement, influencing and promoting the benefits to decision-makers.• Management of procurement process across the group, including the introduction of a central purchasing system and equipment maintenance system across the UK.• Reduce business spend across five divisions and 10 sites – including Europe. • Proactively identify risks and issues, together with their associated solutions.• Identify, tender, negotiate and implement complex maintenance contracts across the group.• Design, build and develop eight databases, including equipment maintenance and supplier databases. Show less
-
-
Education
-
Oxford Brookes University
Business Communications -
Intec Business College
NVQ4, Business Administrsation -
Intec Business College
NVQ3, Business Administration -
Intec Business College
NVQ3, Customer Service -
Peers Upper School
Community
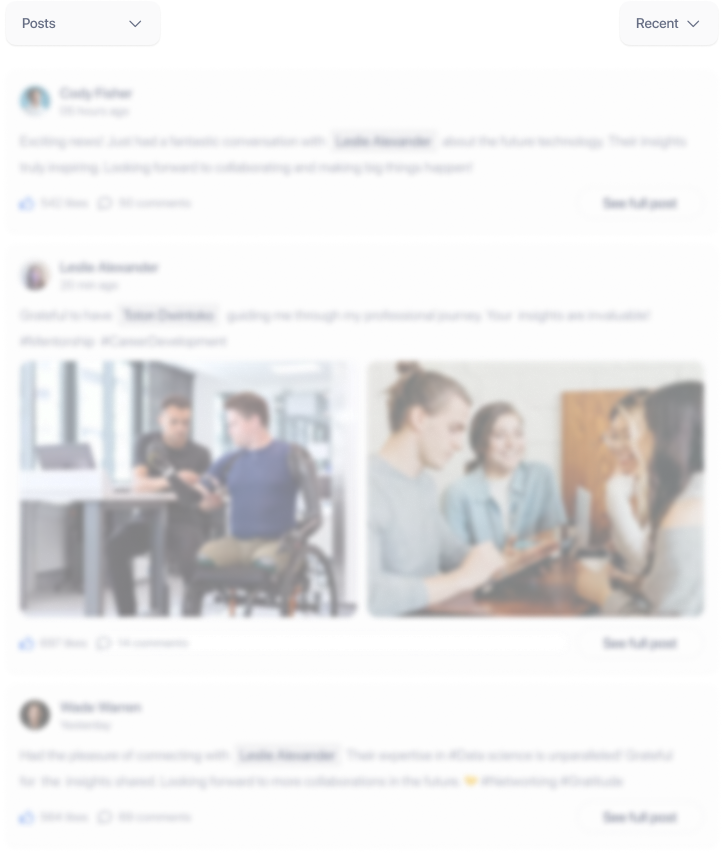