Leydi Walle, MBA, LSSBB
Quality Engineer at Franklin Brazing & Metal Treating- Claim this Profile
Click to upgrade to our gold package
for the full feature experience.
-
English Native or bilingual proficiency
-
Spanish Native or bilingual proficiency
Topline Score
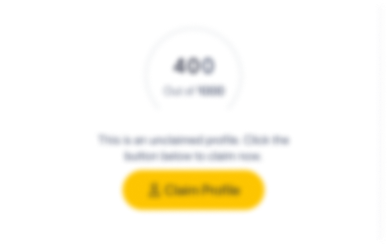
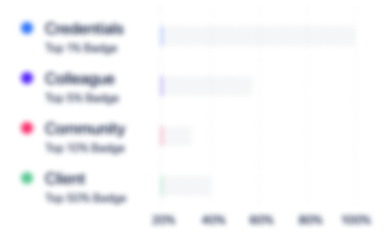
Bio


Credentials
-
Lean Six Sigma Black Belt
Breakthrough Performance Group, LLCNov, 2018- Nov, 2024
Experience
-
Franklin Brazing & Metal Treating
-
United States
-
Industrial Machinery Manufacturing
-
1 - 100 Employee
-
Quality Engineer
-
Dec 2022 - Present
-
-
Manufacturing Engineer
-
Feb 2019 - Present
-
-
-
Markem-Imaje
-
Switzerland
-
Automation Machinery Manufacturing
-
700 & Above Employee
-
Accounts Payable Coordinator -NAM
-
Nov 2015 - May 2017
Responsible for the financial accounting of functions related to accounts payable for Mexico, working with a BPO located in Brazil. This role reports to management in US and Europe. Main responsibilities include: Perform monthly reconciliations and closing activities Timely payment of vendors and expenses Update ERP to prepare for SAP migration Responsible for the financial accounting of functions related to accounts payable for Mexico, working with a BPO located in Brazil. This role reports to management in US and Europe. Main responsibilities include: Perform monthly reconciliations and closing activities Timely payment of vendors and expenses Update ERP to prepare for SAP migration
-
-
-
H&R BLOCK
-
Lawrence, MA and Keene, NH
-
Certified Tax Specialist 2
-
2009 - 2017
Prepare tax returns and consult with clients on tax matters. • Took initiative to pass successive examinations to move up to Tax Specialist 2 level. • Actively working towards achieving Tax Specialist 3. • Successfully processed over 150 returns last tax season and achieved 10% over goal of 50% in client retention. Prepare tax returns and consult with clients on tax matters. • Took initiative to pass successive examinations to move up to Tax Specialist 2 level. • Actively working towards achieving Tax Specialist 3. • Successfully processed over 150 returns last tax season and achieved 10% over goal of 50% in client retention.
-
-
-
Procter & Gamble
-
United States
-
Manufacturing
-
700 & Above Employee
-
Production Department Manager
-
May 1996 - Apr 1999
• For this major consumer products manufacturer, managed ten employees in production department operations for soap factory. Participated actively in company lean manufacturing practices, and in implementation and cost reduction projects • Our factory won several volume contests internally, which had a major impact on our growth. We were selected to be a model for this implementation to help other factories.• Achieved over 95% average improvement in reliability, quality assurance, safety, operations and maintenance costs, and employee development. This reduced waste resources to a minimum and improved the production process of the entire factory. • Improved production capacity by 60% by leading start-up of second continuous process operation to replace batch operation for more than fifty employees, plus engineers, contractors, and technology suppliers. Project included designing new team, integrating current continuous processes, and relocating batch operation employees while maintaining inventory in a construction area. Show less
-
-
New Initiatives Manager
-
Jan 1995 - May 1996
• Evaluated feasibility of projects, defining all cost and activities required to launch more than 30 new initiatives. Led interdisciplinary teams, including Advertising, Strategic Purchases, Customer Service, Production, Maintenance, Quality, and Finance, to follow up all activities on time and within budget. • Managed production of new initiatives until they became established products for production line; supplied special materials and scheduled production according to sales estimation without affecting regular production or inventory cost. Show less
-
-
Contract Manufacturing Manager
-
Jan 1993 - Dec 1994
• Spearheaded contract manufacturing operations, including responding to new package requests, developing procedures, and following up all logistics to receive product on time and avoid cancellations.• Implemented in-house operations to eliminate up-charge of contract manufacturer operation for Club Store presentations.
-
-
-
BUFETE INDUSTRIAL
-
Mexico City, Mexico
-
Process Engineer, New Technologies Department
-
1989 - 1993
• Researched new petroleum refining process technologies to develop basic engineering projects and computer simulations of new processes for several clients, such as PEMEX and Petro Ecuador. • Researched new petroleum refining process technologies to develop basic engineering projects and computer simulations of new processes for several clients, such as PEMEX and Petro Ecuador.
-
-
Education
-
MBA University of Iowa Henry B. Tippie School of Management
Master of Business Administration (MBA) -
LaSalle University, Mexico City, Mexico
Bachelor of Arts (B.A.), Chemical Engineering -
H&R BLOCK
Certified Tax Specialist 2
Community
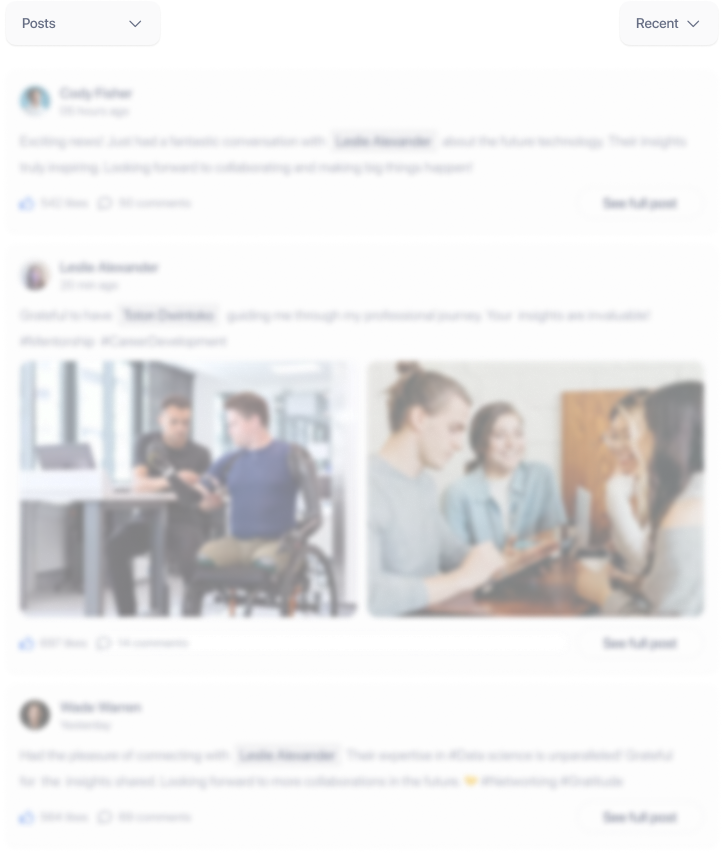