Leon Liu
at Lear Corporation- Claim this Profile
Click to upgrade to our gold package
for the full feature experience.
Topline Score
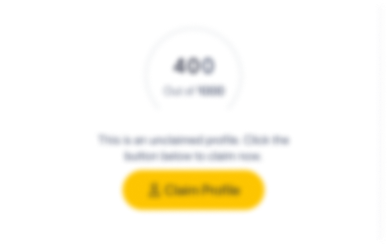
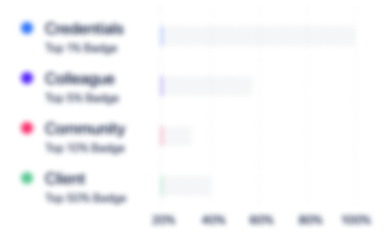
Bio


Experience
-
Lear Corporation
-
United States
-
Motor Vehicle Manufacturing
-
700 & Above Employee
-
-
Dec 2018 - Present
Lead the process ,maintenance, Lean and Trainer to ensure the better supporting to plant.Process1. Carry out capacity planning according to the production demand of SGM;2. Formulate the standard production capacity and standard manpower of each program, and formulate the monthly manpower and overtime requirements;3. Formulation and implementation of annual capacity improvement and manpower reduction plan;4. Daily maintenance and audit of the BOM to ensure the actual is the same as E-BOM;5. Overall management of IE standard work;6. Maintenance and update of LPS system (Manufacturing Execution System) and co-work with LPS team;7. Workshop layout planning and improvement.Equipment and factory maintenance:1. Daily maintenance of production equipment to ensure the normal operation of production;2. Monthly analysis of abnormal issue of production equipment and improve equipment OEE;3. TPM related activities;4. Monthly maintenance of key equipment;5. Maintenance and optimization of automation equipment;6. Daily maintenance of plant facilities;7. Daily maintenance of power equipment (generator, air compressor, high-voltage distribution room, water-cooled air conditioning, fire-fighting system);Lean production:1. Be responsible for managing projects aimed at improving production efficiency, quality and cost saving;2. Cooperate with engineering, production, quality, etc. to complete various indicators of the headquarters;3. Carry out lean production training for employees at all levels to strengthen their understanding of lean production knowledge;4. 5S management in the factory to ensure that 5S related standards are implemented in plant;5. Lead the implementation and tracking of the company's suggestion system, and improve the employee participation rate;6. Manufacturing cost analysis and cost saving plan implementation and follow-up; Show less
-
-
-
Oct 2016 - Nov 2018
1.Lean Trainer - train plant at all level for Lean methods (5S, VSM, TPM, Standard Operation…).2. Plant consultant - coordinate lean production projects and activities in China seating plant.3. Lead and participate continuous improvement activities to support company objective.4. Support shop floor in the implementation of improvement efforts during Kaizen Event.5. Continuously improve OEA and TPM audit performance every year.6.Collection and analyze all plants’ reports, and share with team.7.Award top 3 plants and plant CI, to encourage all plant to improve. 8. Share best practices with all plant.9.Other tasks assigned by supervisor.Total 16 seating plants in China.Outstanding analysis, problem solving and decision-making capability. Show less
-
-
-
Jan 2014 - Sep 2016
1. Develop yearly plant CI training, Operations Excellence Assessment (OEA) - Basics, Kaizen implementation plan and China CI deployment strategy.2. Lead plant to make lean Kaizen workshops through working together with plant team (TPM, Wastes elimination, 5S, Visual Management, Productivity Efficiency, Kanban Pull System.).3. Organize monthly plant Operational Excellence Assessment (OEA) –Basics process, identify improvement opportunities and drive execution of action plan.4. Develop and implement lean, OEA-B.Provide the lean training regarding philosophy, concepts, tools, processes and system.5. Leverage best practices and speed up plant learning process of lean and six sigma and other aspects to establishing operational excellence.6. Support plant to Establish world class level TPM.7. Others from manager. Show less
-
-
-
Dec 2012 - Dec 2013
1.Coordinate with cross function on new project and prepare the WI. 2.Maintain the M-BOM in QAD system base on the E-BOM.3.Layout the production line’s material racks to reduce the pickup time.4.Improve the line balance about the mixed production line.5.The error proofing design for the mixed production line.6.Implement the Lean system and provide a couple of training.7.Improve the layout base on the VSM.
-
-
-
Viasystems
-
Appliances, Electrical, and Electronics Manufacturing
-
400 - 500 Employee
-
Industrial Engineer
-
Jan 2010 - Nov 2012
1.product line New project assembly line layout: according the Takt time to design the assembly line. After Mass Production, design fixture, and improve the production line balance. Design fixture, consider with Poka Yoke and Ergonomics. 2.plant layout The new project planning, and coordinate relevant departments to complete the venue arrangements. In accordance with the relationship, layout the new office. According to the logistics mode, optimize the material warehouse and operation line. 3.time measurement Use MTM method to do the time observation,and found the Kaizen opportunities. Establishment of cycle time database,and maintain the data to improve the accuracy of Quotation. Changeover time observation, use five steps methods to reduce the time of ( SMED ) Single Minute Exchange of Die. 4.project Base on the evolution, select the appropriate project(80,20 principle) to do the Kaizen and implement the Pull system. 5.capacity planning Each end of the month,hold the meeting with PMC, CS, PD and other departments, according to customer demand, equipment condition, calculate the number of capacity loading and the corresponding solutions. 6.Cost compare Compare the cost between RFQ and actual cost.And support RFQ team to estimate the cost. 7.Other things from IE manager. 8.Familiar with the Turret punch, Stamping,Bending,Welding and assembly process. 9.Familiar with ISO14000. Show less
-
-
-
Quanta Storage Inc.
-
Taiwan
-
Computer Hardware Manufacturing
-
1 - 100 Employee
-
Industrial Engineer
-
Mar 2007 - Dec 2009
In charge of the new product introduce (EMS) including process design, roll up the labor cost ,line balance improvement and so on. Target to meet customer’s request. 1.Support sub-material plants(plastics,sheet metal parts)to meet the target time and price. 2.Re-layout the factory and the production line. 3.Time study and balance the production line. 4.Prepare and release the P-FMEA document 5.Provide shop-floor support and improve the subsystem assembly line to qualified. 6.Coordinate with cross functions on new project and prepare the SOP. 7.Make concepts of new equipment. 8.Solve the problems which are happened during the Pilot run with PE, ME, R& D and other related departments. 9.Release the charges order to supplier base on the line shut down database. 10.Develop the capabilities to meet the Company plan. 11.Familiar with the SMT, Injection molding and assembly process. 12.Familiar with TS16949 Show less
-
-
Community
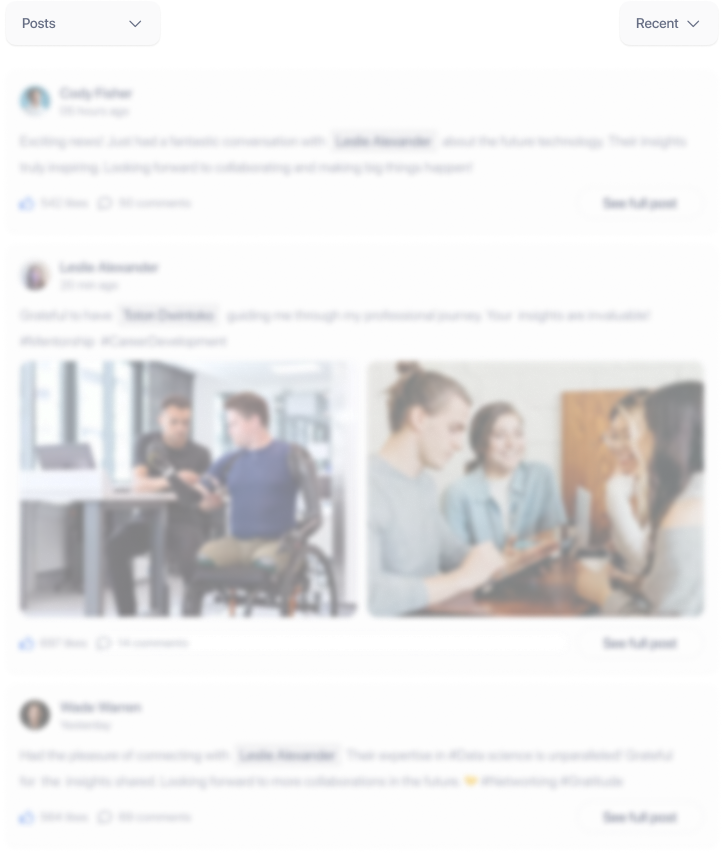