
Lenka Sebkova
Operations Manager at Stoko- Claim this Profile
Click to upgrade to our gold package
for the full feature experience.
-
English Professional working proficiency
-
German Limited working proficiency
-
Czech Native or bilingual proficiency
Topline Score
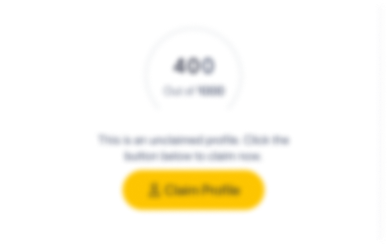
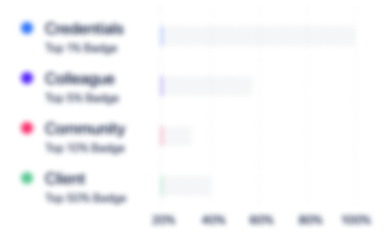
Bio


Credentials
-
Lean Six Sigma Green Belt (ICGB)
Cognitive Process Consulting Ltd.Jan, 2020- Nov, 2024 -
Lean Six Sigma Green Belt
MSys Technologies LLCDec, 2017- Nov, 2024
Experience
-
Stoko
-
Canada
-
Health, Wellness & Fitness
-
1 - 100 Employee
-
Operations Manager
-
Sep 2021 - Present
-
-
Process Development Engineer
-
Mar 2021 - Sep 2021
-
-
-
Arc'teryx Equipment
-
Canada
-
Design Services
-
700 & Above Employee
-
Continuous Improvement Specialist
-
Sep 2019 - Jun 2020
• Maintained a positive environment focusing on Lean Manufacturing strategies and continuous improvement initiatives to improve quality, efficiency and eliminate waste• Mapped business & production processes to predict and identify opportunities for CI and prioritize improvement ideas• Led problem-solving efforts and conducted root cause analysis to reduce inefficiencies in all areas of the business • Facilitated, coordinated and supported Kaizen projects with cross-functional teams with a high emphasis on safety, quality, and Lean Manufacturing• Organized, facilitated and coordinated Lean training and workshops• Balanced multiple projects and met deadlines while exemplifying exceptional leadership and project management skills• Worked with a wide range of stakeholders to understand, clarify, create and maintain manufacturing processes • Set up an SOP (Standard Operating Procedures) business process and co-created viable process documentation and the documents' organization and structure • Cooperated on definition, integration, and implementation of ERP, MES & PLM system within manufacturing processes• Implemented and evolved 6S and visual management tools
-
-
Engineering Technician
-
Jan 2018 - Sep 2019
• Performed data analysis while providing capacity studies and proposed optimal layout for production lines to ensure smooth workflow• Developed Material and Information flow tracking system serving to optimize WIP delivery • Worked on operational time studies and other supporting documentation needed• Managed models thought CS, SR & SMS stages• Assisted production & quality with solving production issues and process alignment• Wrote policies and operating procedures• Monitored abnormalities and defects (auditing)• Cooperated on training coordination & delivery• Developed garment construction knowledge
-
-
-
Magic Yacht Charters
-
Canada
-
Hospitality
-
1 - 100 Employee
-
Customer Service Representative
-
May 2017 - Dec 2017
• Followed customers´ requirements to meet their needs in the profesional way• Served customers during corporate events, wedding cruises, dinner cruises, staff parties, private boat charters etc.• Participated in the preparation, set up, tear down and clean up• Served from few people to hundreds, passed drinks, replenished buffet • Followed customers´ requirements to meet their needs in the profesional way• Served customers during corporate events, wedding cruises, dinner cruises, staff parties, private boat charters etc.• Participated in the preparation, set up, tear down and clean up• Served from few people to hundreds, passed drinks, replenished buffet
-
-
-
Cypress Mountain
-
Canada
-
Recreational Facilities
-
1 - 100 Employee
-
Ski Instructor
-
Dec 2016 - Apr 2017
-
-
-
Skiareál Špindlerův Mlýn
-
Czechia
-
Travel Arrangements
-
1 - 100 Employee
-
Process Improvement Specialist
-
Nov 2015 - Jun 2016
Implemented all the stages of continuous improvement of Six Sigma • Defined and described fundamental processes • Measured the speed of customer´s move among the processes • Analyzed collective data obtained from research • Suggested Improvements of the ongoing processes • Set up Control elements by identifying Key Performance Indicators to maintain the sustainability Implemented all the stages of continuous improvement of Six Sigma • Defined and described fundamental processes • Measured the speed of customer´s move among the processes • Analyzed collective data obtained from research • Suggested Improvements of the ongoing processes • Set up Control elements by identifying Key Performance Indicators to maintain the sustainability
-
-
-
Prague Adventures
-
Czechia
-
Events Services
-
1 - 100 Employee
-
Event Coordinator / Team Building Leader
-
Feb 2015 - Jun 2016
• Coordinated and instructed teams, organized team activities and games• Organized event program, followed precise time management• Prepared activity materials (maps, site designation, instructions)• Evaluated clients during activities• Entertained & supported clients in any needs during the activities• Guided & leaded groups of up to 10 people across Prague • Coordinated and instructed teams, organized team activities and games• Organized event program, followed precise time management• Prepared activity materials (maps, site designation, instructions)• Evaluated clients during activities• Entertained & supported clients in any needs during the activities• Guided & leaded groups of up to 10 people across Prague
-
-
-
Yellow Point spol. s r.o.
-
Czechia
-
Education Administration Programs
-
1 - 100 Employee
-
Event Assistant
-
Dec 2008 - Jun 2016
Team-building instructorSki instructor Team-building instructorSki instructor
-
-
-
-
Lean Six Sigma Coordinator
-
Feb 2015 - Jun 2015
• Cooperated on a University team project that was focused on increasing efficiency of patient´s transportation system• Mapped the employee´s system of sharing information, measured the speed of individual transports, analyzed shareholder interest, defined the project´s risks, transformed Voice of Customer to CTQ, gathered and analyzed collected data • Optimized transfer of hospital patients within the hospital area • Cooperated on a University team project that was focused on increasing efficiency of patient´s transportation system• Mapped the employee´s system of sharing information, measured the speed of individual transports, analyzed shareholder interest, defined the project´s risks, transformed Voice of Customer to CTQ, gathered and analyzed collected data • Optimized transfer of hospital patients within the hospital area
-
-
-
Foxconn Czech Republic
-
Czechia
-
Appliances, Electrical, and Electronics Manufacturing
-
700 & Above Employee
-
Continuous Improvement Coordinator
-
Dec 2012 - May 2013
• Applied the Lean Production Principles in order to improve business processes • Implemented the Kaizen concept within the company office spaces and supported the continuous improvement of environment through the organization• Cooperated with Lean Engineering Department in order to get valuable practical knowledge • Applied the Lean Production Principles in order to improve business processes • Implemented the Kaizen concept within the company office spaces and supported the continuous improvement of environment through the organization• Cooperated with Lean Engineering Department in order to get valuable practical knowledge
-
-
Education
-
University of Economics, Prague
Master's degree, Faculty of Business Administration -
Stockholms universitet
Stockholm Business School -
University of Economics, Prague
Bachelor's degree, Faculty of Business Administration
Community
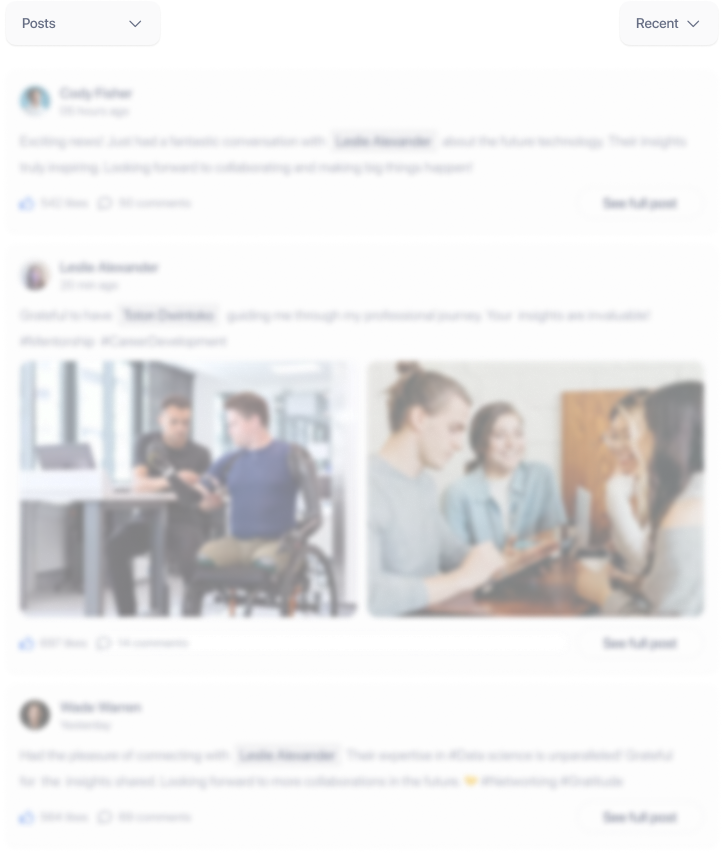