Len Anhold
Director of Operational Excellence & Automation at Fisher Barton- Claim this Profile
Click to upgrade to our gold package
for the full feature experience.
Topline Score
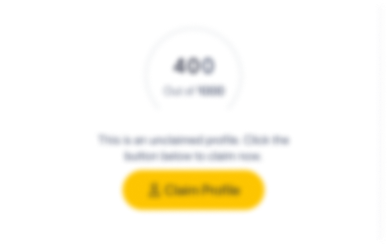
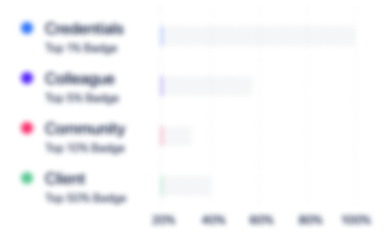
Bio


Experience
-
Fisher Barton
-
United States
-
Machinery Manufacturing
-
1 - 100 Employee
-
Director of Operational Excellence & Automation
-
Dec 2021 - Present
United States
-
-
Director Of Quality
-
Aug 2019 - Dec 2021
Watertown
-
-
-
Fisher Barton Specialty Products
-
United States
-
Industrial Machinery Manufacturing
-
1 - 100 Employee
-
Quality Manager
-
Nov 2018 - Aug 2019
Watertown, wi
-
-
-
-
Quality Manager
-
Nov 2018 - Aug 2019
-
-
-
SSI Technologies, Inc
-
United States
-
Mining
-
200 - 300 Employee
-
Plant Manager
-
Oct 2017 - Aug 2018
Janesville/Beloit, Wisconsin Area Responsible for Machining, Assembly and VVT/Iron Operations in East Plant of SSI Sintered Division
-
-
Quality Manager
-
Oct 2010 - Oct 2017
Manage Quality Department for Powder Metal Manufacturer. Reponsible for Customer Satisfaction, Systems and Continuous Improvement
-
-
-
Bourns, Inc.
-
Appliances, Electrical, and Electronics Manufacturing
-
700 & Above Employee
-
Quality Manager
-
Jan 2007 - Jul 2010
Quality Manager for Sensor Manufacturer. responsible for Quality Systems, Test Lab, APQP, Systems, Customer Satisfaction and Continuous Improvement
-
-
Sr. Quality Engineer
-
Jun 2006 - Jan 2007
-
-
-
SSI Technologies, Inc
-
United States
-
Mining
-
200 - 300 Employee
-
Quality Engineer
-
Oct 2005 - Jun 2006
Returned to Quality in October 2005 to lead APQP activities, manage customer issues and customer specific requirements. Developed new APQP process and associated documentation to compliment company's product realization process. Lead Quality Planning on new program launches in US and Mexico Developed an improved Nonconforming Material Review process that led to reduction in response time and scrap dollars.
-
-
Quality Engineer
-
Nov 2000 - Jun 2006
-
-
Production Leader
-
Jun 2002 - Oct 2005
Responsible for Production Team of a 78 million dollar manufacturing operation 11 Direct Reports (10 Production Team Leaders, 1 Maintenance Leader) Indirect Reports included 15 Maintenance Technicians and over 300 operators Responsible for 11 Production Lines that produce and ship more than one million units/month Leader of Plant Safety Team - Designed and implemented a Plant-Wide Safety Incident Database Creating and monitoring operational budgets Conduct monthly Plant-Wide… Show more Responsible for Production Team of a 78 million dollar manufacturing operation 11 Direct Reports (10 Production Team Leaders, 1 Maintenance Leader) Indirect Reports included 15 Maintenance Technicians and over 300 operators Responsible for 11 Production Lines that produce and ship more than one million units/month Leader of Plant Safety Team - Designed and implemented a Plant-Wide Safety Incident Database Creating and monitoring operational budgets Conduct monthly Plant-Wide meetings to report operational performance to employees Developed and implemented a Basic Skills of Quality curriculum for use in Training Classes
-
-
Quality Engineer
-
Nov 2000 - Jun 2002
Responsible for maintaining the business unit's compliance with all customer requirements, including customer PPAP coordination and submission, customer corrective/preventive actions, interface with customer on quality concerns and engineering issues, also responsible for analysis of customer warranty returns. Manage the activity of the business unit Quality Technicians. Coordinate launch activities of several of our products in Mexico facility, provide Quality direction for PPAP, PSO, safe… Show more Responsible for maintaining the business unit's compliance with all customer requirements, including customer PPAP coordination and submission, customer corrective/preventive actions, interface with customer on quality concerns and engineering issues, also responsible for analysis of customer warranty returns. Manage the activity of the business unit Quality Technicians. Coordinate launch activities of several of our products in Mexico facility, provide Quality direction for PPAP, PSO, safe launch activity and facilitating PPAP of move with customer. Milestones while in Q.E. position: Developed a new QOS and Management Review system for the business unit Designed and implemented an electronic document approval system for all quality system documentation Designed and implemented an improved Process Audit system Provided assistance and direction for successful move of product lines to Mexico facility
-
-
-
Lear Corporation
-
United States
-
Motor Vehicle Manufacturing
-
700 & Above Employee
-
Assistant Quality Manager/QS-9000 Management Representative
-
Jan 1999 - Oct 2000
Promoted in January of 1999 to serve the role of Assistant Quality Manager and QS-9000 Management Representative for 850-person JIT Tier 1 operation with 275 million dollars per year in sales. Responsible for maintaining the QS-9000 registration for the facility and reporting status to the Management Team. Interface with the GM- Janesville Assembly Plant on a daily basis to field concerns then spearhead appropriate actions. Coordinated customer PPAP activities. Acted as the Engineering… Show more Promoted in January of 1999 to serve the role of Assistant Quality Manager and QS-9000 Management Representative for 850-person JIT Tier 1 operation with 275 million dollars per year in sales. Responsible for maintaining the QS-9000 registration for the facility and reporting status to the Management Team. Interface with the GM- Janesville Assembly Plant on a daily basis to field concerns then spearhead appropriate actions. Coordinated customer PPAP activities. Acted as the Engineering interface between Corporate Engineering and the production plant, initiating trial runs, reporting on results and implementing engineering changes. Developed the facility's QOS and Management Review systems and coordinated Management Review Activity. Led cross-functional teams to complete corrective and preventive action plans.
-
-
Quality Engineer
-
Jun 1997 - Jan 1999
Returned to Lear from Milwaukee Wire Products as a Quality Engineer to serve a more diversified role. Maintenance of established QS-9000 system Lead Auditor of Internal Audit Team Voice of Customer and Voice of Process data analysis, tracking of customer satisfaction measurables APQP activities, process changes/deviations, inspection standard/acceptance criteria and visual aids. Champion for key activities within the plant including Problem solving (5-phase, 8-D), Reduction… Show more Returned to Lear from Milwaukee Wire Products as a Quality Engineer to serve a more diversified role. Maintenance of established QS-9000 system Lead Auditor of Internal Audit Team Voice of Customer and Voice of Process data analysis, tracking of customer satisfaction measurables APQP activities, process changes/deviations, inspection standard/acceptance criteria and visual aids. Champion for key activities within the plant including Problem solving (5-phase, 8-D), Reduction Variation Teams and QOS. Participated at customer site in Reduction Variation Teams to initiate improvement actions based on warranty and glove box survey data.
-
-
-
Lear Corporation
-
United States
-
Motor Vehicle Manufacturing
-
700 & Above Employee
-
Quality Systems Coordinator
-
Apr 1995 - Nov 1996
Coordinated activities necessary in a successful completion of QS-9000 registration. Documenting and auditing quality system documentation to comply with the QS-9000 standard, including, policies, procedures, work instructions and output documentation. Lead auditor for internal auditing system. Conducted training sessions on QS-9000 and Internal Auditing for salaried employees. Developed/maintained QOS and document control systems.
-
-
Quality Engineer
-
Apr 1995 - Nov 1996
JIT Manufacturer of Seat Assemblies
-
-
-
Nevada Bob's
-
United Kingdom
-
Retail
-
Assistant Manager
-
Jul 1993 - Apr 1995
Retail sales. Responsible for supervising sales staff, coordinating work efforts and handling customer complaints. Computerized several job aspects.
-
-
-
Milwaukee Wire Products
-
Motor Vehicle Manufacturing
-
1 - 100 Employee
-
Quality Technician
-
Jan 1987 - Jan 1993
QS-9000 Coordinator Returned to Milwaukee Wire Products to coordinate the successful completion of the QS-9000 registration activities within a six month time frame (Registration Audit
-
-
Quality Technician/Computer Operator
-
Jan 1987 - Jan 1993
Served a diverse role in an automotive stamping supplier, performing work in all departments.
-
-
Education
-
University of Wisconsin-Parkside
Business and Communications -
University of Wisconsin-Stout
-
Germantown High School
Community
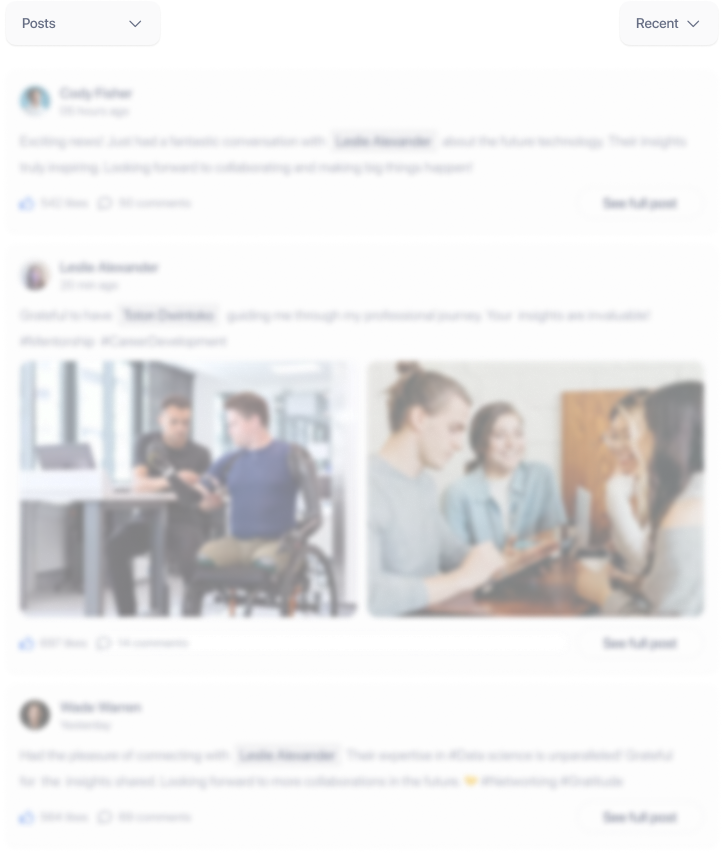