Lee Johnson
Account Manager at MSR-FSR, LLC- Claim this Profile
Click to upgrade to our gold package
for the full feature experience.
Topline Score
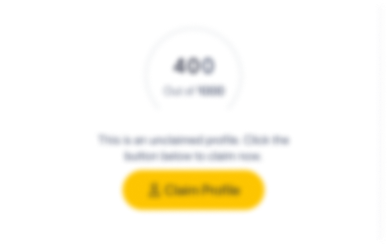
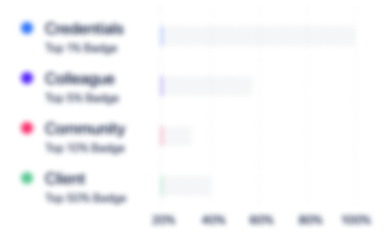
Bio


Experience
-
MSR-FSR, LLC
-
United States
-
Semiconductors
-
100 - 200 Employee
-
Account Manager
-
Mar 2022 - Present
-
-
-
Jefferson Lab
-
United States
-
Research Services
-
500 - 600 Employee
-
Fire Systems Technician
-
Aug 2017 - Mar 2022
Assist with troubleshooting and maintain Fire System Equipment Coordinate, schedule and manage tracking PMs of equipment. Create required procedures and process for Equipment Track Work Orders through Maximo are accurate. Update PM Records and schedules in Maximo as needed. Create operating and maintenance procedures. Interact with a host of vendors and contractors to execute requirements of installation, service and upgrades. Assist Vendors with any technical assistance when required and as needed. Plan and Track all maintenance activities and associated parts. Act as Safety Warden in assigned area following up in employee safety, operation safety, building safety and any other safety duties as needed. Monitor budgets and timeline of projects. Lead Team with upgrades and service contracts Show less
-
-
-
AM TECHNICAL SOLUTIONS
-
LEHI, UT
-
Field Service Engineer, Project Coordinator, Equipment Decommissioning
-
May 2017 - Aug 2017
Coordinate, schedule and manage tracking of decommissioning and maintenance of semiconductor equipment. Make sure the decommissioning requirement procedures are accurate by liaising with vendors, contractors and Client. Interact with a host of vendors and contractors to execute requirements of decommissioning. Assist Vendors with any technical assistance when requires and as needed. Confirm with Client of fulfillment of contract with each piece of equipment. Plan and Track all decommissioning activities and associated parts. Monitor budgets and timeline of projects. Certify the decommissioned equipment is prepared for shipment. Work together with equipment vendor as needed during the decommission process. Meet with Client on regular basis of status in regards to the decommissioning. Show less
-
-
-
RETRONIX INTERNATIONAL
-
BLOOMINGTON, MN
-
Field Service Engineer, Equipment Installer
-
Feb 2017 - Apr 2017
Provided troubleshooting, installations, repairs and upgrades to Semiconductor Equipment. Plan, schedule and track all commissioning and maintenance activities. Certify the equipment installation processes, from initial planning and organization to full equipment setup, installation and operations testing with customer satisfaction in mind. Accurately performed parts exchange on semiconductor manufacturing equipment while simultaneously arranging for equipment calibration and ensuring best practice cost control and purchase order methods. Calibrate and teach robotic machinery and a schedule basis. Work alongside of equipment manufacturer during installs and repairs as needed. Track all repairs and costs associated with installs though repairs. Show less
-
-
-
Vector Security
-
United States
-
Security and Investigations
-
700 & Above Employee
-
Project Manager
-
Feb 2016 - Dec 2016
Conduct research and analysis and develop proposals and review of measurements. Create job quotes for each installation project. Locate and create contracts for contractors with CRM software. Coordinate, schedule and manage Security and Fire Systems Installations. Ensured client satisfaction in all phases of equipment installation processes, from initial planning and organization to full equipment setup, installation and operations testing. Track all commissioning activities. Ensure accurate accounting requirements for each project. Interact with a host of contractors to execute requirements of installation. Liaise with contractors to secure complete full status reports upon completion. Show less
-
-
-
AM Technical Solutions, Inc
-
United States
-
Construction
-
200 - 300 Employee
-
Project Coordinator, Facilities Decommission
-
2015 - 2015
Coordinate, schedule and manage track decommissioning and maintenance of semiconductor equipment. Conduct research and analysis and develop proposals and review of measurements. Ensure accurate decommissioning requirement procedures by liaising with vendors and contractors. Recruit, interview and train temporary staff while simultaneously drafting completion and maintenance reports. Interact with a host of vendors and contractors to execute requirements of decommissioning. Show less
-
-
Project Coordinator, Gas Services
-
2015 - 2015
Plan, schedule and track all commissioning and maintenance activities. Continuously conduct research and draft proposal of measurements in support of all activities. Liaise with vendors and contractors to secure equipment and complete full status reports upon completion.
-
-
Project Coordinator, Equipment Support
-
2014 - 2015
Ensured client satisfaction in all phases of equipment installation processes, from initial planning and organization to full equipment setup, installation and operations testing. Provided customized training to customers on equipment repair and calibration and draft completion reports.
-
-
-
Micron Technology
-
United States
-
Semiconductor Manufacturing
-
700 & Above Employee
-
Coordinator and Senior Technician, Life Safety Systems Project Management
-
2008 - 2014
Ensured FAB tool life safety preventative maintenance scheduling, tracking, planning, upgrades and installations.Continuously monitored budget and timeline requirements and assigned duties accordingly. Collaborated cross-functionally with customers, vendors and construction teams. Drafted and delivered monthly reports to upper management that outlined completion ratio metrics and issues.Provided troubleshooting, installations, repairs and upgrades to Life Safety Systems and HPM Sensors, including the support of the Emergency Response Team during Life Safety Systems events and subsequent reporting. Directly supported the site incident prevention program by coordinating and approving site impact activities. Tracked and documented all operations on the SCADA software package. Show less
-
-
Project Manager, Parts Kitting
-
2004 - 2008
Established a facility-wide “Kitting process” that dramatically improved machine downtime by coordinating stakeholders, vendors, engineers personnel, inventory and procurement of 300 machines with 5,000 spare parts.Employed SAP and other databases to track bill of materials, cycle times and created financial analysis reports. Continuously researched cost savings measures by collaborating with outside service delivery vendors. Developed a roadmap for turn on, documented all procedures and trained all staff across departments. Show less
-
-
Equipment Engineering Technician
-
2003 - 2004
Accurately performed parts exchange on semiconductor manufacturing equipment while simultaneously arranging for equipment calibration and ensuring best practice cost control and purchase order methods. Organized both internal and external vendors for scheduling while assisting in PLC and SCADA installation. Supported recruiting and hiring processes for the Equipment Engineering department. Performed multiple Certified ISO Internal Audits.
-
-
Lead Principal Technician, Equipment Engineering
-
1998 - 2003
Served as Engineering Team Leader for equipment installation, repairs, calibration and upgrades. Coordinated preventative maintenance procedures and schedules while also providing individualized training. Continuously monitored department budgets and implemented cost control procedures as needed.
-
-
-
Germane System LLC
-
Chantilly, VA
-
Procurement/Inventory Manager
-
2003 - 2003
Led the daily management of purchasing and inventory practices for an innovative computer company. Spearheaded the implementation of Just in Time procurement. Successfully reduced inventory retention by $1.1M in just four months. Drafted procurement standard operating procedures for ISO 9002 and implemented multiple software solutions. Led the daily management of purchasing and inventory practices for an innovative computer company. Spearheaded the implementation of Just in Time procurement. Successfully reduced inventory retention by $1.1M in just four months. Drafted procurement standard operating procedures for ISO 9002 and implemented multiple software solutions.
-
-
-
IBM
-
United States
-
IT Services and IT Consulting
-
700 & Above Employee
-
Customer Engineer (Field Service Technician)
-
1992 - 1998
Served as Field Service Engineer for equipment installation, repairs, calibration and upgrades for AS/400 and RISC 6000 computer Equipment. Coordinated preventative maintenance procedures and schedules while also providing individualized for the customer/Client. Continuously monitored department budgets and implemented cost control procedures for my territory as needed. Received numerous Awards for being Number One in Customer Satisfaction.
-
-
Senior Technician
-
1984 - 1992
Served with the Engineering Team for equipment installation, repairs, calibration and upgrades.
-
-
Education
-
Northern Virginia Community College
Associate’s Degree, Electronics
Community
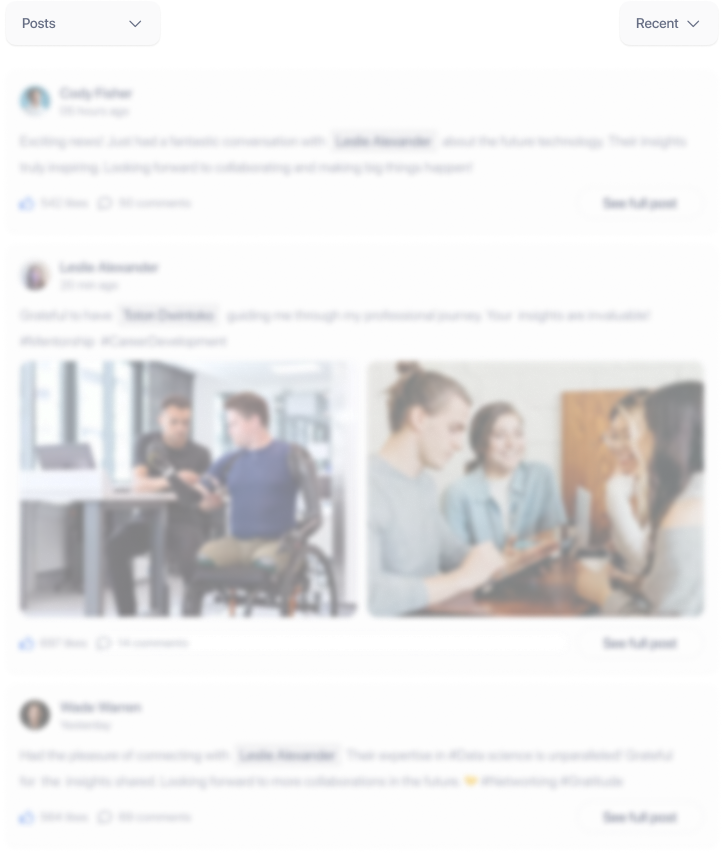