Lee Duckworth
at BatFast Sports- Claim this Profile
Click to upgrade to our gold package
for the full feature experience.
Topline Score
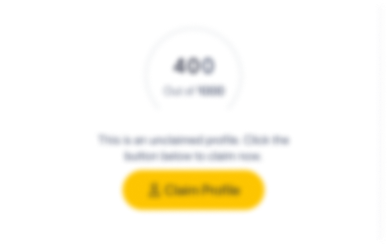
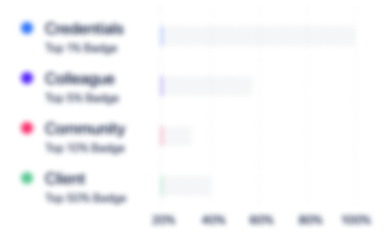
Bio


Experience
-
BatFast
-
United Kingdom
-
Spectator Sports
-
1 - 100 Employee
-
-
Apr 2020 - Present
Key achievements-Total redesign and setup of manufacturing supply chain of Batfast’s Impact scoring technology to enable the business to capitalise on the product demand from the customer. The Initial product was in prototype form, manufactured in-house with very little tooling or process controls. A full set of products took 36 hours to produce with 2 men at part cost of £400 each. Currently <£250 outsourced to Subcon manufacturer.-Patent granted – Impact scoring technology. Wrote all Invention disclosure documents to supply to the patent lawyers and supported the process throughout. (https://www.ipo.gov.uk/p-ipsum/Case/ApplicationNumber/GB2019154.0)-Redesign of key simulator equipment to enable efficient assembly & maintenance on location in a variety of countries. Assembly requires simplistic design to enable unskilled staff to build without very little equipment on site.-Introduced Test, validation & durability processes within the business – Validation of all hardware prior to customer release.-Factory layout design – Redesigned the whole unit area to allow improved visual management, product flow & introduction of an ERP system.-Deployed simulator technology under licence agreement throughout the UK & USA-Introduced Quality Control system to Batfast for complex sheet metal components. (critical/functional component aspects)-Development of automated ball retrieval concepts (POC) 250 balls per hour currently has to be manually picked after a customer session.-Industrial supervisor to a group of 4th year Loughborough University PDE/ME students working on automated ball retrieval for Batfast as their last year's project.-Development of Electromechanical products - Automated camera systems, robotic ball feeders, impact targets, projector control systems, ball release systems, robotic pick and place, conveyance systems.-Worked with 3rd party automation suppliers to develop enhanced products - Improved performance and reduced downtime. Show less
-
-
-
Sep 2019 - Apr 2020
-
-
-
Intelligent Energy
-
United Kingdom
-
Renewable Energy Equipment Manufacturing
-
200 - 300 Employee
-
Principal Engineer - Conceptual design, prototyping & manufacturing engineering
-
Jul 2010 - Aug 2019
As principal engineer I have been responsible for complex research, development and manufacturing projects • Conceptual design of Evaporatively cooled fuel cell – 6 Inventions created • Designed & Implemented manufacturing process for Bi-polar pressed plate production • Research, development and verification of fuel cell stack sealing failures on assemblies with multiple scenarios validated • Application of hydrophobic/hydrophilic materials and applications with regards to liquid water delivery • 8d reporting on failures • Design and Development of all Air, liquid & water cooled fuel cell stacks • Consult DFX principles to peers • Solidworks & CAM manufacturing software and CNC machine centres • Design & manufacturing of complex components • Design & manufacturing of complex manufacturing tools (Mould, Press, Verification) & fixtures Key Projects and Achievements • Development of process techniques required for full automation of air-cooled stack technology – Proven processes were applied to a fully automatic machine • Developed/delivered precision micro water delivery features within the Bipolar plate programme – Production of 25um pressed features which are performance critical • Set up one piece flow manufacturing cell for bi-polar plates in Lboro HQ, saving the business 17 hrs per 324 cell stack in non-value added work • Set up one piece flow manufacturing cell for bi-polar plates in the EU. Reducing part cost from £100 to <£10 • Complex compression moulding development – 3D seals. Multi component current collector assemblies, Endplate heating and various advanced plastics. • Delivered 100kW stack technology to major OEM automaker. • Development of untethered vacuum product carrier, Including design & production of ex-situ process characterisation hardware-for mounting onto magna motion track system (Electronically controlled conveyance system) • Development of web/reel based MEA's, GDL bonding on the fly • Development of web/reel based liquid/printed seals. Show less
-
-
-
American Pan Europe - A Bundy Baking Solution
-
Romania
-
Machinery Manufacturing
-
1 - 100 Employee
-
Engineering Manager
-
Jan 2008 - Jul 2010
• Manage Small Engineering team of Engineers • Identify and implement productivity improvements on CNC machining centres – Manufacturing strategy, improved tooling capability, set-up efficiencies and machine utilisation planning. • Coordinate tooling required for NPI and all current tooling maintenance, mods & Improvements. • Engineering budgetary control & planning. • Improve & advise Tooling/Engineering designs to increase efficiency, productivity, part QT, tool life & production machine capacity. • Fault finding and root cause analysis of production processes – using various QIP methods. • I.D of production wastes with resolutions. • Reduction of product cost via manufacturing strategy. • Business case creation – Manufacturing strategy of product range from batch production to cell production enabling less WIP, improved line efficiency and increased value-add. • Set up 5s system. • Design Tooling/machines/layouts to aid line changeovers and Improve Quality. • Create full plant layouts. • Identify new machinery for process improvements by written Specification/Justification – Wire forming machines, 3 axis CNC machining centres and Lathes, Robots, Projection welding machines, Trumpf presses, Power presses, Conveyors, Welding machines & Press brakes. • Facilities management. Key Achievements: • Introduced NPI system ensuring the new products introduced are implemented to plan – gated process control – swim lines • Coordinated new semi-automated bread tin seam welding machines from concept to implementation. Achieved 2 off machines, justified, Tendered, CAPEX, designed, manufactured & implemented in 10 weeks • Took over Prestige Industrial in 2008, part of a team which Identified products and processes to set up @ HQ. Coordinated machinery moves and process layouts at the HQ site • Improved production cell efficiencies via head count reduction – Improved process flow, cell layout and line balancing. Fabricated tin cell, 20 operators reduced to 12 after Improvements. Show less
-
-
-
Vaillant Group
-
Germany
-
Renewable Energy Semiconductor Manufacturing
-
700 & Above Employee
-
Project/Production Engineer
-
2005 - 2008
• Manage NPI from design concept to Manufacturing – using NPI process. • Manage CAPEX budgets and estimations. • Capital equipment purchasing for manufacture, feasibility, quotations and selection. • Identification of Manufacturing problem solutions & implementation plan creation. • Conduct PFMEA for manufacturing and resolution plans. • One piece flow build analysis and Line balancing from time study data. • TPM system setup with maintenance dept. – Job cards and part kanbans. • Create project plans for all NPI projects. • Work closely with the design dept. advising on various DFA. • Design and setup track and one piece flow build processes – approx. 30 employee cells. • Identify areas for efficiency improvements – Bottle neck Identification, poor performing tooling or complete restructure of manufacturing method. (fully auto lines) • Use modern lean manufacturing techniques (TPS) such as Kaizen, Poke yoke, JIT, Kanban, SMED & 5s. • Ability to create fully detailed process specifications and Engineering concept specifications. • Involved in problem solving teams delivering justified solutions to current Production issues. Ranging from redesigning key equipment to setting up new processes. • Solving test rig issues from hardware to software problems/fault finding under production pressure. • Analyse test rig data to form CP/CPK data, Implement solutions from data analysis/pareto charts. Key Achievements: • Developed Boiler chassis manufacturing method, all tooling/components are ergonomically positioned for ease of build. Quality & Productivity improvements achieved and the method rolled out across the whole manufacturing site for other product ranges. (Due to operator efficiency Increase >10%) • Development/implemented semi-auto boiler test rigs, improved quality & productivity achieved, which helped the business produce 150K extra boilers the following year. • Implemented screw feeding equipment into a One Piece Flow cell, which saved 30s per boiler manufactured Show less
-
-
-
AEROMATIX LIMITED
-
United Kingdom
-
Production Engineer/Toolmaker/Gas burner applications Engineer
-
Aug 1990 - Jul 2005
Applications Engineer: • Technical design and development of partially aerated and fully premixed gas burners. • Solving High & Low gas burning frequency resonance problems. • Premixed burner application and projects consist of cylindrical steel, ceramic and metal fibre constructed burners depending upon customer requirements. • Developments for Companies such as Vaillant , Bosch , Veissmann and Baxi • Foreign travel to customer manufacturing/Development sites to discuss application specification • Working direct with the customer to product approval – Worked with Vaillant for a 4 week period to approve their glow-worm UltraCOM range of boilers. Toolmaker/Production Engineer • Design, manufacture and repair of all types of press tools. • Design and manufacture of all types of Jigs and fixtures including automated robotic fixtures. • Lean manufacturing and SMED projects achieved – Fully automated press tools, cellular layouts and process flow. • Ensuring that the factory plant runs smoothly and efficiently – Production support. • Hydraulic and Pneumatic maintenance – Of machinery and press tooling. • Implemented 4 robotic manufacturing cells, created the floor layouts, help develop the construction of the cells with the suppliers. Also developed all tooling/Semi auto Fixtures to manufacture the burner assemblies. Quality & Productivity improvement were achieved. Show less
-
-
Community
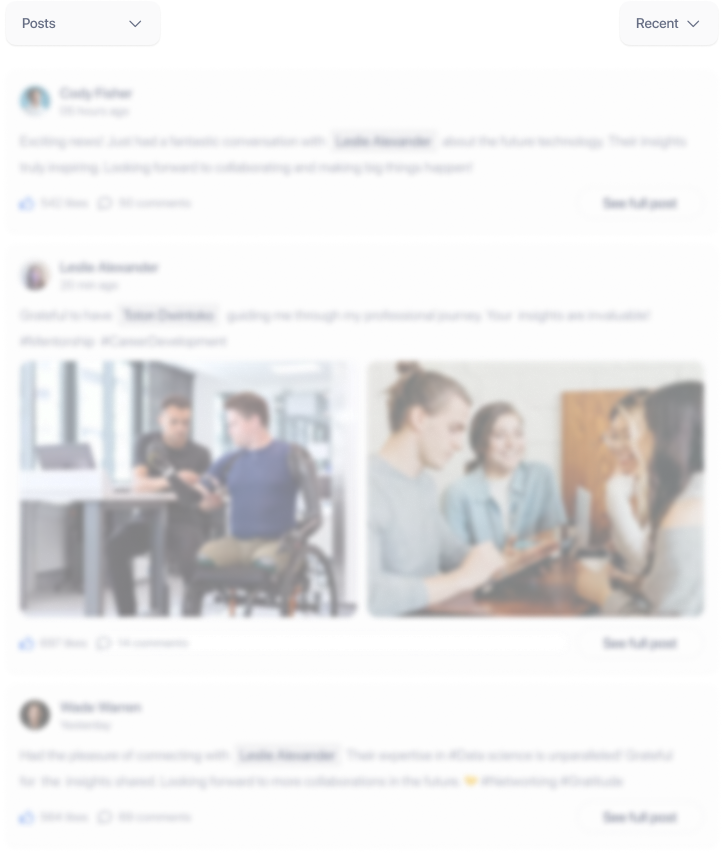