Laurent Defago
Senior Software Engineering Specialist at CAE Inc.- Claim this Profile
Click to upgrade to our gold package
for the full feature experience.
-
Français Native or bilingual proficiency
-
Anglais Full professional proficiency
-
Allemand Elementary proficiency
Topline Score
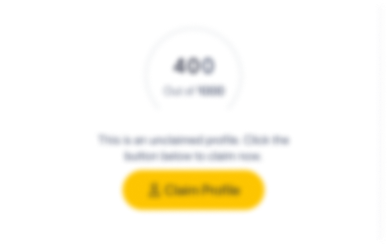
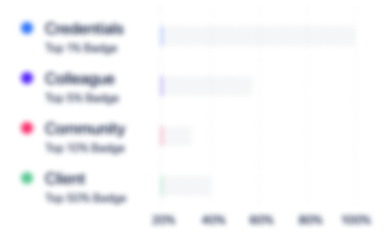
Bio


Experience
-
CAE
-
Canada
-
Aviation and Aerospace Component Manufacturing
-
700 & Above Employee
-
Senior Software Engineering Specialist
-
Dec 2018 - Present
In-Service Engineering Tactical Team In-Service Engineering Tactical Team
-
-
-
BOMBARDIER
-
Canada
-
Aviation and Aerospace Component Manufacturing
-
700 & Above Employee
-
Loads and Dynamics Engineering Specialist
-
Oct 2011 - Sep 2018
Lead engineer for all aeroelasticity analyses (fly-by-wire control and control interaction) for the development and qualification of the CS100 (A220-100), CS300 (A220-300) and Global 7000 - Developed state-space or frequency models of aircraft equipped with flight controls - Planned and realised aeroelastic stability studies, frequency response analyses - Validated flight control laws (with and without autopilot) according to aeroelastic stability criteria, proposed flight control law improvements (dynamic response filtering, sensor location, etc…) - Participated to the ground and flight vibration tests dedicated to aeroservoelasticity: prepared the test plans and the predictions, participated to the development of new testing methods, involved in the safety meetings with the flight crew, followed the tests in TM room as a responsible for safety calls, post-processed and validated the results - Realised certification studies and documents - Analysed in-flight incidents (flight test, post-certification activities and in-service) - Developed new Bombardier tools and methods for aeroservoelasticity and flight test analyses and improved existing tools - Use of Nastran, Patran, Matlab (Simulink, control toolbox, signal processing toolbox) and in-house bombardier tools (Speakeasy)
-
-
-
Safran Engineering Services
-
France
-
Aviation & Aerospace
-
700 & Above Employee
-
“Flight Loop, Simulation & Helicopter Loads” Project Manager
-
Sep 2006 - Oct 2011
Contractor work for Airbus Helicopters(H225 FFS and FTD for HELISIM, H225 FFS for Airbus Helicopters (Aberdeen), H635 FFS for Armasuisse, participated to H175 FFS, EC135 FTD level 3 and AS365 N3+ FTD level 3)Leaded a 5 people team: planned and managed the activities, conducted performance annual reviews, responded to tendersDeveloped flight loops (helicopter, engine and autopilot model assembly) for training simulators (FFS level D, FTD level 3 and FTD)- Planned the development work, quantified the level of effort and wrote the technical specifications- Developed Engine models: simulated thermodynamics, engine control laws, lubrication systems, electrical states, sensors, pilot controls, system interconnections, power transmission, failure cases- Tuned helicopter and engine models according to objective (flight manual performances, JAR/FAR dedicated flight test data) and subjective (pilot impressions) criteria- Analysed flight mechanics behaviour, supervised & analysed flight tests, achieved validation tests on simulator with or without pilot, worked on qualification rule evolutions (JAR FSTDH & FAR Part 60 bases)- Wrote all documents that were necessary to ensure the integration of the models in the simulator and the qualification of the simulator- Coded in C, Fortran & Shell languages, used in-house Airbus Helicopters tools (HOST, SMASH, ISC, HSVT) and Matlab (Simulink, Real-time Workshop)
-
-
"Flight Control/Structure Interactions" Engineer
-
Oct 2001 - Sep 2006
Contractor Work for AIRBUS(A400M, A380, A330, A320 & A3OX)Static aéroélasticity - Realised aircraft in-flight real shape calculations, estimated impact of flexibility on aerodynamic coefficients and surface control efficiencies, determined wing jig shape, dimensioned horizontal tails, fins & control surfaces.- Used Nastran, Patran and specific Airbus tools (Aselong, Aselat, Shell Fortran & Matlab routines)- Gave static aeroelasticity lecture in ENSICA & ENSAE (French aeronautical engineer schools).Flight control law design support- Developed state-space or frequency models of aircraft equipped with flight controls (Matlab, Simulink)- Realised aeroelastic stability studies, flight quality studies and in-flight manoeuvre turbulence & gust load calculations- Validated flight control laws according to aeroelastic stability or in-flight load criteria, proposed flight control law improvements, in-flight load reduction systems.- Used in-house Airbus tools (MatFlut, OSMA) and Matlab (Simulink).
-
-
-
Safran
-
France
-
Aviation and Aerospace Component Manufacturing
-
700 & Above Employee
-
Trainee Engineer
-
Sep 1999 - Jul 2000
Trainee engineer in “Overall Aerothermics” department - Validated a probabilistic method for high-pressure-turbine blade-tip clearance calculation - Applied this method on M88 engine in order to predict blade wear during engine aging. - Developed a simplified calculation tools based on formulations using parameters of the thermodynamic cycle (early development, test follow-up and analysis, integration to regulation software ...) - Aerothermics calculation, use of PATRAN and Safran Aircraft Engines in-house tools (THBN1200, CCL)
-
-
-
Université Claude Bernard Lyon 1
-
France
-
Higher Education
-
700 & Above Employee
-
Student
-
Oct 1997 - Jun 1998
Study and research project during my mechanics master: - Studied the mechanics of the boundary layer separation on the wing profiles: theoretical synthesis on the different types of separations and the separation reduction methods - Analysed the performances of a competition glider scale-model: build the wing of the glider, realized wing tunnel test to visualize the separation (oil and black smoke melt method and injection of smoke in the flow) and proposed improvements to this profile Study and research project during my mechanics master: - Studied the mechanics of the boundary layer separation on the wing profiles: theoretical synthesis on the different types of separations and the separation reduction methods - Analysed the performances of a competition glider scale-model: build the wing of the glider, realized wing tunnel test to visualize the separation (oil and black smoke melt method and injection of smoke in the flow) and proposed improvements to this profile
-
-
Education
-
Ecole nationale supérieure d'Ingénieurs de Constructions Aéronautiques
Engineer, Aerodynamics, Aircraft and Helicopter Flight Mechanics, Aeroelasticity, Engines, Control Laws -
Claude Bernard University (Lyon I)
Master of Mechanics, Structure Mechanics, Fluid Mechanics, Acoustics, Turbomachines
Community
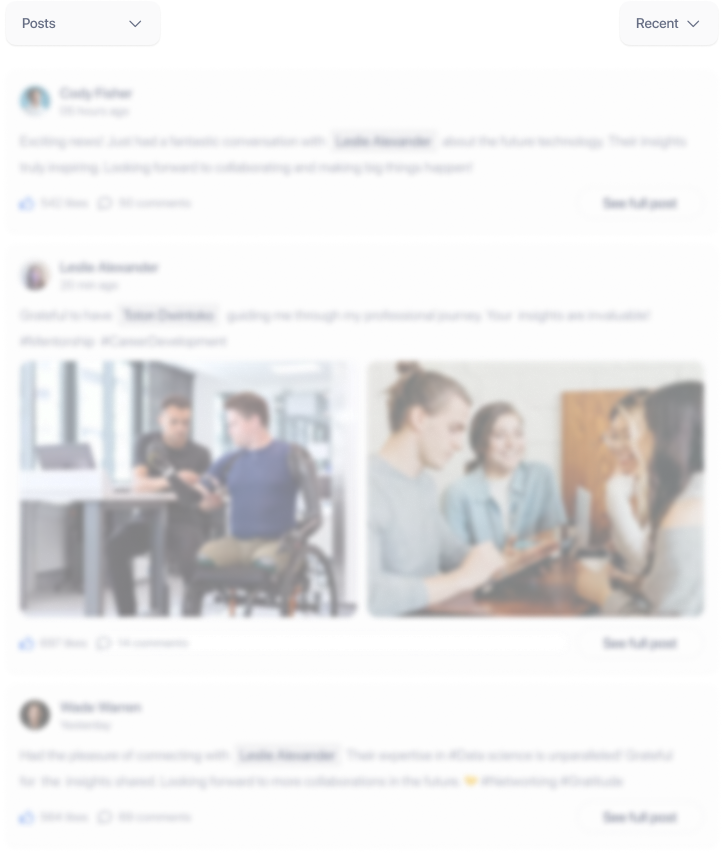