Laurence Evison-DIP NEBOSH CMIOSH OSHCR CQI/IRCA
Safety design at Malone Group- Claim this Profile
Click to upgrade to our gold package
for the full feature experience.
Topline Score
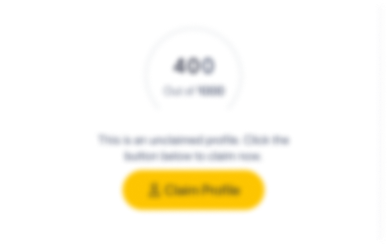
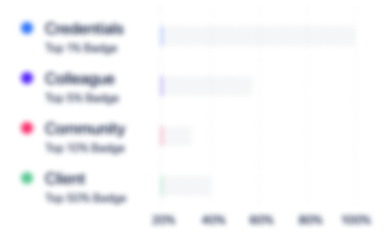
Bio


Credentials
-
nebosh general certificate
NEBOSH
Experience
-
MALONE Group
-
Ireland
-
Business Consulting and Services
-
1 - 100 Employee
-
Safety design
-
Oct 2020 - Present
-
-
-
Unilever
-
United Kingdom
-
Manufacturing
-
700 & Above Employee
-
Project health and safety lead
-
Aug 2019 - Oct 2020
Working for the client to raise the profile of health and safety on the project, I led the implementation of the health and safety management system from the ground up to cover the installation of the new magnum double dip chocolate line. The works included extensive strip outs and relocation of 3 other lines to create space for the installation phase, as well as commissioning the Ben and Jerrys line in the same factory. Working in the middle of a busy food production factory we erected a floor to ceiling hygienic screen to allow us to work without infringing upon the production activities of the wider factory. With an impeccable safety record for the project, and an absolutely minimal impact on timelines due to the usual contractor construction issues, the project was highly successful and very well organised in terms of the day to day running.Care was taken to ensure that the existing food factory standards were adopted and exceeded by all of the multidisciplinary contractors involved.In a first of its kind for unilever projects, the commissioning had to be completed from distance with a combination of laptops, cameras and VR modelling due to the COVID-19 pandemic restrictions on movement of people from country to country. Pioneering this method, the project finished with minimal delays
-
-
-
-
Health And Safety Manager
-
Apr 2019 - Aug 2019
Working as the health and safety manager for a rapidly expanding steel erection company on the UBB Gloucester energy from waste project. When I arrived on site the company required the creation of a comprehensive Health and safety management system having absolutely nothing on file.Everything from RAMS, to registers, training matrices, temporary works, inspection schedules and records all had to be created, whilst managing the health and safety needs of a workforce of 40+ steel erectors. Weldlecs work was predominantly concerned with correcting engineering mistakes made on previously installed steel
-
-
-
-
Site Manager
-
Dec 2018 - Feb 2019
Working as site manager for the principle contractor to oversee installation of the new waste water treatment plant at coca cola’s wakefield plant. The role was multidisciplinary, from steelworks and instrumentation, to fabrication and pipe fitting through to electrical installation, calibration and then commissioning of the plant. Working in tight confines, the project required excellent contractor management and work prioritisation skills, to prevent contractors working on top of each other and creating hazards. All of this had to be achieved whilst maintaining strict food safety standards and being subject to an internal core audit. The project boasted a flawless safety record, with continued stakeholder engagement a top priority throughout.
-
-
-
-
Construction Site Manager
-
Sep 2018 - Dec 2018
Overseeing all aspects of the installation and commissioning of a £5 million automated warehouse retrieval system. The role required excellent man management and organisational skills as the project was behind schedule when I took it over and had to make up for lost time. Managing multiple disciplines and employing a performance based solution focused attitude, as well as cultivating a positive culture and excellent relations with the client and end user led to a successful project with an average audit score of 93% over the life of the project
-
-
CDM manager
-
Mar 2018 - Sep 2018
Managing the mechanical installation of an ARS (automated retrieval system) for a large brewery warehouse. Works included the installation of racking systems, crane rails and shuttle car conveyor systems over 2 warehouse units. The project required the development of stakeholder relationships to create confidence in the principle contractor. A pro-active and positive attitude towards safety and man management resulted in consistently high audit scores and zero lost time incidents over the course of the project. Main duties and responsibilities included:• Completing safety walks and chairing safety meetings as key point of contact to the client on HSE matters.• Sharing HSE best practice across the industry and personal experiences to ensure compliance to health and safety requirements.• Reviewing and issuing RAMS and lifting plans for the project• Recording safety training documentation and maintaining records • Issuance and control of permit to work system. • Monitoring/addressing onsite HSE hazards to ensure compliance with UK legislation and best practice• Performing daily walk downs/site inspections including behavioural interventions and observations before recommending improvements.• Ownership of safety leadership and coaching to onsite workforce • Planning and managing activities including erection of racking, crain rail installations, crane lifts, hot works, work at height, commissioning etc
-
-
-
-
Management Consultant
-
Dec 2017 - Feb 2018
Providing remedial services to help BGS pass their ISO 45001 audit and achieve legislative compliance at their headquarters in Keyworth Nottingham. This project was self directed with the aim of producing a comprehensive safety management system for the National Geological Repository. Working alone and to a tight deadline, I built an action plan around a gap analysis, gathering existing documents and interviewing people from all levels of the business in order to create bespoke documentation that fit BGS needs.
-
-
-
CEMEX
-
Mexico
-
Wholesale Building Materials
-
700 & Above Employee
-
Health and Safety Manager
-
Aug 2017 - Nov 2017
Supervising the tunnelling works at the newly acquired griffin farm quarry in rugby. The works involved the digging of a 6 metre diameter 60 metre long concrete reinforced tunnel to allow the installation of a drag chain conveyor to connect in to the existing network.The role required an in depth knowledge of high risk confined space operations as well as managing multiple works spread out over a large geographical area. Contractors managed included pilling and groundworks, public highways with liaisons with the local councils as well as fencing, forestry and security contractors.In addition the project required good knowledge of IEMA standards as there were extensive great crested newt colonies. Great crested newts are a protected species and so their relocation had to be approached with appropriate care and consideration.The main of the project was heavily focused on engineering with a focus on three stage excavation and spraying techniques to ensure the tunnel was shored up as it was extended. Work was 24 hour and duties included but were not limited to:• Reviewing and approving RAMS • Carrying out site inductions • Hosting safety meetings• Issuance and control of permit to work system• Road settlement testing • Ensuring contractual compliance with construction phase plan• Client facing
-
-
-
Hitachi Zosen Inova
-
Switzerland
-
Services for Renewable Energy
-
700 & Above Employee
-
HSE Advisor/Behavioural change Advisor
-
May 2017 - Jul 2017
Working for the principle contractor on the ferrybridge FM2 multifuel blue book project, I was part of a large multidisciplinary safety team managing all aspects of health and safety from the client level down to subcontractors covering aspects such as scaffolding, steel erection. Civils work, non destructive testing, pipe fitting fire wall installation and lagging. Duties included but were not limited to:• Audits/inspections• Review and approval of documents• Issuance and control of permit to work system• Chairing union safety reps meetings and site tours• Chairing safety and client meetings• Keeping detailed contractor records of competencies and equipment• Monitoring of lighting for nights work, noise monitoring for nuisance in the local community and environmental monitoring• Environmental monitoring carried out to IEMA standards The standards of the project were exceptionally high and the dynamic of the team was to perform to as high a level as possible innovating to find solutions to keep the project on target whilst ensuring the highest standards of health and safety.To this end, my psychology knowledge was utilised frequently. Assisting the Health and Safety manager we developed a behavioural change program for the project with the aim of eventually rolling this out across the business. The purpose of this was to push the safety culture on site and beyond to the next level to achieve workforce engagement with the values of actively caring that HZI champion.The project provided me with unique opportunity to put my knowledge of IEMA standards in to practice as there were colonies of great crested newts on site that had to be protected and carefully relocated. To this end I worked closely with the environmental officer to ensure their habitat was not adversely affected by construction activities
-
-
-
CEMEX
-
Mexico
-
Wholesale Building Materials
-
700 & Above Employee
-
HSE Manager
-
Mar 2017 - May 2017
Working for the principle contractor on a busy multi-contractor site shutdown on a cement plant. My responsibilities included the following:• ensuring contractor compliance with the construction phase plan• carrying out audits and inspections• Liaising to make sure there was continuity of information and standards from the day to the night shift in the form of a hand over• Chairing safety meetings, taking and distributing minutes• Chairing co-ordination meetings• Giving inductions• Actioning near miss and hazard alert reports• Reporting and correcting poor standardsThis role required an understanding of refractory, internal bricking of a kiln and engineering work in order to be effective and ensure safety standards were appropriately high
-
-
-
British Geological Survey
-
United Kingdom
-
Research
-
400 - 500 Employee
-
QHSE consultant
-
Feb 2017 - Mar 2017
Working as a Quality, Health Safety and environmental consultant with the British Geological survey at their headquarters in Nottingham to carry out machinery and activity assessments on geo processing/finishing equipment at their corestore. This role required in depth knowledge of the PUWER regs as well as the Supply of Machinery Safety Regulations in order to adequately assess all of the machinery.The machinery involved predated both the Health and Safety At Work etc act as well as the formation of the European union and all of its directives, providing unique challenges in accessing manufacturers information. The machinery assessed also included machinery that had been manufactured on site, and so required separate assessment to ensure it conformed with the essential health and safety requirements as required under the SMSR 2008.
-
-
-
ZRE KATOWICE S.A.
-
Poland
-
Mechanical Or Industrial Engineering
-
100 - 200 Employee
-
Health And Safety Manager
-
Oct 2016 - Feb 2017
Health and Safety Advisor on the Cramlington chp new build biomass power station. Responsible for meeting the Health and Safety needs of 40 steel erectors carrying out high risk work at height in a dynamic environment. This role often included the lifting of heavy and variably shaped loads requiring transport across a busy construction site and crane lifts to be secured in to position.Responsibilities for a number of subcontractors including scaffolders, contract lifters and non destructive testing speciailist’s were also a part of this role, and required guidance through submitting RAMS and operative competencies as well as day to day safety supervision.The role posed challenges in effective communication as the workforce is predominantly polish speaking. Aside from general Health and Safety and client liaison responsibilities, the role required the rewriting of existing documents and an overhaul of the existing safety management systems in order to meet legislative standards and to ensure worker safety and principle contractor policy compliance.
-
-
-
Actavo
-
Utilities
-
700 & Above Employee
-
Health and Safety Manager
-
Aug 2016 - Sep 2016
Health and Safety Advisor on the Lindsey Oil Refinery (LOR) responsible for looking after 35 Scaffolders carrying out scaffold deconstruction work on numerous industrial units. Main duties include carrying out site inductions, administering company and client drug and alcohol testing, delivering safety briefs to educate the workforce on the importance of health and safety, carrying out inspections and audits, maintaining records, and representing the company in site safety meetings. Other Health and Safety duties and achievements include:• Acts as the bridge between what is happening on site and the wider corporate culture of the company by reporting to regional and national safety management• Regularly liaises with the Site Manager to ensure he is kept up to date with daily reports as to the condition of site safety and the wellbeing of the workforce• Maintains the excellent safety record of the site to ensure a perfect safety record of zero injuries or incidents continues
-
-
-
Lindner Group
-
Germany
-
Construction
-
700 & Above Employee
-
Health and Safety Manager
-
Feb 2015 - Aug 2016
Health and Safety Advisor primarily focused on managing the safety needs of over 40 personnel with key responsibility for inducting new starters, briefing the workforce on RAMS, delivering tool box talks and training up staff. Conducted site-based audits and liaised closely with the principle contractor to ensure that all works carried out complied with legislative procedures. Additionally in charge of overseeing the health and safety needs of 3 other companies - F and H who installed pipe work for the new build and 2 trace heating companies, Thimm and Trace-tec. Demonstrated advanced managerial and communication skills to balance the bespoke needs of each of the 3 companies. Further accomplishments and duties as Health and Safety Advisor were:• Achieved an excellent safety record for the Lindner site • Provided a high level of service to F and H that exceeded expectations • Obliged to pass the safety management of F and H to another Safety Advisor due to contract clashes• Resulted in the company demanding back said services due to high level of attention to detail and superior management qualities after just 2 weeks
-
-
-
-
Health and Safety Officer
-
Dec 2013 - Jan 2015
Safety Officer / Health and Safety Advisor with full ownership for the safety of 20 staff members during major plant remedial works complying with full construction design management regulations. Created and implemented safe systems of work, risk assessments and method statements for allocated tasks on a daily basis ensuring all work was completed safely while remaining compliant with legislation and the requirements of good practice. Meticulously checked and issued permits to work and tasked as the nominated person for attendance at all safety meetings and safety tours. Maintained key documentation including asset registers, inspection records and all supporting documentation and regularly informed the crew with tool box talks and personnel inductions. Proactive control of PPE issue and stock levels and undertook a supporting role in incident investigations and reporting. Provided reliable holiday and sickness cover for crew supervision and reported to the Risk Manager.• Quick to grasp new ideas and concepts leading to being granted autonomy to perform duties without supervision and being sent to other customer sites to perform similar duties• Commended by the client for taking over the day-to-day running of the company’s most profitable site due to the Safety Manager running other sites the company had procured• Proved an indispensable asset as otherwise the company would not have been able to run that site • Exposed to and dealt with multiple health and safety challenges including infection control due to flood water, the safe use of mobile industrial vacuum equipment and writing suitable documentation for the removal of cement materials within storage silos during flood remedial works • Compiled and supplied detailed weekly progress reports to the head office and CDM principle contractor
-
-
-
Costain Group PLC
-
United Kingdom
-
Civil Engineering
-
700 & Above Employee
-
health and safety experienced holewatcher firewatcher and general labourer
-
May 2013 - Oct 2013
Trainee Health and Safety Advisor june 2013- Nov 2013 Ensured the safety of confined space work in high risk environments and skilled in safety requirements required for the high risk industry of refineries. Represented employee safety concerns during contract disputes and aided the site supervisor in running work gangs and reviewing safety paperwork. Fire Watcher | Safety Attendant May 2013 – june 2013Safety Attendant with responsibility during the hot works on refineries, working safely on shutdowns, working at height and confined spaces and carrying out risk assessment method statements, safety audits and writing up health and safety reports.
-
-
Education
-
The University of Huddersfield
BSE Social Psychology, psychology with sociology -
lindsey upper school
Community
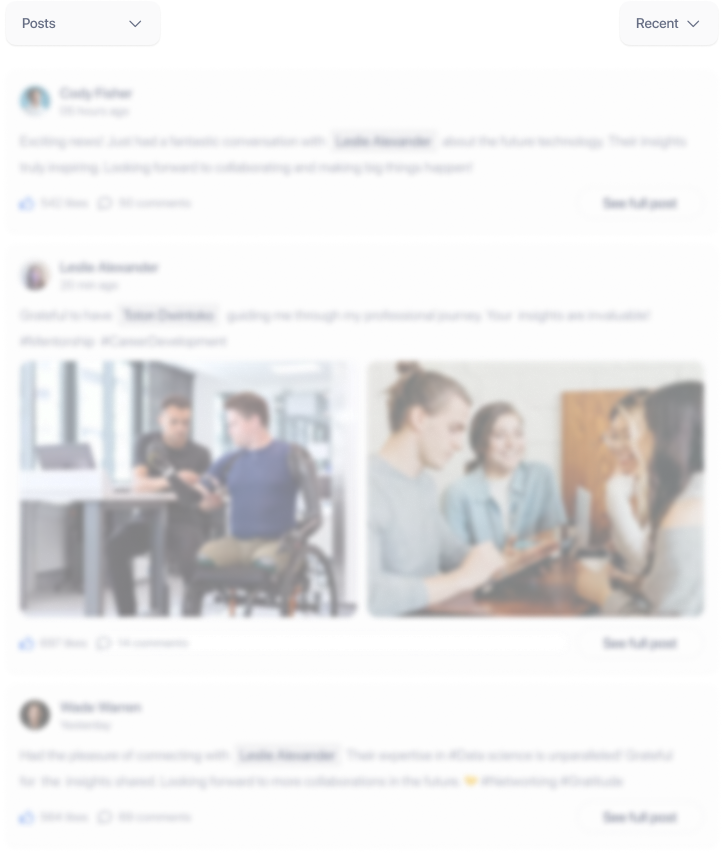