Lauren Shurtleff
Quality Assurance Analyst at Intellijoint Surgical Inc.- Claim this Profile
Click to upgrade to our gold package
for the full feature experience.
-
English -
Topline Score
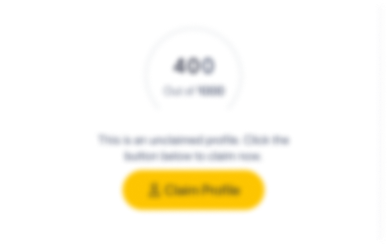
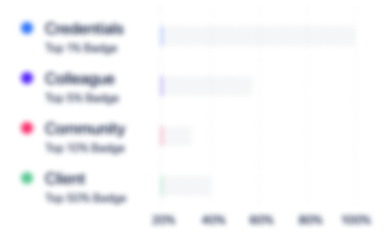
Bio


Credentials
-
Unconscious Bias: Fuel Diversity and Become a Better You
UdemyMar, 2023- Nov, 2024 -
Introduction to Software for Medical Devices and IEO 62304
Medical Device HQDec, 2022- Nov, 2024 -
Practical Regulatory Affairs 2020 - USA FDA Medical Devices
UdemyNov, 2022- Nov, 2024 -
Pharmaceutical and Medical Device Innovations
CourseraSep, 2022- Nov, 2024 -
Introduction to Medical Software
CourseraJun, 2022- Nov, 2024 -
Learn JIRA with real world examples (+Confluence bonus)
UdemyApr, 2022- Nov, 2024 -
ISO 13485 - IQOQPQ - Process Validation for Medical Devices
UdemyFeb, 2022- Nov, 2024 -
Software Quality Assurance
UdemyFeb, 2022- Nov, 2024 -
Applied ISO 14971 Medical Device Risk Management
UdemyJan, 2022- Nov, 2024 -
Introduction to Agile Development and Scrum
CourseraDec, 2021- Nov, 2024 -
ISO 13485:2016 Auditor Training
SAE InternationalNov, 2021- Nov, 2024 -
Dino 101: Dinosaur Paleobiology
CourseraSep, 2021- Nov, 2024 -
"Exceptional Technical Writing"
Hurley Write, Inc.Aug, 2021- Nov, 2024 -
Quality Process Analyst
ASQ - World HeadquartersOct, 2019- Nov, 2024
Experience
-
Intellijoint Surgical Inc.
-
Canada
-
Medical Device
-
100 - 200 Employee
-
Quality Assurance Analyst
-
Jan 2021 - Present
- Review, analyze and report on quality issues and propose disposition and corrective actions for recurring discrepancies - Support quality assurance activities related to audits, training, change control, document and record management - Prepare periodic reports to support the Quality Management System - Analyze sources of quality data to identify problem trends and opportunities for improvement - Assist in the maintenance, approval and creation of quality documentation - Represent quality in product development initiatives (e.g. New Product Development, Verification/Validation, Sustaining Engineering, etc.) - Support planning and execution of design control deliverables - Maintain the content of the Design History File to regulatory and customer requirements - Review and approve product records for release (in-process/final) according to defined requirements and specifications - Inspect products for acceptance according to material specifications - Participate in the development of new medical device technologies, understanding how we can meet all required quality and regulation requirements with a newly defined process - Complaint Manager and leads in investigation and closure of product issues and complaints Show less
-
-
-
Abbott
-
United States
-
Hospitals and Health Care
-
700 & Above Employee
-
Intermediate Quality Engineer
-
Sep 2017 - Dec 2020
- Established and refined Quality Management System and CAPA documentation, standards, and instructions. - Participates in the timely resolution of quality issues and events impacting operations and engineering outputs by providing sound quality knowledge and advice, in line with quality procedures, regulatory requirements and compliance expectations. - Builds and maintains successful cross functional relationships with internal departments such as Engineering, Manufacturing, Operations and Quality. This includes regular time spent in manufacturing areas (cleanrooms, labs and other areas). - Participated in activities to meet internal and external stakeholder deadlines for new product development - Developed and refined incoming and in-process inspection protocols - Review and approval of documentation, including but not limited to: document changes, CAPA system documentation FUE/process and product validation / verification activities. - Perform audit inspection readiness activities - AAMI Quality System Regulation Certified Show less
-
-
-
JYSK
-
Denmark
-
Retail
-
700 & Above Employee
-
Sales Associate
-
Apr 2013 - Aug 2017
- Maintained constant presence on sales floor to address customer needs - Recommended appropriate items and lead customers to selections - Helped maintain displays and constantly restocked products - Assisted in audit counts - Lead summer patio department in terms of sales, organization, and ordering for customer purchases - Won multiple sales contests across the district of the company and in-store - Maintained constant presence on sales floor to address customer needs - Recommended appropriate items and lead customers to selections - Helped maintain displays and constantly restocked products - Assisted in audit counts - Lead summer patio department in terms of sales, organization, and ordering for customer purchases - Won multiple sales contests across the district of the company and in-store
-
-
-
Terra Greenhouses Limited
-
Canada
-
Retail
-
1 - 100 Employee
-
Sales Associate
-
Apr 2015 - Aug 2015
- Familiarized myself of all product sold in the annual and perennial departments i.e. tropical plants, grasses, sun and shade plants - Made recommendations of product to enhance purchases and encourage good gardening - Unloaded product and arranged displays - Familiarized myself of all product sold in the annual and perennial departments i.e. tropical plants, grasses, sun and shade plants - Made recommendations of product to enhance purchases and encourage good gardening - Unloaded product and arranged displays
-
-
-
Parmalat Canada
-
Canada
-
Food and Beverage Manufacturing
-
400 - 500 Employee
-
Quality Control Technician
-
May 2014 - Aug 2014
- Monitored packing, code dating, and labeling of product to reduce customer returns, prevent production errors, and limit cost of shrink - Ensured products met required standards through inspections of raw materials and finished product - Validated and monitored machine operation used within the department - Monitored packing, code dating, and labeling of product to reduce customer returns, prevent production errors, and limit cost of shrink - Ensured products met required standards through inspections of raw materials and finished product - Validated and monitored machine operation used within the department
-
-
-
Hamilton Tiger-Cats Football Club
-
Canada
-
Spectator Sports
-
100 - 200 Employee
-
Seasonal Worker
-
May 2013 - Nov 2013
- Assisted in the set up and take down of the temporary stadium before and after each game - Ensured the safety of the guests at the stadium by monitoring activities of guests - Enhanced guest experienced by creating positive interactions - Assisted in the set up and take down of the temporary stadium before and after each game - Ensured the safety of the guests at the stadium by monitoring activities of guests - Enhanced guest experienced by creating positive interactions
-
-
-
University of Guelph
-
Canada
-
Higher Education
-
700 & Above Employee
-
Undergraduate Student Researcher
-
May 2012 - Aug 2012
- Worked independently on a summer research project that involved various testing and analysis of a unique biodegradable polymer - Independently sought and received training for various technical equipment and was responsible for shipping specimens to be tested at different facilities - Weekly sent progress reports to supervisor of experiments conducted, analysis, and future works. - Produced a manuscript at ends of work term that summarized the research conducted Acknowledged on: Mukherjee, T., Czaka, M., Kao, N., Gupta, R.K., Choi, H.J., Bhattacharya, S., Dispersion study of nanofibrillated cellulose based poly(butylene adipate-co-terephthalate) composites. Carbohyd. Polym. (2013) 102: 537-542 Tested the unique biodegradable polymer with a variety of equipment to test mechanical and chemical properties: - Differential Scanning Calorimeter - Thermogravimetric Analysis - Heat Deflection Temperature - INSTRON - IZOD - Dynamic Mechanical Testing - Scanning Electron Microscope - Atomic Force Microscopy Show less
-
-
-
Fortinos Supermarket Ltd
-
Food & Beverages
-
500 - 600 Employee
-
Salad Bar Clerk/Bulk Foods Clerk
-
Aug 2007 - May 2012
- Efficiently re-stocked bulk items while rotating new product and cleaning displays - Responsible for ordering product when low levels were observed - Arranged seasonal displays and advertising items weekly while ensuring prices for both bulk and produce departments were correct - Responsible for training new employees on health and safety standards and protocols of the position - Directed team of 4-5 individuals to complete daily tasks on time and with care - Awarded raise for exceptional performance Show less
-
-
Education
-
University of Guelph
Bachelor’s Degree, Biomedical/Medical Engineering
Community
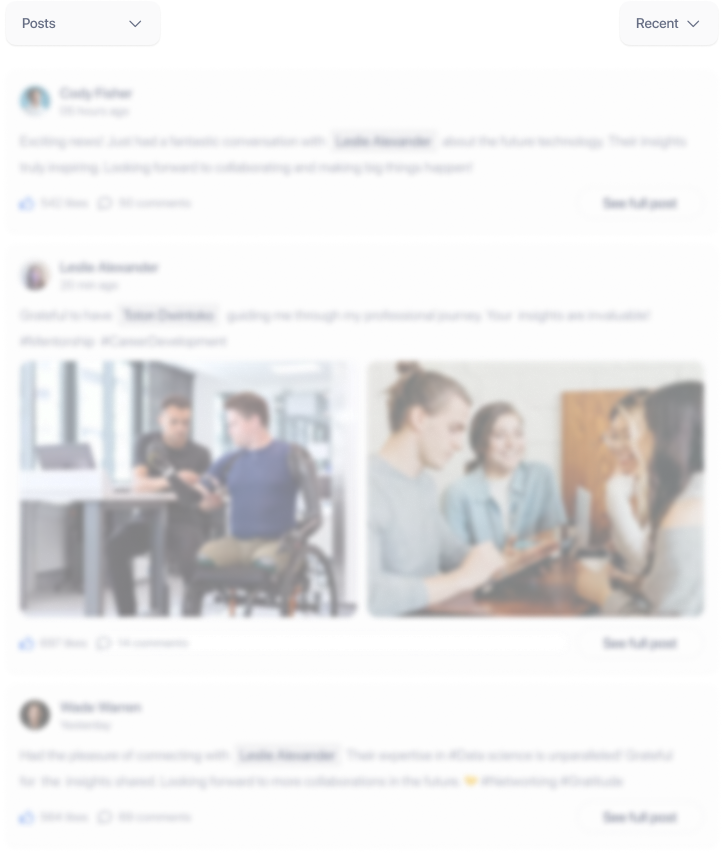