Larry Napier
Senior Certified Recovery Specialist at chargeguard- Claim this Profile
Click to upgrade to our gold package
for the full feature experience.
Topline Score
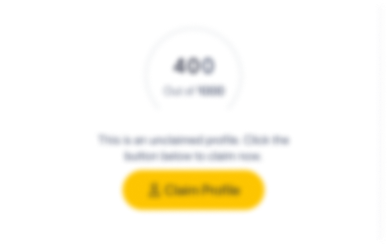
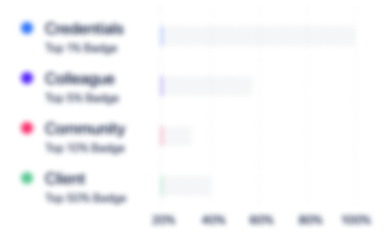
Bio

Scott Robb
My name is Scott Robb and I am currently the Engineering Manager at Midway Product Group. I am writing this letter on behalf of Larry Napier who has expressed interest in working for your firm. During my tenure at American Axle & Mfg. I had the privilege of working directly with Larry. He has exceptional expertise and passion for engineering, quality, and the manufacturing process. He led many of our company's quality improvement and cost reduction activities, resulting in tremendous improvements in both. In addition, Larry demonstrates a tremendous work ethic, putting in the extra hours necessary to ensure a project is completed on time. He's also a good mentor to other members, patiently explaining / training in a methodical manner. I wholeheartedly recommend Larry as a potential member of your team. Regards, Scott Robb Product Engineering Midway Products Group 1 east Layman Drive Monroe, MI Cell 419 619 5171

Sidharth Jayanth
I had opportunity to work with Larry at Associated spring. Larry was clearly interested in helping me grow as an employee. He was amiable mentor and guided me on PPAPs , 8D problem solving approach and other important aspects of Quality systems. Whenever I had concerns or questions, Larry responded well and even followed up later. His patience and willingness to help have made me motivated to do the best job I can.

Niladri Das
As supplier management engineer Larry worked well with all suppliers and resolved issues diplomatically and skillfully. Fairness is essential to this job and Larry was a great practitioner of it. Larry led numerous supplier quality issues to fast resolution through effective project management skills and helped ACH plants meet their quality targets. He is also an excellant quality engineer and has good knowledge of QS/TS requirements. As an individual Larry brings a great attitude to work and is a pleasure to have as part of a team.

Scott Robb
My name is Scott Robb and I am currently the Engineering Manager at Midway Product Group. I am writing this letter on behalf of Larry Napier who has expressed interest in working for your firm. During my tenure at American Axle & Mfg. I had the privilege of working directly with Larry. He has exceptional expertise and passion for engineering, quality, and the manufacturing process. He led many of our company's quality improvement and cost reduction activities, resulting in tremendous improvements in both. In addition, Larry demonstrates a tremendous work ethic, putting in the extra hours necessary to ensure a project is completed on time. He's also a good mentor to other members, patiently explaining / training in a methodical manner. I wholeheartedly recommend Larry as a potential member of your team. Regards, Scott Robb Product Engineering Midway Products Group 1 east Layman Drive Monroe, MI Cell 419 619 5171

Sidharth Jayanth
I had opportunity to work with Larry at Associated spring. Larry was clearly interested in helping me grow as an employee. He was amiable mentor and guided me on PPAPs , 8D problem solving approach and other important aspects of Quality systems. Whenever I had concerns or questions, Larry responded well and even followed up later. His patience and willingness to help have made me motivated to do the best job I can.

Niladri Das
As supplier management engineer Larry worked well with all suppliers and resolved issues diplomatically and skillfully. Fairness is essential to this job and Larry was a great practitioner of it. Larry led numerous supplier quality issues to fast resolution through effective project management skills and helped ACH plants meet their quality targets. He is also an excellant quality engineer and has good knowledge of QS/TS requirements. As an individual Larry brings a great attitude to work and is a pleasure to have as part of a team.

Scott Robb
My name is Scott Robb and I am currently the Engineering Manager at Midway Product Group. I am writing this letter on behalf of Larry Napier who has expressed interest in working for your firm. During my tenure at American Axle & Mfg. I had the privilege of working directly with Larry. He has exceptional expertise and passion for engineering, quality, and the manufacturing process. He led many of our company's quality improvement and cost reduction activities, resulting in tremendous improvements in both. In addition, Larry demonstrates a tremendous work ethic, putting in the extra hours necessary to ensure a project is completed on time. He's also a good mentor to other members, patiently explaining / training in a methodical manner. I wholeheartedly recommend Larry as a potential member of your team. Regards, Scott Robb Product Engineering Midway Products Group 1 east Layman Drive Monroe, MI Cell 419 619 5171

Sidharth Jayanth
I had opportunity to work with Larry at Associated spring. Larry was clearly interested in helping me grow as an employee. He was amiable mentor and guided me on PPAPs , 8D problem solving approach and other important aspects of Quality systems. Whenever I had concerns or questions, Larry responded well and even followed up later. His patience and willingness to help have made me motivated to do the best job I can.

Niladri Das
As supplier management engineer Larry worked well with all suppliers and resolved issues diplomatically and skillfully. Fairness is essential to this job and Larry was a great practitioner of it. Larry led numerous supplier quality issues to fast resolution through effective project management skills and helped ACH plants meet their quality targets. He is also an excellant quality engineer and has good knowledge of QS/TS requirements. As an individual Larry brings a great attitude to work and is a pleasure to have as part of a team.

Scott Robb
My name is Scott Robb and I am currently the Engineering Manager at Midway Product Group. I am writing this letter on behalf of Larry Napier who has expressed interest in working for your firm. During my tenure at American Axle & Mfg. I had the privilege of working directly with Larry. He has exceptional expertise and passion for engineering, quality, and the manufacturing process. He led many of our company's quality improvement and cost reduction activities, resulting in tremendous improvements in both. In addition, Larry demonstrates a tremendous work ethic, putting in the extra hours necessary to ensure a project is completed on time. He's also a good mentor to other members, patiently explaining / training in a methodical manner. I wholeheartedly recommend Larry as a potential member of your team. Regards, Scott Robb Product Engineering Midway Products Group 1 east Layman Drive Monroe, MI Cell 419 619 5171

Sidharth Jayanth
I had opportunity to work with Larry at Associated spring. Larry was clearly interested in helping me grow as an employee. He was amiable mentor and guided me on PPAPs , 8D problem solving approach and other important aspects of Quality systems. Whenever I had concerns or questions, Larry responded well and even followed up later. His patience and willingness to help have made me motivated to do the best job I can.

Niladri Das
As supplier management engineer Larry worked well with all suppliers and resolved issues diplomatically and skillfully. Fairness is essential to this job and Larry was a great practitioner of it. Larry led numerous supplier quality issues to fast resolution through effective project management skills and helped ACH plants meet their quality targets. He is also an excellant quality engineer and has good knowledge of QS/TS requirements. As an individual Larry brings a great attitude to work and is a pleasure to have as part of a team.

Credentials
-
Red X Apprentice
ShaininAug, 2010- Nov, 2024 -
Six Sigma Black Belt Certification – Level I
Ford Motor CompanyOct, 2001- Nov, 2024
Experience
-
chargeguard
-
United States
-
IT Services and IT Consulting
-
1 - 100 Employee
-
Senior Certified Recovery Specialist
-
Jul 2020 - Present
As a Senior Certified Recovery Specialist, I help sellers and vendors on Amazon increase profits by getting back their money owed to them by Amazon from erroneous chargebacks, shortages, pricing claims, and reimbursements. Amazon owes almost all vendors and sellers money. They do not make it easy to get the money back. 70% of disputes on Seller Central are left pending. Many vendors on Vendor Central are offered settlements for as low as 10% of the money owed if it gets that far. With Chargeguard we do the disputes and negotiations for you, you can grow your business instead of fighting with Amazon. Show less
-
-
-
Self Employed
-
United States
-
700 & Above Employee
-
Certified Recovery Specialist
-
Jul 2020 - Present
While Amazon continues proving to be a great opportunity for brands and manufacturers, the challenges at times can be just as “great”. The evolution of Amazon’s push for profitability has been evident in key areas of the business and brands feel the pain. The latest area of challenge is in chargebacks and shortages. While there are legitimate reasons for chargebacks and shortages, there are also situations where chargebacks and shortages occur in error and those situations are happening more often than most would imagine. In total, chargebacks and shortages for 2018 alone equate to over $7B. That is a large figure and addressing it has proven to be a large challenge for brands. Two key challenges in addressing this problem are: 1 - Visibility to the chargeback and shortage fees is almost non-existent. Brands have an extremely difficult time even getting to a point to see the information clearly. Amazon does not make it easy. 2 - Disputing fees is a large task and takes a specialized expertise that is not readily available. This is where ChargeGUARD comes in. We have technology to deliver the visibility to fees that the brands have been missing. We also have the expertise to execute on the management and dispute of the erroneous fees. The combination of the tools, technology, automation and expertise allow our ChargeGUARD team to tackle these challenges once and for all. ✔ To Learn More - Go to the link below where you can see more about ChargeGUARD, where you can use my calculator to get an estimate of your fee recovery potential and where you can request your free audit: www.omniix.com/larryn Show less
-
-
-
Usui International Corporation
-
United States
-
Motor Vehicle Manufacturing
-
100 - 200 Employee
-
Quality Manager
-
Aug 2018 - May 2020
Quality Manager for Tier 1 Automotive Company Managed OEM expectations and certifications. Managed OEM Chargebacks Led initial TS 16949 certification for the new Usui West Chester plant Quality Manager for Tier 1 Automotive Company Managed OEM expectations and certifications. Managed OEM Chargebacks Led initial TS 16949 certification for the new Usui West Chester plant
-
-
-
RGBSI
-
United States
-
Engineering Services
-
700 & Above Employee
-
Supplier Quality Engineer
-
May 2017 - Aug 2018
Work as a contract engineer developing supplier 8D submissions for Brose. Special project to collect outstanding 8D submissions over the last two years. Review 8D submissions for robustness. Work with suppliers to create robust 8D. Work with trouble suppliers to develop and verify root cause and permanent corrective actions. Provide support to the team. Work as a contract engineer developing supplier 8D submissions for Brose. Special project to collect outstanding 8D submissions over the last two years. Review 8D submissions for robustness. Work with suppliers to create robust 8D. Work with trouble suppliers to develop and verify root cause and permanent corrective actions. Provide support to the team.
-
-
-
FCA Fiat Chrysler Automobiles
-
United Kingdom
-
Motor Vehicle Manufacturing
-
700 & Above Employee
-
Quality Control Engineer
-
Jul 2016 - Mar 2017
Quality Control Created Quality Control documentation to transfer quality knowledge from Toledo, Ohio to Belvidere, IL plant. Quality Control Created Quality Control documentation to transfer quality knowledge from Toledo, Ohio to Belvidere, IL plant.
-
-
-
AAM - American Axle & Manufacturing
-
United States
-
Automotive
-
700 & Above Employee
-
Senior Product Engineer
-
Apr 2014 - Apr 2016
Benchmarked competitive designs, established design goals DFMEA and PFMEA Review Redesign of all AAM Universal Joints. Forgings, Heat Treat, Machining, Assembly Create and Administer test plans Create and test prototypes for design validation Lead testing for final product validation. PPAP testing Assist Quality department on special projects Benchmarked competitive designs, established design goals DFMEA and PFMEA Review Redesign of all AAM Universal Joints. Forgings, Heat Treat, Machining, Assembly Create and Administer test plans Create and test prototypes for design validation Lead testing for final product validation. PPAP testing Assist Quality department on special projects
-
-
-
-
Senior Application Engineer
-
2007 - Jan 2014
• Develop product design proposals to meet customer specifications and test requirements. • Lead product development and validation activities including DFMEA, design reviews, drawing and model creation (CAD), finite element analysis (FEA), prototype builds, DV/PV testing, NVH verification, design for manufacturing, and key supplier development. • Develop and maintain prototype and test validation plans to meet key customer program timing. • Support Advanced Program Quality Planning (APQP) activities. • Develop and support cost saving initiatives and proposals. • Insure design reviews are completed as planned in order to support a gated program management process. • Provide technical support to customer during all phases of vehicle development. • Communicate engineering and development issues as needed to Dana internal functions. • Prepare and present test reports, damage analysis, and other engineering analysis confirming requirements have been met. • Analyze warranty data and develop effective counter measures. • Support Advanced Engineering and customer engineering groups to develop and integrate control systems into active traction control products. Show less
-
-
-
Visteon Corporation
-
United States
-
Motor Vehicle Manufacturing
-
700 & Above Employee
-
Metrology Supervisor
-
2006 - 2007
Supervised Metrology areaSupervised keeping gauges and measurement devices certified and kept documentation for TS-16949 audits.Supervised quality techniciansInterpreted GD&T for parts from prints
-
-
Quality Engineer
-
Aug 2004 - Jun 2006
Leadership role on customer complaints to identify, coordinate and effectively resolve problems in a timely manner. Develop technical product training tools to support customer needs. Support customers in new application and business opportunities testing.• Develop customer quality metrics to efficiently monitor, track, and identify product quality trends, customer satisfaction and critical-to-quality product properties to ensure the quality of product.• Identify opportunities and lead quality initiatives throughout organization to drive towards six sigma quality levels. To include… manufacturing product teams, customer service/support teams, field service improvement teams• Provide technical information to Product Marketing on changing customer needs, competitive information, marketplace trends and new product development needs.• Develop partner relationships with key distributors. Become “Key quality” contact and reliable technical resource for customers.• Support/lead implementation of quality tools and systems (ie. Six Sigma, ISO) and established practices and standards.• Train others in support of our quality culture. Show less
-
-
-
-
Supplier Management Engineer
-
2002 - 2004
Take a leadership role on customer complaints to identify, coordinate and effectively resolve problems in a timely manner. Develop technical product training tools to support customer needs. Support customers in new application and business opportunities testing. • Develop customer quality metrics to efficiently monitor, track, and identify product quality trends, customer satisfaction and critical-to-quality product properties to ensure the quality of product. • Identify opportunities and lead quality initiatives throughout organization to drive towards six sigma quality levels. To include… manufacturing product teams, customer service/support teams, field service improvement teams • Provide technical information to Product Marketing on changing customer needs, competitive information, marketplace trends and new product development needs. • Develop partner relationships with key distributors. Become “Key quality” contact and reliable technical resource for customers. • Support/lead implementation of quality tools and systems (ie. Six Sigma, ISO) and established practices and standards. • Train others in support of our quality culture. • Any other duties as assigned by the Director of QA Show less
-
-
-
Visteon Corporation
-
United States
-
Motor Vehicle Manufacturing
-
700 & Above Employee
-
Manufacturing Engineer
-
2000 - 2002
In charge of efficiency on several catalytic converter assembly lines. Solved quality concerns on production lines. Increase production output. In charge of efficiency on several catalytic converter assembly lines. Solved quality concerns on production lines. Increase production output.
-
-
-
Dana Incorporated
-
United States
-
Motor Vehicle Manufacturing
-
700 & Above Employee
-
Co-op Application Engineer
-
May 1998 - Aug 2000
I wrote a MathCAD application to find the amoubt of energy loss as a driveshaft approaches critical speed. I wrote a MathCAD application to find the amoubt of energy loss as a driveshaft approaches critical speed.
-
-
-
-
Whitewater Raft Guide
-
Jun 1983 - Oct 1999
Trip Leader for whitewater rafting Trips. Trip Leader for whitewater rafting Trips.
-
-
-
-
Mailroom Clerk
-
1979 - 1986
-
-
Education
-
The University of Toledo
BSME, Engineering -
Baker College Center for Graduate Studies
MBA, Business -
Northwood High School
Community
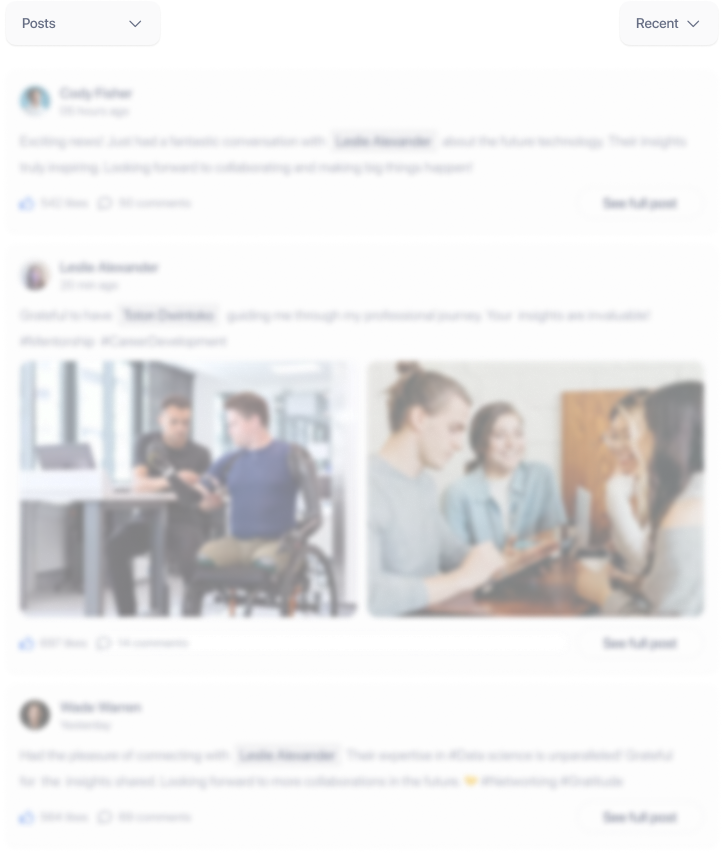