Larry Bernor
Project Manager / Maintenance Manager at Olde Thompson, LLC- Claim this Profile
Click to upgrade to our gold package
for the full feature experience.
Topline Score
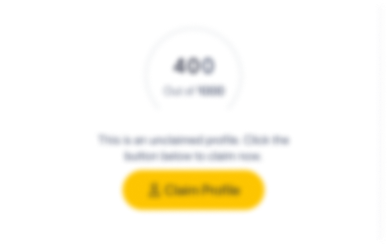
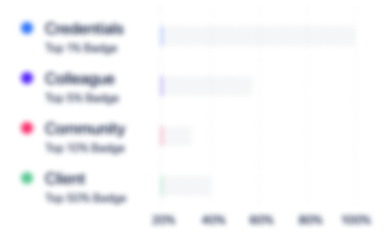
Bio


Experience
-
Olde Thompson, LLC
-
United States
-
Food and Beverage Manufacturing
-
1 - 100 Employee
-
Project Manager / Maintenance Manager
-
Jul 2017 - Present
•Rapidly promoted from Maintenance Manager to Project Manager in 2021 due to exceptional performance •Play a vital role in ensuring the seamless operations of projects including air system, lighting, and ventilation updates •Partner with team members in designing a redundant air supply system that provides 24/7 backup •Expertly apply knowledge and background to coordinate the development of new oil-free compressors and automation systems to meet foods safety concerns and improve employee safety •Utilize Redzone Production Systems to improve food safety, productivity, capacity, inventory reduction, and customer service
-
-
-
SunOpta
-
United States
-
Food and Beverage Manufacturing
-
700 & Above Employee
-
Maintenance Manager
-
Jul 2015 - Jul 2017
•Streamlined and expedited maintenance operations across 2 facilities to maximize productivity and efficiency •Utilized available resources, tools, and materials to promptly resolve issues and challenges •Recruited and hired qualified talent that met position requirements, the goals of the maintenance department, and automation standards •Strategically coordinated, planned, and managed processing, labor, quality, and safety improvement projects •Increased equipment uptime through the implementation of COGZ preventative maintenance
-
-
-
Rexam
-
Packaging & Containers
-
700 & Above Employee
-
Engineering Manager
-
Sep 2014 - 2015
•Guaranteed maintenance, labor, and repair expenses adhered to strict budgetary constraints •Remained in constant contact with project engineering and production teams to communicate repair requirements and improvement strategies for driving plant efficiency •Spearheaded the design and renovation of equipment and facilities in accordance with company goals of maximized yield, capacity, and productivity •Consistently ensured daily operations complied with engineering specifications, standards, and regulations •Offered the necessary resources and training for staff to succeed in overseeing manufacturing process efficiency and cost-effectiveness •Cultivated a positive workplace environment conducive to the satisfaction of company and union employees
-
-
-
Maple Leaf Bakery
-
Oxnard, California, United States
-
Maintenance Manager
-
Jun 2010 - Jul 2014
•Effectively managed, motivated, and coached an 18-member team consisting of 2 supervisors, 1 planner, 1 purchaser, and 14 maintenance technicians •Provided valuable training and guidance for staff to understand safety standards and sanitation regulations •Maintained the integrity and functionality of bakery equipment to maximize the efficiency of facility operations •Efficiently reviewed work orders, historical data, and production schedules to ensure adherence to customer requirements and preventative maintenance goals •Kept lines of communication open with managers and supervisors to discuss daily maintenance needs, schedules, and production goals •Utilized SAP to monitor work orders and parts inventory •Conducted thorough performance evaluations of staff to determine areas of improvement or achievement
-
-
-
Foster Farms Dairy
-
Manufacturing
-
1 - 100 Employee
-
Maintenance Manger
-
Mar 2007 - Jun 2010
•Supervised a team of 30 associates that were capable of meeting safety standards and plant production goals •Maintained accurate and updated records of maintenance operations, updates, and repair schedules throughout Fluid Processing, Ice Cream, and Receiving (evaporator & dryer) departments •Delegated daily tasks and assignments to staff based on production and general maintenance needs •Documented PSM requirements for 2-20,000lb ammonia systems •Worked collaboratively with team members in enforcing environmental regulations, local / state emission guidelines, and San Joaquin Air Pollution Control District standards •Coordinated inspection schedules for wet, dry, and chemical Fire Systems •Controlled ordering and inventory to maintain optimal stock levels of parts and materials
-
-
-
Foster Farms
-
United States
-
Food and Beverage Manufacturing
-
700 & Above Employee
-
Maintenance Supervisor
-
Aug 2003 - Apr 2007
•Educated staff about production requirements, environmental regulations, and safety goals •Efficiently prepared payroll using Kronos Time System •Maintain appropriate stock levels of parts and equipment for facility maintenance •Completed required documentation, equipment testing, and records based on PSM program requirements •Consistently met on-time production demands for repairs and general maintenance •Educated staff about production requirements, environmental regulations, and safety goals •Efficiently prepared payroll using Kronos Time System •Maintain appropriate stock levels of parts and equipment for facility maintenance •Completed required documentation, equipment testing, and records based on PSM program requirements •Consistently met on-time production demands for repairs and general maintenance
-
-
-
Producers Dairy Foods Inc.
-
United States
-
Food and Beverage Manufacturing
-
1 - 100 Employee
-
Maintenance Lead
-
2004 - 2005
-
-
-
Dairyman's Creamery
-
Tulare County, California, United States
-
Maintenance Specialist
-
1988 - 2004
-
-
Education
-
Fresno Pacific University
Bachelor of Arts - BA, Management & Organizational Development -
College of the Sequoias
Associate of Arts - AA, Electronics & Mathematics
Community
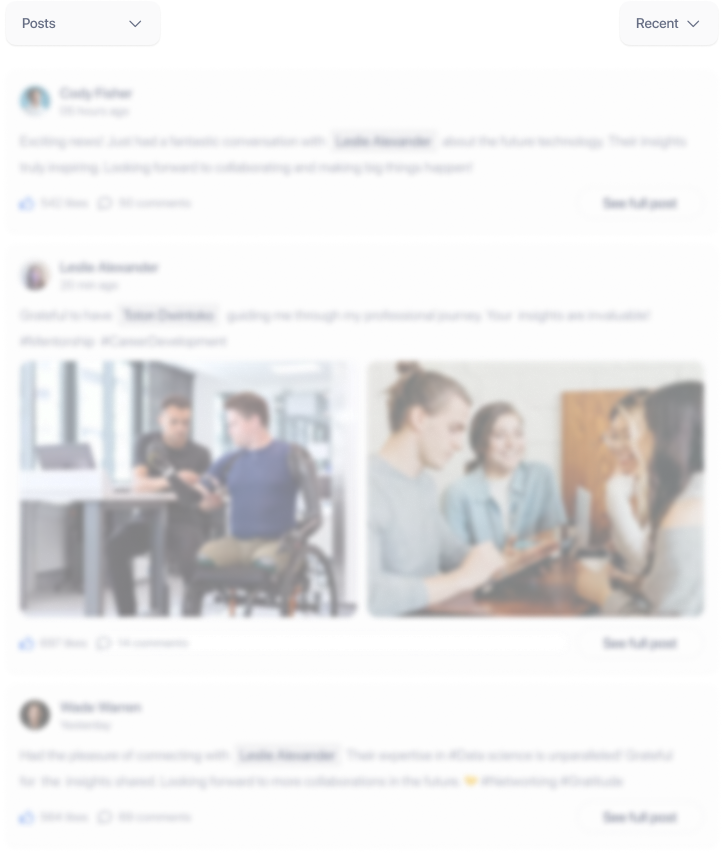