Kyle Supa
Technical Team Leader at Principal Service Solutions, Inc.- Claim this Profile
Click to upgrade to our gold package
for the full feature experience.
-
English Native or bilingual proficiency
-
Thai Native or bilingual proficiency
Topline Score
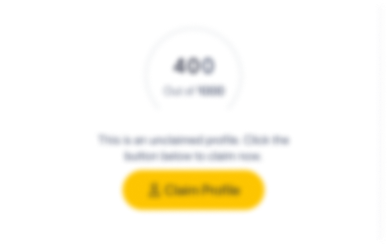
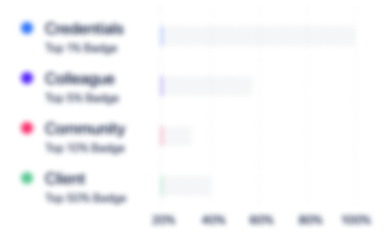
Bio

Genadi Veksler
Kyle Supa is excellent worker, he always proved effective solutions and he have amazing analysis skills and he have an standing interpersonal skills.

Genadi Veksler
Kyle Supa is excellent worker, he always proved effective solutions and he have amazing analysis skills and he have an standing interpersonal skills.

Genadi Veksler
Kyle Supa is excellent worker, he always proved effective solutions and he have amazing analysis skills and he have an standing interpersonal skills.

Genadi Veksler
Kyle Supa is excellent worker, he always proved effective solutions and he have amazing analysis skills and he have an standing interpersonal skills.

Credentials
-
White belt training; problem solving training
-Sep, 2013- Nov, 2024
Experience
-
Principal Service Solutions, Inc.
-
United States
-
Semiconductors
-
1 - 100 Employee
-
Technical Team Leader
-
Jun 2022 - Present
Responsible for overseeing teams of employees and motivating them to complete their job duties effectively. The duties include providing team members with daily objectives, developing and implementing reward systems to motivate employee productivity and communicating with upper management to determine the best methods for meeting business goals. Further job responsibility includes assign tasks to team members, determine the completion timeline and monitor progress to keep the project on track and on schedule, communicate clear instructions to team members, manage the flow of day-to-day operations, and create/distribute reports to update the company on the team’s progress.
-
-
CMP IQ planar Field Service Engineer
-
Mar 2022 - Jun 2022
Perform CMP IQ planar engineer roles on tool conversion project including sub-assemblied modification, upgrade, calibrate, to the final tool completion to run the wafer. currently works on CMP Reflexion system.
-
-
Senior Field Service Engineer
-
Nov 2019 - Mar 2022
Perform equipment conversions, tier0 to tier1 start-up process, and equipment upgrades. Lead the technical expert role on CMP equipment to provide solutions and Best Known Methods (BKM) to the customer and new customer engineers. Perform shift sustaining as requested. Perform work in cleanroom attire. Tools: 300mm Relexion-Desica, Mirra-Mesa, LK, LK-Prime, FIC 4.0, 5.4, 6.4
-
-
-
Westerwood Global
-
Ireland
-
Semiconductor Manufacturing
-
1 - 100 Employee
-
CMP Field Service Engineer
-
Sep 2018 - Aug 2019
Provided advance technical training to the customer and leaded the technical expert role to provide the solutions to the CMP team. Developed the procedures and training process. Performed equipment preventative and corrective maintenance. Performed shift sustaining in cleanroom attire Tools: Expert on 300mm Relexion3600-Desica, Mirra-Mesa, Reflexion-LK, LK-Prime S. Provided advance technical training to the customer and leaded the technical expert role to provide the solutions to the CMP team. Developed the procedures and training process. Performed equipment preventative and corrective maintenance. Performed shift sustaining in cleanroom attire Tools: Expert on 300mm Relexion3600-Desica, Mirra-Mesa, Reflexion-LK, LK-Prime S.
-
-
-
Principal Service Solutions, Inc.
-
United States
-
Semiconductors
-
1 - 100 Employee
-
Field Service Engineer
-
Feb 2017 - Aug 2018
(February 2017 – September 2017) Contract at STMicroelectronics; Grenoble, France (September 2017 – August 2018) Contract at IM Flash; Lehi, Utah USA Perform equipment installations tier0 to tier1 process, upgrades, and decommissions. Lead as technical expert role to provide solutions and Best Known Methods (BKM) to the CMP team. Provide advance technical training to the engineer and technician on shift. Perform shift-sustaining activities. Perform equipment preventative and corrective maintenance. Tools: Expert on 300mm Relexion3600-Desica, Mirra-Mesa, Reflexion-LK, Reflexion LK-Prime.
-
-
-
Applied Materials
-
United States
-
Semiconductor Manufacturing
-
700 & Above Employee
-
Customer engineer
-
Aug 2008 - May 2014
August 2008 – May 2014 CMP Customer Engineer III, Applied Materials, AMGI: Hillsboro, OregonPerformed shift sustaining in cleanroom attire. Assisted senior field personnel on warranty, pay-service, and service contract activities. Served as the company liaison with customer on administrative and technical matters for assigned projects. Re-written the procedures to perform various tasks associated with tool installs, upgrades and ongoing maintenance. Trained new CEs to develop the skills. Developed and applied diagnostic techniques, including 6-sigma, to troubleshoot complex technical problems including software and hardware, optics, electro-optical, electro-mechanical, electro-pneumatic, laser and mechanical. Supported the loan labor at other sites, as requested. Perform equipment preventative and corrective maintenance.
-
-
Customer Engineer
-
Jun 2006 - Aug 2008
June 2006 – August 2008 CMP Customer Engineer II, Applied Materials, AMGI: Chandler, ArizonaPerformed shift sustaining in cleanroom attire. Performed equipment preventative and corrective maintenance. Assisted senior field personnel on warranty, pay-service, and service contract activities. Instructed customers in the operation and maintenance of the systems. Developed and implement plans to increase productivity. Tracked performance of systems as assigned and assist in uptime improvement. Developed and apply diagnostic techniques to resolve complex technical problems on specific Applied Materials products. Support the loan labor at other sites.Tools: Expert on 300mm Reflexion Mirra-Mesa, Desica cleaner.
-
-
-
Brooks Automation
-
United States
-
Semiconductor Manufacturing
-
700 & Above Employee
-
Customer Engineer
-
Mar 2000 - Jun 2006
March 2000 – June 2006 Customer Engineer I, Applied Materials, AMGI: Hillsboro, Oregon Performed shift sustaining on PRI/BROOKS automation equipment. Specialized on products to resolve complex system problems. Repaired and upgraded the workstations and servers correspondent with customer IT department. Performed equipment preventative and corrective maintenance. Obtained uptime 99.999% of AMHS equipment in a manufacturing. Tools: 200mm Stocker7500, Aero Trek, MLRV, PRI/BROOKs robotic motions, Yaskawa robotic motion control system.
-
-
-
-
System analyst
-
1989 - 2000
Conducted failure analysis and in-depth troubleshooting. Developed and implemented the program for cost reduction. Researched, evaluated, and recommended the new technology for the lottery commission organization. Leaded role in development of parts quality program in the organization. Written the technical procedures and provided technical support to field service technicians. Provided customer service and sale support in regional variations. Performed on-site equipment repairs, installation and system upgrades.
-
-
Education
-
Hartford university
Bachelor of Applied Science (BASc), Manufacturing Engineering Technology -
Maryhurst university
Business Administration and Management, General -
ITT Technical Institute-Portland
Associate of Science (AS), Electrical and Electronics Engineering
Community
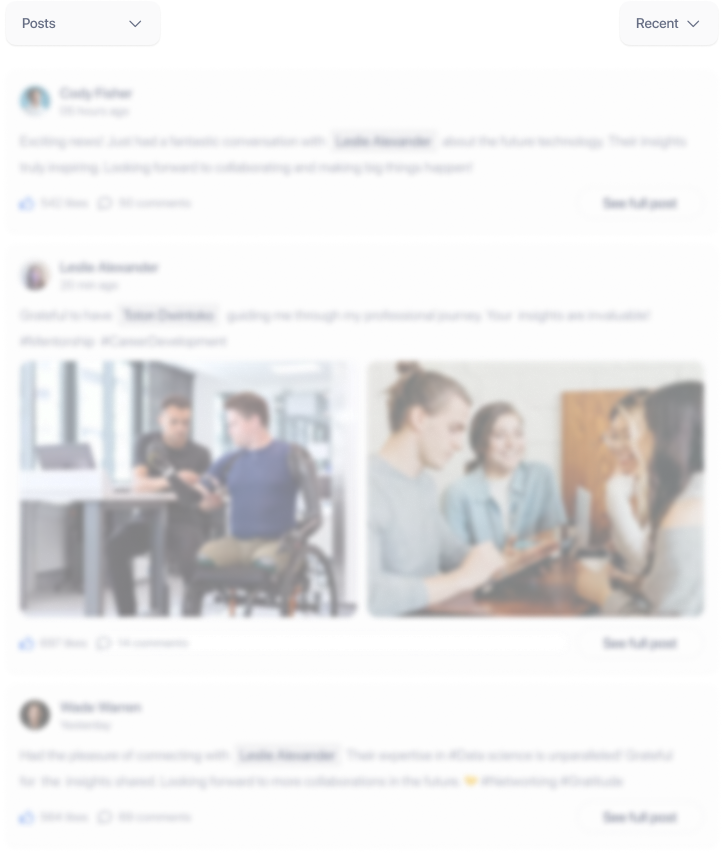