Kyle Schwenker
Process Engineer at DaVinci Roofscapes, a Westlake Company- Claim this Profile
Click to upgrade to our gold package
for the full feature experience.
-
Chinese Elementary proficiency
-
English Native or bilingual proficiency
Topline Score
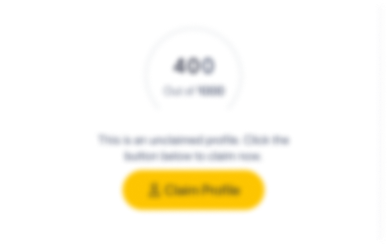
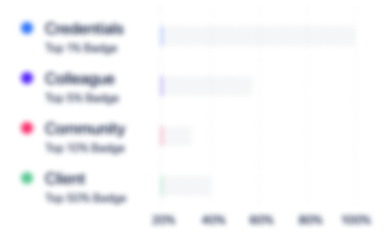
Bio

Jeanne Norton
To Whom It May Concern: It is my pleasure to recommend Mr. Kyle Schwenker. Kyle was an undergraduate student in Plastics Engineering Technology at Pittsburg State University (Pittsburg, KS) that I had the opportunity to teach starting in 2013. Subsequent to having Kyle in class, Kyle worked as an undergraduate research assistant from May 2014 to May 2015, when Kyle graduated with his BS in Plastics and was accepted into the Polymer Graduate Chemistry program at PSU. Kyle transitioned to a graduate research assistantship in my research group at that time. Kyle earned his MS in Polymer Chemistry in 2017. Throughout my relationship with Kyle, I have been exceedingly pleased with his capacity to learn, his excellent work ethic, and his desire to overcome technical challenges. Kyle is technically very skilled in a wide variety of both chemical analyses and plastics processing techniques. (These include, but are not limited to injection molding, compounding, thermal characterization, and mechanical characterization.) His very steep learning curve makes him very well adapted to mastering new procedures and processes. Kyle is also an excellent communicator, in both written and oral forms, and has the capacity to train others to perform at his level in a short period of time. I owe a great deal of my own career success to Kyle's hard work and perseverance while he was working on his thesis. If I had the chance to work with Kyle again in any capacity, I would welcome it. Kyle is a team player and a genuinely good human being. In summary, Kyle Schwenker is an asset to any company or organization that gives him an opportunity to demonstrate his technical expertise. I welcome any additional questions anyone may have about Kyle. Please contact me at jnorton@pittstate.edu. Jeanne H. Norton Jeanne H. Norton, Ph.D. Associate Professor, Plastics Department of Engineering Technology Pittsburg State University Kansas Technology Center, W122b 1701 South Broadway Pittsburg, KS 66762

Michael Giffin
Kyle and I studied at PSU together for out Master's and Bachelor's degrees. During undergraduate, he was quite studious and determined, in particular for the quantity and quality of time spent studying organic chemistry together, which I can speak to personally. Later, during his Master's, he assisted my learning the techniques of DSC and TGA, which we both needed for our research, and he was already proficient at performing. We were under different supervisors, but he still made the time to help out a colleague (me) in need of assistance. Personally, I think this speaks wonders of his character. Although I did not work directly with him on his thesis (compounding and characterizing silica-filled polysiloxane materials), I know he put substantial time and effort into it, and appeared to have an excellent grasp of all things related.

Jeanne Norton
To Whom It May Concern: It is my pleasure to recommend Mr. Kyle Schwenker. Kyle was an undergraduate student in Plastics Engineering Technology at Pittsburg State University (Pittsburg, KS) that I had the opportunity to teach starting in 2013. Subsequent to having Kyle in class, Kyle worked as an undergraduate research assistant from May 2014 to May 2015, when Kyle graduated with his BS in Plastics and was accepted into the Polymer Graduate Chemistry program at PSU. Kyle transitioned to a graduate research assistantship in my research group at that time. Kyle earned his MS in Polymer Chemistry in 2017. Throughout my relationship with Kyle, I have been exceedingly pleased with his capacity to learn, his excellent work ethic, and his desire to overcome technical challenges. Kyle is technically very skilled in a wide variety of both chemical analyses and plastics processing techniques. (These include, but are not limited to injection molding, compounding, thermal characterization, and mechanical characterization.) His very steep learning curve makes him very well adapted to mastering new procedures and processes. Kyle is also an excellent communicator, in both written and oral forms, and has the capacity to train others to perform at his level in a short period of time. I owe a great deal of my own career success to Kyle's hard work and perseverance while he was working on his thesis. If I had the chance to work with Kyle again in any capacity, I would welcome it. Kyle is a team player and a genuinely good human being. In summary, Kyle Schwenker is an asset to any company or organization that gives him an opportunity to demonstrate his technical expertise. I welcome any additional questions anyone may have about Kyle. Please contact me at jnorton@pittstate.edu. Jeanne H. Norton Jeanne H. Norton, Ph.D. Associate Professor, Plastics Department of Engineering Technology Pittsburg State University Kansas Technology Center, W122b 1701 South Broadway Pittsburg, KS 66762

Michael Giffin
Kyle and I studied at PSU together for out Master's and Bachelor's degrees. During undergraduate, he was quite studious and determined, in particular for the quantity and quality of time spent studying organic chemistry together, which I can speak to personally. Later, during his Master's, he assisted my learning the techniques of DSC and TGA, which we both needed for our research, and he was already proficient at performing. We were under different supervisors, but he still made the time to help out a colleague (me) in need of assistance. Personally, I think this speaks wonders of his character. Although I did not work directly with him on his thesis (compounding and characterizing silica-filled polysiloxane materials), I know he put substantial time and effort into it, and appeared to have an excellent grasp of all things related.

Jeanne Norton
To Whom It May Concern: It is my pleasure to recommend Mr. Kyle Schwenker. Kyle was an undergraduate student in Plastics Engineering Technology at Pittsburg State University (Pittsburg, KS) that I had the opportunity to teach starting in 2013. Subsequent to having Kyle in class, Kyle worked as an undergraduate research assistant from May 2014 to May 2015, when Kyle graduated with his BS in Plastics and was accepted into the Polymer Graduate Chemistry program at PSU. Kyle transitioned to a graduate research assistantship in my research group at that time. Kyle earned his MS in Polymer Chemistry in 2017. Throughout my relationship with Kyle, I have been exceedingly pleased with his capacity to learn, his excellent work ethic, and his desire to overcome technical challenges. Kyle is technically very skilled in a wide variety of both chemical analyses and plastics processing techniques. (These include, but are not limited to injection molding, compounding, thermal characterization, and mechanical characterization.) His very steep learning curve makes him very well adapted to mastering new procedures and processes. Kyle is also an excellent communicator, in both written and oral forms, and has the capacity to train others to perform at his level in a short period of time. I owe a great deal of my own career success to Kyle's hard work and perseverance while he was working on his thesis. If I had the chance to work with Kyle again in any capacity, I would welcome it. Kyle is a team player and a genuinely good human being. In summary, Kyle Schwenker is an asset to any company or organization that gives him an opportunity to demonstrate his technical expertise. I welcome any additional questions anyone may have about Kyle. Please contact me at jnorton@pittstate.edu. Jeanne H. Norton Jeanne H. Norton, Ph.D. Associate Professor, Plastics Department of Engineering Technology Pittsburg State University Kansas Technology Center, W122b 1701 South Broadway Pittsburg, KS 66762

Michael Giffin
Kyle and I studied at PSU together for out Master's and Bachelor's degrees. During undergraduate, he was quite studious and determined, in particular for the quantity and quality of time spent studying organic chemistry together, which I can speak to personally. Later, during his Master's, he assisted my learning the techniques of DSC and TGA, which we both needed for our research, and he was already proficient at performing. We were under different supervisors, but he still made the time to help out a colleague (me) in need of assistance. Personally, I think this speaks wonders of his character. Although I did not work directly with him on his thesis (compounding and characterizing silica-filled polysiloxane materials), I know he put substantial time and effort into it, and appeared to have an excellent grasp of all things related.

Jeanne Norton
To Whom It May Concern: It is my pleasure to recommend Mr. Kyle Schwenker. Kyle was an undergraduate student in Plastics Engineering Technology at Pittsburg State University (Pittsburg, KS) that I had the opportunity to teach starting in 2013. Subsequent to having Kyle in class, Kyle worked as an undergraduate research assistant from May 2014 to May 2015, when Kyle graduated with his BS in Plastics and was accepted into the Polymer Graduate Chemistry program at PSU. Kyle transitioned to a graduate research assistantship in my research group at that time. Kyle earned his MS in Polymer Chemistry in 2017. Throughout my relationship with Kyle, I have been exceedingly pleased with his capacity to learn, his excellent work ethic, and his desire to overcome technical challenges. Kyle is technically very skilled in a wide variety of both chemical analyses and plastics processing techniques. (These include, but are not limited to injection molding, compounding, thermal characterization, and mechanical characterization.) His very steep learning curve makes him very well adapted to mastering new procedures and processes. Kyle is also an excellent communicator, in both written and oral forms, and has the capacity to train others to perform at his level in a short period of time. I owe a great deal of my own career success to Kyle's hard work and perseverance while he was working on his thesis. If I had the chance to work with Kyle again in any capacity, I would welcome it. Kyle is a team player and a genuinely good human being. In summary, Kyle Schwenker is an asset to any company or organization that gives him an opportunity to demonstrate his technical expertise. I welcome any additional questions anyone may have about Kyle. Please contact me at jnorton@pittstate.edu. Jeanne H. Norton Jeanne H. Norton, Ph.D. Associate Professor, Plastics Department of Engineering Technology Pittsburg State University Kansas Technology Center, W122b 1701 South Broadway Pittsburg, KS 66762

Michael Giffin
Kyle and I studied at PSU together for out Master's and Bachelor's degrees. During undergraduate, he was quite studious and determined, in particular for the quantity and quality of time spent studying organic chemistry together, which I can speak to personally. Later, during his Master's, he assisted my learning the techniques of DSC and TGA, which we both needed for our research, and he was already proficient at performing. We were under different supervisors, but he still made the time to help out a colleague (me) in need of assistance. Personally, I think this speaks wonders of his character. Although I did not work directly with him on his thesis (compounding and characterizing silica-filled polysiloxane materials), I know he put substantial time and effort into it, and appeared to have an excellent grasp of all things related.

Experience
-
DaVinci Roofscapes, a Westlake Company
-
United States
-
Wholesale Building Materials
-
1 - 100 Employee
-
Process Engineer
-
Jul 2022 - Present
-
-
-
Splintek, Inc.
-
United States
-
Wellness and Fitness Services
-
1 - 100 Employee
-
Chemist
-
Jan 2019 - Sep 2022
Manage the Research and Development Lab at Splintek, which manufactures high-quality healthcare products to enhance the quality of life for our customers by providing a more comfortable and healthier sleeping experience. Splintek manufactures both prescription and over-the-counter products under the SleepRight® and HearRight® brand names. The products include low-temp and non-boil dental guards, tongue cleaners, nasal breathe aids, vapor inhalers, sleep inhalers, ear plugs, and memory foam… Show more Manage the Research and Development Lab at Splintek, which manufactures high-quality healthcare products to enhance the quality of life for our customers by providing a more comfortable and healthier sleeping experience. Splintek manufactures both prescription and over-the-counter products under the SleepRight® and HearRight® brand names. The products include low-temp and non-boil dental guards, tongue cleaners, nasal breathe aids, vapor inhalers, sleep inhalers, ear plugs, and memory foam pillows. Operate the R&D lab to support production, test products, and participate in new product development projects. Support production by preparing resin formulations for injection molded healthcare products. Test product by conducting wear testing trials on dental guards to support product claims. Analyzing the wear on the dental guards and surface roughness of ceramic materials using a Keyence 3D microscope. Participate in new product development projects by manufacturing current and new products with new materials or designs and testing the new products to evaluate conformance for product launch. Coordinate and review out-sourced bio-compatibility testing with approved research organizations to ensure new product are compliant with FDA regulations. Submit 510(K) forms to the FDA for approval of marketing new products. Coordinate and maintain proper calibration for all needed lab equipment .
-
-
Chemist/Quality Manager
-
Jan 2019 - Jan 2020
Operate the R&D lab to support production, test product, and participate in new product development projects. Support production by preparing resin formulations for injection molded healthcare products. Test product by conducting wear testing trials on dental guards to support product claims. Analyzing the wear on the dental guards and surface roughness of ceramic materials using a Keyence 3D microscope. Participate in new product development projects by manufacturing current and new products… Show more Operate the R&D lab to support production, test product, and participate in new product development projects. Support production by preparing resin formulations for injection molded healthcare products. Test product by conducting wear testing trials on dental guards to support product claims. Analyzing the wear on the dental guards and surface roughness of ceramic materials using a Keyence 3D microscope. Participate in new product development projects by manufacturing current and new products with new materials or designs and testing the new products to evaluate conformance for product launch. Ensure the company and employees follow all federal and global regulations, as well as meet all customer requirements and agreements set forth by the quality management system. Coordinate and review out-sourced bio-compatibility testing with approved research organizations to ensure new product are compliant with FDA regulations. Submit 510(K) forms to the FDA for approval of marketing new product. Coordinate and maintain proper calibration for all needed lab equipment .
-
-
-
Honeywell
-
United States
-
Appliances, Electrical, and Electronics Manufacturing
-
700 & Above Employee
-
Scientist II
-
Jun 2017 - Jan 2019
Managed the thermal analysis lab in the analytical department to support both development and production projects. Administered various thermal analysis instruments and techniques; such as TA Instruments thermogravimetric analyzer (TGA), differential scanning calorimeter (DSC), and thermal mechanical analyzer (TMA); as well as three Netzsch dilatometers. Test samples included determining weight loss, residue, melting point, degree of curing, glass transition temperature, and coefficient of… Show more Managed the thermal analysis lab in the analytical department to support both development and production projects. Administered various thermal analysis instruments and techniques; such as TA Instruments thermogravimetric analyzer (TGA), differential scanning calorimeter (DSC), and thermal mechanical analyzer (TMA); as well as three Netzsch dilatometers. Test samples included determining weight loss, residue, melting point, degree of curing, glass transition temperature, and coefficient of thermal expansion in plastics, polymeric materials, and ceramics. Maintained work instructions and lab procedures for the analysis equipment for training purposes that included more through documented information. Established new instrument procedures for novel samples; maintained testing procedures for legacy materials; and improved calibration procedures to provide more adequate and consistent data. Interfaced with engineers and customers to develop instrument methods and procedures pertaining to their specific material and analysis requirements. Interpreted both production and development samples, proposed theories based on results, and wrote reports. Received my Six Sigma Greenbelt through Honeywell. Was promoted from a Scientist I to a Scientist II in 16 months of working at Honeywell. Show less Managed the thermal analysis lab in the analytical department to support both development and production projects. Administered various thermal analysis instruments and techniques; such as TA Instruments thermogravimetric analyzer (TGA), differential scanning calorimeter (DSC), and thermal mechanical analyzer (TMA); as well as three Netzsch dilatometers. Test samples included determining weight loss, residue, melting point, degree of curing, glass transition temperature, and coefficient of… Show more Managed the thermal analysis lab in the analytical department to support both development and production projects. Administered various thermal analysis instruments and techniques; such as TA Instruments thermogravimetric analyzer (TGA), differential scanning calorimeter (DSC), and thermal mechanical analyzer (TMA); as well as three Netzsch dilatometers. Test samples included determining weight loss, residue, melting point, degree of curing, glass transition temperature, and coefficient of thermal expansion in plastics, polymeric materials, and ceramics. Maintained work instructions and lab procedures for the analysis equipment for training purposes that included more through documented information. Established new instrument procedures for novel samples; maintained testing procedures for legacy materials; and improved calibration procedures to provide more adequate and consistent data. Interfaced with engineers and customers to develop instrument methods and procedures pertaining to their specific material and analysis requirements. Interpreted both production and development samples, proposed theories based on results, and wrote reports. Received my Six Sigma Greenbelt through Honeywell. Was promoted from a Scientist I to a Scientist II in 16 months of working at Honeywell. Show less
-
-
-
Pittsburg State University
-
United States
-
Higher Education
-
700 & Above Employee
-
Graduate Research Assistant
-
Aug 2015 - May 2017
Conducted compounding research on a lab-scale Thermo Fisher Scientific Process 11 twin screw extruder. Extruded both semi-crystalline and amorphous thermoplastic resins to study the affects of processing and recycling on the materials. Produced plastic extrudate from the extruder; then ground up extrudate and used the regrind to injection mold tensile test bars for tensile testing using an Arburg injection molding machine. Performed tensile testing on a MTS Corporation mechanical tester to… Show more Conducted compounding research on a lab-scale Thermo Fisher Scientific Process 11 twin screw extruder. Extruded both semi-crystalline and amorphous thermoplastic resins to study the affects of processing and recycling on the materials. Produced plastic extrudate from the extruder; then ground up extrudate and used the regrind to injection mold tensile test bars for tensile testing using an Arburg injection molding machine. Performed tensile testing on a MTS Corporation mechanical tester to compare mechanical properties on various processed and recycled parts. Evaluated the thermal stability of the samples by a TA Instruments Thermogravimetric Analyzer (TGA); as well as studied the crystallization temperature, melting temperature, and glass transition temperature of samples by a TA Instruments Differential Scanning Calorimeter (DSC). Wrote work instructions for the Process 11 for training proposes, provided training on the Process 11 and the analytical equipment; and supervised an undergraduate student conducting research to evaluate the distribution of filler by the Process 11. Compounded commercial and experimental siloxane polymers with three silica fillers using the Process 11 to produce appropriate materials for potential additive manufacturing applications. The polymers and fillers were premixed together before extrusion, they were then further mixed by the Process 11 to produce extrudate, and the extrudate was characterized for specific properties. The formulated materials were tested by TGA to evaluate the distribution of filler, the yield stress of the materials was determined by oscillatory rheometry, and the thixotropic behavior was studied in the materials by flow rheology Rheological testing was performed on a TA Instruments rotational rheometer. Trained a graduate student on the various processing and characterization techniques to continue further research. Presented two posters and defended a master’s thesis on the work performed. Show less Conducted compounding research on a lab-scale Thermo Fisher Scientific Process 11 twin screw extruder. Extruded both semi-crystalline and amorphous thermoplastic resins to study the affects of processing and recycling on the materials. Produced plastic extrudate from the extruder; then ground up extrudate and used the regrind to injection mold tensile test bars for tensile testing using an Arburg injection molding machine. Performed tensile testing on a MTS Corporation mechanical tester to… Show more Conducted compounding research on a lab-scale Thermo Fisher Scientific Process 11 twin screw extruder. Extruded both semi-crystalline and amorphous thermoplastic resins to study the affects of processing and recycling on the materials. Produced plastic extrudate from the extruder; then ground up extrudate and used the regrind to injection mold tensile test bars for tensile testing using an Arburg injection molding machine. Performed tensile testing on a MTS Corporation mechanical tester to compare mechanical properties on various processed and recycled parts. Evaluated the thermal stability of the samples by a TA Instruments Thermogravimetric Analyzer (TGA); as well as studied the crystallization temperature, melting temperature, and glass transition temperature of samples by a TA Instruments Differential Scanning Calorimeter (DSC). Wrote work instructions for the Process 11 for training proposes, provided training on the Process 11 and the analytical equipment; and supervised an undergraduate student conducting research to evaluate the distribution of filler by the Process 11. Compounded commercial and experimental siloxane polymers with three silica fillers using the Process 11 to produce appropriate materials for potential additive manufacturing applications. The polymers and fillers were premixed together before extrusion, they were then further mixed by the Process 11 to produce extrudate, and the extrudate was characterized for specific properties. The formulated materials were tested by TGA to evaluate the distribution of filler, the yield stress of the materials was determined by oscillatory rheometry, and the thixotropic behavior was studied in the materials by flow rheology Rheological testing was performed on a TA Instruments rotational rheometer. Trained a graduate student on the various processing and characterization techniques to continue further research. Presented two posters and defended a master’s thesis on the work performed. Show less
-
-
-
Etco Specialty Products Inc
-
United States
-
Research Services
-
1 - 100 Employee
-
Machine Technician
-
Jan 2013 - Aug 2015
Learned and performed various processing techniques to prevent flash, blushing, and weld lines on PVC, Nylon, and Polypropylene parts using JSW injection molding machines. Assisted in mold cleaning, mold changeovers, and insert changes for new production runs. Prepared resin for parts, ground up scrap parts (recycled material), and cleaned production lines for new product when the lines were switched over. Trimmed, organized, and boxed finished parts to be shipped to customers. Obtained a… Show more Learned and performed various processing techniques to prevent flash, blushing, and weld lines on PVC, Nylon, and Polypropylene parts using JSW injection molding machines. Assisted in mold cleaning, mold changeovers, and insert changes for new production runs. Prepared resin for parts, ground up scrap parts (recycled material), and cleaned production lines for new product when the lines were switched over. Trimmed, organized, and boxed finished parts to be shipped to customers. Obtained a forklift certification. Show less Learned and performed various processing techniques to prevent flash, blushing, and weld lines on PVC, Nylon, and Polypropylene parts using JSW injection molding machines. Assisted in mold cleaning, mold changeovers, and insert changes for new production runs. Prepared resin for parts, ground up scrap parts (recycled material), and cleaned production lines for new product when the lines were switched over. Trimmed, organized, and boxed finished parts to be shipped to customers. Obtained a… Show more Learned and performed various processing techniques to prevent flash, blushing, and weld lines on PVC, Nylon, and Polypropylene parts using JSW injection molding machines. Assisted in mold cleaning, mold changeovers, and insert changes for new production runs. Prepared resin for parts, ground up scrap parts (recycled material), and cleaned production lines for new product when the lines were switched over. Trimmed, organized, and boxed finished parts to be shipped to customers. Obtained a forklift certification. Show less
-
-
-
Pittsburg State University
-
United States
-
Higher Education
-
700 & Above Employee
-
Research Assistant
-
May 2014 - May 2015
Performed research on various polyethylene-based formulations to produce sample parts by rotational molding for potential fuel tank applications. Gained experience on a Medkeff-nye Roto-Lab Machine to produce the parts with four diverse fillers. Specimens were cut from sample parts for IZOD impact testing using a Testing Machines Inc. (TMI) impact tester. Specimens were also cut for uniform thickness measurements and to conduct permeation studies. Additional sample parts were dropped off of a… Show more Performed research on various polyethylene-based formulations to produce sample parts by rotational molding for potential fuel tank applications. Gained experience on a Medkeff-nye Roto-Lab Machine to produce the parts with four diverse fillers. Specimens were cut from sample parts for IZOD impact testing using a Testing Machines Inc. (TMI) impact tester. Specimens were also cut for uniform thickness measurements and to conduct permeation studies. Additional sample parts were dropped off of a scaffold to measure impact strength (specific test for fuel tanks). Wrote a summary paper about the project to create and present a poster at ANTEC; which was apart of the National Plastic Exposition (NPE) in 2015. Wrote work instructions for the rotational molding machine to help students get a better understanding of how the machine starts up and operates. Show less Performed research on various polyethylene-based formulations to produce sample parts by rotational molding for potential fuel tank applications. Gained experience on a Medkeff-nye Roto-Lab Machine to produce the parts with four diverse fillers. Specimens were cut from sample parts for IZOD impact testing using a Testing Machines Inc. (TMI) impact tester. Specimens were also cut for uniform thickness measurements and to conduct permeation studies. Additional sample parts were dropped off of a… Show more Performed research on various polyethylene-based formulations to produce sample parts by rotational molding for potential fuel tank applications. Gained experience on a Medkeff-nye Roto-Lab Machine to produce the parts with four diverse fillers. Specimens were cut from sample parts for IZOD impact testing using a Testing Machines Inc. (TMI) impact tester. Specimens were also cut for uniform thickness measurements and to conduct permeation studies. Additional sample parts were dropped off of a scaffold to measure impact strength (specific test for fuel tanks). Wrote a summary paper about the project to create and present a poster at ANTEC; which was apart of the National Plastic Exposition (NPE) in 2015. Wrote work instructions for the rotational molding machine to help students get a better understanding of how the machine starts up and operates. Show less
-
-
-
Farm Bureau Financial Services
-
United States
-
Insurance
-
700 & Above Employee
-
Cleaner
-
Aug 2010 - Aug 2013
Maintained a clean working environment by dusting, vacuuming, and sweeping floors of an insurance office over the weekends. Cleaned bathrooms, took out the trash, and picked up trash outside. In the summer, I would occasionally mow the lawn and in the winter I would shovel the parking lot of snow and ice. Maintained a clean working environment by dusting, vacuuming, and sweeping floors of an insurance office over the weekends. Cleaned bathrooms, took out the trash, and picked up trash outside. In the summer, I would occasionally mow the lawn and in the winter I would shovel the parking lot of snow and ice.
-
-
Education
-
Pittsburg State University
Master’s Degree, Polymer Chemistry -
Pittsburg State University
Bachelor of Engineering (BE), Plastics and Polymer Engineering Technology/Technician -
Pittsburg High School
Community
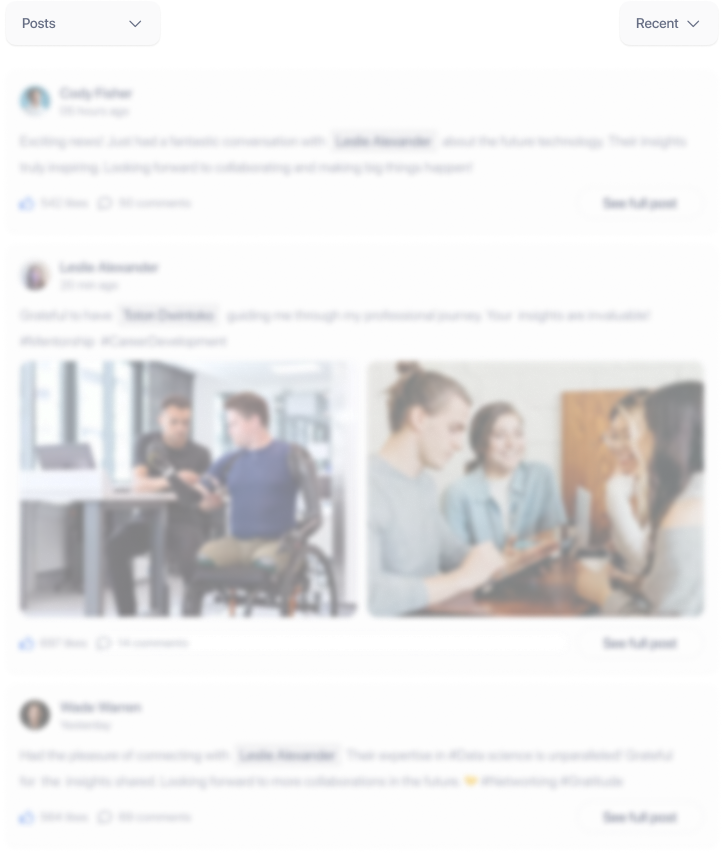