Kyle Hintze
Vice President Operations at In-Place Machining Company- Claim this Profile
Click to upgrade to our gold package
for the full feature experience.
Topline Score
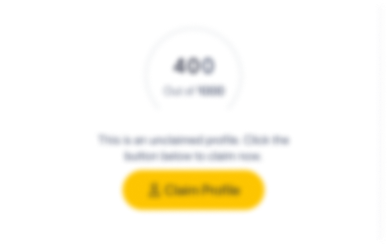
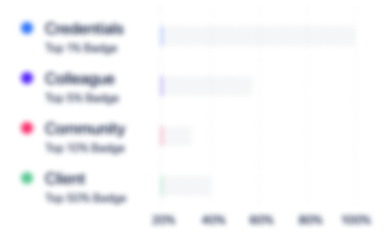
Bio


Credentials
-
Lean Manufacturing Black Belt
-
Experience
-
In-Place Machining Company
-
United States
-
Machinery Manufacturing
-
1 - 100 Employee
-
Vice President Operations
-
Apr 2018 - Present
-
-
-
Inteplast Building Products
-
Cartersville, GA & Milwaukee, WI
-
General Manager
-
Dec 2015 - Apr 2018
Oversee and direct all facility operations. • Multi-Site Full P & L responsibility. • Direct all aspects of facility operations to achieve budgeted profit results and other established success criteria (Safety, Quality, Delivery, Cost, and Inventory). • Drive process capability and process improvements throughout organization. • Achieve financial objectives by establishing plans, collaborate in development of annual budget, manage high level capital expenditures, and implement continuous improvement measures. • Implement short- and long-range operating objectives in support of all business strategy and provide strategic direction for achievement of initiatives. • Established metrics and goals to track performance and instill accountability for results in safety, quality, delivery and productivity. • Develop, coach and mentor direct reports to maximize potential and capabilities; provide visible leadership. • Promote Lean Manufacturing tools and techniques in all production and related processes to increase efficiency and minimize operational costs. • Develop and control improvement initiatives to drive efficiencies that reduce COGS and labor usage.
-
-
-
Sunlite Plastics, Inc.
-
Medical Equipment Manufacturing
-
1 - 100 Employee
-
Plant Manager
-
Nov 2013 - Dec 2015
Oversee and direct all manufacturing operations. - Direct and manage plant operations for production, scheduling, maintenance, engineering, and materials. - Implemented 5S program. - Increased production output by 15% in 2014. - Created new employee training program and doubled workforce to accommodate increased production output initiative. - Increased productivity from 68% to 88% in 2014. - Increased On-Time delivery in 2014 from 82% to 97% in 2014. - Achieved $82,000 material cost savings in 2014, on pace for $88,000 in 2015. - Develop, implement and manage annual operating budgets. - Lead managers to achieve performance expectations and operational goals & objectives. - Review financial statements, sales and activity reports, and other performance data to measure productivity and goal achievement and to determine areas needing cost reduction and program improvement. - Monitor and manage inventory of raw materials, components, supplies and capital expenditures. - Implement standard processes for tooling, engineering, production and process controls.
-
-
-
F. Ziegler Enterprises, Ltd.
-
Italy
-
Packaging and Containers Manufacturing
-
1 - 100 Employee
-
Director of Operations
-
Aug 2011 - Oct 2013
Oversee and direct all manufacturing operations. - Manage all the daily operations: production, scheduling, maintenance, engineering, and materials. - Analyze and evaluate feasibility of strategic plans in terms of budgetary requirements, logistics, and manpower. - Ensure sufficient budget to carry out strategic initiatives. - Evaluate previous year's strategic plan and budget to assess successes. - Develop and maintain manufacturing operations business plans to include all program requirements, labor hours, cycle, and production costs. - Establish production and quality control standards, develop budget and cost controls, and obtain data regarding types, quantities, specifications, and delivery dates of products ordered. - Monitor and manage inventory of raw materials, components, supplies and capital expenditures. - Implement standard processes throughout all departments. - Provide guidance to the development of a manufacturing process plan, including personnel requirements, material needs, subcontract requirements, facility needs, and tooling and equipment needs. - Ensure all established costs, quality, and delivery commitments are met.
-
-
-
-
Operations Manager
-
Sep 2008 - Jun 2009
Manage daily operations by directing personnel and production scheduling, ensuring quality, reducing costs, increasing productivity, and monitoring budget and operational metrics. • Executed daily scheduling requirements for personnel, equipment, production and shipping. • All scheduling aspects performed first hand. • Production scheduling established through customer interaction, supplied schedules and kanban inventory system. • Production Scheduling maintained through Globalshop ERP system. • Materials Management. • Utilized statistical analysis tools for accurate assessment for areas for improvement. • Personally implemented Cell Manufacturing techniques which resulted in an increase of production efficiency from 65% in Sept 2008 to 80% in Feb 2009. • Reduced production lead times by 75% by implementing employee cross-training and One-Piece flow manufacturing practices. • Reduced on hand raw material inventory from over $100,000 to less than $20,000 by initiating release schedules from suppliers. • Reduced Finished Goods inventory through Kan-Ban inventory control implementation. • Initiated Lean Manufacturing principles • Managed 15 direct employees and over 125 indirect employees.
-
-
-
-
Operations Manager
-
Dec 2005 - Sep 2008
Establish and maintain daily operations for purchasing, production, scheduling, inventory control, and shipping & receiving. Promote and motivate team environment. • Promoted from Production Manager • Lean Manager • Responsible for Master Scheduling of equipment, production, purchasing, personnel, and shipping. • Scheduling requirements performed exclusively first hand. • Production scheduling established through “made-to-order” customer requirements. • Expert with Epicor ERP Software. • Materials Management • Through the use of Lean Principles and Cell manufacturing techniques productivity increased from 55% in 2005 to 92% by Jan. 2007. • One-piece material flow emphasis resulted in an On-Time Delivery increase from 48% in 2005 to 97% by Jan. 2007. • Implemented Cell Manufacturing techniques to increase productivity and efficiency. • Utilized statistical analysis for accurate assessment of procedures in order to develop strategies for improving work flow processes. • Provided ongoing operational process analysis, communicated project status, and identified and resolved operational issues and constraints. • Implemented Lean Manufacturing – 3P, 5S, Value Stream Mapping, Kaizen • Reduced labor costs from near 20% to 8% - 10% by focusing and applying cross-training emphasis with employees, implementing improved work instructions and procedures, and adding visual aids for quality detection. • Exceeded aggressive sales goals and revenue targets for 3 consecutive years. • Increased employee morale & performance and decreased turnover within 6 months thru cross-training, performance and attendance bonuses, and regular communication. • Managed 5 direct employees and 45-55 indirect employees.
-
-
-
-
Operations Manager
-
2001 - 2005
Coordinated new projects for launch and presided over daily operations of scheduling, shipping & receiving, purchasing, and quality assurance. • Hands-On production, personnel and equipment scheduling. • Lean Manager • Expert with Peachtree ERP Software • Oversaw international operations with Chinese partners. • Regular communication and travel with Chinese partners. • Maintained Quality Control through ISO 9000:2001 standards • Emphasized continuous improvement by setting daily, monthly, and quarterly goals. • Reduced material costs by 50% by implementing scrap reduction initiatives. • Implemented employee training procedures and increased standards and regulations.
-
-
Education
-
University of Phoenix
Master of Business Administration - MBA -
University of Phoenix
BA, Business Management -
University of Wisconsin Oshkosh
BA, Accounting
Community
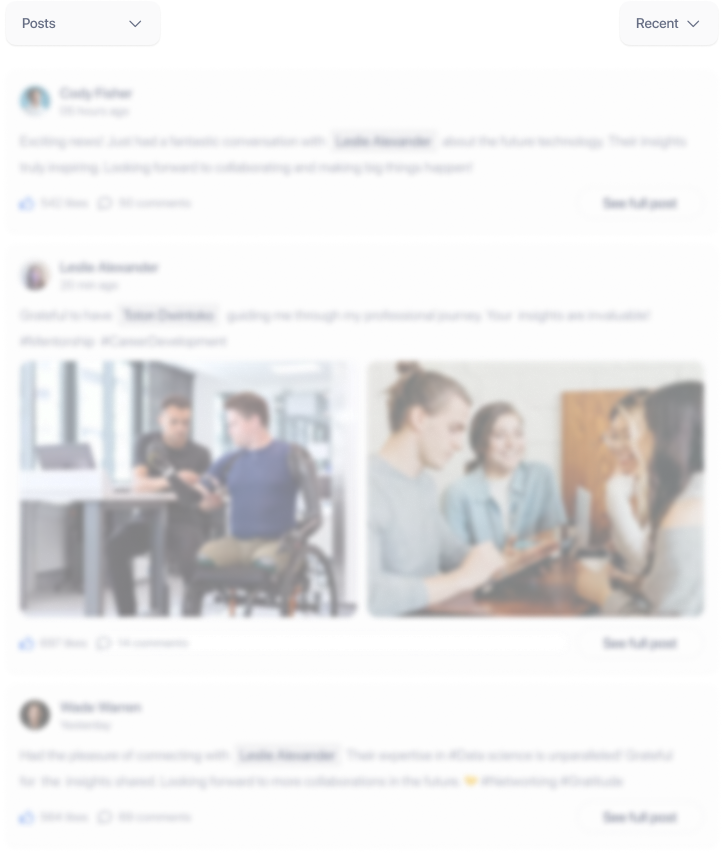