Kurt Maxey
Director of Operations at Tucker Powersports- Claim this Profile
Click to upgrade to our gold package
for the full feature experience.
Topline Score
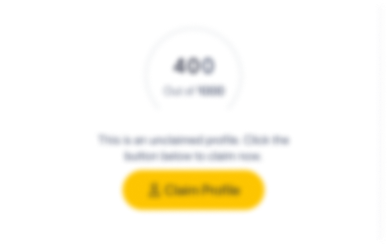
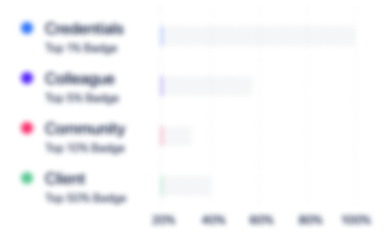
Bio


Experience
-
Tucker Powersports
-
United States
-
Wholesale
-
1 - 100 Employee
-
Director of Operations
-
May 2022 - Present
-
-
-
Komatsu Mining
-
United States
-
Mining
-
700 & Above Employee
-
Distribution Operations Manager
-
2017 - Feb 2020
I successfully managed 2 distribution warehouses (service parts and OE) in the Milwaukee area. I led in the development and delivery of the performance for KPI’s (key performance indicators) and P&L for both sites. I led inbound, outbound, quality, inventory management, maintenance, shipping and CI (continuous improvement). I developed and led a group of 16 salaried employees and 140 hourly employees in achieving or exceeding KPI’s. I successfully managed 2 distribution warehouses (service parts and OE) in the Milwaukee area. I led in the development and delivery of the performance for KPI’s (key performance indicators) and P&L for both sites. I led inbound, outbound, quality, inventory management, maintenance, shipping and CI (continuous improvement). I developed and led a group of 16 salaried employees and 140 hourly employees in achieving or exceeding KPI’s.
-
-
-
Harley-Davidson Motor Company
-
United States
-
Motor Vehicle Manufacturing
-
700 & Above Employee
-
3PL Distribution Manager
-
2009 - 2017
I ran the distribution operations for North America and Canada for all shipments for parts accessories and moter clothes, including fulfilling restocking for all Internation distribution centers. I evaluated and collaborated with the 3PL on continous improvment to ensure quality, delivery and cost targets were met and/or exceeded. I developed and executed work unit plans that supported the financial and operational goals at a department/functional level. I performed to multi million expense budget (P&L). Show less
-
-
Operations Support Resource Manager
-
2005 - 2009
I managed a 230,000 square foot warehouse that shipped parts and accessories to all domestic dealers and European distribution centers. I met or exceeded all KPI's (safety, productivity, quality, cost and people) for the facility. I led and developed a staff of 9 salaried employees with indirect responsibility for up to 200 hourly employees that report into them.
-
-
Work Group Advisor
-
Oct 2003 - Dec 2005
Work Group Advisor 2003 - 2005 Responsible for 40 to 60 union employees in the distribution parts and accessory division making sure that all employees are working to meet/exceed departments delivery, quality, safety and productivity measures and to lead efforts for improvement in those key areas.. Customer delivery rate for QRD of 99.7% in 2004. Exceeded Lines per hour goal for 2004, 29.6, worked on reducing indirect labor. Exceeded quality goal for 2004, 98.4%, by coaching employees Show less
-
-
-
Motorola Mobility (a Lenovo Company)
-
United States
-
Computers and Electronics Manufacturing
-
700 & Above Employee
-
Order Fulfillment Manager
-
1999 - 2003
Responsible for the order fulfillment of key customer accounts, coordinating the production floor to meet customer demand, overseeing order entry, processing, inventory control, warehousing, receiving, shipments and returns for key customer accounts· Reduced ship delinquencies on retail accounts by 17% by developing and executing shipment planning· Increased retail customer satisfaction ratings by 15% using survey data to guide actions· Reduced excess inventory by 25% by carefully planning inbound shipments of product Show less
-
-
Line Manager III
-
1997 - 1999
Responsible for supervising three automated manufacturing lines including a team of thirty (30) to fifty (50) cellular operators, identify and achieve cost measures and reduce cycle time, meet customer requested ship dates, perform disciplinary discussions as mandated, daily tracking and approval of employees hours in a time entry system. Develop, enhance and implement procedures and policies to surpass initiative goals and perform performance evaluations (PACP) and individual dialogues· Reduced cycle time by 10% by evaluating and re-writing procedures· Reduced head count in area by 10% · Reduced quality defects by 20% by implementing a revised training program Show less
-
-
Group Leader Auto line Distribution
-
Jan 1995 - Jan 1997
Supervise thirty cellular operators and make sure that they were helping to achieve company productivity goals and quality goals, daily tracking and weekly inputting of time for all cellular operators and all robotics technicians· Instituted a high involvement team to reduce on-line quality defects· Helped lead first pack lines to become quality certified
-
-
Cellular Operator Auto line Distribution
-
Jan 1993 - Jan 1995
Responsible for helping meet the daily quality, productivity and cycle time goals of department
-
-
Education
-
Concordia College and University of Wisconsin Parkside
B.A, Business Management and Communications -
Concordia University-Wisconsin
Bachelor, Business
Community
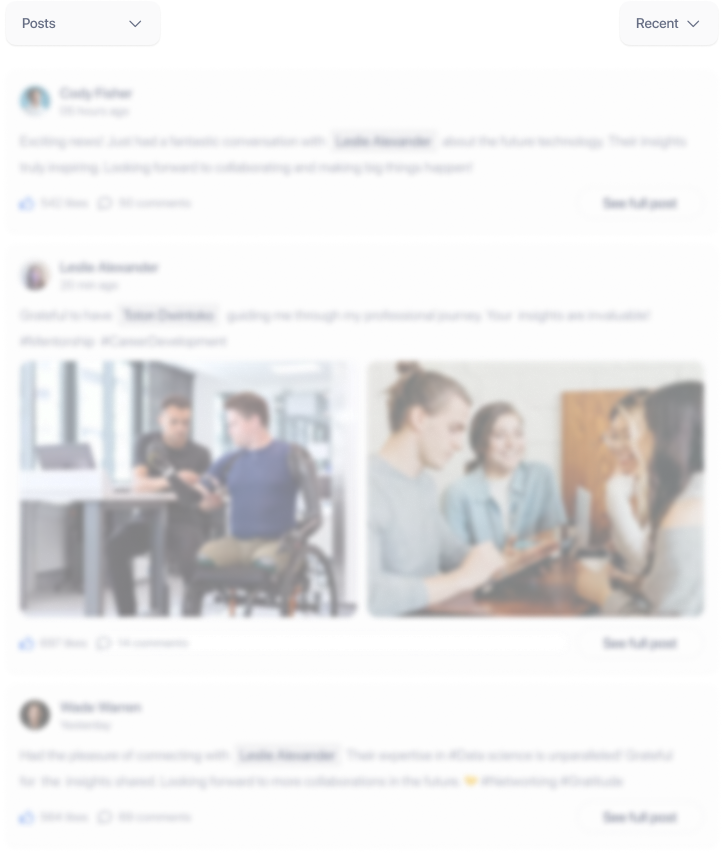