Konrad Diehl
Quarry Superintendent at County Line Stone Co Inc- Claim this Profile
Click to upgrade to our gold package
for the full feature experience.
-
English -
-
Spanish -
Topline Score
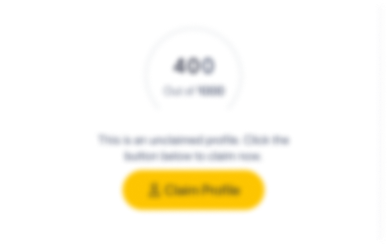
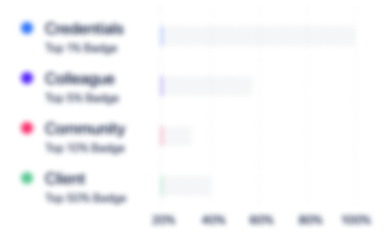
Bio


Experience
-
County Line Stone
-
United States
-
Construction
-
1 - 100 Employee
-
Quarry Superintendent
-
Nov 2019 - Present
Responsible for all daily quarry operations in order to safely fulfill customer demands and maintain sufficient inventory levels to supply aggregates and asphalt to the greater Buffalo and Rochester market.Assume the role of quarry Safety Director, manage all plant safety and policies. MSHA, OSHA. Directly supervise 20 union employees to efficiently quarry limestone, maintain equipment, load customers, and make HMA. Manage quarry expansion and development while overseeing all drilling and blasting operations, which include the following:- blasting patterns and layouts- management of subcontractor drilling companies - management of subcontractor blasting companies - advise on blasting/loading techniques to minimize vibration/sound while efficiently fracturing rock to maximize TPH through the crushing plant but also be diligent to maintain a sufficient supply of Rip Rap in each blastDetermine the daily crushing plan and mining location for the mining team. Daily operation & set up of both crushing plants to efficiently & safely crush limestone. Plant operation includes the following:- determine production scheduling to meet demands of various products- plant startup and shutdown- Manage crushing plants & oversee daily maintenance- Optimize screen cuts and TPH through screen theory and proper screen media- Troubleshoot plant automation (PLC) & electrical devices - yard loading activity HMA Plants:Oversee daily operations of 3 HMA batch plants with RAP systems-HMA plant maintenance -NYS HMA lab certifiedWinter/Shutdown period- Establish shutdown work list of routine maintenance of the crushing plants and HMA plants- Implement plant upgrades to increase efficiency in the crushing operations- Management of ‘stripping’ crew to move overburden and relocate to uncover reserves- Review incurred expenses from previous year to optimize processes- Research equipment and propose capital investment plan for crushing equipment and mobile equipment Show less
-
-
Plant Engineer
-
May 2017 - Nov 2019
-
-
-
Shipley Center for Innovation
-
Clarkson University
-
Business Consultant
-
Sep 2016 - May 2017
-
-
-
Clarkson University
-
United States
-
Higher Education
-
700 & Above Employee
-
Student
-
Aug 2012 - May 2017
Graduated with my Bachelors of Science in Engineering & Management in May 2017. Graduated with my Bachelors of Science in Engineering & Management in May 2017.
-
-
-
GE Transportation, a Wabtec company
-
United States
-
Truck Transportation
-
700 & Above Employee
-
Locomotive Test Intern
-
May 2016 - Aug 2016
-Led a team that tested and diagnosed issues on the locomotives. Final step before shipping to the customer. -Managed a crew of 16 union employees. -Assured safety standards were being adhered to. -Applied 5s and lean principles to reduce inefficiencies and increase the rate of production. -Led a team that tested and diagnosed issues on the locomotives. Final step before shipping to the customer. -Managed a crew of 16 union employees. -Assured safety standards were being adhered to. -Applied 5s and lean principles to reduce inefficiencies and increase the rate of production.
-
-
-
GE Transportation, a Wabtec company
-
United States
-
Truck Transportation
-
700 & Above Employee
-
Material Simplification - Supply Chain Coop
-
Jan 2015 - Aug 2015
Assisting in assuring that all material is readily available for each locomotive that is being produced. This includes: - Communicate to other material leaders throughout GE - Must be able to produce updates to building managers - Miscellaneous material management tasks - Working with GE buyers to order more parts or find out where our ordered parts are - Communicate with our Engineering team if parts need to be modified or scrapped. - Must clearly be able to read Engineering drawings and find the correct parts. Other Tasks: - Currently working on multiple highly interactive projects - Getting a clear understand for Microsoft Access and being able to use that to communicate with multiple other programs i am using. Show less
-
-
-
-
Quality Assurance Supervisor
-
Jun 2013 - Aug 2013
Worked at General Motors Component Holding over the summer of 2013. Hired by RMJ services. -Required to sort through and inspect parts for the assembly of air conditioner units for GM cars. -Managed a team of 8 workers and communicated with plant management. -Developed international skills by communicating with outsourced companies located in Mexico. Worked at General Motors Component Holding over the summer of 2013. Hired by RMJ services. -Required to sort through and inspect parts for the assembly of air conditioner units for GM cars. -Managed a team of 8 workers and communicated with plant management. -Developed international skills by communicating with outsourced companies located in Mexico.
-
-
-
-
Ceo & President
-
Sep 2012 - Mar 2013
Helped create and build a startup company called PremiumPark. Executive Summary- PremiumPark is a service-based company that will assist both drivers and parking lot/garage owners by enhancing their ability to cope with different problems that arise in the parking industry. Our main service for now will be an online website/mobile app that allows drivers to find parking in specific areas. They will be able to determine how congested that parking venue will be and then pre-order a ticket for that venue and pay for it via credit card online. This service will not only help drivers through convenience and guaranteeing them a spot, but it will also be beneficial to venue owners by way of increased revenue and an increased efficient use of all of their available parking spaces. Project is currently inactive. Show less
-
-
-
Tops Markets
-
United States
-
Retail Groceries
-
700 & Above Employee
-
Retail Associate
-
Feb 2010 - Jun 2012
Worked at Tops Market for two years as a cashier. I interacted daily with customers which required people skills. My communication and interaction skills were increased dramatically. Also required the handling of money. Worked at Tops Market for two years as a cashier. I interacted daily with customers which required people skills. My communication and interaction skills were increased dramatically. Also required the handling of money.
-
-
Education
-
Clarkson University
Bachelor of Science - BS, Engineering and Management -
Clarence High School
Advanced Regents Diploma
Community
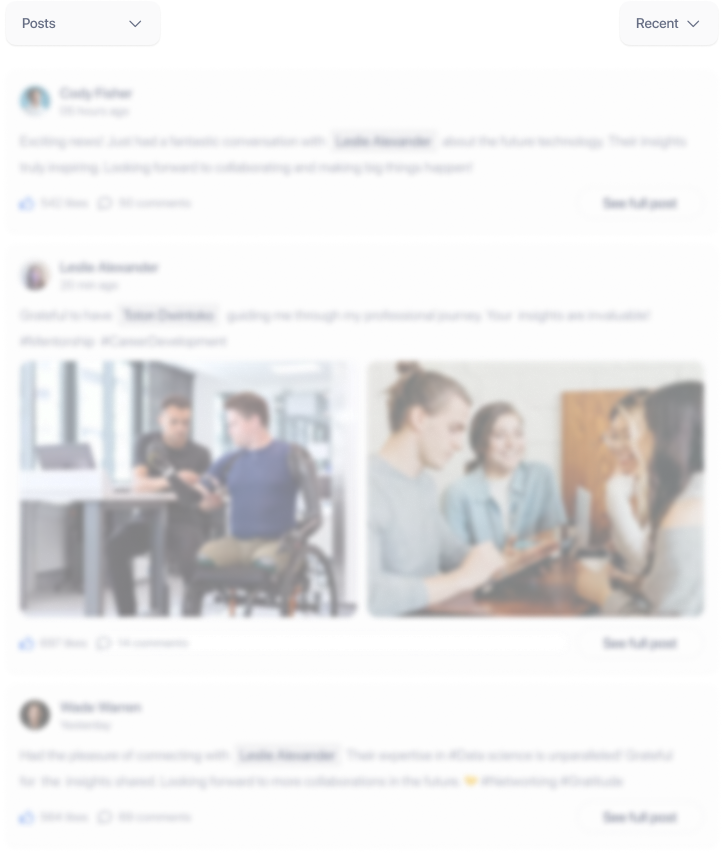