Kim Scrogham, MBA
Manufacturing Controller - Powered Division at Proterra Inc- Claim this Profile
Click to upgrade to our gold package
for the full feature experience.
Topline Score
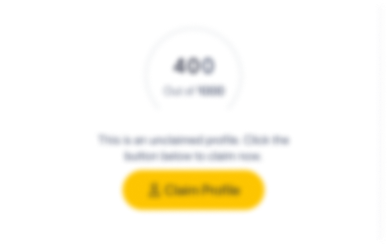
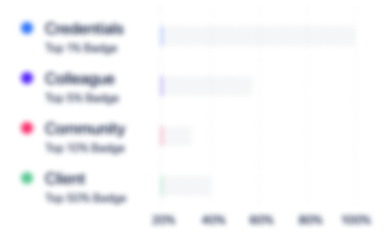
Bio

Bruce Glombicki
I was fortunate to have worked with Kim Scrogham during her time at Stepan. I am an engineer who was very concerned with continuous product improvement. I started making incremental improvements in the processes and noticed that some of the financial data relating to product profitability was less than ideal. I tried to get help with the run accounting that I was seeing. I was brushed aside by other plant accountants. I then asked Kim for her help. Kim set aside time to discuss how my products were made, what assets were used, and some of the accounting that seemed odd to me. By having Kim's 'Let's get this figured out' attitude, Kim and I were able to make great strides in optimizing my run accounting. With Kim's help and guidance, we were able to minimize batch and run discrepancies. By listening and learning some complex processes, Kim was able to troubleshoot and fix the accounting problems I was experiencing. She had valuable inputs into my process too. Kim was easy to work with, and one heck of a team player. I have no reservation at all about highly recommending Kim as a key accounting professional.

Weilenmann Louise
I recommend Kim as a Plant Controller, during the time a worked with Kim she worked well with Staff, was very knowledgeable had timely reporting and was very helpful with SAP BW reporting.

Bruce Glombicki
I was fortunate to have worked with Kim Scrogham during her time at Stepan. I am an engineer who was very concerned with continuous product improvement. I started making incremental improvements in the processes and noticed that some of the financial data relating to product profitability was less than ideal. I tried to get help with the run accounting that I was seeing. I was brushed aside by other plant accountants. I then asked Kim for her help. Kim set aside time to discuss how my products were made, what assets were used, and some of the accounting that seemed odd to me. By having Kim's 'Let's get this figured out' attitude, Kim and I were able to make great strides in optimizing my run accounting. With Kim's help and guidance, we were able to minimize batch and run discrepancies. By listening and learning some complex processes, Kim was able to troubleshoot and fix the accounting problems I was experiencing. She had valuable inputs into my process too. Kim was easy to work with, and one heck of a team player. I have no reservation at all about highly recommending Kim as a key accounting professional.

Weilenmann Louise
I recommend Kim as a Plant Controller, during the time a worked with Kim she worked well with Staff, was very knowledgeable had timely reporting and was very helpful with SAP BW reporting.

Bruce Glombicki
I was fortunate to have worked with Kim Scrogham during her time at Stepan. I am an engineer who was very concerned with continuous product improvement. I started making incremental improvements in the processes and noticed that some of the financial data relating to product profitability was less than ideal. I tried to get help with the run accounting that I was seeing. I was brushed aside by other plant accountants. I then asked Kim for her help. Kim set aside time to discuss how my products were made, what assets were used, and some of the accounting that seemed odd to me. By having Kim's 'Let's get this figured out' attitude, Kim and I were able to make great strides in optimizing my run accounting. With Kim's help and guidance, we were able to minimize batch and run discrepancies. By listening and learning some complex processes, Kim was able to troubleshoot and fix the accounting problems I was experiencing. She had valuable inputs into my process too. Kim was easy to work with, and one heck of a team player. I have no reservation at all about highly recommending Kim as a key accounting professional.

Weilenmann Louise
I recommend Kim as a Plant Controller, during the time a worked with Kim she worked well with Staff, was very knowledgeable had timely reporting and was very helpful with SAP BW reporting.

Bruce Glombicki
I was fortunate to have worked with Kim Scrogham during her time at Stepan. I am an engineer who was very concerned with continuous product improvement. I started making incremental improvements in the processes and noticed that some of the financial data relating to product profitability was less than ideal. I tried to get help with the run accounting that I was seeing. I was brushed aside by other plant accountants. I then asked Kim for her help. Kim set aside time to discuss how my products were made, what assets were used, and some of the accounting that seemed odd to me. By having Kim's 'Let's get this figured out' attitude, Kim and I were able to make great strides in optimizing my run accounting. With Kim's help and guidance, we were able to minimize batch and run discrepancies. By listening and learning some complex processes, Kim was able to troubleshoot and fix the accounting problems I was experiencing. She had valuable inputs into my process too. Kim was easy to work with, and one heck of a team player. I have no reservation at all about highly recommending Kim as a key accounting professional.

Weilenmann Louise
I recommend Kim as a Plant Controller, during the time a worked with Kim she worked well with Staff, was very knowledgeable had timely reporting and was very helpful with SAP BW reporting.

Experience
-
Proterra Inc
-
United States
-
Motor Vehicle Manufacturing
-
500 - 600 Employee
-
Manufacturing Controller - Powered Division
-
May 2023 - Present
-
-
-
Electrolux Group
-
Sweden
-
Manufacturing
-
700 & Above Employee
-
Plant Controller
-
Sep 2020 - May 2023
-
-
-
ATA
-
Ireland
-
Industrial Machinery Manufacturing
-
100 - 200 Employee
-
Site Controller
-
Sep 2018 - Sep 2020
-
-
-
Newell Brands
-
United States
-
Manufacturing
-
700 & Above Employee
-
Plant Controller - Mogadore Operations
-
2015 - Sep 2018
Finance partner for Plant Leadership Team. Monthly/Quarterly/Annual Estimate Preparation and Analysis.Creation of ad-hoc reporting, internal metrics and Make vs. Buy data analysis. Budget preparation and analysis. Key plant financial contact and partner for financial data, reporting , productivity vetting, VA/VE project vetting, and financial support.First Pass Capital and Productivity project financial approvalProduct Costing and analysisMonth end close, flash and manufacturing splits by division/product lineSupervising and approval of accounting staff functions, including month end Show less
-
-
Plant Controller
-
Feb 2013 - 2015
Responsible for all plant level reporting, make vs. buy analysis, YOY standards analysis and budgeting. Maintain and update plant budget estimates and keep current with all financials that will impact the plant. Responsible for all plant level Asset reporting.First pass financial liason for all Capital requests and closing at the plant level. Ad Hoc reporting and any additional expense analysis for plant.Working with plant management team to understand the financials and the impacts of change to the estimates.Creating and maintaining plant based spend metrics to measure YOY performance by spend account, department or category. Bridging gaps to Gross Margin at the plant level, and helping determine productivity target areas. Show less
-
-
Assistant Controller
-
2011 - 2013
Weekly and daily Plant reporting, Monthly Plant Metric reporting. Responsible for all plant level Asset reporting. Maintain and report major Capital Project spend information. Ad Hoc reporting and expense analysis for plant. Month end journal entries, Budget to actual analysis, month end reporting. Variance Analysis, Cycle Count Analysis.
-
-
-
Forbo Flooring Systems
-
Netherlands
-
Building Materials
-
700 & Above Employee
-
Plant Accountant
-
2008 - 2011
As the plant accountant at Forbo/HB Fuller I was able to help streamline the processes including error corrections, cycle counts, month end close and financial reporting. I was involved in setting up training, and training the staff in the Maintenance Work order module for SAP. As the plant accountant at Forbo/HB Fuller I was able to help streamline the processes including error corrections, cycle counts, month end close and financial reporting. I was involved in setting up training, and training the staff in the Maintenance Work order module for SAP.
-
-
-
Stepan Company
-
United States
-
Chemical Manufacturing
-
700 & Above Employee
-
Plant Accountant II
-
2005 - 2008
-
-
Education
-
North Central College
MBA, Accounting -
DeVry University
BS, Accounting
Community
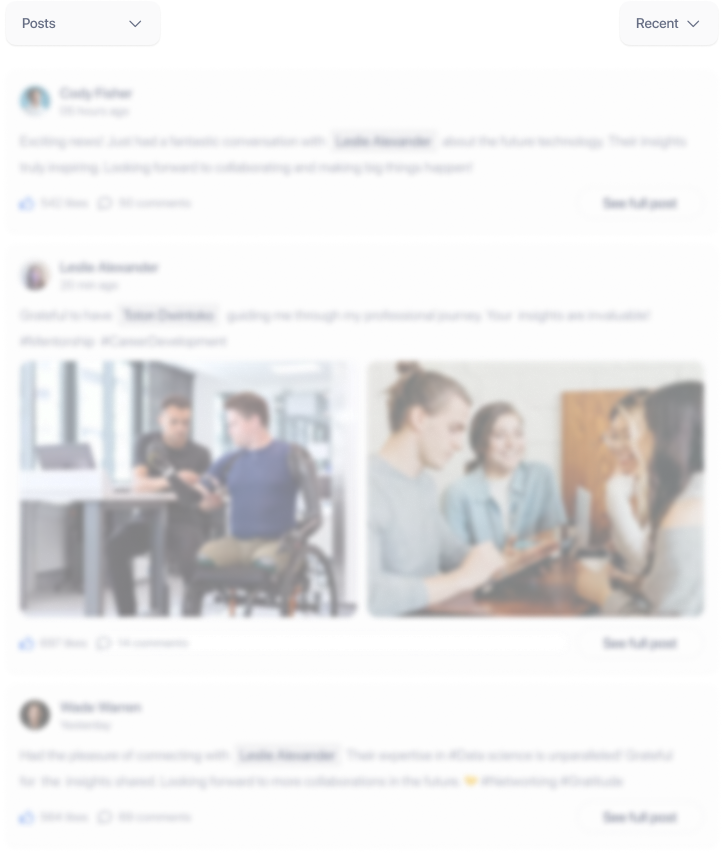