Khurram Bashir
Operations Manager at Black Lake- Claim this Profile
Click to upgrade to our gold package
for the full feature experience.
Topline Score
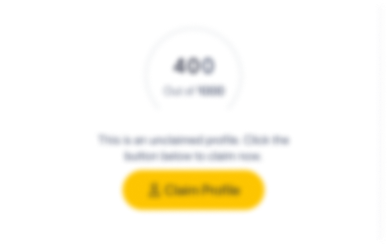
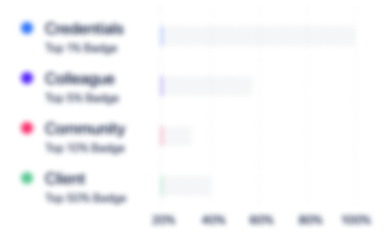
Bio


Experience
-
Black Lake
-
United Arab Emirates
-
Oil and Gas
-
1 - 100 Employee
-
Operations Manager
-
Dec 2022 - Present
-
-
-
Parker Wellbore
-
United States
-
Oil and Gas
-
700 & Above Employee
-
Machine Shop Manager
-
Oct 2013 - Jun 2023
Overall incharge of machine shop and welding shop operations which includes threading of API connections, stabilizer and fishing tools hard facing and grinding. Managing the client quiries and providing quotations & solutions. Overall incharge of machine shop and welding shop operations which includes threading of API connections, stabilizer and fishing tools hard facing and grinding. Managing the client quiries and providing quotations & solutions.
-
-
-
International Tubular Services
-
Islamabad-Pakistan
-
HSEQ Manager/FMR
-
Dec 2008 - Sep 2013
•Implementation and maintenance of Group policies, objectives, IMS and GMP to ensure full compliance with company, group, client and governmental HSE requirements •Provide support in developing, reviewing and monitoring of the HSEQ Plan and objectives and targets. •Support team in conducting Risk Assessments and ensure it covers all company operations and ensure risk controls measures are taken to meet or exceed the applicable legal requirements. •Produce HSEQ performance reports and submit for management review. •Responsible for reviewing accident and incident HSEQ reports and investigations •Ensure new staffed are trained and all company visitors and contractors are educated for health safety management as per their roles and activities and evaluated employee & contractors HSE performance. •Manage customer complaints, non-conformance, and Corrective and preventive actions. •Managing ISO-9001, ISO-14001, OHSAS-18001, API-Q1, API-5CT, and API-7-1implementation in line with ITS Group manuals & directions. •Manage the premium licensee (VAM, TENARISHYDRIL, JFE & BENOIT) qualification, documentations, royalty reporting, correspondence and audits. •Manages internal & external Audits. •Managing the Contractors suitability as per the requirements. •Conduct capability analysis against the customer inquiries to assure all processes involve, material needed, competence of people required are sufficient to start production as per our IMS plan. •Develop processes quality control parameters and monitor accordingly by developing procedures and maintaining records. (CNC Programming, Surface treatment (Zn / Mn Phosphate, Abrasive blasting, swaging and stress relieve, hard banding, redressing of tools etc) •Supervise and direct Quality control Team to ensure timely and accurate completion of quality projects and tasks. •Manages the monitoring & monitoring equipment. •Manages the non conforming product and customer complaints. Show less
-
-
-
-
Student of Naveed Sb
-
2012 - 2012
-
-
-
Conqueror Medical Pvt Ltd
-
Sialkot-Pakistan
-
Operation Manager
-
Jan 2002 - Nov 2008
Manages operational activities for the surgical instruments from start to end involve designing & development, import and export, productions, packaging and storage. Crafted and successfully implemented numerous initiative and strategies to achieve management’s goals. Acted as project manager and team leader for maintenance of surgical instrument technical Standards like ISO 7153-1, 7151, 7740, & 7741 and ISO 13485 Give key Support Quality department establishing, implementing and maintaining in Management System and Peachtree cost and accounting system. Develop the quality plan for the manufacturing of surgical instruments. Supporting the marketing and sales team in finalizing the Tenders and customer contract bids, terms and conditions and delivery schedules Beside this I am being the boss of the department responsible for •Ensure the implementation of process quality standards and Quality program •Conduct the validation of special & outsource processes like forging shops, Milling and lathe machine operations, tempering, filling and grinding, acid, passivation, electro polishing, ultrasonic cleaning and sandblasting and packaging. • Development & implementation of production plan and ensuring on time delivery to customers as per agreed delivery schedule •Plan for the procurement of raw materials, consumables, forgings, semi finished products against customer orders and inquiries. •Annual evaluation & assessment of employee, Sub Contractors & Vendors. Also identify the training need assessment of them. •Approve the sub-contracting billing, vendor’s purchase cases and employee attendance records and forward to finance for payments. •Managing the internal & external audit includes second party audits of client technical audits and supplier routine workshop assessments. •Customer correspondences regarding the inquiries and complaints •Manages for the import and export shipments along with export departments Show less
-
-
Education
-
Gomal University
Master In Public Administration, Marketing Management
Community
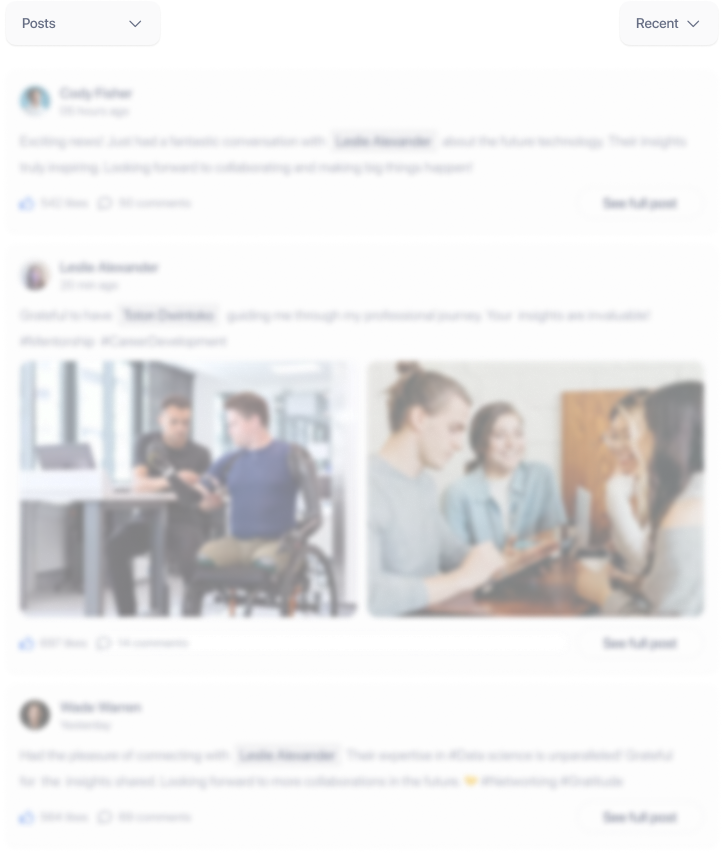