Khoa C.
Sr. Engineer Spaceship Propulsion Design at Virgin Galactic- Claim this Profile
Click to upgrade to our gold package
for the full feature experience.
-
English -
-
Vietnamese -
Topline Score
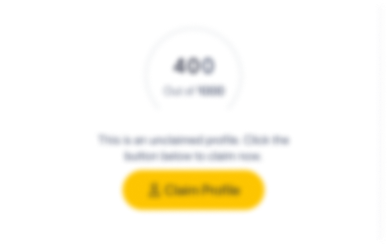
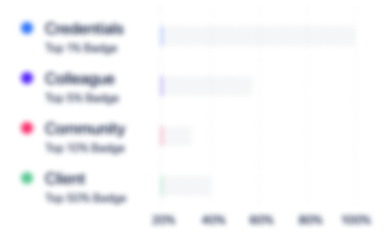
Bio

Carl Nelson
Khoa did solid work for me while at UNL. He was self-motivated and did a lot of good design and computer modeling work on modular robot systems. Ultimately his work was published in a peer-reviewed conference, which is an impressive accomplishment for an undergraduate.

R. Glenn Sellar
I've hired and mentored >40 interns over the years and Khoa is one of the best. I've been particularly impressed by his maturity and highly professional attitude. Khoa is serious about his work, reliable, and works very well in a team environment. He's also unusually capable for someone at the start of their career and showed considerable flexibility and willingness to take on a variety of tasks both within and outside of his Mechanical Engineering discipline.

Carl Nelson
Khoa did solid work for me while at UNL. He was self-motivated and did a lot of good design and computer modeling work on modular robot systems. Ultimately his work was published in a peer-reviewed conference, which is an impressive accomplishment for an undergraduate.

R. Glenn Sellar
I've hired and mentored >40 interns over the years and Khoa is one of the best. I've been particularly impressed by his maturity and highly professional attitude. Khoa is serious about his work, reliable, and works very well in a team environment. He's also unusually capable for someone at the start of their career and showed considerable flexibility and willingness to take on a variety of tasks both within and outside of his Mechanical Engineering discipline.

Carl Nelson
Khoa did solid work for me while at UNL. He was self-motivated and did a lot of good design and computer modeling work on modular robot systems. Ultimately his work was published in a peer-reviewed conference, which is an impressive accomplishment for an undergraduate.

R. Glenn Sellar
I've hired and mentored >40 interns over the years and Khoa is one of the best. I've been particularly impressed by his maturity and highly professional attitude. Khoa is serious about his work, reliable, and works very well in a team environment. He's also unusually capable for someone at the start of their career and showed considerable flexibility and willingness to take on a variety of tasks both within and outside of his Mechanical Engineering discipline.

Carl Nelson
Khoa did solid work for me while at UNL. He was self-motivated and did a lot of good design and computer modeling work on modular robot systems. Ultimately his work was published in a peer-reviewed conference, which is an impressive accomplishment for an undergraduate.

R. Glenn Sellar
I've hired and mentored >40 interns over the years and Khoa is one of the best. I've been particularly impressed by his maturity and highly professional attitude. Khoa is serious about his work, reliable, and works very well in a team environment. He's also unusually capable for someone at the start of their career and showed considerable flexibility and willingness to take on a variety of tasks both within and outside of his Mechanical Engineering discipline.

Credentials
-
Leading When You're Not in Charge
LinkedInMay, 2022- Nov, 2024 -
Agile Foundations
LinkedInSep, 2021- Nov, 2024 -
Agile Project Leadership
LinkedInSep, 2021- Nov, 2024 -
Transitioning from Waterfall to Agile Project Management
LinkedInSep, 2021- Nov, 2024 -
Engineer In Training (EIT)
NCEESMay, 2012- Nov, 2024
Experience
-
Virgin Galactic
-
United States
-
Aviation and Aerospace Component Manufacturing
-
700 & Above Employee
-
Sr. Engineer Spaceship Propulsion Design
-
May 2022 - Present
Provide technical leadership to the design and development of new valves and mechanical components to support the integration of the rocket propulsion system for existing and new spaceship programs. This include requirement development and management for the propulsion valves and working through full product design lifecycle with Suppliers. Provide technical leadership to the design and development of new valves and mechanical components to support the integration of the rocket propulsion system for existing and new spaceship programs. This include requirement development and management for the propulsion valves and working through full product design lifecycle with Suppliers.
-
-
-
VACCO Industries
-
United States
-
Defense and Space Manufacturing
-
200 - 300 Employee
-
Senior Project Engineer
-
Jun 2019 - May 2022
Project management for the development of NASA's ORION space valves and Boeing’s AGM-86 ALCM Programs: • Managed the complete project life cycle and provided technical leadership to the design, analysis, development, and testing of motorized and solenoid actuated space valves to support customer flight testing • Managed and maintained weekly project reporting and tracking to ensure project is completed in a timely manner • Monitored the compliance of all project requirements and scope changes to ensure project is within program budget • Estimated project hours for out-of-scope changes and provided project schedule updates to program office & customer • Led failure investigations and provided dispositions for non-conformances to support project completion • Led production effort to successfully build, test, and deliver solenoid and motor actuated space valves to customer to support program milestones Show less
-
-
-
Woodward, Inc.
-
United States
-
Aviation and Aerospace Component Manufacturing
-
700 & Above Employee
-
Senior Mechanical Engineer
-
Aug 2016 - Jun 2019
Project system management for the development of airplane Thrust Reverser Actuation Systems (TRAS):• Managed and led project team to drive the design and development of solenoid control valves, electric and hydraulic locks, hydraulic actuators, manual drive clutch mechanism, hydraulic tubing/hose, and flexible synchronization shafts• Collaborated with customer to develop technical requirements for NPI system development and product specifications• Performed Verification and Validation (V&V) for entire actuation systems to customer specification requirements• Managed over 500+ requirements and defined artifacts to ensure product design meets customer requirements• Led PDR, CDR, MRR, TRR activities and technical customer/supplier meetings to support TRAS program development• Independently wrote acceptance and qualification test procedures and reports for various valves, actuators, and locks• Led and support component acceptance and qualification testing in accordance with RTCA DO-160G• Investigated, planned, troubleshoot, and resolved acceptance and qualification test failures using RCCA processes• Led and drove completion of ground and flight test instrumented components to support NPI TRAS system development• Developed and performed iterative trade studies to improve fire sealing and blanket design for an expansion joint tube• Prepared and reviewed technical engineering proposal for new development TRAS programs• Utilize lean six sigma techniques to improve the quality and manufacturing process time for components on Woodward's TRAS legacy programs. Show less
-
-
Mechanical Engineer II
-
Nov 2012 - Aug 2016
Mechanical design and development of airplane Thrust Reverser Actuation Systems (TRAS):• Managed the design of several Line Replaceable Units (LRUs) to support the development of the Airbus A320neo/A330neo commercial jet and GE Passport 20 Engine business jet• NX 7.5 and SolidWorks CAD design and drawings of actuators, isolation and directional control valves, synchronization tubing/hoses, flexible shafts, tertiary lock systems, and manual drive systems• Developed interface and source control drawings (ICD & SCD) per customer requests• Prepared and reviewed compliance matrices to support program development• Successfully led weight reduction effort for GE Passport 20 TRAS pivot door actuator to redesign and reduce weight of an existing actuator by 2.5+ lbs to support customer system weight reduction campaign• Generated detail drawings and CAD model using NX for various TRAS assemblies to design electric and hydraulic locks, hydraulic actuators, manual drive clutch mechanism, hydraulic tubing/hose, and flexible synchronization shafts• Utilized MMPDS, aerospace, and military standards to select material/hardware for the design of locks and actuators• Performed 100+ tolerance stack-up analysis to verify the mechanical fit and performance of an Electric Tertiary Lock• Created and implemented a special tolerance sizing tool to design the synchronization system for various TRAS programs• Utilized GD&T per ASME Y14.5 to create, review, and correct drawings to support product design and development• Created and managed ECRs/ECNs for the production release of drawings and reports using PTC Windchill PLM Show less
-
-
-
GE Aerospace
-
United States
-
Aviation and Aerospace Component Manufacturing
-
700 & Above Employee
-
Unigraphics/SolidWorks Designer via Belcan TechServices
-
Jan 2012 - Nov 2012
Mechanical design and development of airplane Thrust Reverser Actuation Systems (TRAS): • Utilized Unigraphics NX7.5 and SolidWorks 2006/2012 to modify the design and drawings of components for hydraulic valves and actuators to support sustaining and NPI programs • Converted legacy drawings from SolidWorks, AutoCAD, and image files to Unigraphics NX7.5 • Responsible for the review, incorporation of redlines, and creation of engineering change request of mechanical drawings and design/test documentations Show less
-
-
-
Chatsworth Products
-
United States
-
IT Services and IT Consulting
-
200 - 300 Employee
-
Manufacturing Industrial Engineer via Aerotek
-
Nov 2011 - Jan 2012
Implemented an Enterprise Resource Planning program, EPICOR, to improve manufacturing quality and productivity: • Developed manufacturing processes for sheet metal server and cable managing cabinets/racks • Utilize engineering change orders, bill of materials, and drawing revisions, to update manufacture operations Implemented an Enterprise Resource Planning program, EPICOR, to improve manufacturing quality and productivity: • Developed manufacturing processes for sheet metal server and cable managing cabinets/racks • Utilize engineering change orders, bill of materials, and drawing revisions, to update manufacture operations
-
-
-
Land Sea Discovery Group Research & Development
-
Pasadena, CA
-
Mechanical Design Engineer
-
May 2011 - Jan 2012
Underwater vessel design for a Targeted UV Chem Bio Explosive Detector (TUCBED) instrument probe: • Collaborated with scientists to design a pressure vessel to house the TUCBED, which included a multi-seal quartz window mounted endcap, window retention plate, and a hermetically sealed electrical endcap • Designed a test fixture and improved an existing design of an underwater modular optical baffle for 100-meter ground testing of the TUCBED • Performed FEA stress analysis using SolidWorks SimulationXpress to ensure the design of the TUCBED pressure vessel have sufficient margin of safety for underwater testing • Utilized SolidWorks 2011 to create CAD models, detail drawings, and material part list to procure pressure vessel and test fixture for development testing • Managed the procurement of designed components and interacted with machine shops to reduce manufacturing cost and lead time to meet project schedule Show less
-
-
-
-
SolidWorks Design/Drafter via Randstad Engineering
-
Sep 2011 - Sep 2011
Modification of aerospace fastener drawings and assist in improving document control process: • Utilized AutoCAD 2006 and DWG True View to create and revise fastener drawings • Utilized FoxPro 2.0 and WSS 2007 to track drawings, ECOs, and DCRs changes • Interacted with factory floor personnel to troubleshoot manufacturing drawing errors • Performed engineering analysis for breakneck diameter, gage protrusion, and head height of fasteners • Utilized NAS, AS, ASTM, and ASME standards to perform design reviews of fastener drawings Show less
-
-
-
NASA Jet Propulsion Laboratory
-
United States
-
Defense and Space Manufacturing
-
700 & Above Employee
-
Mechanical Engineer
-
Jan 2011 - May 2011
Modification of Opto-Mechanical Design for Combined Raman Microprobe & Multispectral Microscopic Imager:• Collaborated with engineers & scientists to re-design an imager optical lens barrel to maximize CCD camera field of view• Modified an existing illuminator light box design to eliminate trap light and maximize light output for the imager• Completed thermal analysis, build, and test of a prototype heat sink fan assembly for a solid-state laser• Performed linearity test and statistical analysis of a photo sensor CCD camera by examining rock samples Show less
-
-
Mechanical Engineer
-
Sep 2010 - Dec 2010
Development of the Aircraft Borne Scanning Microwave Limb Sounding (MLS) Instrument:• Utilized NX6 to generate conceptual models and drawings to support the MLS project development• Redesigned and improved the rotational inertial balance of an existing aluminum rotary microwave chopper• Modified the design of a rotational test fixture to support the ground testing of the MLS cryogenic dewar• Performed heat transfer analysis to design an opto-mechanical structure with sufficient thermal contact for thermal sensitive electronic receivers Show less
-
-
-
Omaha Public Power District
-
United States
-
Utilities
-
700 & Above Employee
-
Project Engineer
-
May 2010 - Aug 2010
Compiled design documents for vendors and assisted Nuclear Project team with various upgrade projects: • Modified engineering change documents for the replacement of thermal valve equipment • Researched and compiled electrical equipment qualification table for replacement valves • Performed structural pipe and welding support analysis for the potable water tank project • Assisted in performing preventive maintenance inventory inspections for the water screen project Compiled design documents for vendors and assisted Nuclear Project team with various upgrade projects: • Modified engineering change documents for the replacement of thermal valve equipment • Researched and compiled electrical equipment qualification table for replacement valves • Performed structural pipe and welding support analysis for the potable water tank project • Assisted in performing preventive maintenance inventory inspections for the water screen project
-
-
-
NASA Microgravity University
-
Lincoln, Nebraska
-
UNL Undergraduate Research Assistant Fellowship
-
Dec 2009 - May 2010
Successfully validated thermal parameters of a cryo-cooler in NASA reduced gravity flight week for Ad Astra Rocket Co. VASIMR ISS Demonstrator Mission: • Assisted in assembling and load testing of an aluminum structure for use in reduced gravity environment • Collaborated and assembled a flight-like cryo-cooler and performed a vacuum leak test • Supported in the construction of the cryo-cooler’s Mylar radiation shield Successfully validated thermal parameters of a cryo-cooler in NASA reduced gravity flight week for Ad Astra Rocket Co. VASIMR ISS Demonstrator Mission: • Assisted in assembling and load testing of an aluminum structure for use in reduced gravity environment • Collaborated and assembled a flight-like cryo-cooler and performed a vacuum leak test • Supported in the construction of the cryo-cooler’s Mylar radiation shield
-
-
-
University of Nebraska-Lincoln
-
United States
-
Higher Education
-
700 & Above Employee
-
Secondary Research Investigator - UCARE
-
Jan 2008 - May 2010
I designed from concept a four degrees-of-freedom modular self-reconfigurable robot for space application using SolidWorks 2006. Additionally, I performed kinematic optimization analysis to determine the mobility of the robot joints and formulated five unique robot locomotion gaits. This successful design and research results were presented at several conferences and was published in the ASME 2011 International Design Engineering Conference proceeding. I designed from concept a four degrees-of-freedom modular self-reconfigurable robot for space application using SolidWorks 2006. Additionally, I performed kinematic optimization analysis to determine the mobility of the robot joints and formulated five unique robot locomotion gaits. This successful design and research results were presented at several conferences and was published in the ASME 2011 International Design Engineering Conference proceeding.
-
-
Education
-
University of Nebraska-Lincoln
Bachelor of Science, Mechanical Engineering
Community
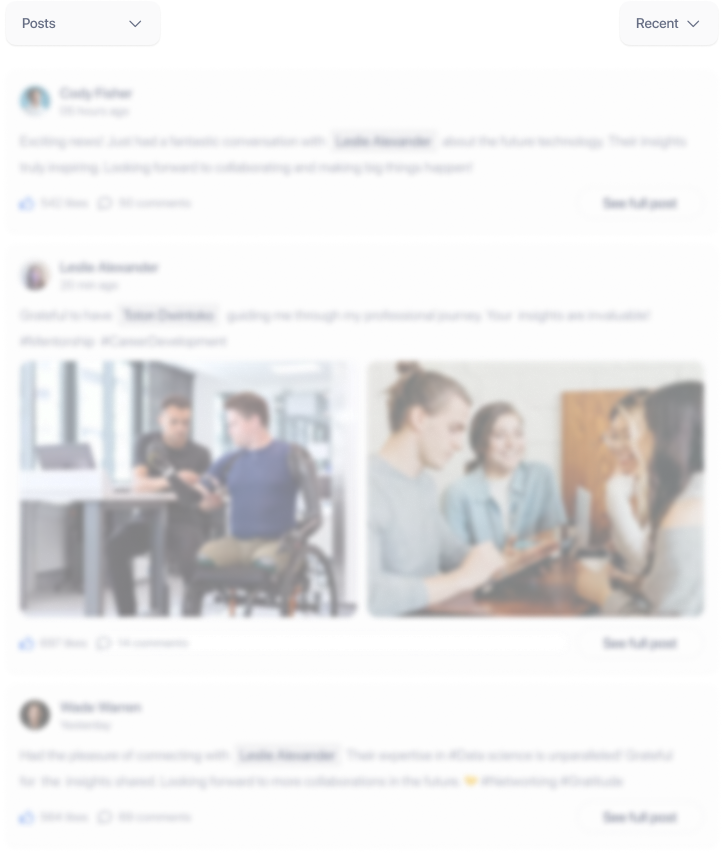