Kevin McNerney
Founder at DeviceAlliance- Claim this Profile
Click to upgrade to our gold package
for the full feature experience.
Topline Score
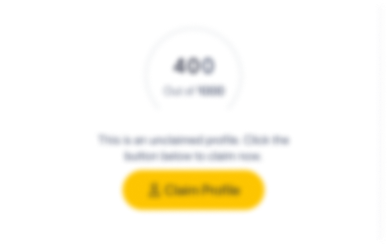
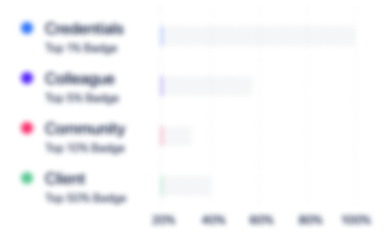
Bio


Experience
-
DeviceAlliance
-
United States
-
Medical Equipment Manufacturing
-
1 - 100 Employee
-
Founder
-
Jan 2010 - 14 years
Southern California Founder, past President and Board Member of DeviceAlliance™, a member-focused community of experienced southern California medical device professionals committed to building relationships, sharing knowledge, and gaining insight into the key issues and opportunities within the medical device industry.
-
-
-
-
Executive Medical Device Consulting
-
Jan 2010 - 14 years
Orange County, California, United States Leveraging 30+ years of global Medical Device engineering, operations, and program management to assist aspiring businesses in attainment of stretch goals in a range of areas. My strengths include an extreme breadth of experience, a collaborative nature, and a strong desire to create results. At this juncture in my career, I only consider opportunities with companies that present a fun and collaborative environment in an exciting business niche.
-
-
-
Unlicensed Chimp Technologies
-
Entertainment Providers
-
COO
-
May 2014 - May 2017
Irwindale, CA Unlicensed Chimp Technologies is a Brand Activation and Engagement company. UCT utilizes a unique platform of location-based interactive technology and user applications to create crowd-based immersive experiences which drive significantly higher levels of engagement, brand loyalty and data collection.
-
-
-
Nanospectra Biosciences
-
Biotechnology Research
-
1 - 100 Employee
-
Interim COO / Vice President (VP) Operations
-
Jul 2011 - Apr 2013
Irvine CA / Houston TX Nanospectra is a novel nanotechnology-based cancer therapy company working to commercialize a novel and powerful targeted therapy for tumor ablation. Consult-to-perm COO responsibilities including development of the commercialization plan, capital equipment and disposable product design and manufacture, nanoparticle process scale up and creation and development and implementation of viable US and European regulatory pathway strategies.
-
-
-
CryoCare Inc
-
Medical Device
-
Vice President (VP) Operations
-
Jul 2010 - Jul 2011
Irvine, CA CryoCare is early stage cryoablation company specializing in women’s health. Initial responsibilities include technology transfer, 510 submission, manufacturing strategy and funding support. CryoCare is an exciting opportunity which utilizes a “next generation” platform technology that we believe can put cryo on the forefront of many existing and newly developed more-invasive procedures.
-
-
-
Allergan
-
Pharmaceutical Manufacturing
-
700 & Above Employee
-
Engr and Ops Consultant - hired by Vice President (VP) Operations
-
2007 - 2009
Irvine, CA A premier global specialty pharmaceutical and medical device company with over $4 billion in sales. • Managed a complex product improvement program for a critical aesthetic drug delivery system. The newly introduced product was already over $100 million in sales and 30% growth. • Development through globalization of the new design was accomplished in 12 months, less than ½ the time originally estimated. The new design effectively eradicated a 4% field failure rate to zero.
-
-
-
Beckman Coulter Diagnostics
-
United States
-
Medical Equipment Manufacturing
-
700 & Above Employee
-
Operations Consultant to VP Operations /Mfg
-
2006 - 2007
A Leading manufacturer of biomedical testing instrument systems with $3 billion in global sales. • Performed a company-wide analysis of the reagent manufacturing operations to identify a “Best of Class” vision and related implementation plan involving integration of manufacturing automation, project management, LEAN, Six Sigma and other associated World Class initiatives
-
-
-
-
Vice President (VP) Operations
-
2003 - 2005
Ontario, CA LifePoint, Inc. is a diagnostic device start-up, completing development and scale-up a saliva-based, blood-comparable drug and alcohol testing system with substantial global opportunity in the law enforcement, industrial and hospital testing markets. • Recruited to manage the reestablishment of the Operations organization after funding issues resulted in loss of all but one indirect support staff. Assessed technical and resource requirements, recruited and hired all support management… Show more LifePoint, Inc. is a diagnostic device start-up, completing development and scale-up a saliva-based, blood-comparable drug and alcohol testing system with substantial global opportunity in the law enforcement, industrial and hospital testing markets. • Recruited to manage the reestablishment of the Operations organization after funding issues resulted in loss of all but one indirect support staff. Assessed technical and resource requirements, recruited and hired all support management staff. • Managed the development of the manufactured product and packaging design, validation and subsequent production scale-up of both a sophisticated electromechanical instrument and complex disposable device within a 5-month period. • In response to key business plan requirements, developed and began implementation of a multi-faceted cost reduction plan to reduce the disposable device cost by 80% through design changes, off-shore manufacturing and automation. • Established requirements for the “next generation” instrument including sourcing of a contract-manufacturing partner capable of both product redesign and low-cost production. • Key participant in “repackaging” the company’s product and business strategy. • Funding issues led to LifePoint’s insolvency. Led an employee-based asset buy-out plan. Show less
-
-
-
Power Medical Interventions
-
Medical Equipment Manufacturing
-
1 - 100 Employee
-
Vice President (VP) Operations
-
2000 - 2003
New Hope, PA Founded in 1999, Power Medical is an innovative and aggressive developer of a “next generation” surgical stapling and cutting system. In a very short period, the company has developed and launched (domestic and international) a sophisticated electro-mechanical platform with over ten enabling devices launched or in development. • Built and managed the contract manufacturing, planning, purchasing, distribution and manufacturing engineering departments. • Ad-hoc engineering project… Show more Founded in 1999, Power Medical is an innovative and aggressive developer of a “next generation” surgical stapling and cutting system. In a very short period, the company has developed and launched (domestic and international) a sophisticated electro-mechanical platform with over ten enabling devices launched or in development. • Built and managed the contract manufacturing, planning, purchasing, distribution and manufacturing engineering departments. • Ad-hoc engineering project leader for the Circular line, responsible for bringing a complex surgical stapling/cutting system (SurgASSIST ™) from prototype to international market in world-class time. • Grew contract-manufacturing capacity to support a sales growth from $2 million to $12 million. Requirements included establishment and management of four contract manufacturing organizations in addition to one major product line transfer. • Participant in an extensive FDA audit process. • Left Power Medical after customer related functionality issues lead to a stall in funding and instability in full time employment. Show less
-
-
-
Leiner Health Products
-
Pharmaceutical Manufacturing
-
1 - 100 Employee
-
Director of Corporate Engineering
-
1999 - 2000
Carson, CA Joined Leiner, a privately owned, $700 million vitamin, supplement and OTC drug manufacturer / distributor to lead a major technical infrastructure development program. • Created a corporate engineering group to support the technical requirements of a growing company with little to no technical infrastructure. • Developed a component spec system and formalized the change control process. Established several component consolidation programs with annual savings in excess of $2… Show more Joined Leiner, a privately owned, $700 million vitamin, supplement and OTC drug manufacturer / distributor to lead a major technical infrastructure development program. • Created a corporate engineering group to support the technical requirements of a growing company with little to no technical infrastructure. • Developed a component spec system and formalized the change control process. Established several component consolidation programs with annual savings in excess of $2 million. • Introduced a cross-functional project management process to significantly improve the success rate and time to market of new product designs. Show less
-
-
-
B. Braun Group
-
Germany
-
Medical Equipment Manufacturing
-
700 & Above Employee
-
Director Mfg. Engr/ Corp. Engr/ SAP Implementation
-
1994 - 1999
Irvine, CA Progressive management responsibilities in a $350 million IV solutions and sets company recently purchased by B.Braun. Managed most of the primary engineering and operations technical functions as well as direction of a new manufacturing/supply chain systems integration. • Director, SAP Manufacturing. SAP project integration leader for an enterprise based manufacturing business system implementation. • Director, Manufacturing Engineering and Maintenance. Management of 140 people… Show more Progressive management responsibilities in a $350 million IV solutions and sets company recently purchased by B.Braun. Managed most of the primary engineering and operations technical functions as well as direction of a new manufacturing/supply chain systems integration. • Director, SAP Manufacturing. SAP project integration leader for an enterprise based manufacturing business system implementation. • Director, Manufacturing Engineering and Maintenance. Management of 140 people and an $18 million budget. Major projects included new cleanroom construction, implementation of new maintenance/parts inventory management software, and CA Air Board certification of a co-gen catalyst system. • Manager, Process and Sterilization Engineering. Responsibilities including process design and pharmaceutical scale-up and for a generic nasal drug. Directed Sterilization Engineering department functions including change control, new cycles, equipment, systems and qualification associated with on-going operations and new product NDA applications. • Manager, Automation Engineering. Responsibility for new equipment development and implementation related to cost reductions, new product designs and product/process improvements. Show less
-
-
-
Mentor Worldwide LLC
-
United States
-
Medical Device
-
100 - 200 Employee
-
Engineering Manager
-
Jun 1993 - Nov 1994
A $50 million division specializing in Class III silicone and saline breast implant devices. • Completion of an 110M sf cleanroom manufacturing facility, transfer and revalidation of all operations from the existing California location. Built an engineering group (5 engineers) responsible for manufacturing support, R&D new product implementation and new process development in a PMA regulated business.
-
-
-
Baxter International Inc.
-
United States
-
Medical Equipment Manufacturing
-
700 & Above Employee
-
Program Manager, Manager, Supervisor and Engineer
-
1986 - 1993
A $200 million division of Baxter International consisting of 10 major domestic and international manufacturing locations. • Manager, Special Machinery / Packaging. Oversee plant capital appropriation budgets for packaging and automation. Annual spending exceeds $1 million and created $750 thousand of annual cost improvements. • Program Manager, Restructuring. Managed the orderly transfers of a $30 million scrub and biopsy tray production line, twelve latex glove-packaging lines and… Show more A $200 million division of Baxter International consisting of 10 major domestic and international manufacturing locations. • Manager, Special Machinery / Packaging. Oversee plant capital appropriation budgets for packaging and automation. Annual spending exceeds $1 million and created $750 thousand of annual cost improvements. • Program Manager, Restructuring. Managed the orderly transfers of a $30 million scrub and biopsy tray production line, twelve latex glove-packaging lines and a $35 million specialty procedural tray line to a new facility in Kingstree, South Carolina. • Program Manager, Malaysia Surgeon’s Glove Program, (Penang, Malaysia). Managed $54 million budget and a team of ten engineers and 12 on-site contractors responsible for general plant construction, glove dipping and packaging equipment design and start-up, latex compounding and wastewater treatment. • Project Engineer/Supervisor, Special Machinery. Designed, constructed and installed two $3 million glove dip lines. Saved $1.2 million through an innovative manufacturing process redesign. Show less
-
-
-
-
Areas of Interest & Expertise
-
1979 - 1980
A Manufacturing and Engineering executive with over 20 years experience in both the medical device and pharmaceutical industries. Vice President (VP), Director, Operations, Manufacturing, Engineering, Project Managment. Classically trained in 4 fortune 100 companies. Major domestic and international management successes including new factory design and construction (Penang, Malaysia), new product developments, expansions, relocations, start-ups and turn-arounds. Cross-cultural communicator… Show more A Manufacturing and Engineering executive with over 20 years experience in both the medical device and pharmaceutical industries. Vice President (VP), Director, Operations, Manufacturing, Engineering, Project Managment. Classically trained in 4 fortune 100 companies. Major domestic and international management successes including new factory design and construction (Penang, Malaysia), new product developments, expansions, relocations, start-ups and turn-arounds. Cross-cultural communicator with significant Pacific Rim, European, Mexico and Caribbean experience. Engineering management responsibilities in packaging, automation, process, sterilization, manufacturing and maintenance. Extensive manufacturing and business systems experience through involvement with world-class manufacturing and implementation of an integrated manufacturing / supply chain program including LEAN, Six Sigma, MRP, ERP, warehouse, and distribution and manufacturing shop-floor systems. Expertise in new device and drug development, Class I, II, and III medical devices, 510K, PMA, NDA, ISO 9001 certification, CDER and CDRH. Products include IV solutions and sets, pharmaceuticals, immunoassay drug testing systems, medical lasers and ophthalmic diagnostic equipment, less invasive surgical systems, surgical gloves and drapes, breast implants, custom procedure sets, medical adhesives, vitamins, supplements and OTC drugs. Show less
-
-
Education
-
Pepperdine Graziadio Business School
MBA, Business Administration -
University of Virginia
BSME, Mechanical Engineering
Community
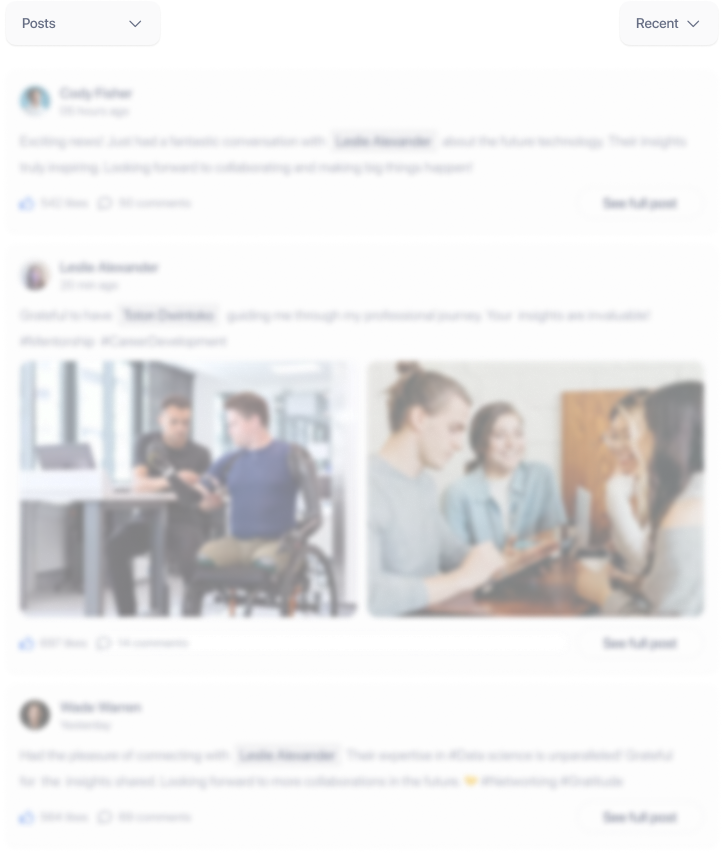