Kevin Schueller
Director of Manufacturing Operations at Henderson Products, Inc.- Claim this Profile
Click to upgrade to our gold package
for the full feature experience.
Topline Score
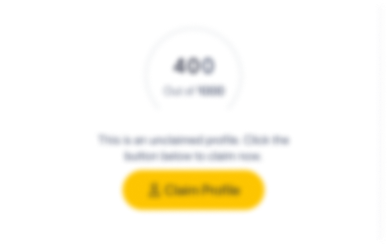
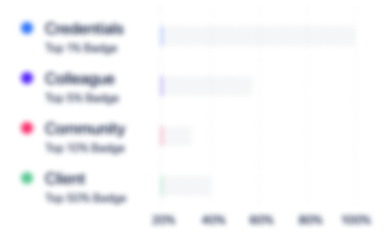
Bio

Jon Reth
Kevin is a very good teacher and leader. Many concepts he passed on to me are what I use on a daily basis in a leadership position. He is a very quick learner and an excellent problem solver.

Nathan J. Etten
I had the great pleasure to work with Kevin on a daily basis while at XL Specialized Trailers. He portrayed professionalism, outstanding leadership abilities and his analytical mindset resonated through in all areas of his work. He was a great asset to me and a crucial part of the improvements made within the organization. I look forward to the opportunity to work with him again.

Jon Reth
Kevin is a very good teacher and leader. Many concepts he passed on to me are what I use on a daily basis in a leadership position. He is a very quick learner and an excellent problem solver.

Nathan J. Etten
I had the great pleasure to work with Kevin on a daily basis while at XL Specialized Trailers. He portrayed professionalism, outstanding leadership abilities and his analytical mindset resonated through in all areas of his work. He was a great asset to me and a crucial part of the improvements made within the organization. I look forward to the opportunity to work with him again.

Jon Reth
Kevin is a very good teacher and leader. Many concepts he passed on to me are what I use on a daily basis in a leadership position. He is a very quick learner and an excellent problem solver.

Nathan J. Etten
I had the great pleasure to work with Kevin on a daily basis while at XL Specialized Trailers. He portrayed professionalism, outstanding leadership abilities and his analytical mindset resonated through in all areas of his work. He was a great asset to me and a crucial part of the improvements made within the organization. I look forward to the opportunity to work with him again.

Jon Reth
Kevin is a very good teacher and leader. Many concepts he passed on to me are what I use on a daily basis in a leadership position. He is a very quick learner and an excellent problem solver.

Nathan J. Etten
I had the great pleasure to work with Kevin on a daily basis while at XL Specialized Trailers. He portrayed professionalism, outstanding leadership abilities and his analytical mindset resonated through in all areas of his work. He was a great asset to me and a crucial part of the improvements made within the organization. I look forward to the opportunity to work with him again.

Credentials
-
Certified Manufacturing Technologist
SMEDec, 2014- Oct, 2024
Experience
-
Henderson Products, Inc.
-
United States
-
Mechanical Or Industrial Engineering
-
1 - 100 Employee
-
Director of Manufacturing Operations
-
Apr 2023 - Present
A more strategic role in positioning Henderson Products for continued manufacturing success and future growth. Still part of the day to day manufacturing environment but focused on development of leadership and He Derain Operating System Development.
-
-
Manufacturing Manager
-
Mar 2020 - Apr 2023
-
-
Continuous Improvement Engineering Manager
-
Apr 2016 - Mar 2020
-
-
-
John Deere
-
Construction
-
1 - 100 Employee
-
Manufacturing Engineer II PDP
-
Feb 2012 - Apr 2016
Work in the new product group for Cab Assembly for the large tractor platform. I am responsible for the Manufacturing Process of our new products. Responsibilities include: Standard Work, OMS's, Tooling and Fixture Purchases, Line Design, Material Presentation, BOM, and work with Quality on PFMEA. Responsible for product launches and Builds for new products. Work with materials group, design, quality and current manufacturing to implement new designs. Work in the new product group for Cab Assembly for the large tractor platform. I am responsible for the Manufacturing Process of our new products. Responsibilities include: Standard Work, OMS's, Tooling and Fixture Purchases, Line Design, Material Presentation, BOM, and work with Quality on PFMEA. Responsible for product launches and Builds for new products. Work with materials group, design, quality and current manufacturing to implement new designs.
-
-
-
XL Specialized Trailers
-
United States
-
Transportation/Trucking/Railroad
-
1 - 100 Employee
-
QUALITY SYSYEMS MANAGER
-
Jan 2009 - Feb 2012
Oversee facilities quality system. Became first Quality Manager in organizations history. Developed quality standards - document, train and enforce based on internal and industrial standards. Implemented Standard Operating Procedures based on needs of individual areas. Tracked and maintained quality paretos - training employees on top issues. Worked with Design Engineering to develop standards parts to help eliminate extra parts and extra tooling. Assist in the launching of new products to… Show more Oversee facilities quality system. Became first Quality Manager in organizations history. Developed quality standards - document, train and enforce based on internal and industrial standards. Implemented Standard Operating Procedures based on needs of individual areas. Tracked and maintained quality paretos - training employees on top issues. Worked with Design Engineering to develop standards parts to help eliminate extra parts and extra tooling. Assist in the launching of new products to ensure quality. Key Accomplishments: Tracked and developed key quality metrics - FPY, Frequency, and Customer Complaints Developed closed loop quality system - External and Internal issues were tracked to determine root cause Developed quality system - document, track and train Reduce Quality issues by 15% Built quality staff - ISO 9000 and Six Sigma Experience XL Specialized Trailers
-
-
CONTINUOUS IMPROVEMENT MANAGER (Lean Leader)
-
Jan 2009 - Feb 2012
Oversee entire plants lean transformation efforts. Instrumental in launching 5S program with completion of entire plant scheduled for 2011. Responsible to flow improvements with focusing on efficiency gain, quality improvements, inventory reduction or cost savings. Lead trainer of facility on Lean Manufacturing Concepts. Leader of all Kaizen and Lean Initiative Events. Key Accomplishments: Generated Access databases to streamline maintenance requests and time off requests Leader of… Show more Oversee entire plants lean transformation efforts. Instrumental in launching 5S program with completion of entire plant scheduled for 2011. Responsible to flow improvements with focusing on efficiency gain, quality improvements, inventory reduction or cost savings. Lead trainer of facility on Lean Manufacturing Concepts. Leader of all Kaizen and Lean Initiative Events. Key Accomplishments: Generated Access databases to streamline maintenance requests and time off requests Leader of 30+ events in 2 years focusing on efficiency gain, quality improvements, inventory reduction, cost savings or standard work development Complete facility layout change focusing on flow improvement and reduction of inventory Developed JIT delivery of raw materials Implemented visual management - Production Control Boards, Heijunk Boards and Andon System Reduction in inventory - Reduce obsolete inventory by $50,000 XL Specialized Trailers
-
-
FINAL PROCESS MANAGER
-
Jul 2010 - Dec 2011
Supervisor of 15 employees, focusing on on-time delivery, efficiency and customer satisfaction. Developed standard work and production control boards to manage employees. Crossed trained employees to improve through put by 100k a week. Created production schedule to maximize invoicing. Key Accomplishments: Improved efficiency from 45% to 115% in 2 months by rebalancing work flow and proper staffing Developed quality standards and regulations based on DOT standards Trained… Show more Supervisor of 15 employees, focusing on on-time delivery, efficiency and customer satisfaction. Developed standard work and production control boards to manage employees. Crossed trained employees to improve through put by 100k a week. Created production schedule to maximize invoicing. Key Accomplishments: Improved efficiency from 45% to 115% in 2 months by rebalancing work flow and proper staffing Developed quality standards and regulations based on DOT standards Trained predecessor on lean methods and quality systems Increased revenue/hour worked by 15%
-
-
FABRICATION SUPERVISOR
-
Dec 2009 - Sep 2010
Supervisor of 18 employees, focusing on on-time delivery, efficiency, and quality of parts. Developed and improved methods of scheduling department - focusing on reduction of WIP, inventory turns, and efficiency gains. Created a cross function department for better utilization. Key Accomplishments: Improved Tracking of Efficiency - Improved for 65% to 110% in 3 months Developed Flex Metrics to better staff department Reduced WIP through department from 8 trailers to 4
-
-
-
Terex Corporation
-
United States
-
Machinery Manufacturing
-
700 & Above Employee
-
QUALITY ENGINEER
-
May 2008 - Dec 2008
Documentation and implementation of product improvements. Liaison between Engineering and Production for print updates, BOM changes, and product improvements. Supervisor of 3 quality inspectors. Responsible for proper RGA documentation and closed loop quality system. Internal ISO 9000 auditor. Key Accomplishments: Established quality standards Proper documentation for standard work, engineering changes, and purchasing changes for product line. Documentation and implementation of product improvements. Liaison between Engineering and Production for print updates, BOM changes, and product improvements. Supervisor of 3 quality inspectors. Responsible for proper RGA documentation and closed loop quality system. Internal ISO 9000 auditor. Key Accomplishments: Established quality standards Proper documentation for standard work, engineering changes, and purchasing changes for product line.
-
-
-
Allsteel
-
United States
-
Furniture and Home Furnishings Manufacturing
-
300 - 400 Employee
-
FLOW IMPROVEMENT ENGINEER
-
Jan 2008 - May 2008
Worked in multiple facilities working on information to production flow. Responsible for developing and implementing standard scheduling database throughout facility. Part of cross functional lean team to align goals and improvements with company goals. Key Accomplishments: Developed standard scheduling database Reduced scheduling families by 45%
-
-
INDUSTRIAL/QUALITY/MANUFACTURING ENGINEER
-
Apr 2006 - Jan 2008
Engineer for a specific product line, focusing on: standard costing, efficiency improvements, BOM updates, completing cost initiatives, flow/process improvements and quality monitoring. Responsible for new production launches - implementing tooling, BOM and quality checks. Participate and lead RCI events using spaghetti diagrams, time observation forms, tact time, standard work, cycle time bar chart and fish bone diagrams. Part of team focusing on margin improvement of products. Key… Show more Engineer for a specific product line, focusing on: standard costing, efficiency improvements, BOM updates, completing cost initiatives, flow/process improvements and quality monitoring. Responsible for new production launches - implementing tooling, BOM and quality checks. Participate and lead RCI events using spaghetti diagrams, time observation forms, tact time, standard work, cycle time bar chart and fish bone diagrams. Part of team focusing on margin improvement of products. Key Accomplishments: Completing cost initiatives - saved $750k annually; Completed new product launch as scheduled with no major issues Reduced customer complaints by 50% Improved product margin by 40%
-
-
-
HNI Corp
-
Mexico
-
Furniture
-
1 - 100 Employee
-
LEAN PROCESS ENGINEER
-
Jan 2006 - Apr 2006
Key Accomplishments: Developed value stream mapping training used by entire corporation Researched and document Best Practices of facilities within HNI Key Accomplishments: Developed value stream mapping training used by entire corporation Researched and document Best Practices of facilities within HNI
-
-
Education
-
Iowa State University
BS, Industrial Technology; Manufacturing
Community
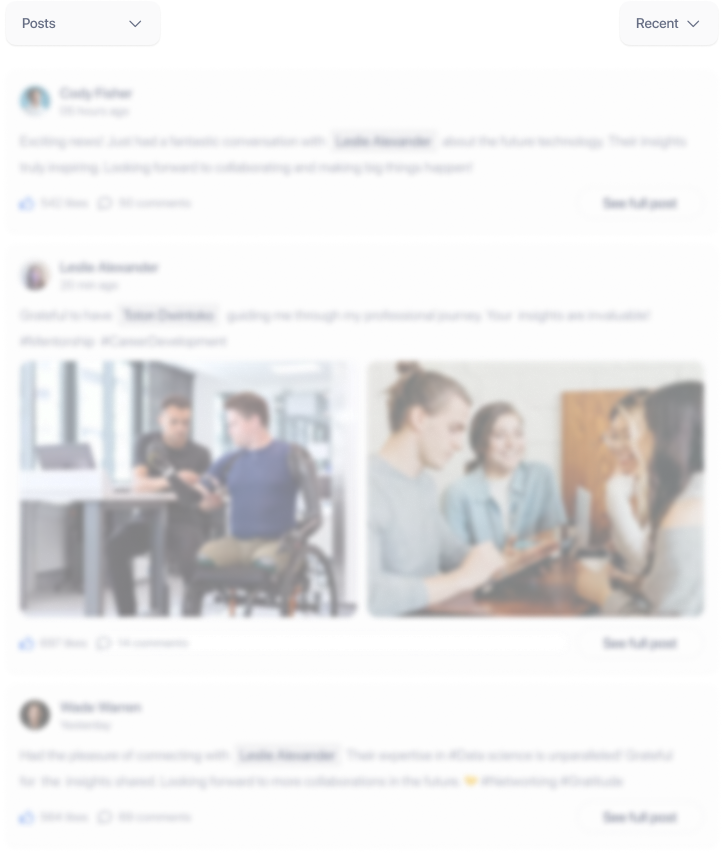