Kev Pye
Group Quailty Manager at Oxylitre Holdings Ltd- Claim this Profile
Click to upgrade to our gold package
for the full feature experience.
Topline Score
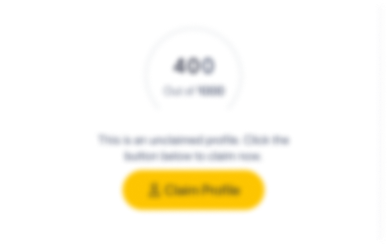
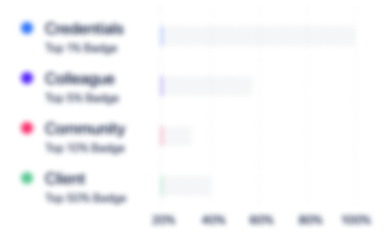
Bio

Dean Lambert
Kevin is a thoroughly professional Manager whom is a pleasure to work with, his can do attitude and attention to detail would benefit any team.

Dean Lambert
Kevin is a thoroughly professional Manager whom is a pleasure to work with, his can do attitude and attention to detail would benefit any team.

Dean Lambert
Kevin is a thoroughly professional Manager whom is a pleasure to work with, his can do attitude and attention to detail would benefit any team.

Dean Lambert
Kevin is a thoroughly professional Manager whom is a pleasure to work with, his can do attitude and attention to detail would benefit any team.
0
/5.0 / Based on 0 ratingsFilter reviews by:
Credentials
-
Operations management Diploma
Training TaleMay, 2022- Sep, 2024 -
Business Management Diploma
Oxford Home Study CollegeDec, 2020- Sep, 2024 -
ISO 13485 lead Auditor
The Knowledge AcademyNov, 2020- Sep, 2024 -
Lone Working And Violence At Work
Commodious TrainingNov, 2020- Sep, 2024 -
ISO 45001:2018 Occupational Health & Safety Management systems
TheKnights of safetyOct, 2020- Sep, 2024 -
ISO 9001:2015 Lead auditor
Udemy AcademyJun, 2020- Sep, 2024 -
IOSH Managing safely
IOSH Merseyside BranchMay, 2014- Sep, 2024
Experience
-
-
Group Quailty Manager
-
Dec 2019 - Present
Implement and define any new requirements into the Quality Manual and/or Quality procedures specified by the European Directives or Regulatory standards. Assist the external Notified body during the the annual Quality assessment and to rectify or implement any requirements made from the results.Implement any modifications to the design of medical products through the Technical department which have been initiated by any new legislation and requirements set by the European Directives and/or the Regulatory standards Assist the Technical department in the design of any new product advising on product legislation and conformity requirements.Implementing and maintaining all product Technical files which consist of a summary technical document, declaration to the European Directives, design and other technical specifications and information. Produce and maintain IFU's and service manuals for all product ranges, that include the safety requirements and procedures.Maintaining the operation of the complaints function which involves liaisons with customers directly and resolving any complaints recieved.organise and lecture training courses for customers who wish to carry out their own maintenance and service programmes.Implementing Health and Safety procedures.
-
-
-
Vivatinell
-
United Kingdom
-
Manufacturing
-
1 - 100 Employee
-
Engineering and Quality Manager
-
Jan 2019 - Nov 2019
-
-
-
ELIS
-
France
-
Facilities Services
-
700 & Above Employee
-
Shift production manager
-
May 2018 - Jan 2019
Ensure a safe working environment with zero recordable injuries in compliance with internal policies and external legislation and efficient operation of the manufacturing shift.Lead safety huddles, participate in safety meetings and enforce plant safety rules. Participate on safety audits.Ensure that SOP's are embedded and followed within the Operations area.To lead and support the shift supervisors to ensure the operational excellence is embedded.Ensure resources and personnel are available and allocated to meet operational demand.Ensure that KPI's are met and exceeded through high levels of plan adherence.Responsible for performance metrics (OEE, Throughput etc)Management of on-shift performances, absence, disciplinary and incidents
-
-
-
-
Group leader
-
Oct 2014 - May 2018
Ensure delivery of all agreed operating plansto achieve financial results, satisfying both internal and external customers.Develop a culture of continuos improvement and deliver performance improvements through increasing productivity, reducing costs, identifying and eliminating all forms of waste.Maximise equipment efficency for output whilst minimising scrap and waste - OEE.Ensuring right first time quality, reducing scrap and completing root cause analysis to ensure repeat failures are removed.Working closely with the maintenance department to maintain machinery and house keeping levels to a high standard of cleanliness and operational reliability, ensuring that all preventative maintenance tasks are identified and executed.Investigating all customer complaints, ensuring that the root cause is identified and actions are tracked and completed to stop any re-occurrence.Monitoring and managing and consumables item spend off all team members within budget constraints.Daily review issues highlighted as a means to minimise wastage and cost.Delivery of core briefing and meeting frameworks.Liase with planning..
-
-
-
Flextex Ltd
-
United Kingdom
-
Plastics Manufacturing
-
1 - 100 Employee
-
Operations manager
-
Oct 2013 - Aug 2014
My current responsibilities include: Health and SafetySystems, Safety inspections and reports, House keeping inspection and reports, Training, Risk assessments and accident reporting, Facilities management, maintenance etc. Plant and MachineryStandard Operating Procedures, Stand machine settings, Parts and spares management, Training specifications or modules per machine, Routine maintenance plan - develop and execution. Training and DevelopmentDevelop training plan for workshop and individual operators, Develop training modules (machine specific), FLT`s, 1st aid and firefighting Performance ManagementImplement annual appraisals, Agree and manage targets for all workers, KPI reporting, Cost reduction program OperationsEnsure robust systems in place for stock management, Oversee all breakdowns / repairs to machines, Structure plan to business needs ManagementWeekly brief to include KPI`s, Sickness and absence, Production totals, Monthly management meeting, Develop longer term operational plan, aligned with company strategy
-
-
-
LINPAC Packaging
-
United Kingdom
-
Packaging & Containers
-
200 - 300 Employee
-
Senior operational teamleader
-
Dec 1999 - Sep 2013
Key responsibilites:Manage Health, Safety, Hygiene & Environment (HSHE) issues for the cell during the shift to ensure a zero accident mentality.Production to plan (Quality, Cost, Delivery) to meet cell stratagey.Ensure effective shift handovers by team members.Develop good communication, team spirit and commitment within the team.Drive LPOS development within the team to ensure effective problem solving tools are utilised.Use pareto analysis to identify the top 3 areas for improvement and drive to close out.Achieve business and departmental objectives by best use of resource hour on hour.Manage the asset care to plan.Identify 100 year fixes for operational problems using the appropriate problem solving approach.Identification and reduction of all waste.Management of on-shift performances, disciplinary, resource and incidents.Attend and present cell daily review and other relevant meetings.Process appropriate transactions within local IT systems.Liaison with other functions, eg planning sales, accounts, asset care, logistics and HR.Team development and succession planning.Engage in bottom up improvement.
-
-
Education
-
Rainford high school
Community
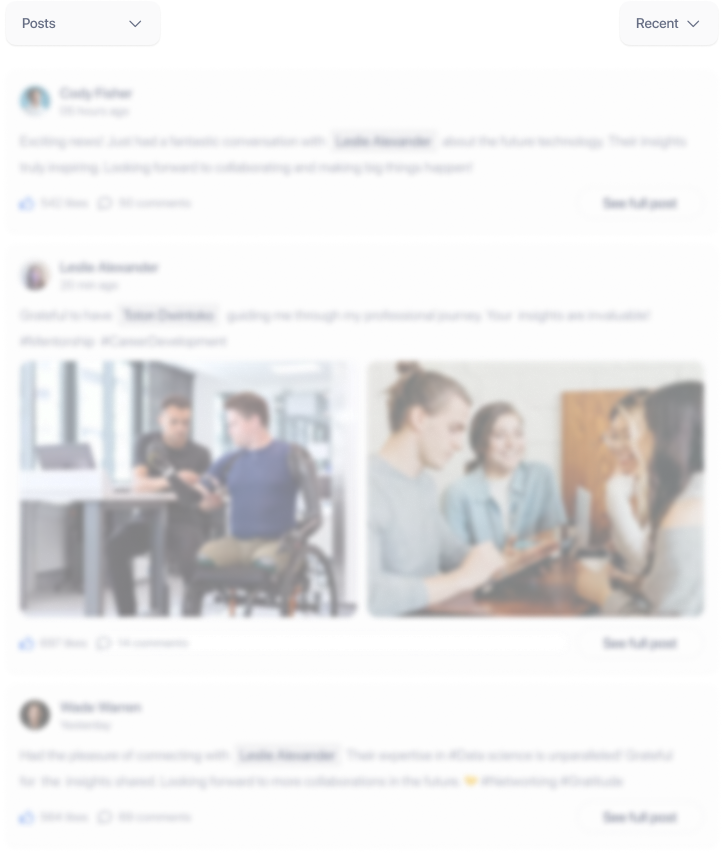