Kestutis Markulevicius
Warehouse Supervisor at TRT Lighting Limited- Claim this Profile
Click to upgrade to our gold package
for the full feature experience.
Topline Score
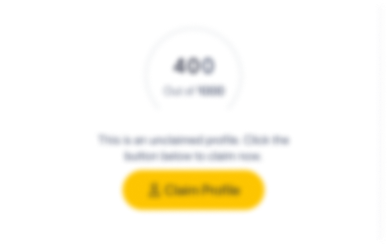
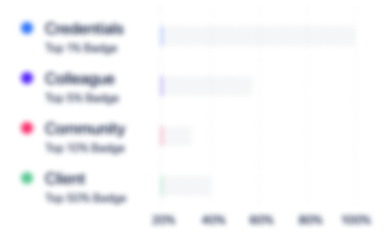
Bio


Experience
-
TRT Lighting Limited
-
United Kingdom
-
Appliances, Electrical, and Electronics Manufacturing
-
1 - 100 Employee
-
Warehouse Supervisor
-
Sep 2020 - Present
-
-
-
Helander Precision Engineering
-
United Kingdom
-
Aviation and Aerospace Component Manufacturing
-
1 - 100 Employee
-
Warehouse Operative
-
Jun 2019 - Aug 2020
-
-
-
Reliance Worldwide Corporation
-
United States
-
Wholesale Building Materials
-
400 - 500 Employee
-
Warehouse Manager
-
Mar 2014 - Dec 2018
The company continued growing almost 30% year-on-year within the UK marketand the staff numbers kept increasing. I was promoted to the position of awarehouse manager, as that better represented my increased responsibilities andstaff count. Existing responsibilities include:*Managing a team of six people on day-to-day basis to ensure smoothwarehousing processes*Working extremely closely with the production team to ensure overalloperational efficiencies*Carrying out various long and short-term projects in conjunction with theoperations and production managers*Worked alongside the internal sales and operations directors to increase OTIF performance from 60% to 95% on average
-
-
Warehouse Supervisor
-
Feb 2012 - Mar 2014
Due to the exponential growth of Reliance Worldwide Corporation, the position of awarehouse supervisor opened. I felt that it would be a very different challengemoving away from production into warehousing and saw a lot of opportunity forimprovement and growth:*Within the first three months optimized the warehouse layout and stockconsolidation to create 20% additional pallet spaces without decreasing stock holding*Reworked the goods inwards processes to ensure better quality control and faster turnover of stock. *Within the first year worked extensively withthe quality management team to ensure that over 80% of all SKUs coming in through the door get inspected, which is about 60% increase since June 2012.*Within the first two years assembled an extremely cohesive and efficientwarehousing team, majority of which has been working with me since late 2012*Managed to keep down staff numbers, hiring only two new extra people since 2012 as the company grew by around 40% revenue year-on-year
-
-
Production Planner
-
Jan 2010 - Feb 2012
As career progression in Lithuania was limited, I decided to take Reliance’s offer to come back and work in the United Kingdom. Due to the vast amount of experience I acquired in Lithuania managing a manufacturing facility, the company felt I was most fitted for the role of a production planner.*Managed a staff of 16 people alongside the production supervisor*Carried out all production related activities within SAP. Did daily MRP runs, raised production orders,monitored stock positions*Worked closely with the internal sales and warehouse departments, ensuring that all customer requirements were met on time*Ensured adequate quality assembly work was carried out, compiled with various ISO standards
-
-
-
Terra Animalis
-
Zapyskis Kaunas
-
Production Manager
-
Aug 2007 - Dec 2009
Due to the background I had as a quality inspector in an international company and strong understanding of the English language, I was hired for a position of the production manager in the biggest animal food manufacturer in Lithuania. During my time there I went on various management and production courses to learn some of the most popular business operations philosophies. *Managed a staff of over 30 people. *Maintained close relationships with customers and suppliers *Worked on developing new products in accordance to Terra Animalis’ manufacturing capabilities *Optimized production efficiencies within the manufacturing floor *Liaised with other senior managers to communicate the upcoming landscape of manufacturing, forecast, and anything related to the production output
-
-
-
Reliance Worldwide Corporation
-
United States
-
Wholesale Building Materials
-
400 - 500 Employee
-
Quality Inspector
-
Jul 2005 - Jul 2007
After working in the company as an assembler for half a year, I was offered the position of a quality inspector and did not hesitate to take the opportunity. The most important skill I learned as part of this role is not the ISO standards or different inspection methods, but rather the understanding of how every cog in the business ties together to achieve the end result. *Liaised with customers and vendors to rectify various pre and post-production issues *Worked with every department within the company to ensure satisfactory communication both externally and internally *Worked closely with the production team to ensure everyone is adhering to quality expectations presented by the customers
-
-
Education
-
Aleksandro Stulginskio University, Kaunas (Lithuania)
BA in Water Engineering (Incomplete, 3 semesters), Structural Engineering -
Ezerelis middle/high school, Kaunas (Lithuania)
High school diploma, High school diploma
Community
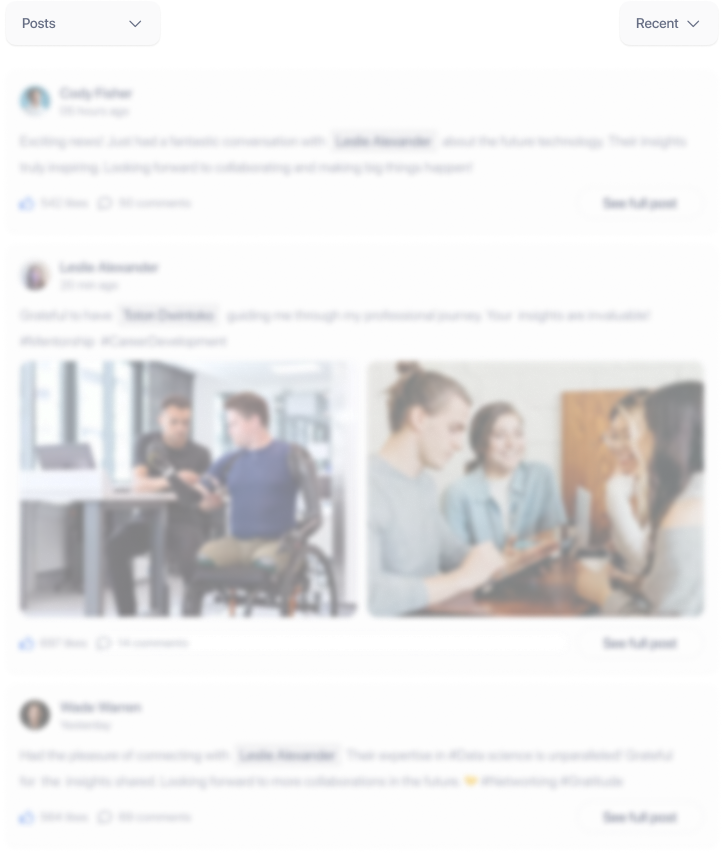