Ken Perino
Vice President of Quality at Supira Medical- Claim this Profile
Click to upgrade to our gold package
for the full feature experience.
Topline Score
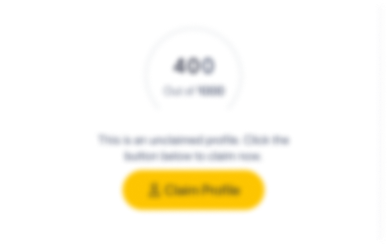
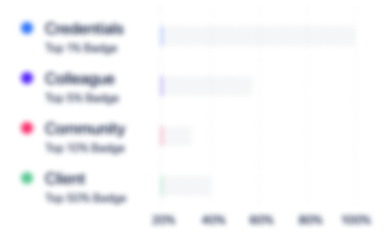
Bio

Steve Baker
Ken started in Quality and then was asked to take on increasing responsibility for preparing medical device Regulatory submissions. He worked diligently and maintained his sense of humor even under pressure. As an R&D engineer I appreciate Ken’s willingness and ability to suggest multiple alternative approaches to reaching a goal. Ken’s key work helped us get regulatory clearance quickly.

Steve Baker
Ken started in Quality and then was asked to take on increasing responsibility for preparing medical device Regulatory submissions. He worked diligently and maintained his sense of humor even under pressure. As an R&D engineer I appreciate Ken’s willingness and ability to suggest multiple alternative approaches to reaching a goal. Ken’s key work helped us get regulatory clearance quickly.

Steve Baker
Ken started in Quality and then was asked to take on increasing responsibility for preparing medical device Regulatory submissions. He worked diligently and maintained his sense of humor even under pressure. As an R&D engineer I appreciate Ken’s willingness and ability to suggest multiple alternative approaches to reaching a goal. Ken’s key work helped us get regulatory clearance quickly.

Steve Baker
Ken started in Quality and then was asked to take on increasing responsibility for preparing medical device Regulatory submissions. He worked diligently and maintained his sense of humor even under pressure. As an R&D engineer I appreciate Ken’s willingness and ability to suggest multiple alternative approaches to reaching a goal. Ken’s key work helped us get regulatory clearance quickly.

Credentials
-
ISO 13485:2003 Certified Lead Auditor
BSI
Experience
-
Supira Medical
-
United States
-
Medical Equipment Manufacturing
-
1 - 100 Employee
-
Vice President of Quality
-
Nov 2022 - Present
-
-
-
Rakuten Medical
-
United States
-
Biotechnology
-
1 - 100 Employee
-
Senior Director Global Quality Systems
-
Sep 2019 - Nov 2022
Responsible for implementing and managing the Global Quality System for the company, including all Quality Systems elements to meet FDA 21 CFRs, Combination Product regulation, ISO 13485:2016, Japan and Taiwan regulations. • Hired and lead personnel to build Quality organization in support of company objectives and to meet regulations. • Envisioned, implemented, and maintain Quality System (procedures and practices) to meet Global regulations • Budgeted, selected, implemented, and maintain corporate Electronic Quality Management System (EQMS), automating the majority of quality system elements on a global scale. Implemented & validated on schedule and within budget. • Lead Quality representative on cross functional teams involving Regulatory pathways, R & D and Med Device Design Control activities, CMO partnerships and Post Market Surveillance process
-
-
-
Abbott
-
United States
-
Hospitals and Health Care
-
700 & Above Employee
-
Director Of Quality
-
Jan 2017 - Sep 2019
Spearheaded quality and compliance integration activities of Abbott-acquired St. Jude Medical sites (U.S. and international). Lead site compliance representative for FDA and notified body audits and interactions. Directed due diligence for potential Abbott M&A, reviewing all quality aspects (design, manufacturing, post-market), resulting in successful contract negotiations to bring new product line to Abbott.• Instituted compliance and inspection preparedness programs in Abbott U.S. and international sites. Facilitated FDA and ISO notified body audits, resulting in no FDA 483 and no major notified body audit findings.• Spearheaded quality system simplification and integration activities (policies and procedures) to bring St. Jude Medical sites into compliance with Abbott quality system.
-
-
Senior Director, Quality Assurance, Topera Medical (acquired by Abbott Laboratories in 2015)
-
Dec 2014 - Dec 2017
Oversaw all division quality assurance activities, including overall quality system ownership, complaint management (failure analysis, MDR/Vigilance reporting), CAPA, NCR, production quality (R.I., production line, final test), software QA (V&V), supplier quality, internal & external audits, document control, and employee training. • Budgeted, selected, and facilitated implementation of division electronic quality system, including document control, change management, non-conformance documentations, and employee training.• Led audits with FDA and ISO notified body, resulting in no FDA 483 and no notified body audit findings.• Spearheaded all quality system elements to ensure cGMP and QSR compliance, and ISO certification. • Drove continuous improvement of quality system, processes and product improvements across the organization• Built quality organization (including hiring personnel) to support company objectives.• Streamlined and simplified quality system, reducing non-value-added activities and eliminating redundancy.
-
-
-
-
Sr. Director Quality Assurance and Regulatory Compliance
-
2009 - 2014
As part of Bayer Healthcare (Berkeley CA site), authored and directed quality system compliance efforts for the Kogenate FS product line. Developed and implemented procedures and processes to comply with Combination Product regulations. As part of Pathway Medical, implemented and maintained processes and procedures, ensuring cGMP compliance and ISO certification. Provided quality assurance vision to strategic goals in form of schedules, quality plans, and budgets. Served as corporate compliance officer, ensuring company compliance with all regulations and laws governing medical devices. Provided quality assurance vision and facilitation to simplify manufacturing operations, transforming from batch-mode manufacturing style to demand-flow style, and implementation of state-of-the-art quality assurance techniques. Directed quality assurance and engineering activities, including risk management, design controls, product and process validations, quality planning, document control, supplier quality, CAPA, NCR, internal and external audit process, employee training, SPC, sterilization qualification and validation, test plans and qualification testing, field complaints, failure analysis, MDR & Vigilance reporting, and inspection planning and implementation such as first article, receiving inspection, in-process, and final inspections.
-
-
-
-
Director Regulatory Affairs
-
2008 - 2009
Led strategic planning and implementation of submissions for new and modified company products, including 510(k) U.S. and technical file for CE Mark certification. Created and submitted company’s first technical file, resulting in receipt of CE Mark from notified body, providing product entry into European Union for commercial use. Authored and submitted special 510(k)s, resulting in regulatory clearance of product iterations. Led strategic planning and implementation of submissions for new and modified company products, including 510(k) U.S. and technical file for CE Mark certification. Created and submitted company’s first technical file, resulting in receipt of CE Mark from notified body, providing product entry into European Union for commercial use. Authored and submitted special 510(k)s, resulting in regulatory clearance of product iterations.
-
-
-
EndoGastric Solutions
-
Medical Equipment Manufacturing
-
1 - 100 Employee
-
Director Regulatory Affairs / Quality Assurance
-
2005 - 2008
As the Director of Regulatory Affairs, spearheaded regulatory strategy and all company regulatory filings, including 510(k) and IDE in U.S. and IRB ethics committee approvals for international clinical studies. Oversaw product approvals in all international markets. Created company technical file, resulting in CE Mark and commercial use in EU. Facilitated and aided with clinical trials (protocol design, CRA activities, follow-up, data analysis, and review). Instituted corporate compliance program. Defended compliance program in FDA audit, resulting in zero findings. As the Director of Quality Assurance, developed and implemented quality system, as well as responsibility for all quality assurance functions. Received ISO 13485:2003 certification and CE Mark. Facilitated FDA and notified body audits, resulting in no major findings.
-
-
-
FUJIFILM Sonosite, Inc.
-
United States
-
Medical Equipment Manufacturing
-
700 & Above Employee
-
Director Quality Assurance
-
1999 - 2005
Developed corporate quality system (processes and procedures) to meet ISO and FDA requirements. Completed successful ISO 13485:2003 certification, including CE Mark. Directed operations group to establish manufacturing, including facility layout, equipment purchase, process and procedure development, manufacturing line development, and hiring/training of employees. Developed and led corporate wide quality team chartered with reviewing operating results, cost and quality data, and initiating corrective and preventive actions as necessary. Chaired corporate CAPA system, internal audits, and supplier quality. Facilitated audits with FDA and ISO notified body, resulting in no major findings. - Manager, Product and Supplier Quality, 2002-2003. Implemented supplier management processes, including supplier audit, approval, and performance. Chaired corporate receiving inspection and first-article function. Partnered with manufacturing and test engineering on in-process and final inspection and test implementation. Collaborated with operations in implementing process FMEA, process SPC, and DOE practices. - Operations Manager, 2000-2002. Directed manufacturing engineering, test engineering, supplier quality engineering, and production. Hired and led team to initiate ultrasound system manufacturing, utilizing demand flow and Lean techniques. Completed first builds on time, with successful validation. - Business Systems Program Manager, 1999-2000. Served as program manager for Oracle ERP Business System implementation. Led cross-functional team to implement corporate-wide Oracle business applications, with implementation finished on schedule and on budget. Envisioned, budgeted, and implemented corporate-wide MES system, successfully utilizing electronic systems to integrate regulatory standards into manufacturing process to drive efficiency, compliance, and continuous improvement.
-
-
-
-
Quality Assurance Manager / Manufacturing Manager
-
1997 - 1999
As the Quality Assurance Manager, responsible for supplier quality, receiving inspection, CAPA and internal audit processes. As the Manufacturing Manager responsibilities included first managing the build, test and failure analysis of the company's capital equipment line, and then managing the outsourcing of the line when the company was acquired. As the Quality Assurance Manager, responsible for supplier quality, receiving inspection, CAPA and internal audit processes. As the Manufacturing Manager responsibilities included first managing the build, test and failure analysis of the company's capital equipment line, and then managing the outsourcing of the line when the company was acquired.
-
-
-
-
Senior Quality Engineer
-
1992 - 1997
Responsible for assuring product quality, reliability and QSR compliance for multiple product lines. Responsible for assuring product quality, reliability and QSR compliance for multiple product lines.
-
-
-
AMD
-
United States
-
Semiconductor Manufacturing
-
700 & Above Employee
-
Quality Engineer
-
1988 - 1992
Held positions in Quality Engineering, Industrial/Mfg. Engineering and Operations Management. Held positions in Quality Engineering, Industrial/Mfg. Engineering and Operations Management.
-
-
Education
-
Fresno State University
Bachelor of Science (B.S.), Industrial Engineering -
Diablo Valley College
Associate of Arts and Sciences (AAS), Electronics
Community
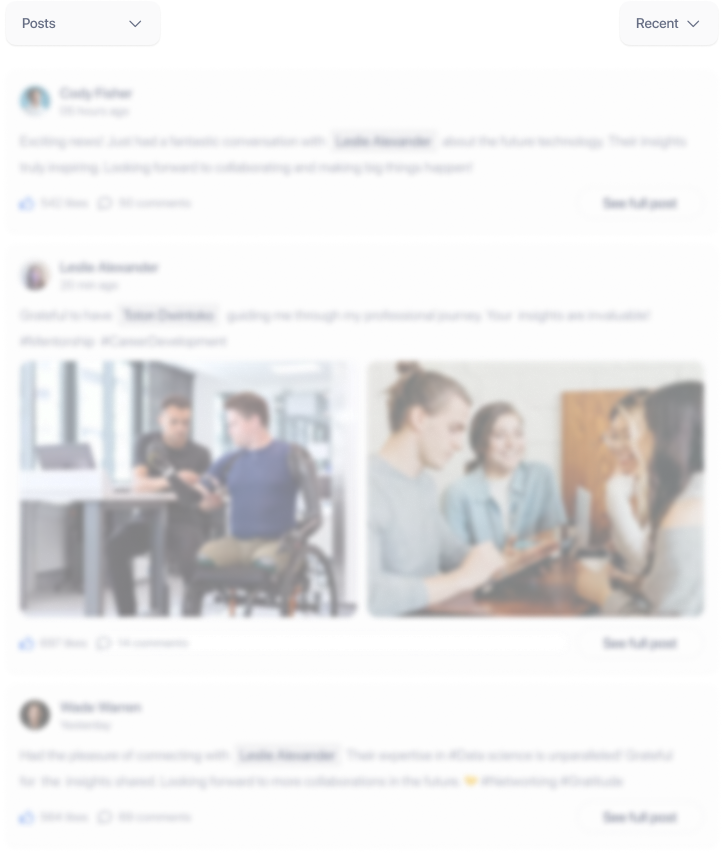