Kenneth Zink
Quality Assurance Manager at Allied Materials & Equipment Co., Inc.- Claim this Profile
Click to upgrade to our gold package
for the full feature experience.
Topline Score
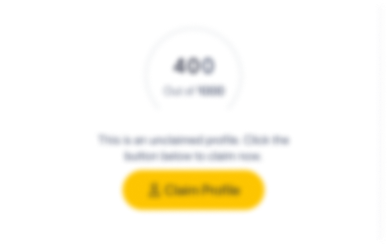
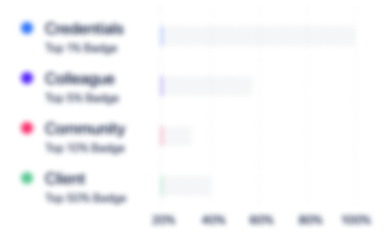
Bio


Experience
-
Allied Materials & Equipment Co., Inc.
-
United States
-
Manufacturing
-
1 - 100 Employee
-
Quality Assurance Manager
-
Mar 2015 - Present
Currently I am the Quality Assurance Manager over entire Factory. My main duties are writing of Quality policy, Training, Audits, Tool Calibration and product inspection. As Quality Assurance Manager, review customers' complaints to determine root cause, corrective actions and follow-up. Monitor trends in complaints for possible problem. Main Objective is to gain ISO 9001/2008 Compliance. Review Production activities and capabilities in light of contract quality requirements. Analyze quality data to detect unsatisfactory trends or weaknesses in the quality inspection system. Identify areas through trend analyzes to determine corrective measures. Under Government Contract for GSA meet frequently with the DPSC Inspectors for complete compliance and authorizations for shipping. To certify QLSM for small arms components. Achieved alternate release procedures for consistently meeting high Quality in the process. Supervise 2 inspectors in the program, conducted training to Read, interpret, and apply technical data, blueprints, engineering drawings, product specifications or technical manuals. Show less
-
-
-
Federal Bureau of Prisons - Career Connections
-
United States
-
Law Enforcement
-
700 & Above Employee
-
Quality Assurance Manager
-
Feb 2009 - Present
Clothing and Textiles-Print Factory-Warehouse and Recycling I was Assigned as The Complex Quality Assurance manager Developed and wrote local quality manual, processes, and procedures in compliance with ISO 9001:2008. USP Leavenworth Quality Management System and maintain ISO 9001:2008 certification. Completed all Documentations for 100% compliance leeds program. 2010 Operational Reviewer in Charge. As Quality Assurance Manager, review customers' complaints to determine root cause, corrective actions and follow-up. Monitor trends in complaints for possible problem.Review Production activities and capabilities in light of contract quality requirements. Analyze quality data to detect unsatisfactory trends or weaknesses in the quality inspection system. Identify areas through trend analyzes to determine corrective measures.Under Government Contract for GSA meet frequently with the DPSC Inspectors for complete compliance and authorizations for shipping.Achieved alternate release procedures for consistently meeting high Quality in the process.Employed 20+ inmate inspectors in the program, conducted training to Read, interpret, and apply technical data, blueprints, engineering drawings, product specifications or technical manuals.Acting Factory Manager, supervising foreman, assigning the foreman to inmate detail assignments, and scheduling production to meet customer's needs.Provide oversight of security screening of inmates leaving the factoryUtilized metal detectors, hand wand, PAT searches, and visual searches Utilize MRP Resource planning to assist in production needs. Participate in monthly financial meetings, analyze data for labor, Quality, Stocking levels. Attend community relations board meeting, On numerous occasions I am called upon to fill the position of Administrative Warden and with this position was tasked with the Operation of the factory Show less
-
-
Complex Quality Assurance Manager
-
Jul 2007 - Jan 2009
Clothing and Textiles-Warehouse-Systems furniture and Furniture Division Raw Lumber. I was Assigned as The Complex Quality Assurance manager Developed and wrote local quality manual, processes, and procedures in compliance with ISO 9001:2008. USP Leavenworth Quality Management System and maintain ISO 9001:2008 certification. Completed all Documentations for 100% compliance leeds program. 2010 Operational Reviewer in Charge. As Quality Assurance Manager, review customers' complaints to determine root cause, corrective actions and follow-up. Monitor trends in complaints for possible problem.Review Production activities and capabilities in light of contract quality requirements. Analyze quality data to detect unsatisfactory trends or weaknesses in the quality inspection system. Identify areas through trend analyzes to determine corrective measures.Under Government Contract for GSA meet frequently with the DPSC Inspectors for complete compliance and authorizations for shipping.Achieved alternate release procedures for consistently meeting high Quality in the process.Employed 40 inmate inspectors in the program, conducted training to Read, interpret, and apply technical data, blueprints, engineering drawings, product specifications or technical manuals.Acting Factory Manager, supervising foreman, assigning the foreman to inmate detail assignments, and scheduling production to meet customer's needs.Provide oversight of security screening of inmates leaving the factoryUtilized metal detectors, hand wand, PAT searches, and visual searches Utilize MRP Resource planning to assist in production needs. Participate in monthly financial meetings, analyze data for labor, Quality, Stocking levels. Attend community relations board meeting, On numerous occasions I am called upon to fill the position of Administrative Warden and with this position was tasked with the Operation of the factory Show less
-
-
Complex Quality Assurance Manager
-
Aug 2005 - Jul 2007
Contractor for ISO 9001-2000 In October of 2006 completed Complex Recertification for ISO with noticed creativity and examples only utilized in the free cooperate world Recognized by Auditors. I initiated Blueprint review engineering change to our current product. Main objective was to develope process approach documents to assure proper work flow and fast transition for new employees Maintained written, verbal, and telephone conversation for the development of the new KD office furniture for the Product Support Center. Completed resolution of approx. 280 Quality notifications and over 180 Returns. I was able reduce the active Notifications from 280 to 18 Quality notifications and 16 returns prior to my move to the Medium institution. I also followed up on damage claims and was able to recover approx. $75,000.00 from two shipping companies. I have drafted procedures to avoid this in the future. Passed information cooperate office to aid in the reduction of damages in the future. Developed process approach for the Furniture Operation. I presented training program to upper management in a Quality Assurance conference in San Diego in Nov. 2005 Created training program that is accredited by the Department of Labor. List of innovations, Developed document controls universal for LOW,MED,CAMP, Quality Management System Upgrades: Developed New Quality Policy, New Quality Measures, New Quality Objectives, New Process-Based Internal Audits, New Comprehensive Process Area Procedures, New Centralized, ISO-Based Document Control System, New Inmate Training Database, New Production Identification Database, New Streamlined Inspection, characteristic Recording Process, New Inmate Training Classes QMS Clerical Personnel Restructuring, New ISO Qualified Inmate Position Instructions, New ISO Qualified Building, Instructions, New ISO Qualified Corrective Action Program, New ISO Qualified Management Analysis, Received Supervisor Of the Quarter, Supervisor Of the Month 2006. Show less
-
-
Industrial Specialist/Quality Assurance Manager
-
Jul 2003 - Jul 2005
Clothing and Textile-Warehouse/Shipping and receiving. Industrial Specialist/Quality Assurance Overseen Operation of Clothing manufacturing. Responsible for the complete restructure of the Quality Assurance Department. Certifying all QA inspectors through a training program. These programs consist of on the job-training, cross training and verbal and written testing. Currently I have 14 certified Inspectors.Resolved all customer complaints that occur within 48 hours with complete customer satisfaction. Role as industrial specialist responsible for Develop training needs, Open communication with all venders, maintain the waiting list for prior and non-prior experienced workers UNICOR and research qualification for New Hires.Developed 9 new products for the Bureau of prisons. I developed Medical lab coats, surgical scrubs, and warm-up jackets. I was responsible for work instructions, raw material requirements and labor calculations to determine cost. The completed project was presented to the Veterans administration in Washington D.C. and was accepted and approved. These items are currently in production today.As the Industrial Specialist I supervised 6 staff members and 30 workers Show less
-
-
Fabric Worker Supervisor
-
Dec 1996 - Jul 2003
As a foreman in the Textile factory at U.S.P. Leavenworth I was responsible for monitoring raw materials I was responsible for the manufacturing of the tool bag line, 1046 inserts, meteorological parachutes, and have also worked as a foreman in the #1, #2, #3 mailbags and the warehouse sorting operations. I supervised approximately 120 Workers. I received numerous special act awards for production and setting finished goods records for mailbag repair. I was Correctional Worker of the year in 1999. Show less
-
-
-
BoP Consultoría
-
Colombia
-
Banking
-
100 - 200 Employee
-
Factory Manager
-
Feb 1990 - Present
From July 31 until October 9th, 2011 I am appointing acting Associate Warden Of Industries and Education. As Factory Manager my duties include but not limited to maintaining rigid quality control specifications as required by DCMA Military contracts, as well as independent customers. My supervision encompasses planning coordinating and direction of all factory activities. I am responsible for technical review and acceptance of contracts for integration into production. I am responsible for maintaining close liaison with program management staff and corporate office. Primary responsibility is maintained production schedules and oversight of all required raw material for completion of finished goods. As the Factory Manager I utilize the centralized automated system (MILLENNIUM) these schedules are updated in SAP which allow me to track production real time. My Supervisory roles include planning, organizing, and reviewing work, administering personnel matters and dealing effectively with union, employees and upper management. My responsibility to my staff include evaluating work performance, identifying training needs, recommendations for promotions, awards and disciplinary actions as well as resolving complaints and grievances. Currently responsible for a multi-million dollar production factory. Main contracts are DCMA, Fort Knox, United States Air Force Academy and West Point. We are manufacturing T-shirts and storage bags. I currently have 5 employees that I am responsible for. Factory Managers duties are extensive and require constant attention to insure a Quality product, on time delivery, cost reduction and green initiatives. I maintain certifications as an ISO Internal Auditor, Lean Six Sigma Yellow belt. I have recently completed Leadership Phase 1 and Phase 2 Leadership Training. In April 2011 was voted Supervisor of the Quarter. Show less
-
-
-
UNICOR Federal Prison Industries
-
United States
-
Law Enforcement
-
1 - 100 Employee
-
Factory Manager
-
Feb 2009 - Dec 2012
Clothing And Textiles-Shipping and Receiving I was Assigned Factory manager Of Clothing and Textiles As Factory Manager my duties were Blueprint specifications as required by DCMA Military contracts, Supervision encompasses planning coordinating and direction of all factory activities from Raw material to Shipping. I was Responsible for technical review and acceptance of contracts Responsible for maintaining close liaison with program management staff and corporate office. Primary responsibility is maintained production schedules and oversight of all required raw material for completion of finished goods. Factory Manager I utilize the centralized automated system MILLENNIUM)to schedule all Current and Future Jobs My Supervisory roles include planning, organizing, and reviewing work, administering personnel matters and dealing effectively with union, employees and upper management, responsibility to my staff include evaluating work performance, identifying training needs, recommendations for promotions, awards and disciplinary actions as well as resolving complaints and grievances. I was Responsible for a multi-million dollar production factory. Contracts included DCMA, Fort Knox; My factory manufactured T-shirts and storage bags. I supervised 5 employees and 120 line workers. As Factory Manager my duties are extensive and require constant attention to insure a Quality product, on time delivery, cost reduction and green initiatives. I maintain certifications as an ISO Internal Auditor, Lean Six Sigma Yellow belt. I have recently completed Leadership Phase 1 and Phase 2 Leadership Training. In April 2011 was voted Supervisor of the Quarter. Completed 10 Quick wins and 2 Lean Six Sigma Project/results of thousands in Savings Show less
-
-
Community
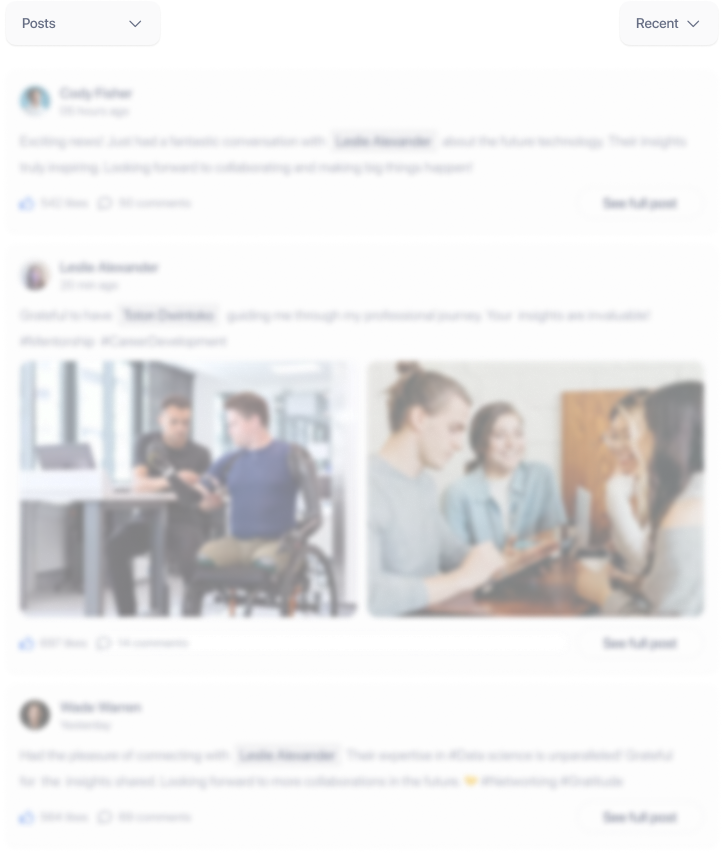