Kenneth Vojtech
Vice President of Operations at Van Asten Painting Inc.- Claim this Profile
Click to upgrade to our gold package
for the full feature experience.
Topline Score
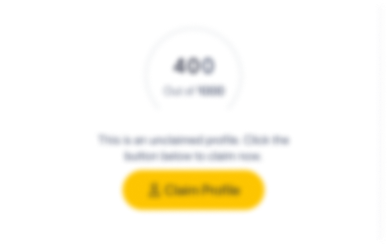
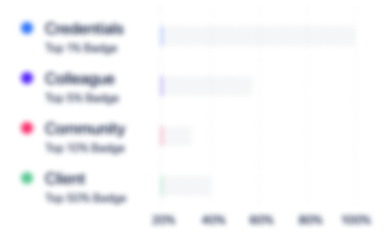
Bio

David Dillinger
Ken is exceptional! He has a sharp mind and keen eye for seeing solutions. Listens intently to the customer to facilitate the right product the first time!

Scott McCranie, MBA
Ken is a true professional and very knowledgeable.

David Dillinger
Ken is exceptional! He has a sharp mind and keen eye for seeing solutions. Listens intently to the customer to facilitate the right product the first time!

Scott McCranie, MBA
Ken is a true professional and very knowledgeable.

David Dillinger
Ken is exceptional! He has a sharp mind and keen eye for seeing solutions. Listens intently to the customer to facilitate the right product the first time!

Scott McCranie, MBA
Ken is a true professional and very knowledgeable.

David Dillinger
Ken is exceptional! He has a sharp mind and keen eye for seeing solutions. Listens intently to the customer to facilitate the right product the first time!

Scott McCranie, MBA
Ken is a true professional and very knowledgeable.

Credentials
-
Certified Coatings Inspector
AMPP CredentialsApr, 2022- Nov, 2024 -
Protective Coatings Inspector Level 2
SSPC: The Society for Protective CoatingsMar, 2018- Nov, 2024 -
Lead Abatement Supervisor DHS Cert# 208126
State of Wisconsin
Experience
-
Van Asten Painting Inc.
-
United States
-
Consumer Services
-
1 - 100 Employee
-
Vice President of Operations
-
Sep 2015 - Present
-
-
Technical Project Manager
-
Oct 2013 - Sep 2015
-
-
-
TD Fischer
-
United States
-
Advertising Services
-
1 - 100 Employee
-
Director of Inventory Control & Purchasing
-
Jul 2013 - Oct 2013
• Review and place purchase orders verbally and electronically for all raw materials or finished goods and outside services • Establish and implement purchasing strategies, policies, and procedures • Collaborate with Plant Management to establish inventory safety stock levels, reorder amounts, and lead times for all raw materials and finished goods • Collaborate with Engineering and Product Management to source new and alternative raw material • Collaborate with Product Management to source new and alternative purchased finished goods • Establish, build, and maintain relationships with all key suppliers • Negotiate pricing, contracts, and payment terms with suppliers • Review and resolve any discrepancies with supplier invoices, grievances, claims, conflicts, product non-conformance or quality issues • Prepare and maintain supplier evaluation forms and Supply Position Risk Assessments • Manage J.I.T and rush sourcing • Provide raw material and finished goods projections to key suppliers to ensure product availability on a timely basis • Evaluate all purchase orders to ensure that order quantities are the most cost effective possible for material and freight costs • Provide Accounting Department with periodic raw material and finished goods material costs to assist in maintaining product costing, and projected raw material and finished goods costs for annual price meetings • Arrange supplier meetings with appropriate TD Fischer Group personnel to review and resolve any problems or issues as needed • Show less
-
-
-
Jacobs
-
United States
-
Business Consulting and Services
-
700 & Above Employee
-
Test & Evaluation Engineer/Project Officer
-
Mar 2012 - Apr 2013
•Repeatedly earned promotion through superior performance and demonstrated ability to quickly learn and master complex concepts to increasingly responsible positions.•Prepare, coordinate, track, disseminate engineering/test communications to include program documentation, briefings, summaries and reports.•Monitor program events to coordinate, plan, and execute events that support testing, training, and experimentation of PM MRAP (FOV) Family of Vehicles.•Serves as a subject matter expert on CS13 (Capability Set) in planning formal test events, experiments, and field exercises in support of PM MRAP needs and requirements.•Risk/Issue Assessment, Risk Management and Risk tracking•Applied Lean Six Sigma and Program Management Institute (PMI) Body of Knowledge (PMBOK) PMP principles where applicable to help ensure efficient execution of program activities.•Able to set deadlines, establish priorities, resolve situations, and complete projects using thorough judgment while in a fast paced working environment. Show less
-
-
Intermediate Systems Administrator
-
Oct 2011 - Mar 2012
• Detailed planning, developing, testing, contracting, producing, providing acquisition logistics support, and disposing of given IT systems and equipment. • Participated in pilot deployments and Process Action Teams (PAT) and Integrated Product Teams (IPT) for PEO CS-CSS Mobile Armor Initiatives.• Risk/Issue Assessment, Risk Management and Risk tracking
-
-
Computer Systems Admin III
-
Jan 2011 - Oct 2011
• Maintained visibility over all of MRAP IT and information assurance duties and served as a primary point of contact for detailed fleet management planning to identify, develop and implement specific goals and objectives related to the modernization and sustainment of MRAP IT systems.• Full authority/responsibility for all PM MRAP Property Accountability and Equipment Management and Maintenance programs. Serves as a point of contact (POC) for property accountability and equipment movement/Issuing issues. Spot checks hand receipt accounts periodically for accuracy and sufficiency and for compliance with instruction, makes field visits to determine proper application and effectiveness of property control, recommends corrective action to be taken on resolution of discrepancies. Maintains document control and ensures that appropriate actions is taken to fix responsibility for Government property which is destroyed, lost, stolen or damaged Determines property book items, and assures all designated property is bar-coded. Show less
-
-
Education
-
Lawrence Technological University
Bachelor of Science (BS), Industrial Management -
Dorsey Business Schools-Roseville
Graduated, Microsoft Certified Systems Engineer Course
Community
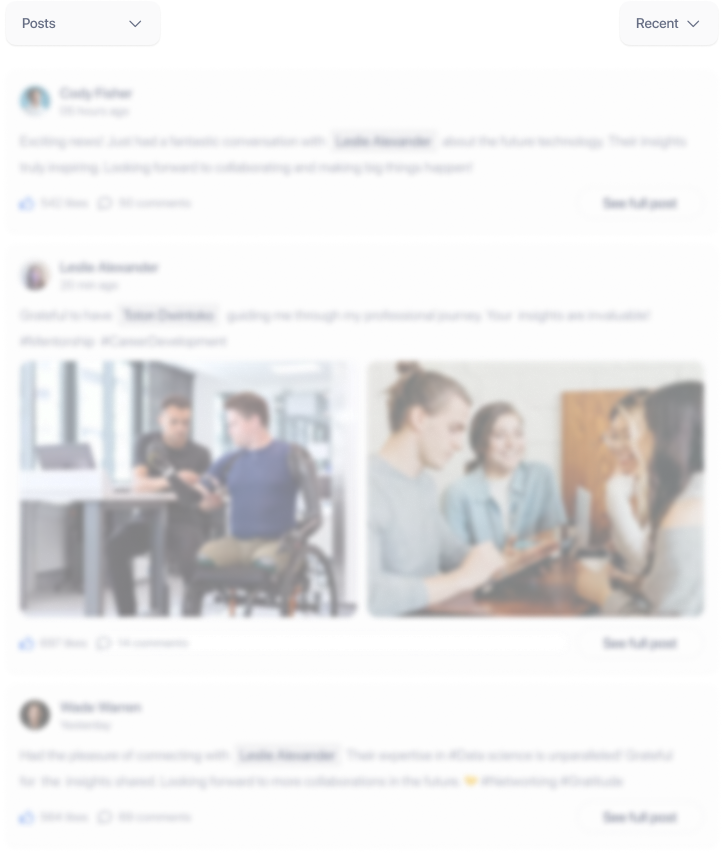