Kenan Gündoğdu
Production Chief at MPS Metal Plastik Sanayi- Claim this Profile
Click to upgrade to our gold package
for the full feature experience.
-
Türkçe Native or bilingual proficiency
-
İngilizce Professional working proficiency
Topline Score
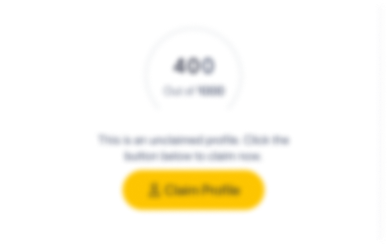
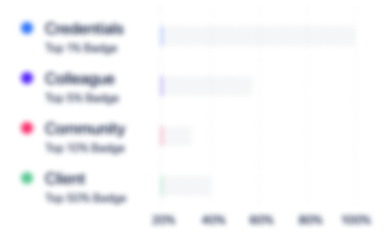
Bio


Credentials
-
ISO 9001:2008 (Internal Auditor Certification),
Mega Teknik DanışmanlıkJul, 2011- Nov, 2024 -
TPM
Kalite Sistem GrubuApr, 2010- Nov, 2024 -
BRC
Moody InternationalFeb, 2009- Nov, 2024
Experience
-
MPS Metal Plastik Sanayi
-
Türkiye
-
Packaging and Containers Manufacturing
-
1 - 100 Employee
-
Production Chief
-
Apr 2015 - Present
-
-
-
Sumer Plastic and Paper Industry Trading Co.
-
Türkiye
-
Plastics Manufacturing
-
1 - 100 Employee
-
Operations Manager
-
May 2014 - Nov 2014
• Responsible for; -Performing process analysis and improvement in different operations - Executing cost cutting and efficiency projects Performing personnel performance evaluations -Decreased logistic cost of company 6% by pallet optimization • Responsible for; -Performing process analysis and improvement in different operations - Executing cost cutting and efficiency projects Performing personnel performance evaluations -Decreased logistic cost of company 6% by pallet optimization
-
-
-
Promotüp A.Ş.
-
İstanbul, Türkiye
-
Operations Manager
-
Jun 2013 - Feb 2014
• Responsible for; -Overall production process of tube making lines -Planning of tube making lines in all aspects from workforce activities to product delivery -All the operations in supply chain management such as stock planning, material management and warehouse management -Defining quality procedures in conjuction with operating staff and setting up & maintaining controls and documentation procedures. (ISO 9001, GMP) -Increased OEE of tube making machines 5% by improving… Show more • Responsible for; -Overall production process of tube making lines -Planning of tube making lines in all aspects from workforce activities to product delivery -All the operations in supply chain management such as stock planning, material management and warehouse management -Defining quality procedures in conjuction with operating staff and setting up & maintaining controls and documentation procedures. (ISO 9001, GMP) -Increased OEE of tube making machines 5% by improving change over time Show less • Responsible for; -Overall production process of tube making lines -Planning of tube making lines in all aspects from workforce activities to product delivery -All the operations in supply chain management such as stock planning, material management and warehouse management -Defining quality procedures in conjuction with operating staff and setting up & maintaining controls and documentation procedures. (ISO 9001, GMP) -Increased OEE of tube making machines 5% by improving… Show more • Responsible for; -Overall production process of tube making lines -Planning of tube making lines in all aspects from workforce activities to product delivery -All the operations in supply chain management such as stock planning, material management and warehouse management -Defining quality procedures in conjuction with operating staff and setting up & maintaining controls and documentation procedures. (ISO 9001, GMP) -Increased OEE of tube making machines 5% by improving change over time Show less
-
-
-
-
Production Chief
-
Sep 2011 - May 2013
Responsible for; -Production process of Pet Extrusion and Slitter line. -Planning of Pet Extrusion and Slitter line in all aspects from workforce activities to product delivery. -Worked on the complete installation process of whole pet extrusion and slitter line including operator trainings, optimizing process conditions, trial production and tests, etc. - Reduced per/kg cost by 7,2% via optimizing RCPs, decreasing scrap ratio, improving raw materials quality before the… Show more Responsible for; -Production process of Pet Extrusion and Slitter line. -Planning of Pet Extrusion and Slitter line in all aspects from workforce activities to product delivery. -Worked on the complete installation process of whole pet extrusion and slitter line including operator trainings, optimizing process conditions, trial production and tests, etc. - Reduced per/kg cost by 7,2% via optimizing RCPs, decreasing scrap ratio, improving raw materials quality before the extrusion process. (Cost analysis project, 2013) -Increased OEE of PET extrusion line 20% by improving availability, performance and quality of Pet line. -Increased OEE of slitter machine 12% by improving availability, performance and quality of slitter machine. -Reporting to plant manager with one direct report (extrusion specialist) and three indirect reports (shift foreman)
-
-
Production Engineer
-
Mar 2009 - Aug 2011
• Responsible for; -Training blue-collar workers about production methods and processes -Running improvement projects using tools like kaizen, 5S, TPM etc -Arranging necessary layout, tools and equipments to enable production people to conduct their work economical, at required quality -Leading autonomous maintenance activities in production lines to improve productivity with TPM. -Participating in machinery investment projects -Preparing and evaluating daily, weekly and… Show more • Responsible for; -Training blue-collar workers about production methods and processes -Running improvement projects using tools like kaizen, 5S, TPM etc -Arranging necessary layout, tools and equipments to enable production people to conduct their work economical, at required quality -Leading autonomous maintenance activities in production lines to improve productivity with TPM. -Participating in machinery investment projects -Preparing and evaluating daily, weekly and monthly OEE, production report and action plan -Tracking monthly and annual production budget -Increased Overall Equipment Efficiency (OEE) in printing line by 2% via one point lessons and 5S improvements - Decreased workforce resource 25% for one of the production lines (thermoforming+printing machine) -Worked on the complete installation process of bag production
-
-
Education
-
Orta Doğu Teknik Üniversitesi / Middle East Technical University
2,15, Food Engineering -
Bayburt Anatolian High School
4,56, Science
Community
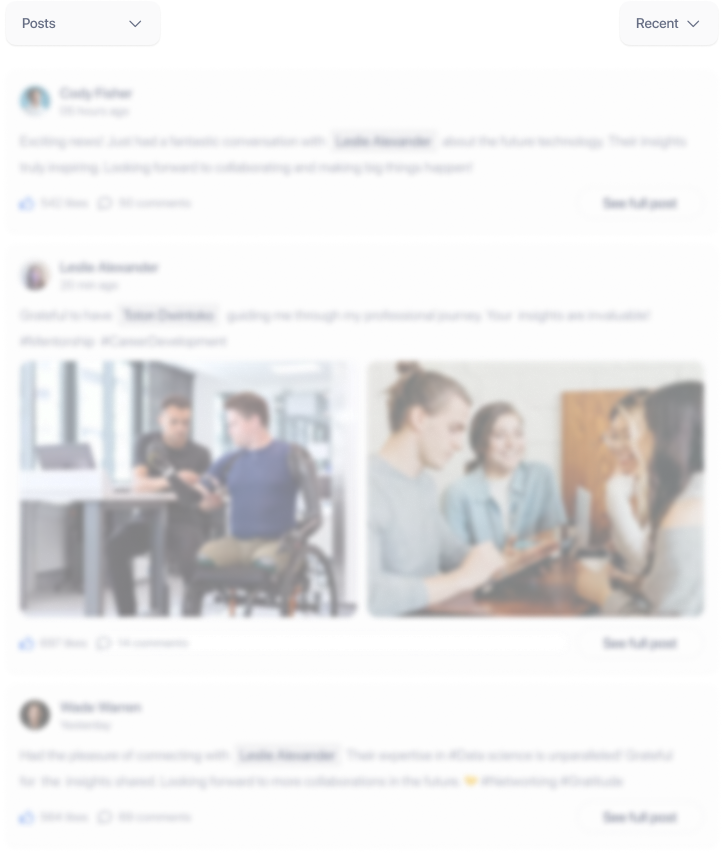