Ken Scott
Associate Director Supplier Quality, Business Process Management at Raytheon Technologies- Claim this Profile
Click to upgrade to our gold package
for the full feature experience.
-
English -
Topline Score
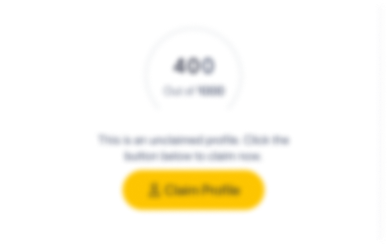
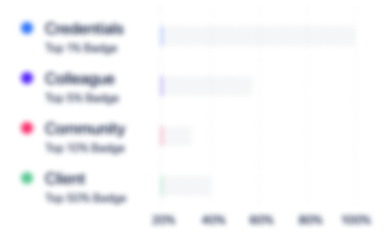
Bio


Credentials
-
Lead Auditor
ASQ
Experience
-
Raytheon Technologies
-
United States
-
Aviation and Aerospace Component Manufacturing
-
700 & Above Employee
-
Associate Director Supplier Quality, Business Process Management
-
Jan 2017 - Present
• Drove strategic global initiatives of lean and continuous process improvements that have led to a 15% increase in process efficiencies. • Partnered with business units and suppliers to drive strategic progressive performance improvements which have led to 20% reduction in risk and an increase by 10% for on-time delivery. • Led analysis and read across of global business unit Corrective Action and Preventative Action (CAPA) Reporting management process which reduced the cost of poor quality (COPQ) by $5M annually. • Supported the global leadership team in support Policy Deployment, Macro Planning, and Lean principles (Production System) through strategic initiatives. • Managed initiatives in the execution of the Supplier Audit Program, PPAP Program, Special Process Compliance, Supplier Corrective Action Board, Defect Reduction, and Development Programs. Reduced COPQ by 10%, and improved error free rating by 50% and on-time delivery by 10%. • Analyzed quality trends and used leading indicators to strategically plan initiatives that minimize potential risks. • Established and facilitate the Corrective Action Board and Management Review processes for the SBU to ensure quality business results are measured, reviewed, and improved in line with QMS requirements. • Established on-going review process to ensure compliance, continuous improvement in results and maturity; internally, suppliers and aftermarket support. Reach-out to Enterprise Quality for support as needed. • Prepared business best practice case studies for Supplier Quality key process advancement and movement toward industry best practices (including Kaizen Events, Training and Lunch and Learn sessions). Show less
-
-
-
Oceaneering
-
United States
-
Oil and Gas
-
700 & Above Employee
-
Program Quality Assurance Manager
-
Sep 2013 - Dec 2016
Defined, developed and implemented the process traveler routers to capture process flow, time allocation, process hold points, verification and validation (FATs) of critical characteristic requirements. Part of corporate team for defining and developing Quality program software (Smartsolve and PLM). Lead the implementation team on capabilities, performance and training personnel. Evaluating training processes and programs utilizing data to determine training needs and requirements. Improving processes leading up to API Q1/ISO certification and monogram licensing. Guiding, facilitating and maintaining API Q1/ISO certification process. Implement and execute compliance programs that ensure adequate management of compliance and reliability related risks. Managing and maintaining the QMS in a manner that complies with QMS requirements, strategic and quality objectives which have led to continual improvement and execution to procedural requirements. Facilitating and performing routine input tools and reports such as Corrective Action and Preventative Action (CAPA) reports, Quality Plans, Nonconformance (NCR) reports, Databooks, Inspection and Test Plans. Collecting and analyzing key performance indicator metrics and collecting and analyzing data required for corporate defined key performance indicators, which includes compiling high quality and accurate inputs from various sources such as NCR/CAPA data, supplier performance data, cost of poor quality (COPQ) data and on-time delivery data. Reviewing Customer Contracts to ensure Quality resources are applied and support design reviews to assure compliance with contract requirements. Managing quality of suppliers’ products and processes through qualifications, process initiatives and audits. Directing and assisting suppliers in developing quality improvement programs and systems. Performing Supplier’s quality rating, on-time delivery, and NCR/SCAPAs. Show less
-
-
-
Parsons Corporation
-
United States
-
Professional Services
-
700 & Above Employee
-
Quality Manager
-
Nov 2011 - Sep 2013
Responsible for developing and managing high quality and cost-effective Quality Management System. Responsible for provide the resources, knowledge, and culture to carry out the Quality responsibilities through all groups and suppliers. Led the undertaking of internal and external audits of design, manufacturing, construction and Contractors of the program to evaluate conformance and effectiveness to established procedures. Defined, established and evaluated requirements for potential EPIC contractors such as RFPs / RFIs / RFQs Provided leadership for Quality support activities for project to ensure that products and services provided meet customer and Parsons’ requirements. Provided leadership for development and implementation of Quality Control Program, procedures, resource allocation, and training. Developed, established and evaluated the adequacy of specific programs used to train and test inspection, examination, and testing personnel. Created and implemented the program Quality and Inspection and Test Plans for use across the program organization. Evaluated the quality of planning, design and construction activities accomplished by engineering and contractors to assure the work is in conformance with the contract requirements and industry standards. Defined, developed and managed Risks Assessments Ensured compliance with API Q1/ISO 9001 standards. Show less
-
-
-
Integrated Power Services
-
United States
-
Industrial Machinery Manufacturing
-
400 - 500 Employee
-
Quality Assurance Manager
-
Aug 2009 - Nov 2011
Developed and managed the Quality System compliance, developed and documented corrective action plans, contacted and interacted with suppliers pertaining to quality issues. Interfaced with customers to resolve product issues and implementing product and process improvements that address the customers’ concerns and or issues. Defined, developed and implemented 10CFR50 Appendix B/NQA-1 QMS to certification for two division. Lead corporate team in the implementation Quality program software (Compliant Pro) for 17 division on capabilities, performance and training. Managed overall quality management policy & procedures, as well as department objectives including implementation. Defined, developed and implemented strategic performance indicators (Quality, Responsiveness and Relationships) to senior management against an agreed set of standard metrics/reports. Maintained uniform plant quality management systems; ensuring customer satisfaction and supervise employees. Developed, recommended, and implemented inspection/analysis techniques, quality & process control procedures and audit plans to ensure specifications & standards are met. Assisted in diagnosing manufacturing/quality problems and in establishing corrective action programs for defect and failure prevention. Work across functions to establish quality specifications/standards for raw materials as well as development of specification/testing requirements. Manage suppliers to continually improve quality/cost & lead time/inventory. Ensured compliance with 10CFR50 Appendix B, NUPIC and NQA-1 standards. Show less
-
-
-
ADC Telecommunications
-
Telecommunications
-
1 - 100 Employee
-
Quality Manager
-
2008 - 2009
-
-
-
Westinghouse Electric Company
-
Nuclear Electric Power Generation
-
700 & Above Employee
-
Sr. Supplier Quality Engineer
-
2004 - 2007
-
-
Education
-
Prairie View A&M University
Master of Business Administration (M.B.A.), Executive Master of Business Administration -
Sam Houston State University
Master of Science - MS, Project Management -
Southern University and A&M College- Baton Rouge
BS, Mathematics
Community
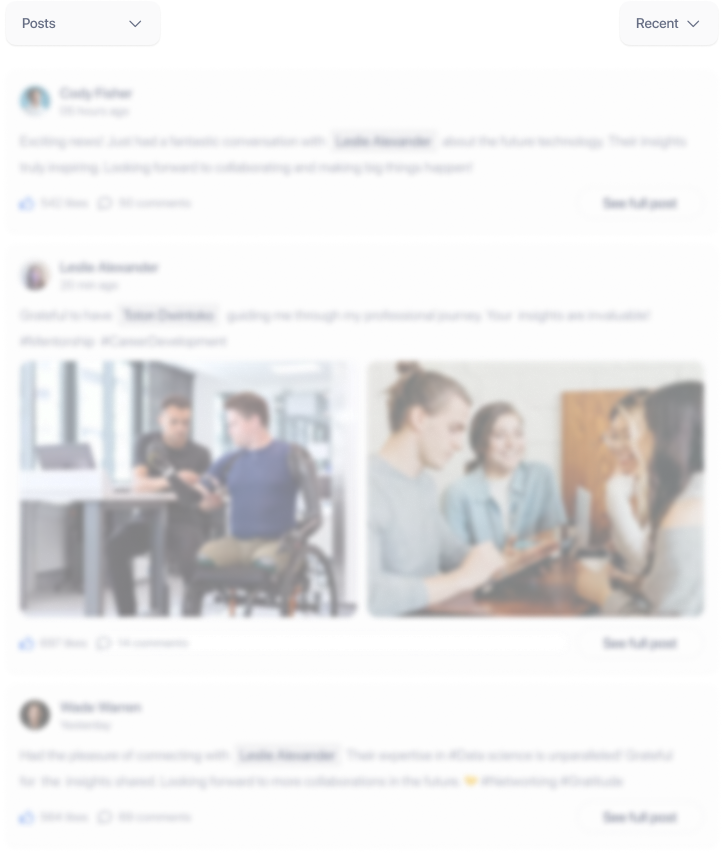