Ken Ferguson
Continuous Improvement Manager at United Hardware- Claim this Profile
Click to upgrade to our gold package
for the full feature experience.
Topline Score
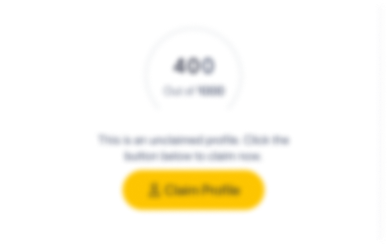
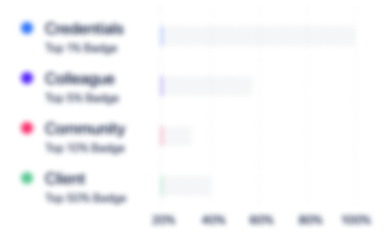
Bio


Credentials
-
CAPM Exam Prep Seminar
Instructing.com - Joseph PhillipsJan, 2023- Nov, 2024 -
Gemba Kaizen: A Commonsense Approach to Continuous Improvement (Blinkist Summary)
LinkedInFeb, 2021- Nov, 2024 -
Lean Six Sigma Green Belt (ICGB)
Management & Strategy InstituteJan, 2019- Nov, 2024 -
Certified Associate in Project Management (CAPM)®
Project Management InstituteDec, 2022- Nov, 2024
Experience
-
United Hardware
-
United States
-
Wholesale
-
100 - 200 Employee
-
Continuous Improvement Manager
-
Oct 2021 - Present
-
-
Production Supervisor
-
Mar 2021 - Oct 2021
-
-
-
Vestas
-
Denmark
-
Industrial Machinery Manufacturing
-
700 & Above Employee
-
Production Supervisor
-
Apr 2019 - Mar 2021
• Supervised a team of 34 employees in Webs and Carbon production • Implemented improvements to increase efficiency and meet internal customer requirements • Monitored quality defects and took corrective action to address root causes • Evaluated employee performance and provided coaching and support for success • Supervised a team of 34 employees in Webs and Carbon production • Implemented improvements to increase efficiency and meet internal customer requirements • Monitored quality defects and took corrective action to address root causes • Evaluated employee performance and provided coaching and support for success
-
-
-
Elkay Manufacturing
-
United States
-
Manufacturing
-
400 - 500 Employee
-
Production Supervisor
-
Jun 2018 - Apr 2019
• Managed a team of 43 employees in Cabinet production, including Face Frame assembly and cabinet finishing • Achieved daily production goals and order fulfilment • Analyzed QC data to identify trends and took corrective action to address root causes • Led weekly kaizen meetings to identify and implement process improvements using the PDCA method • Implemented Frontline Management Boards to track hourly production pace and identify and document corrective actions for shortfalls • Managed a team of 43 employees in Cabinet production, including Face Frame assembly and cabinet finishing • Achieved daily production goals and order fulfilment • Analyzed QC data to identify trends and took corrective action to address root causes • Led weekly kaizen meetings to identify and implement process improvements using the PDCA method • Implemented Frontline Management Boards to track hourly production pace and identify and document corrective actions for shortfalls
-
-
-
Old West Mattress
-
Denver, CO
-
Production Manager
-
Sep 2014 - Feb 2018
• Responsible for 25 employees in mattress and boxspring production. • Quality assurance: Conduct daily quality inspections and take corrective actions to assure quality standards are met. • Developed customized production reports giving employees detailed schedules to follow. • Safety Trainer: Conduct monthly safety meetings on general topics and address any specific hazards identified in our facility • Purchasing and inventory control • Responsible for 25 employees in mattress and boxspring production. • Quality assurance: Conduct daily quality inspections and take corrective actions to assure quality standards are met. • Developed customized production reports giving employees detailed schedules to follow. • Safety Trainer: Conduct monthly safety meetings on general topics and address any specific hazards identified in our facility • Purchasing and inventory control
-
-
-
Sermaro Mattress Company
-
Greater Denver Area
-
Plant Manager
-
Apr 2013 - Aug 2014
• Managed 15 employees in mattress production, warehouse, and delivery • Responsible for the full scope of plant operation including Purchasing/Receiving, Shipping/Warehouse, Product Development, Maintenance, Dealer Relations, Drafting and enforcing policy, Hiring and training, Process improvement • Managed 15 employees in mattress production, warehouse, and delivery • Responsible for the full scope of plant operation including Purchasing/Receiving, Shipping/Warehouse, Product Development, Maintenance, Dealer Relations, Drafting and enforcing policy, Hiring and training, Process improvement
-
-
-
Sealy
-
Furniture and Home Furnishings Manufacturing
-
500 - 600 Employee
-
Production Supervisor
-
Jul 2011 - Apr 2013
• Responsible for 20 employees in mattress production. • Assure budget compliance , quality conformance, and schedule fulfillment (On time and complete) • Conduct continuous Improvement projects utilizing lean principles. • Responsible for 20 employees in mattress production. • Assure budget compliance , quality conformance, and schedule fulfillment (On time and complete) • Conduct continuous Improvement projects utilizing lean principles.
-
-
-
American Paltech
-
Greater Denver Area
-
Production Manager
-
Jul 2010 - Jul 2011
• Responsible for all aspects of first shift production including warehouse, quality control, budget compliance, inventory control, shipping, safety, and training. • Certified forklift trainer • Developed and maintain payroll and attendance files to track and calculate piece work and attendance • Responsible for all aspects of first shift production including warehouse, quality control, budget compliance, inventory control, shipping, safety, and training. • Certified forklift trainer • Developed and maintain payroll and attendance files to track and calculate piece work and attendance
-
-
-
Sierra Springs
-
Greater Denver Area
-
Plant Manager
-
2008 - 2010
* Responsible for all aspects of water bottling operation including purchasing, maintenance, quality, FDA compliance, HACCP Program, project management, budget, inventory control, shipping, safety, and training. * CPO certified, Certified SQF practitioner * Significantly improved national quality score and production efficiency through improved monitoring methods and corrective action planning and execution. * Developed purchasing and inventory management tools to assure proper… Show more * Responsible for all aspects of water bottling operation including purchasing, maintenance, quality, FDA compliance, HACCP Program, project management, budget, inventory control, shipping, safety, and training. * CPO certified, Certified SQF practitioner * Significantly improved national quality score and production efficiency through improved monitoring methods and corrective action planning and execution. * Developed purchasing and inventory management tools to assure proper inventory levels. Show less * Responsible for all aspects of water bottling operation including purchasing, maintenance, quality, FDA compliance, HACCP Program, project management, budget, inventory control, shipping, safety, and training. * CPO certified, Certified SQF practitioner * Significantly improved national quality score and production efficiency through improved monitoring methods and corrective action planning and execution. * Developed purchasing and inventory management tools to assure proper… Show more * Responsible for all aspects of water bottling operation including purchasing, maintenance, quality, FDA compliance, HACCP Program, project management, budget, inventory control, shipping, safety, and training. * CPO certified, Certified SQF practitioner * Significantly improved national quality score and production efficiency through improved monitoring methods and corrective action planning and execution. * Developed purchasing and inventory management tools to assure proper inventory levels. Show less
-
-
-
Tri-Star Bedding
-
Greater Denver Area
-
Plant Manager
-
2007 - 2008
* Responsible for 4 supervisors and 50+ shop floor employees. * Oversaw all aspects of plant operations including Scheduling, Materials Management, Logistics, and Maintenance. * Developed computer tools for production monitoring, scheduling, and purchasing. * Responsible for 4 supervisors and 50+ shop floor employees. * Oversaw all aspects of plant operations including Scheduling, Materials Management, Logistics, and Maintenance. * Developed computer tools for production monitoring, scheduling, and purchasing.
-
-
-
Simmons Bedding Company
-
United States
-
Manufacturing
-
400 - 500 Employee
-
Production Manager
-
1999 - 2007
* Responsible for management of 3 – 5 supervisors and 50 – 65 shop floor employees. * Responsible for 3 mechanics and the maintenance budget. * Implemented and managed national quality program during the absence of a Quality Manager. * Co-wrote quality tracking spreadsheets which were implemented company-wide in 17 plants. * Wrote purchasing program to streamline daily ordering of raw materials. This program was adopted by National Purchasing and became the Mandatory Best Practice… Show more * Responsible for management of 3 – 5 supervisors and 50 – 65 shop floor employees. * Responsible for 3 mechanics and the maintenance budget. * Implemented and managed national quality program during the absence of a Quality Manager. * Co-wrote quality tracking spreadsheets which were implemented company-wide in 17 plants. * Wrote purchasing program to streamline daily ordering of raw materials. This program was adopted by National Purchasing and became the Mandatory Best Practice company wide. Show less * Responsible for management of 3 – 5 supervisors and 50 – 65 shop floor employees. * Responsible for 3 mechanics and the maintenance budget. * Implemented and managed national quality program during the absence of a Quality Manager. * Co-wrote quality tracking spreadsheets which were implemented company-wide in 17 plants. * Wrote purchasing program to streamline daily ordering of raw materials. This program was adopted by National Purchasing and became the Mandatory Best Practice… Show more * Responsible for management of 3 – 5 supervisors and 50 – 65 shop floor employees. * Responsible for 3 mechanics and the maintenance budget. * Implemented and managed national quality program during the absence of a Quality Manager. * Co-wrote quality tracking spreadsheets which were implemented company-wide in 17 plants. * Wrote purchasing program to streamline daily ordering of raw materials. This program was adopted by National Purchasing and became the Mandatory Best Practice company wide. Show less
-
-
-
Sealy
-
Furniture and Home Furnishings Manufacturing
-
500 - 600 Employee
-
Production Supervisor
-
1991 - 1999
* Supervised 20 – 30 production employees * Spearheaded quality initiative implementing corrective actions throughout the factory. * Assisted “troubled” plants in other parts of the country to help improve quality and production problems. * Supervised 20 – 30 production employees * Spearheaded quality initiative implementing corrective actions throughout the factory. * Assisted “troubled” plants in other parts of the country to help improve quality and production problems.
-
-
-
Restonic
-
United States
-
Consumer Goods
-
1 - 100 Employee
-
Production Foreman
-
1990 - 1991
Instrumental participant in the start-up process from ground level to fully functional operation. Responsible for all aspects of production with a crew of 10 - 12 Wrote production schedule and tracked pieces to ensure loads were complete. Instrumental participant in the start-up process from ground level to fully functional operation. Responsible for all aspects of production with a crew of 10 - 12 Wrote production schedule and tracked pieces to ensure loads were complete.
-
-
-
Marine Corp Reserve
-
Salem, Oregon
-
Combat Engineer
-
Jun 1983 - May 1987
6th Engineer Support Battalion - Heavy Equipment Operator 6th Engineer Support Battalion - Heavy Equipment Operator
-
-
Education
-
western baptist
-
McKay
Community
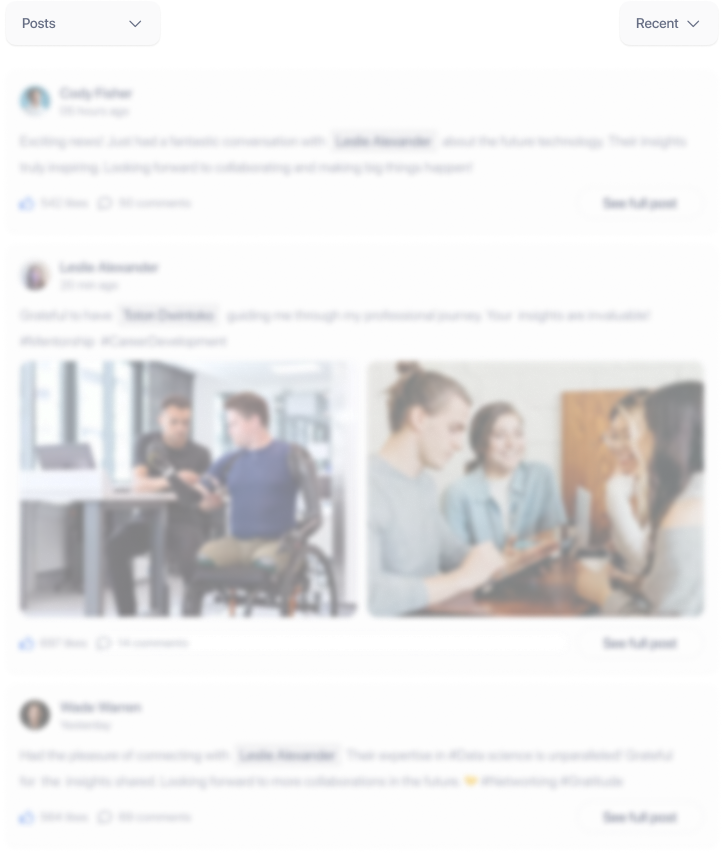